- お役立ち記事
- Door Stopper Manufacturing Process and Holding Power Strengthening
Door Stopper Manufacturing Process and Holding Power Strengthening
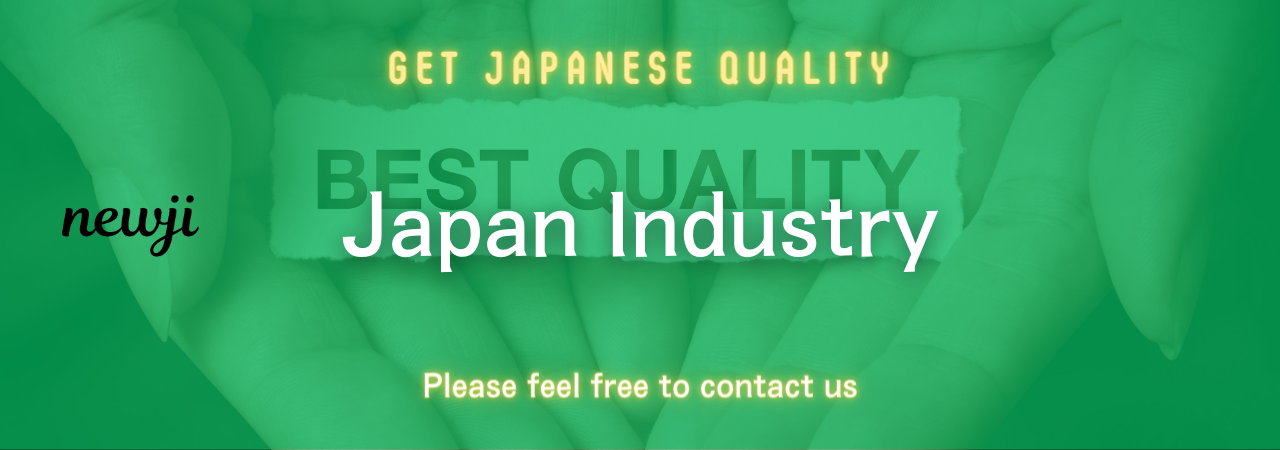
目次
Introduction to Door Stoppers
Door stoppers are small yet crucial components found in nearly every home, office, or public building.
They help in keeping doors open, closed, and prevent them from banging against walls or other objects.
Understanding the manufacturing process of door stoppers can give insight into their durability and holding power.
This involves a series of steps that ensure the final product is both functional and long-lasting.
This article will delve into the intricate world of door stopper manufacturing and methods to enhance their holding power.
Materials Used in Door Stopper Manufacturing
The first step in manufacturing door stoppers is selecting the right materials.
The materials used can significantly affect the performance and longevity of the door stopper.
Common materials include rubber, plastic, metal, and even stone.
– **Rubber:** Known for its flexibility and durability, rubber is often used in door stoppers to ensure a non-slip grip.
It’s particularly effective in creating door wedges and floor-mounted stoppers.
– **Plastic:** Lightweight and cost-effective, plastic is a popular choice for household door stoppers.
It’s easy to mold into various shapes and sizes, making it versatile.
– **Metal:** Typically used in high-traffic areas, metal door stoppers offer superior strength and resilience.
They are often used in wall-mounted or hinge pin stoppers.
– **Stone:** Aesthetic and heavy, stone stoppers are often preferred for decorative purposes.
They are less common but provide an elegant touch to any room.
Manufacturing Process of Door Stoppers
Manufacturing door stoppers involves several key processes, each crucial to producing a reliable product.
1. Design and Prototype
The manufacturing process begins with designing and prototyping the door stopper.
Designers create sketches and 3D models, considering factors like size, shape, material, and intended use.
Prototypes are then produced to test the functionality and safety of the design.
2. Material Selection and Preparation
Once a design is finalized, the next step is selecting and preparing the materials.
For rubber and plastic stoppers, raw materials are melted and poured into molds.
For metal stoppers, the metal is cut and shaped through stamping or machining.
It’s crucial that the materials are prepared to precise specifications to ensure uniformity in production.
3. Molding and Shaping
The core manufacturing process comes after the preparation stage, where materials are molded and shaped into the desired form.
Rubber and plastic stoppers undergo injection molding, a process that injects the melted materials into molds where they cool and solidify.
Metal stoppers, on the other hand, may require more intensive processes like die-casting or forging for shaping.
4. Finishing and Quality Control
After molding, the stoppers move to the finishing stage.
Here they are cleaned, trimmed, and possibly painted or coated to enhance appearance and durability.
Quality control is a crucial part of this stage to ensure each stopper meets industry standards and specifications.
Tests for durability, grip, and holding power are conducted to weed out any defective products.
Enhancing the Holding Power of Door Stoppers
Holding power is a critical aspect of a door stopper’s functionality.
A good door stopper should hold the door securely in place, preventing unwanted movement.
Here are some methods to strengthen a door stopper’s holding power:
Design Optimization
The shape of a door stopper plays a crucial role in its holding power.
V-shaped designs are particularly effective at gripping the ground and door bottom.
By optimizing the design for maximum surface contact, manufacturers can produce stoppers with superior holding power.
In addition, the use of textured surfaces can increase friction and prevent slipping.
Material Improvement
Using high-friction materials is key to a door stopper’s holding capability.
Rubber, for instance, provides excellent grip due to its inherent friction properties.
Alternatively, incorporating a non-slip base, such as a layer of silicone or textured rubber, can significantly enhance holding power.
Incorporating Weight
The heavier the stopper, the more stable it is likely to be.
By adding weight to the stopper through dense materials like metal or adding a weighted core, the stability of the door stopper can be improved.
This reduces the likelihood of the door pushing the stopper aside under force.
Testing and Feedback
Continuous testing is essential in improving door stopper designs.
Collecting customer feedback can provide insight into performance issues and areas for enhancement.
Manufacturers often conduct iterative testing, evaluating how changes in design or material affect the holding power before finalizing the product.
Conclusion
The process of manufacturing door stoppers involves a series of thoughtful and precise steps, from material selection to final quality checks.
By optimizing design elements and selecting appropriate materials, manufacturers can significantly enhance the holding power of door stoppers.
Whether it’s a simple wedge or an intricate metal design, each stopper plays a vital role in our everyday safety and convenience.
Understanding the manufacturing process helps us appreciate these small but indispensable tools in our daily lives.
資料ダウンロード
QCD調達購買管理クラウド「newji」は、調達購買部門で必要なQCD管理全てを備えた、現場特化型兼クラウド型の今世紀最高の購買管理システムとなります。
ユーザー登録
調達購買業務の効率化だけでなく、システムを導入することで、コスト削減や製品・資材のステータス可視化のほか、属人化していた購買情報の共有化による内部不正防止や統制にも役立ちます。
NEWJI DX
製造業に特化したデジタルトランスフォーメーション(DX)の実現を目指す請負開発型のコンサルティングサービスです。AI、iPaaS、および先端の技術を駆使して、製造プロセスの効率化、業務効率化、チームワーク強化、コスト削減、品質向上を実現します。このサービスは、製造業の課題を深く理解し、それに対する最適なデジタルソリューションを提供することで、企業が持続的な成長とイノベーションを達成できるようサポートします。
オンライン講座
製造業、主に購買・調達部門にお勤めの方々に向けた情報を配信しております。
新任の方やベテランの方、管理職を対象とした幅広いコンテンツをご用意しております。
お問い合わせ
コストダウンが利益に直結する術だと理解していても、なかなか前に進めることができない状況。そんな時は、newjiのコストダウン自動化機能で大きく利益貢献しよう!
(Β版非公開)