- お役立ち記事
- DX and Virtual Reality in Small and Medium Manufacturing: Immersive Training and Product Design Innovation
DX and Virtual Reality in Small and Medium Manufacturing: Immersive Training and Product Design Innovation
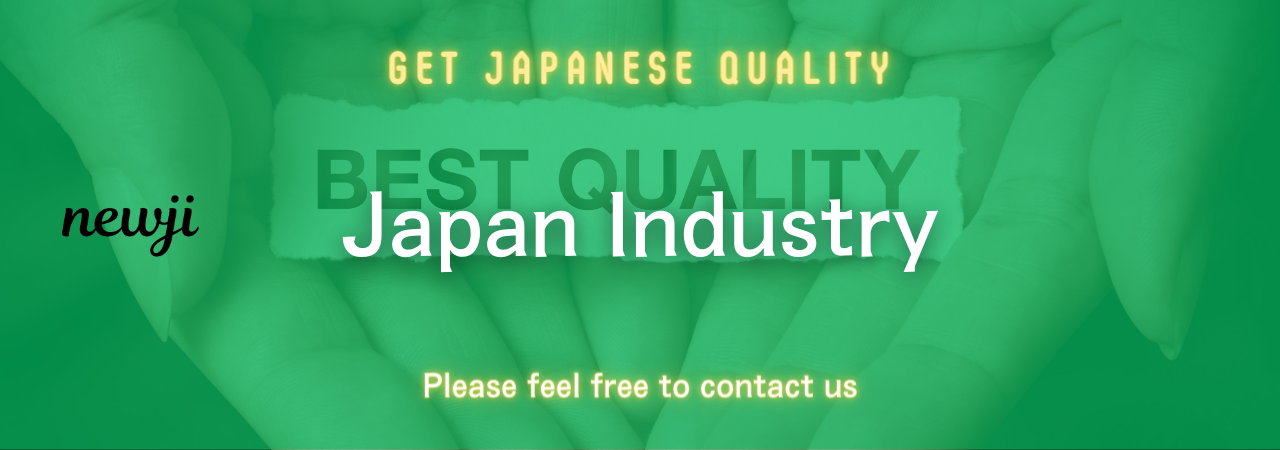
In recent years, the world of manufacturing has seen groundbreaking advancements in technology, particularly with digital transformation (DX) and virtual reality (VR).
For small and medium-sized manufacturing businesses, these innovations present exciting opportunities to enhance training processes and revolutionize product design.
This article explores how DX and VR are making waves in the industry, allowing businesses to stay ahead of the curve while cutting costs and boosting efficiency.
目次
The Power of Digital Transformation (DX)
Digital transformation involves integrating digital technologies into all aspects of a business, fundamentally changing how operations are conducted and delivering value to customers.
For small and medium-sized manufacturers, DX can take many forms, from automation and data analytics to cloud computing and advanced robotics.
One primary benefit of DX in manufacturing is the ability to streamline operations.
By using digital tools to automate routine tasks, manufacturers can reduce human error, improve precision, and free up staff to focus on more complex issues.
This leads to faster production times and a more agile manufacturing process.
Furthermore, DX provides manufacturers with valuable data insights.
By analyzing data from various sources, businesses can make more informed decisions, optimize inventory management, and predict maintenance needs before equipment failures occur.
This proactive approach minimizes downtime and enhances overall productivity.
Virtual Reality (VR) and Its Impact on Manufacturing
Virtual reality, often associated with gaming and entertainment, is making significant strides in the manufacturing sector.
VR technology enables the creation of immersive, three-dimensional simulations that can mimic real-world environments.
This capability has far-reaching implications for both training and product design.
Immersive Training Programs
One of the most exciting applications of VR in manufacturing is its use in training programs.
Traditional training methods often involve static materials such as manuals, presentations, or videos.
With VR, however, trainees can experience hands-on learning in a safe and controlled environment.
For example, a production line worker can use a VR headset to virtually navigate the entire manufacturing process.
They can interact with machinery, practice assembly techniques, and even troubleshoot potential issues, all without the risks associated with real-life exposure.
This immersive training reduces the learning curve, increases retention, and ensures workers are well-prepared for their roles.
Moreover, VR training can be customized to suit individual needs.
If a worker requires more practice on a specific task, the VR program can offer repeated training sessions until they achieve mastery.
This flexibility contrasts sharply with one-size-fits-all training approaches, ensuring each employee receives the attention necessary for success.
Revolutionizing Product Design
Another transformative application of VR in manufacturing lies in product design.
Traditionally, product development involves creating physical prototypes, which can be time-consuming and costly.
VR technology allows designers to create and manipulate virtual prototypes, significantly speeding up the design process.
With VR, designers can visualize products in three dimensions, make real-time modifications, and assess the feasibility of their designs before any physical production occurs.
This not only saves time and resources but also fosters more innovative solutions.
Designers can experiment with various iterations, explore alternative materials, and make data-driven decisions to enhance product performance.
Moreover, VR enables collaboration across different teams.
Design, engineering, and marketing teams can all view and interact with the virtual prototype simultaneously, facilitating better communication and ensuring everyone is aligned throughout the development process.
This collaborative approach reduces misunderstandings, accelerates decision-making, and results in more refined products.
Implementing DX and VR in Small and Medium Manufacturing
While the benefits of DX and VR are clear, small and medium-sized manufacturers may face challenges in implementation.
Limited budgets and resources can make it difficult to adopt new technologies.
However, several strategies can help overcome these barriers.
Start Small and Scale Gradually
It’s essential for businesses to start with manageable projects when implementing DX and VR.
Piloting small initiatives allows manufacturers to test the waters, identify potential issues, and learn from the experience without a significant financial commitment.
Successful projects can then be scaled up gradually.
Seek External Expertise
Collaborating with technology providers and consultants who specialize in DX and VR can be highly beneficial.
These experts can offer guidance, provide training, and ensure that the chosen solutions are tailored to the business’s specific needs.
External support can accelerate the adoption process and maximize the return on investment.
Leverage Government and Industry Programs
Many governments and industry organizations offer grants, subsidies, and programs to support digital transformation in manufacturing.
By leveraging these resources, small and medium-sized manufacturers can access financial support, training opportunities, and networking platforms to facilitate their DX and VR initiatives.
Future Prospects and Conclusion
The integration of DX and VR in small and medium manufacturing is just the beginning.
As technology continues to evolve, we can expect even more sophisticated tools and applications that push the boundaries of what’s possible.
For example, advancements in artificial intelligence (AI) and machine learning could further enhance predictive maintenance and quality control.
Similarly, augmented reality (AR) could complement VR by overlaying digital information onto the physical environment, providing real-time guidance to workers on the production floor.
In conclusion, digital transformation and virtual reality offer small and medium manufacturing businesses unparalleled opportunities to enhance training, streamline operations, and revolutionize product design.
While challenges exist, strategic implementation, external expertise, and leveraging available resources can pave the way for success.
By embracing these innovations, manufacturers can stay competitive, respond to market demands more effectively, and drive growth in an increasingly digital world.
資料ダウンロード
QCD調達購買管理クラウド「newji」は、調達購買部門で必要なQCD管理全てを備えた、現場特化型兼クラウド型の今世紀最高の購買管理システムとなります。
ユーザー登録
調達購買業務の効率化だけでなく、システムを導入することで、コスト削減や製品・資材のステータス可視化のほか、属人化していた購買情報の共有化による内部不正防止や統制にも役立ちます。
NEWJI DX
製造業に特化したデジタルトランスフォーメーション(DX)の実現を目指す請負開発型のコンサルティングサービスです。AI、iPaaS、および先端の技術を駆使して、製造プロセスの効率化、業務効率化、チームワーク強化、コスト削減、品質向上を実現します。このサービスは、製造業の課題を深く理解し、それに対する最適なデジタルソリューションを提供することで、企業が持続的な成長とイノベーションを達成できるようサポートします。
オンライン講座
製造業、主に購買・調達部門にお勤めの方々に向けた情報を配信しております。
新任の方やベテランの方、管理職を対象とした幅広いコンテンツをご用意しております。
お問い合わせ
コストダウンが利益に直結する術だと理解していても、なかなか前に進めることができない状況。そんな時は、newjiのコストダウン自動化機能で大きく利益貢献しよう!
(Β版非公開)