- お役立ち記事
- DR and FMEA
月間76,176名の
製造業ご担当者様が閲覧しています*
*2025年3月31日現在のGoogle Analyticsのデータより
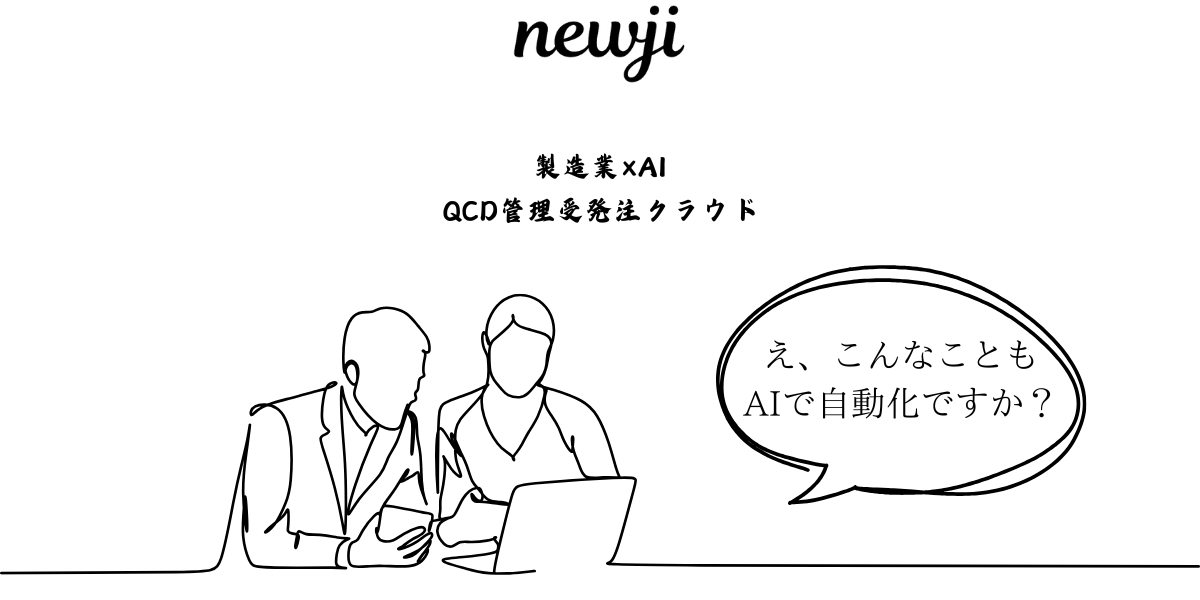
DR and FMEA
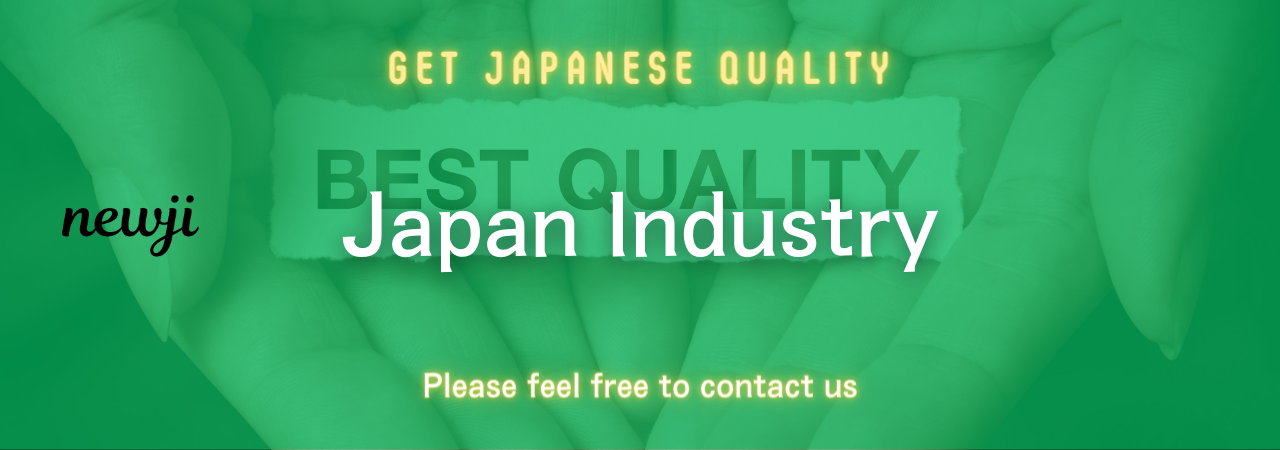
Understanding DR and FMEA
Design Review (DR) and Failure Mode and Effects Analysis (FMEA) are two essential techniques in engineering and product development.
They help ensure the reliability, safety, and functionality of products.
For beginners, understanding these terms might seem complex, but breaking down each concept will clarify their roles and importance.
What is Design Review (DR)?
Design Review is a process where the design of a product, system, or component is evaluated.
The main goal is to ensure that the design meets all the necessary specifications and requirements.
The review process helps identify potential problems early in the design phase.
By catching these issues before production begins, teams can save time and resources.
During a Design Review, a team of experts examines every aspect of a design.
They assess its functionality, quality, and overall performance.
They may consider customer needs, safety standards, and regulatory constraints.
A Design Review is not a one-time event.
It often occurs at several stages of the product development lifecycle, such as concept development, preliminary design, and detailed design.
The Importance of Design Review
Conducting a thorough Design Review brings several benefits.
First, it improves product quality by ensuring that the final design is effective and efficient.
By identifying and mitigating risks early in the process, teams can reduce errors and avoid costly redesigns.
Additionally, Design Review enhances collaboration.
It involves cross-functional teams, including engineers, designers, and stakeholders.
By bringing together diverse perspectives, the process encourages problem-solving and innovation.
Another significant benefit is ensuring compliance with industry standards and regulations.
A well-structured Design Review process checks that the product meets all necessary guidelines before it enters the market.
What is Failure Mode and Effects Analysis (FMEA)?
Failure Mode and Effects Analysis (FMEA) is a systematic method for evaluating a product or process to identify potential failure modes.
The goal is to determine the effects of these failures and prioritize actions to mitigate them.
FMEA aims to enhance reliability and safety. It helps teams understand how and where things might go wrong, and what the consequences might be.
There are two main types of FMEA:
1. Design FMEA (DFMEA): Focuses on potential failures in the product design phase.
2. Process FMEA (PFMEA): Examines possible failures in manufacturing and assembly processes.
FMEA is a proactive approach, meaning it seeks to eliminate risks before they occur.
Unlike reactive approaches, which address problems after they arise, FMEA anticipates issues, minimizing their impact on the end product.
Steps Involved in FMEA
Conducting an FMEA involves several key steps:
1. **Identify the Process or Design**: Begin by clearly defining the design or process to be analyzed.
2. **List Potential Failure Modes**: Identify all possible failures, considering what could go wrong in the design or process.
3. **Determine Effects of Failures**: Analyze the potential effects and severity of each failure mode on the product or process.
4. **Assess Causes and Occurrences**: Investigate the causes of each failure mode and estimate its likelihood of occurrence.
5. **Determine Detection Methods**: Evaluate the current controls and methods in place for detecting each failure.
6. **Calculate Risk Priority Number (RPN)**: Assign a severity, occurrence, and detection rating to each failure mode and calculate the RPN.
7. **Prioritize Actions**: Use the RPN to prioritize which failure modes require immediate attention and action.
8. **Implement Improvements**: Develop and implement actions to reduce or eliminate high-risk failure modes.
9. **Review and Update**: Regularly review the FMEA process to ensure ongoing effectiveness and update it as necessary.
The Benefits of FMEA
FMEA offers several advantages to product development and manufacturing processes.
It enhances safety by identifying and mitigating failure risks before they occur.
This not only protects users and operators but also limits liability for manufacturers.
Additionally, FMEA can improve product quality.
By proactively addressing potential issues, businesses can reduce defects and improve customer satisfaction.
Cost savings is another significant benefit.
Identifying problems early in the design phase can prevent costly production issues, leading to more efficient use of resources.
Finally, FMEA promotes continuous improvement.
By regularly updating and reviewing FMEA results, organizations can adapt to changes and further refine their processes.
Integrating DR and FMEA for Success
While Design Review and FMEA are distinct processes, their integration is crucial for achieving optimal results in product development.
Together, they create a comprehensive approach to risk management and quality assurance.
During Design Review, teams can incorporate FMEA findings to address potential failure modes in the design phase.
Similarly, insights from Design Reviews can inform FMEA teams about areas of focus or concern.
Collaboration between these processes ensures that products are both well-designed and thoroughly evaluated for potential risks.
Conclusion
Understanding the roles of Design Review and FMEA is critical for anyone involved in product development.
By incorporating these processes, teams can enhance quality, safety, and reliability, ultimately leading to successful product launches.
While it may seem challenging to grasp these concepts initially, breaking them down into manageable components makes them accessible to team members and stakeholders alike.
With the right approach, DR and FMEA can become integral tools in your project’s success.
資料ダウンロード
QCD管理受発注クラウド「newji」は、受発注部門で必要なQCD管理全てを備えた、現場特化型兼クラウド型の今世紀最高の受発注管理システムとなります。
ユーザー登録
受発注業務の効率化だけでなく、システムを導入することで、コスト削減や製品・資材のステータス可視化のほか、属人化していた受発注情報の共有化による内部不正防止や統制にも役立ちます。
NEWJI DX
製造業に特化したデジタルトランスフォーメーション(DX)の実現を目指す請負開発型のコンサルティングサービスです。AI、iPaaS、および先端の技術を駆使して、製造プロセスの効率化、業務効率化、チームワーク強化、コスト削減、品質向上を実現します。このサービスは、製造業の課題を深く理解し、それに対する最適なデジタルソリューションを提供することで、企業が持続的な成長とイノベーションを達成できるようサポートします。
製造業ニュース解説
製造業、主に購買・調達部門にお勤めの方々に向けた情報を配信しております。
新任の方やベテランの方、管理職を対象とした幅広いコンテンツをご用意しております。
お問い合わせ
コストダウンが利益に直結する術だと理解していても、なかなか前に進めることができない状況。そんな時は、newjiのコストダウン自動化機能で大きく利益貢献しよう!
(β版非公開)