- お役立ち記事
- Don’t miss the quality department! Specific examples of quality improvement using Six Sigma
Don’t miss the quality department! Specific examples of quality improvement using Six Sigma
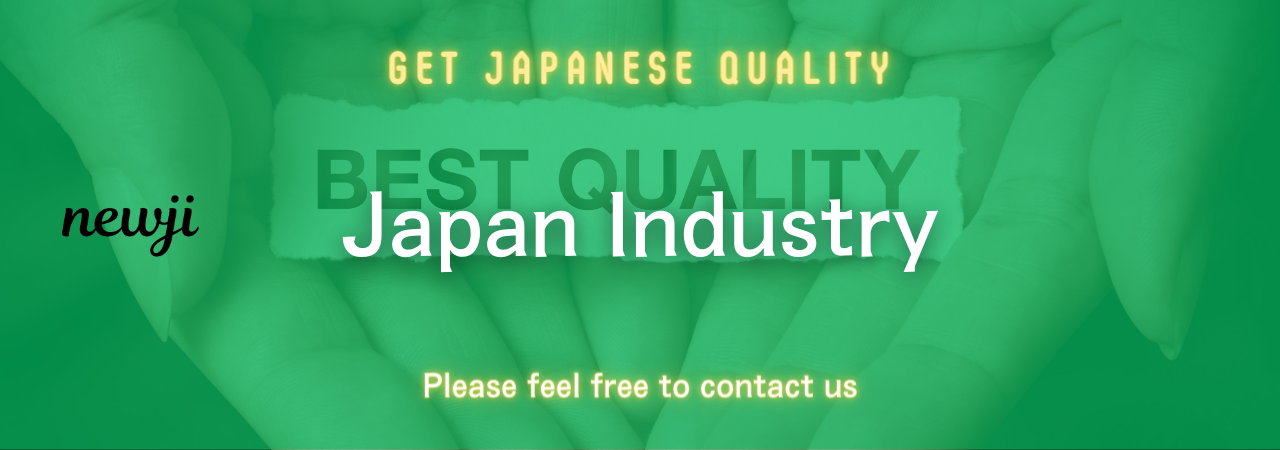
目次
Understanding Six Sigma
Six Sigma is a systematic methodology aimed at improving the quality of processes by identifying and eliminating defects or inefficiencies.
Developed by Motorola in the 1980s, Six Sigma’s core objective is to achieve near-perfect quality, targeting not more than 3.4 defects per million opportunities.
The approach uses data-driven techniques and statistical analysis to refine processes, enhance performance, and ensure products or services meet customer expectations consistently.
The Six Sigma process is represented through the DMAIC framework, which stands for Define, Measure, Analyze, Improve, and Control.
Each phase of the DMAIC methodology plays a crucial role in the overall process improvement, requiring a disciplined approach to problem-solving.
Organizations from various industries have adopted Six Sigma to drive quality improvements, streamline operations, and reduce costs.
Define Phase: Establishing Goals and Objectives
The Define phase sets the foundation for the Six Sigma project by clearly identifying the problem or opportunity for improvement.
It involves establishing project goals and objectives that align with the company’s strategic priorities.
During this phase, project teams gather input from stakeholders to understand customer requirements and expectations.
Defining the scope of the project is crucial to prevent scope creep and ensure that team efforts remain focused.
In this stage, tools such as project charters and SIPOC (Suppliers, Inputs, Processes, Outputs, Customers) diagrams are often used.
These tools help outline the process flow and highlight areas that require attention.
Case Study: Reducing Order Processing Time
A retail company faced challenges with longer-than-average order processing times, leading to customer dissatisfaction and increased costs.
Using Six Sigma’s Define phase, the project team identified the primary goal: to reduce order processing time by 30% within six months without compromising quality or customer service.
With a clear objective in place, the company proceeded to the next phase of the DMAIC process.
Measure Phase: Collecting and Analyzing Data
In the Measure phase, teams gather relevant data to understand the current performance of the process being analyzed.
This phase involves defining key performance indicators (KPIs) and identifying data sources.
It is essential to collect accurate and reliable data to establish a baseline against which improvements can be measured.
Measuring the existing process includes quantifying variations and understanding why defects occur.
Techniques such as Pareto charts, histograms, and process maps are commonly used tools that help visualize data and identify patterns.
The collected data lays the groundwork for subsequent analysis and decision-making.
Case Study: Evaluating Order Processing Data
Once the retail company defined its project goal of reducing order processing time, it proceeded to measure the current process.
The team collected data on the average time taken for each step of the order processing cycle, from order receipt to delivery.
By analyzing this data, the team identified bottlenecks and variations that contributed to longer processing times, particularly during the order fulfillment stage.
Analyze Phase: Identifying Root Causes
The Analyze phase of Six Sigma focuses on identifying the root causes of defects or inefficiencies within a process.
By understanding these underlying causes, teams can develop targeted solutions that will lead to sustainable improvements.
Statistical analysis tools such as cause-and-effect diagrams, regression analysis, and hypothesis testing are often employed during this phase.
This stage encourages a deep dive into the data and the process, challenging assumptions and removing any potential biases.
It’s crucial to differentiate between symptoms and root causes to effectively address the issues at hand.
Case Study: Addressing Fulfillment Bottlenecks
Through in-depth analysis, the retail company’s Six Sigma team discovered that the primary bottleneck in their order processing was the fulfillment stage.
The root cause analysis revealed that delays were due to inefficient inventory management and a lack of coordination between warehouse staff.
By identifying these root causes, the team could move on to finding effective solutions to improve the process.
Improve Phase: Implementing Solutions
The Improve phase involves developing and implementing solutions to address the root causes identified in the Analyze phase.
Teams design and test interventions that are both effective and sustainable.
This phase often involves brainstorming sessions, pilot testing, and evaluating different improvement strategies.
The focus is on making data-driven decisions that lead to tangible improvements in process performance.
Innovative solutions, such as process re-engineering and adopting new technologies, might be explored.
Case Study: Streamlining Order Fulfillment
To improve their order processing times, the retail company’s team devised several solutions focused on streamlining the fulfillment stage.
They implemented a new inventory management system to better track stock levels and reduce out-of-stock situations.
Additionally, they trained warehouse staff on more efficient picking and packing techniques.
These measures resulted in a significant reduction in processing times, achieving the project goal of a 30% decrease in order processing time within the specified timeframe.
Control Phase: Sustaining Improvements
The final stage of the DMAIC process, the Control phase, ensures that the improvements achieved during the Improve phase are sustained over time.
This involves putting systems and processes in place to maintain the gains made and prevent regression.
Monitoring tools, control charts, and standard operating procedures (SOPs) are essential in this phase.
Regular audits, employee feedback, and continuous monitoring help address any arising issues and keep the process on the right track.
Case Study: Maintaining Efficiency Gains
Having successfully streamlined their order processing, the retail company put a control plan into action to sustain its improvements.
They implemented regular training programs for staff, ongoing monitoring of the new inventory system, and established key performance metrics to track order processing times.
Through these measures, they ensured that their newfound efficiency was maintained, ultimately leading to improved customer satisfaction and reduced costs.
Conclusion: Embracing Six Sigma for Continuous Quality Improvement
Six Sigma has proved to be an invaluable methodology for organizations seeking to enhance quality and reduce inefficiencies in their processes.
By systematically applying the DMAIC framework, companies can identify areas for improvement, implement effective solutions, and maintain high standards over time.
Whether it’s in manufacturing, healthcare, or service industries, Six Sigma provides a structured approach to problem-solving that can lead to significant quality improvements.
Organizations embracing Six Sigma not only improve their operations but also foster a culture of continuous improvement, setting them on a path to long-term success.
資料ダウンロード
QCD調達購買管理クラウド「newji」は、調達購買部門で必要なQCD管理全てを備えた、現場特化型兼クラウド型の今世紀最高の購買管理システムとなります。
ユーザー登録
調達購買業務の効率化だけでなく、システムを導入することで、コスト削減や製品・資材のステータス可視化のほか、属人化していた購買情報の共有化による内部不正防止や統制にも役立ちます。
NEWJI DX
製造業に特化したデジタルトランスフォーメーション(DX)の実現を目指す請負開発型のコンサルティングサービスです。AI、iPaaS、および先端の技術を駆使して、製造プロセスの効率化、業務効率化、チームワーク強化、コスト削減、品質向上を実現します。このサービスは、製造業の課題を深く理解し、それに対する最適なデジタルソリューションを提供することで、企業が持続的な成長とイノベーションを達成できるようサポートします。
オンライン講座
製造業、主に購買・調達部門にお勤めの方々に向けた情報を配信しております。
新任の方やベテランの方、管理職を対象とした幅広いコンテンツをご用意しております。
お問い合わせ
コストダウンが利益に直結する術だと理解していても、なかなか前に進めることができない状況。そんな時は、newjiのコストダウン自動化機能で大きく利益貢献しよう!
(Β版非公開)