- お役立ち記事
- DX Casting Process Reduces Casting Losses and Improves Material Yield
DX Casting Process Reduces Casting Losses and Improves Material Yield
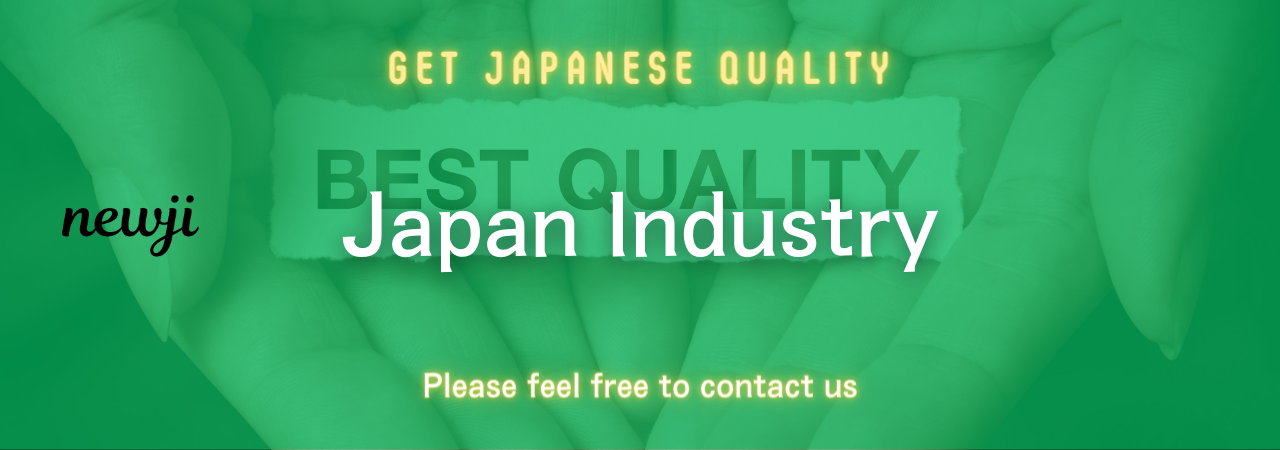
Traditional casting processes are a fundamental part of manufacturing and have been used for centuries to create intricate shapes from molten metal.
However, these processes often suffer from significant material losses, casting defects, and inefficient resource usage.
The digital transformation in casting, or DX casting, promises to revolutionize this age-old industry by making it more efficient, reducing waste, and improving material yield.
目次
What is DX Casting?
DX casting, or digital transformation casting, leverages advanced technologies such as big data, artificial intelligence (AI), and machine learning to improve casting processes.
By incorporating sensors, real-time data analytics, and automated feedback loops, manufacturers can optimize every stage of casting.
This results in higher quality products, reduced waste, and faster production times.
How Does DX Casting Process Work?
The DX casting process integrates digital tools to monitor and control various parameters throughout the casting cycle.
Here’s a breakdown of key components in DX casting:
1. Real-Time Data Collection
Sensors are embedded in casting equipment to collect data on temperature, pressure, and other critical parameters.
This data is collected in real-time and transmitted to a central monitoring system.
Real-time data collection helps identify deviations from optimal conditions immediately, allowing for quick adjustments.
2. Data Analysis and Optimization
Once data is collected, it is analyzed using AI and machine learning algorithms.
These algorithms can predict potential issues, such as defects or material weaknesses, before they occur.
By identifying these issues early on, manufacturers can make informed decisions to adjust the process and avoid losses.
3. Automated Feedback Loops
The insights gained from data analysis are fed back into the system.
Automated feedback loops enable the casting equipment to self-correct by adjusting parameters like temperature or cooling rates.
This ensures that the casting process remains within optimal conditions, reducing the likelihood of defects and material waste.
4. Predictive Maintenance
DX casting can also help in predictive maintenance of equipment.
By monitoring equipment health in real-time and analyzing historical data, manufacturers can predict when machinery might fail or need maintenance.
This proactive approach helps in reducing downtime and extending the life of casting equipment.
Benefits of DX Casting
The adoption of DX casting offers numerous benefits to manufacturers:
1. Reduced Material Waste
Traditional casting processes often result in a significant amount of material waste due to defects and inefficiencies.
DX casting minimizes these losses by ensuring optimal process conditions, thereby improving material yield.
2. Improved Product Quality
By utilizing real-time monitoring and advanced analytics, DX casting significantly enhances product quality.
Defects are detected and rectified early, resulting in finished products that meet higher quality standards.
3. Increased Efficiency
DX casting optimizes the entire casting process, from start to finish.
This leads to shorter production cycles and increased efficiency, ultimately reducing costs and time-to-market for products.
4. Enhanced Sustainability
Reducing material waste and improving efficiency contribute to more sustainable manufacturing processes.
DX casting helps manufacturers lower their environmental footprint by minimizing resource consumption and waste generation.
5. Cost Savings
While the initial investment in DX casting technology can be significant, the long-term cost savings are substantial.
Reduced material waste, improved product quality, and increased efficiency all contribute to lower operational costs.
Case Studies of DX Casting Implementation
Several companies have successfully implemented DX casting and reaped the benefits.
Here are a couple of examples:
Example 1: Automotive Industry
An automotive manufacturer integrated DX casting into its production lines to produce engine components.
By monitoring and optimizing temperature and pressure conditions, the company significantly reduced defect rates.
This led to fewer rejections and reworks, ultimately improving material yield and lowering costs.
Example 2: Aerospace Industry
An aerospace company utilized DX casting to manufacture turbine blades with complex geometries.
The advanced analytics and real-time monitoring enabled precise control over the casting process.
As a result, the company achieved higher quality blades with reduced material waste and improved overall efficiency.
The Future of DX Casting
The future of DX casting looks promising as more manufacturers recognize its benefits and invest in digital technologies.
Continuous advancements in AI, machine learning, and IoT (Internet of Things) will further enhance the capabilities of DX casting.
In addition, increased adoption of Industry 4.0 principles will drive the integration of digital tools across all aspects of manufacturing.
Emerging technologies such as digital twins, which create virtual replicas of casting processes, will allow manufacturers to simulate and optimize operations before actual production.
This will further reduce material losses and improve material yield.
Conclusion
The DX casting process offers a transformative approach to traditional casting techniques.
By leveraging real-time data, advanced analytics, and automated feedback loops, manufacturers can significantly reduce material losses and improve material yield.
As more companies adopt DX casting, the industry will move toward more efficient, sustainable, and cost-effective manufacturing processes.
With its numerous benefits, DX casting is poised to become the standard in modern manufacturing, paving the way for a future where resource efficiency and product quality are paramount.
資料ダウンロード
QCD調達購買管理クラウド「newji」は、調達購買部門で必要なQCD管理全てを備えた、現場特化型兼クラウド型の今世紀最高の購買管理システムとなります。
ユーザー登録
調達購買業務の効率化だけでなく、システムを導入することで、コスト削減や製品・資材のステータス可視化のほか、属人化していた購買情報の共有化による内部不正防止や統制にも役立ちます。
NEWJI DX
製造業に特化したデジタルトランスフォーメーション(DX)の実現を目指す請負開発型のコンサルティングサービスです。AI、iPaaS、および先端の技術を駆使して、製造プロセスの効率化、業務効率化、チームワーク強化、コスト削減、品質向上を実現します。このサービスは、製造業の課題を深く理解し、それに対する最適なデジタルソリューションを提供することで、企業が持続的な成長とイノベーションを達成できるようサポートします。
オンライン講座
製造業、主に購買・調達部門にお勤めの方々に向けた情報を配信しております。
新任の方やベテランの方、管理職を対象とした幅広いコンテンツをご用意しております。
お問い合わせ
コストダウンが利益に直結する術だと理解していても、なかなか前に進めることができない状況。そんな時は、newjiのコストダウン自動化機能で大きく利益貢献しよう!
(Β版非公開)