- お役立ち記事
- Driving Improvement in Manufacturing with Quality Control Circles (QC Circles)
月間76,176名の
製造業ご担当者様が閲覧しています*
*2025年3月31日現在のGoogle Analyticsのデータより
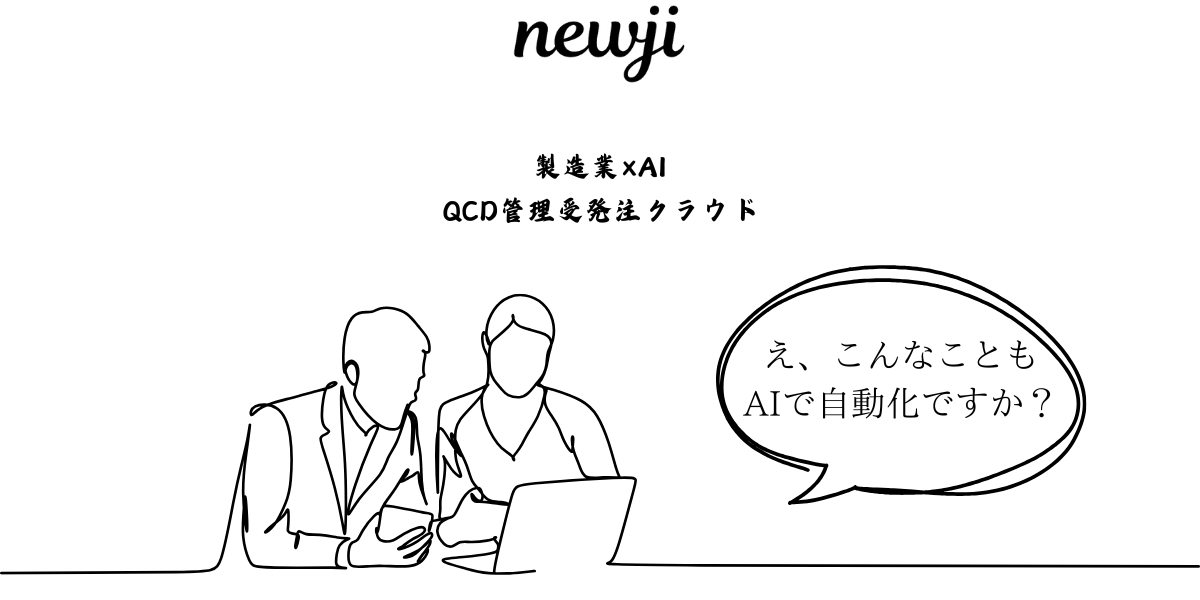
Driving Improvement in Manufacturing with Quality Control Circles (QC Circles)
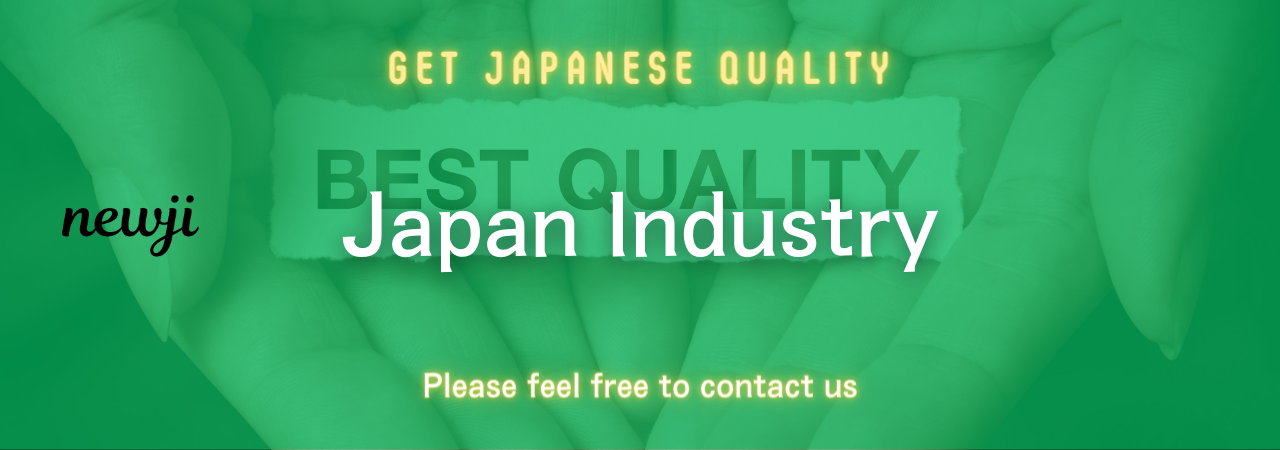
In the fast-paced world of manufacturing, maintaining high standards is essential to produce quality products consistently.
One of the most effective ways to achieve this is through Quality Control Circles, commonly known as QC Circles.
These circles are small groups of workers who regularly meet to discuss and solve work-related problems.
Let’s explore how QC Circles can drive improvement in manufacturing processes.
目次
Understanding Quality Control Circles
Quality Control Circles originated in Japan and have been a cornerstone of continuous improvement practices for decades.
The concept is simple but powerful: empower employees to take an active role in identifying and solving problems within their work environment.
This participatory approach fosters a sense of ownership and accountability among workers.
How QC Circles Work
QC Circles typically consist of a small group of employees, usually from the same work area or department.
These groups meet regularly to discuss issues, perform analysis, and develop solutions.
Each member contributes their unique perspective and expertise, leading to well-rounded and effective problem-solving.
Benefits of Implementing QC Circles
Integrating QC Circles into manufacturing processes offers numerous benefits for both the company and its employees.
Improved Product Quality
One of the primary goals of QC Circles is to enhance product quality.
By identifying root causes of defects and developing targeted solutions, QC Circles help to reduce errors and improve the overall quality of the manufactured goods.
Increased Employee Engagement
QC Circles encourage employees to take an active role in their work processes.
This involvement leads to higher levels of job satisfaction and engagement.
When employees feel that their opinions and contributions matter, they are more likely to be motivated and committed to the company’s goals.
Enhanced Problem-Solving Skills
Participating in QC Circles helps employees develop critical thinking and problem-solving skills.
These skills are valuable not only for addressing immediate issues but also for fostering a culture of continuous improvement within the organization.
Cost Reduction
By identifying inefficiencies and implementing effective solutions, QC Circles can lead to significant cost savings.
Reducing waste, minimizing rework, and improving resource utilization are just a few ways that QC Circles can contribute to a company’s bottom line.
Challenges and Solutions in Implementing QC Circles
While the benefits of QC Circles are clear, implementing them successfully can present some challenges.
Understanding these challenges and addressing them proactively is crucial for the success of QC Circles.
Overcoming Resistance to Change
Employees may be resistant to the new approach, particularly if they are accustomed to traditional hierarchical management structures.
To overcome this resistance, it’s important to communicate the purpose and benefits of QC Circles clearly and to involve employees in the planning and implementation process.
Ensuring Consistent Participation
Maintaining regular and consistent participation in QC Circle activities can be challenging.
Scheduling meetings at convenient times and providing adequate support and resources can help ensure that employees remain engaged and committed to the process.
Providing Adequate Training
Employees need proper training to effectively participate in QC Circles.
This includes training on problem-solving techniques, data analysis, and effective communication.
Investing in training ensures that QC Circles can function effectively and achieve their objectives.
Steps to Implement QC Circles in Manufacturing
Introducing QC Circles in a manufacturing environment requires careful planning and execution.
Here are some steps to get started:
Step 1: Gain Management Support
The success of QC Circles depends on the support and commitment of the management team.
Management must provide the necessary resources, support, and encouragement to ensure the initiative’s success.
Step 2: Form QC Circles
Identify and form small groups of employees from the same work area or department.
Ensure that each group has a mix of skills and expertise to facilitate effective problem-solving.
Step 3: Provide Training
Offer comprehensive training sessions to all members of the QC Circles.
This training should cover topics such as problem-solving methodologies, data analysis, and group dynamics.
Step 4: Schedule Regular Meetings
Establish a regular meeting schedule for the QC Circles.
These meetings should provide a platform for discussing issues, analyzing data, and developing action plans.
Step 5: Monitor Progress and Provide Feedback
Regularly monitor the progress of QC Circle activities and provide constructive feedback.
Celebrate successes and provide additional support where needed to overcome challenges.
Case Study: Success through QC Circles
Let’s take a look at a real-world example of how QC Circles have driven improvement in a manufacturing company.
ABC Manufacturing, a company specializing in automotive parts, faced issues with product defects and high production costs.
The company decided to implement QC Circles to address these challenges.
After forming QC Circles and providing the necessary training, the teams began meeting regularly to identify and address issues.
One QC Circle focused on reducing defects in a specific part of the production process.
Through root cause analysis and brainstorming, the team identified several factors contributing to the defects.
They implemented solutions such as adjusting machine settings and improving inspection procedures.
Within a few months, the defect rate significantly decreased, leading to better product quality and reduced costs.
Employees also reported higher job satisfaction and engagement, as they felt empowered to make a difference.
Conclusion
Quality Control Circles offer a powerful approach to driving continuous improvement in manufacturing.
By involving employees in problem-solving and decision-making processes, QC Circles not only improve product quality but also enhance employee engagement and reduce costs.
While there may be challenges in implementing QC Circles, with proper planning and support, the benefits far outweigh the difficulties.
Investing in QC Circles can lead to a more efficient, productive, and satisfied workforce, driving long-term success for the company.
資料ダウンロード
QCD管理受発注クラウド「newji」は、受発注部門で必要なQCD管理全てを備えた、現場特化型兼クラウド型の今世紀最高の受発注管理システムとなります。
ユーザー登録
受発注業務の効率化だけでなく、システムを導入することで、コスト削減や製品・資材のステータス可視化のほか、属人化していた受発注情報の共有化による内部不正防止や統制にも役立ちます。
NEWJI DX
製造業に特化したデジタルトランスフォーメーション(DX)の実現を目指す請負開発型のコンサルティングサービスです。AI、iPaaS、および先端の技術を駆使して、製造プロセスの効率化、業務効率化、チームワーク強化、コスト削減、品質向上を実現します。このサービスは、製造業の課題を深く理解し、それに対する最適なデジタルソリューションを提供することで、企業が持続的な成長とイノベーションを達成できるようサポートします。
製造業ニュース解説
製造業、主に購買・調達部門にお勤めの方々に向けた情報を配信しております。
新任の方やベテランの方、管理職を対象とした幅広いコンテンツをご用意しております。
お問い合わせ
コストダウンが利益に直結する術だと理解していても、なかなか前に進めることができない状況。そんな時は、newjiのコストダウン自動化機能で大きく利益貢献しよう!
(β版非公開)