- お役立ち記事
- DX and cyber-physical systems in manufacturing: Innovation brought about by the convergence of the real and digital worlds
DX and cyber-physical systems in manufacturing: Innovation brought about by the convergence of the real and digital worlds
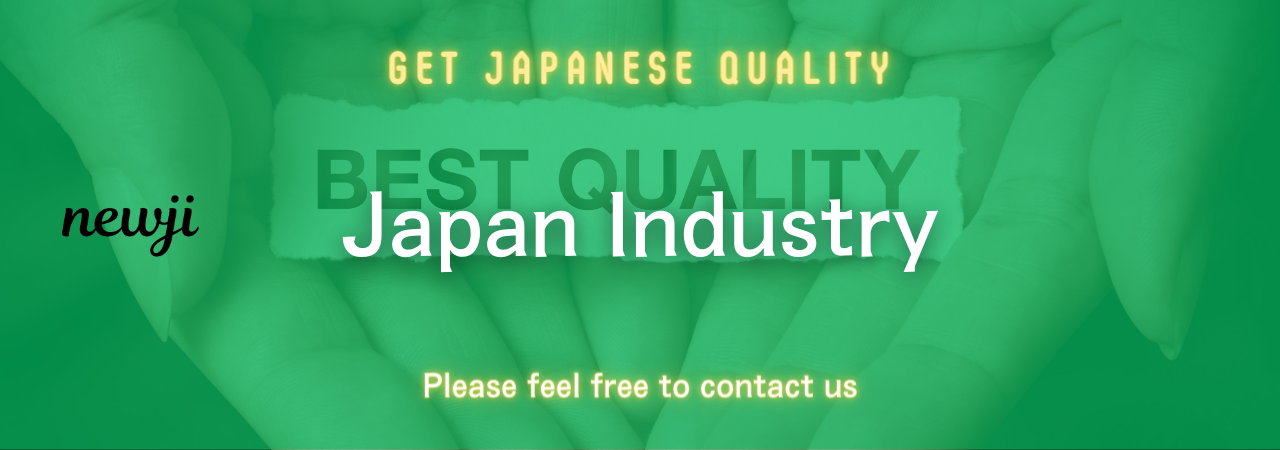
In today’s fast-paced world, industries must continuously innovate to remain competitive.
One of the most transformative changes currently reshaping manufacturing is the convergence of the real and digital worlds through Digital Transformation (DX) and Cyber-Physical Systems (CPS).
These advancements are not just buzzwords; they represent a significant shift in how manufacturing processes are designed, managed, and optimized.
目次
Understanding Digital Transformation (DX) in Manufacturing
Digital Transformation in manufacturing involves leveraging digital technologies to improve processes, increase efficiency, and enhance product quality.
This transformation isn’t simply about adopting new tools; it’s about reshaping the entire operational framework and business model.
DX initiatives might include integrating advanced analytics, IoT devices, machine learning, and automation into the production chain.
The Role of IoT in Manufacturing
The Internet of Things (IoT) connects machines, sensors, and systems, enabling them to communicate in real-time.
In manufacturing, IoT devices collect vast amounts of data from various sources, including production lines, inventory systems, and distribution networks.
This data provides valuable insights that help in decision-making, predictive maintenance, and process optimization.
Machine Learning and Predictive Analytics
Machine learning algorithms analyze historical and real-time data to identify patterns and predict future outcomes.
In manufacturing, this means machines can predict when a component might fail and schedule maintenance before it causes downtime.
Predictive analytics help in optimizing supply chain management, reducing waste, and improving quality control.
Cyber-Physical Systems: Bridging the Physical-Digital Divide
Cyber-Physical Systems represent the integration of computational algorithms and physical processes.
In a CPS, embedded computers and networks monitor and control physical processes, usually with feedback loops where physical processes affect computations and vice versa.
The Architecture of Cyber-Physical Systems
CPS typically consist of three main components: sensors and actuators, computational units, and communication networks.
Sensors gather data from the physical environment, which is processed by computational units to make decisions.
Actuators then execute these decisions in the physical world.
This seamless interaction ensures that systems are adaptable and responsive to real-time conditions.
Applications of CPS in Manufacturing
In manufacturing, CPS can be used for precise control and monitoring of automated production lines.
They allow for real-time tracking of manufacturing workflows, meaning any deviations or inefficiencies can be immediately addressed.
For example, adaptive control systems in robotic arms can adjust their movements based on sensor feedback, improving accuracy and speed.
Innovation at the Intersection of DX and CPS
Combining DX with CPS in manufacturing leads to significant innovations.
The synergy of these technologies enhances productivity, reduces costs, and fosters the development of smart factories.
Smart Factories
A smart factory leverages both DX and CPS to create a highly flexible and efficient manufacturing environment.
Production processes are continuously monitored and optimized through real-time data analytics and automated decision-making systems.
This level of automation allows for rapid changes in production lines to accommodate new products or modifications without the need for extensive downtime.
Enhanced Worker Safety
One of the immediate benefits of integrating DX and CPS is improved worker safety.
Smart sensors and AI can detect hazardous conditions and automatically shut down machinery to prevent accidents.
Augmented reality (AR) can provide workers with real-time instructions and hazard alerts, reducing the risk of human error.
Personalized Manufacturing
These technologies enable a shift from mass production to mass customization.
Manufacturers can now produce customized products at scale, tailoring products to individual customer specifications without significant increases in production costs.
This capability is particularly beneficial in industries such as automotive, aerospace, and consumer electronics.
Challenges and Considerations
While the convergence of DX and CPS in manufacturing brings numerous benefits, it also entails challenges that must be addressed.
Cybersecurity
With increased connectivity comes greater vulnerability to cyber-attacks.
Manufacturers must invest in robust cybersecurity measures to protect sensitive data and ensure the integrity of their systems.
This involves not only implementing advanced security protocols but also regular training for employees on best practices.
Skills Gap
Adopting these advanced technologies requires a workforce with the necessary skills.
There is a growing need for workers proficient in data analytics, machine learning, and system integration.
Manufacturers must invest in training and development programs to bridge this skills gap.
Initial Investment Costs
Implementing DX and CPS can involve significant upfront costs.
This includes investment in new technologies, infrastructure, and training.
However, the long-term benefits in terms of efficiency, cost savings, and competitive advantage often justify these initial expenditures.
The Future of Manufacturing: A Digital-Physical Symbiosis
The convergence of DX and CPS is setting the stage for the next industrial revolution, often referred to as Industry 4.0.
In this era, manufacturing processes will become even more intelligent, interconnected, and responsive.
Advanced Automation
Future manufacturing systems will feature advanced levels of automation with minimal human intervention.
Self-organizing production lines, adaptive manufacturing processes, and autonomous logistics are just a few examples of what lies ahead.
Integrative Ecosystems
Manufacturers will collaborate within integrative ecosystems, where data is shared across the supply chain.
This transparency and collaboration will lead to improved efficiency, reduced waste, and better alignment with market demands.
Sustainable Manufacturing
The integration of DX and CPS will also drive sustainable manufacturing practices.
Real-time monitoring and optimization will reduce energy consumption and waste production.
Moreover, advanced analytics will support the development of eco-friendly products and processes.
In conclusion, DX and CPS are revolutionizing the manufacturing landscape.
By bridging the gap between the digital and physical worlds, these technologies are fostering innovation and efficiency.
As we look to the future, manufacturers that embrace these advancements will be well-positioned for success in an increasingly competitive and complex market.
資料ダウンロード
QCD調達購買管理クラウド「newji」は、調達購買部門で必要なQCD管理全てを備えた、現場特化型兼クラウド型の今世紀最高の購買管理システムとなります。
ユーザー登録
調達購買業務の効率化だけでなく、システムを導入することで、コスト削減や製品・資材のステータス可視化のほか、属人化していた購買情報の共有化による内部不正防止や統制にも役立ちます。
NEWJI DX
製造業に特化したデジタルトランスフォーメーション(DX)の実現を目指す請負開発型のコンサルティングサービスです。AI、iPaaS、および先端の技術を駆使して、製造プロセスの効率化、業務効率化、チームワーク強化、コスト削減、品質向上を実現します。このサービスは、製造業の課題を深く理解し、それに対する最適なデジタルソリューションを提供することで、企業が持続的な成長とイノベーションを達成できるようサポートします。
オンライン講座
製造業、主に購買・調達部門にお勤めの方々に向けた情報を配信しております。
新任の方やベテランの方、管理職を対象とした幅広いコンテンツをご用意しております。
お問い合わせ
コストダウンが利益に直結する術だと理解していても、なかなか前に進めることができない状況。そんな時は、newjiのコストダウン自動化機能で大きく利益貢献しよう!
(Β版非公開)