- お役立ち記事
- DX for Drilling Machine Processes Dramatically Improves Ability to Handle Small Lot Production
DX for Drilling Machine Processes Dramatically Improves Ability to Handle Small Lot Production
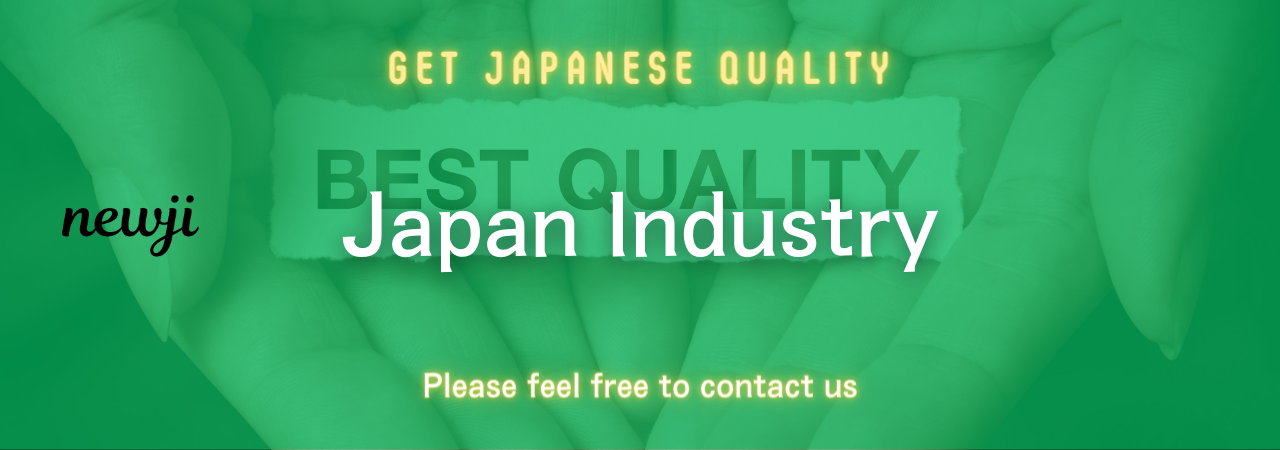
In the modern manufacturing landscape, the ability to adapt and respond to smaller production quantities is critical.
This is particularly true for companies utilizing drilling machines in their processes.
Digital Transformation (DX) has brought about significant advancements in this area, dramatically improving the efficiency and capabilities of drilling machine operations when dealing with small-lot production.
目次
Understanding Digital Transformation in Drilling Processes
Digital Transformation, often abbreviated as DX, involves integrating digital technology into every aspect of a business, fundamentally changing how operations are conducted and how value is delivered to customers.
In the context of drilling machine processes, DX encompasses the use of advanced software, automation, and data analytics to optimize production workflows.
By harnessing these technologies, manufacturers can achieve greater precision, reduce downtime, and enhance flexibility.
This transformation is vital for small-lot production, where each unit may require different specifications and rapid adjustments.
The Challenges of Small Lot Production
Before diving into the benefits of DX, it’s essential to understand the challenges associated with small-lot production.
Traditional manufacturing models are often geared towards large-scale production, where the same item is produced in high volumes.
This approach can lead to significant inefficiencies when dealing with smaller orders.
Switching between different product specifications can result in extended setup times, increased material waste, and elevated costs.
Moreover, the risk of human error is higher when frequent changes are required, potentially compromising quality and consistency.
All these factors make small-lot production challenging without the aid of advanced technologies.
How DX Enhances Drilling Machine Processes for Small Lots
Automated Setup and Configuration
One of the primary ways DX improves drilling machine processes is through automated setup and configuration.
Advanced software can store various product specifications and automatically adjust machine settings based on the specific requirements of each lot.
This capability drastically reduces the time and effort needed to switch between different products, minimizing downtime and enhancing productivity.
Real-time Monitoring and Data Analytics
Real-time monitoring and data analytics play a crucial role in optimizing drilling processes.
Sensors and IoT (Internet of Things) devices can gather data from drilling machines and provide insights into their performance.
Analyzing this data helps identify potential issues before they lead to significant problems, allowing for proactive maintenance and reducing unexpected downtime.
Additionally, data analytics can reveal patterns and trends, helping manufacturers make informed decisions about process improvements and resource allocation.
Enhanced Precision and Quality Control
Digital Transformation enables enhanced precision and quality control in drilling operations.
Advanced control systems and software can achieve higher levels of accuracy, ensuring that each hole is drilled to the exact specifications required.
This precision is particularly important for small-lot production, where even minor deviations can result in defective products.
Moreover, automated inspection systems can detect anomalies and ensure that each unit meets quality standards, reducing the likelihood of defects and rework.
Improved Flexibility and Adaptability
One of the most significant advantages of DX is the improved flexibility and adaptability it offers.
Manufacturers can quickly respond to changing customer demands and market conditions.
For example, if a new order requires a different hole size or pattern, digital systems can swiftly adjust machine settings and execute the new requirements.
This adaptability is invaluable for small-lot production, where customization and rapid changes are often necessary.
Case Studies: Success Stories of DX in Drilling Machine Processes
Leading Aerospace Manufacturer
A leading aerospace manufacturer implemented a comprehensive DX strategy for its drilling machine operations.
By integrating advanced software and automation, the company reduced setup times by 60%, significantly increasing its ability to handle small-lot production.
Real-time monitoring and predictive maintenance reduced downtime by 40%, enhancing overall efficiency.
The result was improved product quality, greater customer satisfaction, and a substantial reduction in operational costs.
Automotive Supplier
An automotive supplier faced challenges with frequent product changes and small order volumes.
By adopting DX technologies, the company achieved seamless transitions between different products, reducing setup times by 50%.
Advanced analytics provided insights into machine performance, leading to a 30% reduction in maintenance costs.
The company also saw a 20% improvement in product quality, thanks to enhanced precision and automated quality control systems.
Implementing DX: Steps for Manufacturers
Assess Current Processes
The first step in implementing DX is to assess current drilling machine processes.
Identify areas where digital technologies can bring about improvements, such as setup times, quality control, and maintenance.
Understanding these pain points will help prioritize the implementation efforts.
Invest in Technology
Investing in the right technology is crucial for successful DX implementation.
This may include advanced software, IoT devices, sensors, and automation systems.
Partnering with technology providers who specialize in manufacturing solutions can ensure that the chosen technologies align with specific business needs.
Train Employees
Equipping employees with the necessary skills to operate and maintain new digital systems is essential.
Training programs should cover system usage, data analytics, and troubleshooting.
Engaging employees in the DX journey ensures a smoother transition and maximizes the benefits of the new technologies.
Monitor and Optimize
Continuous monitoring and optimization are vital for long-term success.
Regularly review data and performance metrics to identify areas for further improvement.
Stay updated with the latest advancements in digital manufacturing to keep processes efficient and competitive.
Digital Transformation for drilling machine processes offers numerous benefits, especially in handling small-lot production.
Automated setup and configuration, real-time monitoring, enhanced precision, and improved flexibility are just some of the advantages.
Case studies from aerospace and automotive sectors demonstrate the successful implementation and outcomes of DX strategies.
By assessing current processes, investing in technology, training employees, and continuously optimizing, manufacturers can unlock significant efficiencies and remain competitive in an ever-evolving market.
資料ダウンロード
QCD調達購買管理クラウド「newji」は、調達購買部門で必要なQCD管理全てを備えた、現場特化型兼クラウド型の今世紀最高の購買管理システムとなります。
ユーザー登録
調達購買業務の効率化だけでなく、システムを導入することで、コスト削減や製品・資材のステータス可視化のほか、属人化していた購買情報の共有化による内部不正防止や統制にも役立ちます。
NEWJI DX
製造業に特化したデジタルトランスフォーメーション(DX)の実現を目指す請負開発型のコンサルティングサービスです。AI、iPaaS、および先端の技術を駆使して、製造プロセスの効率化、業務効率化、チームワーク強化、コスト削減、品質向上を実現します。このサービスは、製造業の課題を深く理解し、それに対する最適なデジタルソリューションを提供することで、企業が持続的な成長とイノベーションを達成できるようサポートします。
オンライン講座
製造業、主に購買・調達部門にお勤めの方々に向けた情報を配信しております。
新任の方やベテランの方、管理職を対象とした幅広いコンテンツをご用意しております。
お問い合わせ
コストダウンが利益に直結する術だと理解していても、なかなか前に進めることができない状況。そんな時は、newjiのコストダウン自動化機能で大きく利益貢献しよう!
(Β版非公開)