- お役立ち記事
- DX conversion of chemical plants and introduction of real-time quality control
月間77,185名の
製造業ご担当者様が閲覧しています*
*2025年2月28日現在のGoogle Analyticsのデータより
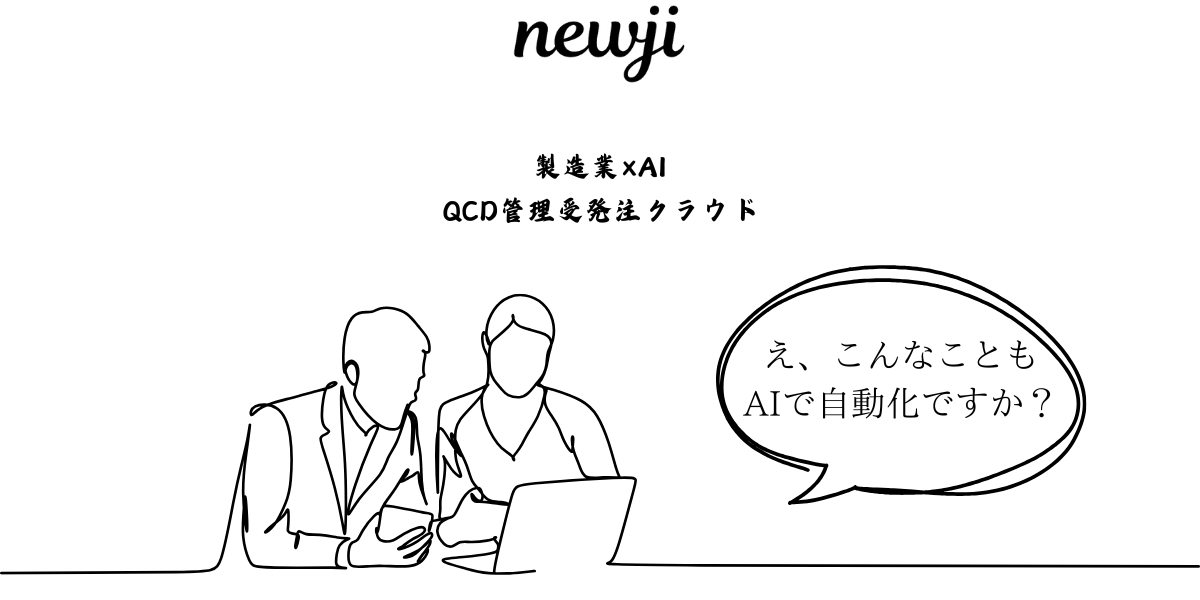
DX conversion of chemical plants and introduction of real-time quality control
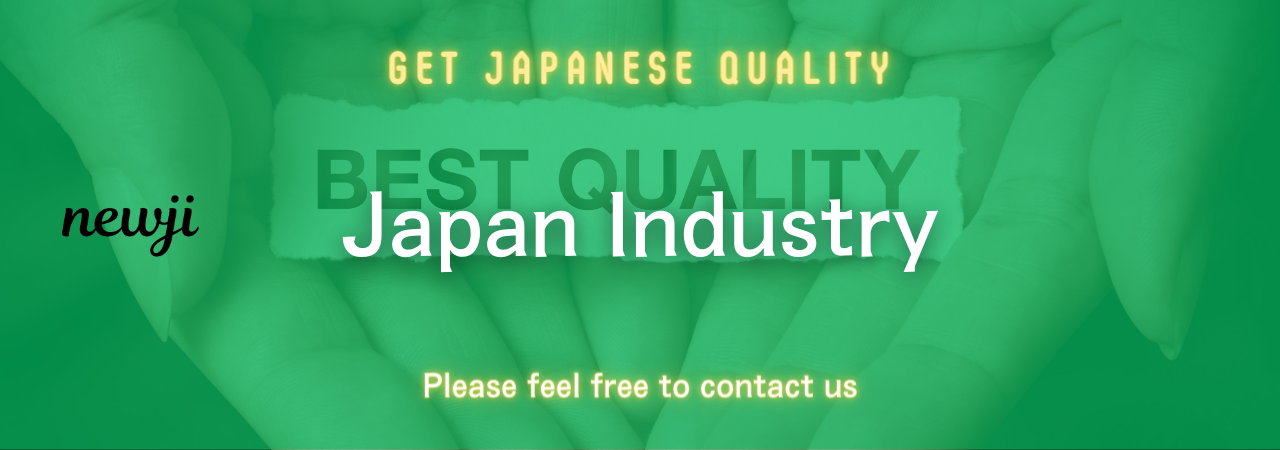
目次
Understanding DX Conversion in Chemical Plants
Digital Transformation, often abbreviated as DX, has been a buzzword across numerous industries for the past few years.
In the realm of chemical plants, this transformation is nothing short of revolutionary.
The primary goal of DX is to enhance operational efficiency, reduce risks, and ultimately boost productivity and profitability.
For chemical plants, this involves integrating digital technologies into every aspect of the process, ranging from manufacturing to quality control.
Implementing DX in chemical plants encompasses adopting advanced technologies such as the Internet of Things (IoT), artificial intelligence (AI), big data analytics, and cloud computing.
By harnessing these technologies, chemical plants can optimize workflows, reduce downtime, and enhance safety measures.
They can also use predictive analytics to foresee potential machinery failures or identify areas where operational improvements can be made.
The Role of Real-Time Quality Control
A crucial component of DX conversion in chemical plants is the introduction of real-time quality control.
Real-time quality control refers to the continuous monitoring and assessment of manufacturing processes as they occur.
This proactive approach allows plant operators to ensure that products meet strict industry standards without waiting until the end of the production line to catch defects.
In traditional chemical plants, quality checks are often conducted at the end of the manufacturing process.
However, real-time quality control shifts this paradigm, allowing operators to address issues as they arise, minimizing waste and improving overall product quality.
This approach also enables the identification of variations in production, allowing for immediate corrective actions.
Benefits of Real-Time Quality Control in Chemical Plants
The advantages of integrating real-time quality control through DX conversion in chemical plants are manifold.
One of the most significant benefits is the marked reduction in waste.
By catching defects early in the production process, plants can minimize the number of products that need to be discarded or reworked.
This not only conserves resources but also leads to cost savings.
Moreover, real-time quality control can lead to improved product consistency.
In industries where precision and uniformity are paramount, such as pharmaceuticals or specialty chemicals, ensuring consistent quality is critical.
Real-time monitoring allows for adjustments to be made during production, ensuring that each batch meets the required specifications.
Another notable benefit is enhanced decision-making capabilities.
With real-time data at their fingertips, plant managers can make informed decisions quickly.
This agility is crucial in today’s fast-paced, competitive market.
Furthermore, the integration of AI and machine learning algorithms can provide predictive insights, suggesting potential solutions for identified issues.
Challenges in Implementing DX and Real-Time Quality Control
While the benefits are substantial, the implementation of DX and real-time quality control in chemical plants is not without challenges.
One of the primary hurdles is the initial investment required for adopting new technologies.
This includes the cost of new hardware, software, employee training, and maintenance.
Additionally, integrating these digital systems with existing legacy systems can pose technical challenges.
Many chemical plants have been operating for years, if not decades, and overhauling established systems requires careful planning and execution to avoid disruptions.
Furthermore, there is a significant cultural shift involved.
Employees need to be trained not only on new tools and systems but also on the importance of embracing technology-driven change.
There might be resistance from some quarters, particularly among those who are accustomed to traditional processes.
Data security is another concern.
With the increased reliance on digital systems and cloud-based solutions, safeguarding sensitive data from cyber threats becomes a critical priority for chemical plants.
Steps to Successful DX Conversion and Real-Time Quality Control Implementation
To successfully navigate the challenges and embrace the future of chemical manufacturing, there are several key steps that plants can take.
Firstly, a comprehensive assessment of current processes and systems should be conducted.
Understanding the existing operational landscape is vital to identify areas that would benefit the most from DX conversion and real-time quality control.
Secondly, developing a clear implementation roadmap is crucial.
This plan should outline the technologies to be adopted, the timeline for implementation, and the expected outcomes.
It’s essential for chemical plants to set realistic goals and benchmarks to measure the success of the transformation.
Engaging with technology partners can also facilitate a smoother transition.
Working with experts in IoT, AI, and cloud computing can provide chemical plants with vital insights and support throughout the process.
Employee training is another critical step.
By equipping staff with the knowledge and skills required to operate new systems, chemical plants can ensure a smoother transition and promote a culture of continuous improvement.
Finally, an ongoing monitoring and evaluation framework should be established.
This allows plants to assess the impact of DX conversion and real-time quality control systems, ensuring they are meeting their intended goals and making necessary adjustments along the way.
The Future of Chemical Plants with DX and Real-Time Quality Control
As chemical plants continue to embrace digital transformation and adopt real-time quality control measures, the industry is expected to become more efficient, sustainable, and competitive.
These technological advancements hold the key to unlocking new opportunities, from discovering innovative product formulations to enhancing supply chain resilience.
The adoption of DX and real-time quality control will shape the future of chemical manufacturing, creating facilities that are not just producers but innovators in their field.
Ultimately, those who embrace these changes are likely to gain a significant advantage in the marketplace, positioning themselves as leaders in the constantly evolving industrial landscape.
資料ダウンロード
QCD管理受発注クラウド「newji」は、受発注部門で必要なQCD管理全てを備えた、現場特化型兼クラウド型の今世紀最高の受発注管理システムとなります。
ユーザー登録
受発注業務の効率化だけでなく、システムを導入することで、コスト削減や製品・資材のステータス可視化のほか、属人化していた受発注情報の共有化による内部不正防止や統制にも役立ちます。
NEWJI DX
製造業に特化したデジタルトランスフォーメーション(DX)の実現を目指す請負開発型のコンサルティングサービスです。AI、iPaaS、および先端の技術を駆使して、製造プロセスの効率化、業務効率化、チームワーク強化、コスト削減、品質向上を実現します。このサービスは、製造業の課題を深く理解し、それに対する最適なデジタルソリューションを提供することで、企業が持続的な成長とイノベーションを達成できるようサポートします。
製造業ニュース解説
製造業、主に購買・調達部門にお勤めの方々に向けた情報を配信しております。
新任の方やベテランの方、管理職を対象とした幅広いコンテンツをご用意しております。
お問い合わせ
コストダウンが利益に直結する術だと理解していても、なかなか前に進めることができない状況。そんな時は、newjiのコストダウン自動化機能で大きく利益貢献しよう!
(β版非公開)