- お役立ち記事
- DX conversion of chemical plants and real-time optimization of processes
月間77,185名の
製造業ご担当者様が閲覧しています*
*2025年2月28日現在のGoogle Analyticsのデータより
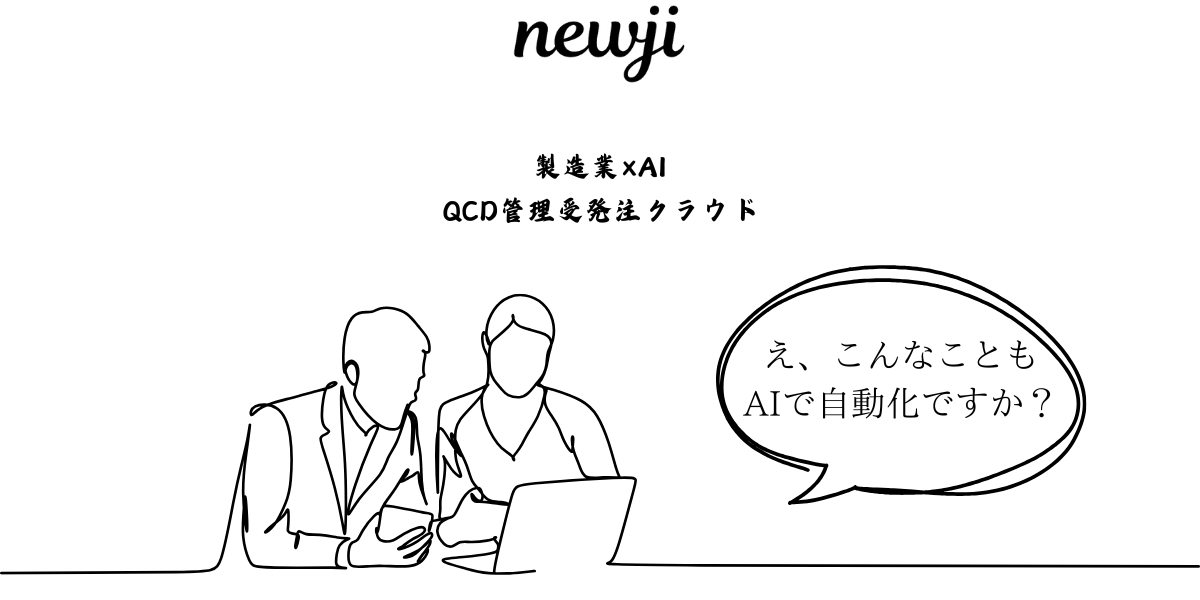
DX conversion of chemical plants and real-time optimization of processes
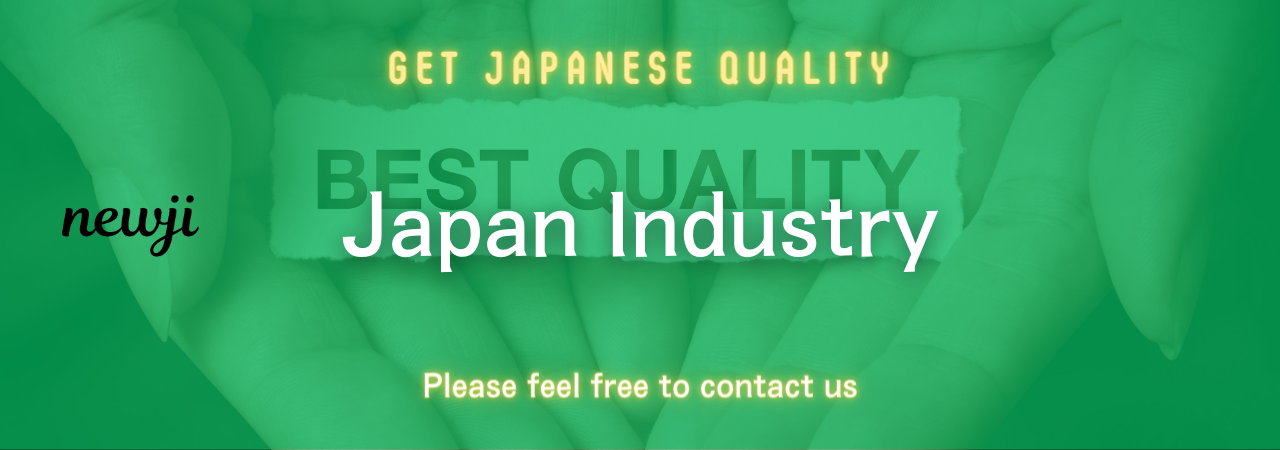
目次
Introduction to DX in Chemical Plants
Digital transformation, often abbreviated as DX, is revolutionizing industries across the globe.
In particular, the chemical industry is embracing this shift to enhance operational efficiency and optimize processes.
The DX conversion of chemical plants is paramount in achieving these goals.
By integrating digital technologies, chemical plants can streamline operations, reduce waste, and improve productivity.
The Importance of DX Conversion
The need for DX in chemical plants cannot be overstated.
In an industry characterized by complex processes and stringent regulatory standards, leveraging digital technologies can lead to significant advantages.
The primary objective of DX conversion is to harness data-driven insights to make informed decisions.
This capability is essential in optimizing chemical processes and ensuring safe and efficient plant operations.
Enhanced Data Collection and Analysis
One of the critical aspects of DX conversion is the improved capacity for data collection and analysis.
Chemical plants generate massive amounts of data daily.
Through digital transformation, this data can be captured in real-time and analyzed to reveal patterns, trends, and opportunities for improvement.
Advanced analytics tools enable plant operators to identify process inefficiencies and take corrective actions swiftly.
Risk Management and Safety Improvements
Safety is a top priority in any chemical plant.
DX conversion can significantly enhance risk management procedures.
By using predictive analytics and machine learning algorithms, potential hazards can be identified before they lead to incidents.
This proactive approach not only protects the workforce but also ensures compliance with safety regulations.
Real-Time Process Optimization
Real-time optimization of chemical processes is a game-changer for the industry.
It involves making continuous adjustments to processes based on live data to maximize efficiency.
With real-time optimization, chemical plants can respond promptly to changes in raw material quality, market demand, and production constraints.
The Role of IoT and Automation
The Internet of Things (IoT) and automation are crucial components of real-time process optimization.
IoT devices equipped with sensors provide continuous data feeds on process variables such as temperature, pressure, and flow rates.
Automation systems use this data to maintain optimal operating conditions, minimizing human intervention and error.
Benefits of Real-Time Optimization
The benefits of real-time optimization are numerous.
For starters, it leads to reduced energy consumption and lower operating costs.
By optimizing resource use, chemical plants can minimize waste and environmental impact.
Moreover, real-time optimization ensures consistent product quality, thereby enhancing customer satisfaction and competitive advantage.
Challenges in DX Conversion
While the benefits of DX conversion and real-time process optimization are clear, the journey is not without its challenges.
Implementing these digital solutions requires a significant investment in technology and infrastructure.
Additionally, there is a need for workforce training to ensure employees can effectively leverage the new technologies.
Data Security and Privacy Concerns
Data security is a major concern in the age of digital transformation.
As chemical plants become more connected, the risk of cyber-attacks increases.
It is crucial to implement robust cybersecurity measures to protect sensitive data and ensure the integrity of operations.
Integration with Legacy Systems
Many chemical plants operate with legacy systems that may not be compatible with new digital technologies.
Integration of these systems with modern solutions can be complex and may require customized approaches.
However, bridging the gap between old and new systems is essential for seamless digital transformation.
The Future of Chemical Plants
The digital transformation of chemical plants marks the beginning of a new era in the industry.
Looking forward, the integration of artificial intelligence and advanced analytics is expected to take process optimization to new heights.
As technologies continue to evolve, chemical plants must remain agile and adaptable to maintain a competitive edge.
The Role of Collaboration
Collaboration between technology providers, industry experts, and regulatory bodies is key to successful DX conversion.
By working together, stakeholders can develop innovative solutions that meet the specific needs of the chemical industry.
This collaborative approach will ensure sustainable growth and development in the long run.
Commitment to Sustainability
Sustainability is a critical consideration for the future of the chemical industry.
Digital transformation offers opportunities to reduce environmental impact and promote eco-friendly practices.
By optimizing processes and reducing waste, chemical plants can contribute to a more sustainable future.
Conclusion
In conclusion, the DX conversion of chemical plants and real-time optimization of processes is essential for the industry’s growth and success.
While challenges exist, the benefits of improved safety, efficiency, and sustainability outweigh the hurdles.
By embracing digital technologies, chemical plants can transform their operations and pave the way for a brighter future.
資料ダウンロード
QCD管理受発注クラウド「newji」は、受発注部門で必要なQCD管理全てを備えた、現場特化型兼クラウド型の今世紀最高の受発注管理システムとなります。
ユーザー登録
受発注業務の効率化だけでなく、システムを導入することで、コスト削減や製品・資材のステータス可視化のほか、属人化していた受発注情報の共有化による内部不正防止や統制にも役立ちます。
NEWJI DX
製造業に特化したデジタルトランスフォーメーション(DX)の実現を目指す請負開発型のコンサルティングサービスです。AI、iPaaS、および先端の技術を駆使して、製造プロセスの効率化、業務効率化、チームワーク強化、コスト削減、品質向上を実現します。このサービスは、製造業の課題を深く理解し、それに対する最適なデジタルソリューションを提供することで、企業が持続的な成長とイノベーションを達成できるようサポートします。
製造業ニュース解説
製造業、主に購買・調達部門にお勤めの方々に向けた情報を配信しております。
新任の方やベテランの方、管理職を対象とした幅広いコンテンツをご用意しております。
お問い合わせ
コストダウンが利益に直結する術だと理解していても、なかなか前に進めることができない状況。そんな時は、newjiのコストダウン自動化機能で大きく利益貢献しよう!
(β版非公開)