- お役立ち記事
- DX in Electroless Nickel Plating Realizes High Corrosion Resistance and Improved Productivity
DX in Electroless Nickel Plating Realizes High Corrosion Resistance and Improved Productivity
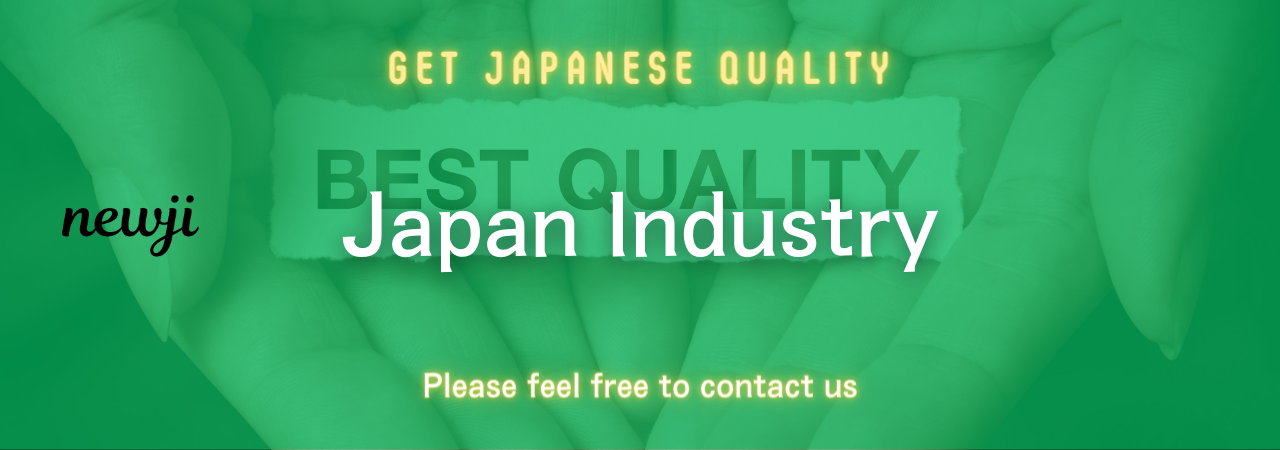
In the modern age of industrial advancements and technological breakthroughs, digital transformation (DX) is emerging as a pivotal force across various sectors.
One such area experiencing significant benefits from DX is electroless nickel plating.
Widely adopted in the manufacturing industry, electroless nickel plating has long been praised for its corrosion resistance, uniform coating, and versatility.
However, with the integration of DX, the process has not only enhanced corrosion resistance further but also significantly boosted productivity.
目次
Understanding Electroless Nickel Plating
Electroless nickel plating is a chemical process used to deposit a layer of nickel-phosphorus alloy onto a substrate without the need for an external electric current.
This method provides a uniform coating even on complex geometries, making it highly desirable in various industries such as automotive, electronics, and aerospace.
The primary advantages of this technique include excellent corrosion resistance, hardness, and wear resistance.
Despite these benefits, traditional electroless nickel plating processes can be time-consuming and require meticulous attention to detail.
The Role of Digital Transformation
Digital transformation involves the integration of digital technology into all areas of business, fundamentally changing how operations are conducted and how value is delivered to customers.
When applied to electroless nickel plating, DX leverages technologies such as the Internet of Things (IoT), artificial intelligence (AI), and machine learning (ML) to enhance the efficiency and effectiveness of the plating process.
One of the key aspects of DX in electroless nickel plating is the use of IoT devices and sensors.
These tools enable real-time monitoring of the plating process, ensuring optimal conditions at all times.
By continuously collecting data on variables such as temperature, pH levels, and coating thickness, operators can make immediate adjustments to maintain the highest quality standards.
IoT and Real-Time Monitoring
The integration of IoT devices in electroless nickel plating allows for unprecedented levels of control and precision.
Sensors embedded in the plating baths and equipment provide real-time feedback on critical parameters.
This constant stream of data ensures that any deviations from the desired conditions are quickly identified and addressed.
For example, maintaining the correct temperature and pH levels is crucial for achieving a consistent and high-quality nickel coating.
With IoT sensors, these variables can be monitored continuously, and automated systems can make the necessary adjustments to keep them within the optimal range.
This level of control helps in reducing defects and ensuring uniform coating thickness, both of which play a vital role in enhancing corrosion resistance.
AI and Machine Learning for Predictive Maintenance
Another significant advantage of integrating DX in electroless nickel plating is the application of AI and ML for predictive maintenance.
Traditional maintenance practices often involve routine checks and reactive measures after a breakdown has occurred.
However, with AI-driven predictive maintenance, it is possible to anticipate potential issues before they lead to equipment failure or process disruptions.
Machine learning algorithms analyze historical data from the plating process and equipment to identify patterns that precede failures.
By understanding these patterns, the system can predict when a piece of equipment is likely to require maintenance, allowing for proactive interventions.
This not only minimizes downtime but also extends the lifespan of the equipment, resulting in significant cost savings and increased productivity.
Enhanced Corrosion Resistance
One of the most notable benefits of DX in electroless nickel plating is the dramatic improvement in corrosion resistance.
With real-time monitoring and precise control over the plating parameters, the quality and consistency of the nickel coating are significantly enhanced.
Furthermore, advanced data analytics enable a deeper understanding of the factors that influence corrosion resistance.
By analyzing the data collected during the plating process, manufacturers can identify the optimal combination of variables that yield the best corrosion-resistant properties.
This knowledge can then be used to refine and optimize the plating process, ensuring that the resulting nickel coating offers superior protection against corrosion.
Boosted Productivity
In addition to improving the quality of the nickel coating, DX also has a profound impact on the overall productivity of the electroless nickel plating process.
Automated monitoring and control systems streamline the process, reducing the need for manual interventions and oversight.
This leads to faster turnaround times and higher throughput, enabling manufacturers to meet increasing demand without compromising on quality.
Reduced Waste and Increased Efficiency
One of the key factors contributing to boosted productivity is the reduction in waste and rework.
Real-time monitoring and precise control ensure that the plating process is always operating at its optimal state.
This minimizes the occurrence of defects and rejects, leading to a higher yield of acceptable products.
Additionally, predictive maintenance helps in preventing unexpected equipment failures, which can cause significant downtime and production losses.
By addressing potential issues before they escalate, manufacturers can maintain a smooth and continuous production flow, further enhancing efficiency and productivity.
Scalability and Adaptability
DX also brings scalability and adaptability to the electroless nickel plating process.
As market demands fluctuate, manufacturers can quickly adjust their production capacity to match the requirements.
The digital systems in place allow for seamless scaling up or down without compromising on the quality of the nickel coating.
Moreover, the adaptability of digital systems means that manufacturers can easily integrate new technologies and processes as they become available.
This ensures that the electroless nickel plating process remains at the forefront of technological advancements, continuously benefiting from the latest innovations.
In conclusion, digital transformation is revolutionizing the field of electroless nickel plating.
By incorporating IoT, AI, and machine learning technologies, manufacturers can achieve higher levels of precision, control, and efficiency.
The result is a significant enhancement in corrosion resistance, boosted productivity, reduced waste, and increased efficiency.
As the manufacturing industry continues to embrace digital transformation, the future of electroless nickel plating looks brighter than ever.
資料ダウンロード
QCD調達購買管理クラウド「newji」は、調達購買部門で必要なQCD管理全てを備えた、現場特化型兼クラウド型の今世紀最高の購買管理システムとなります。
ユーザー登録
調達購買業務の効率化だけでなく、システムを導入することで、コスト削減や製品・資材のステータス可視化のほか、属人化していた購買情報の共有化による内部不正防止や統制にも役立ちます。
NEWJI DX
製造業に特化したデジタルトランスフォーメーション(DX)の実現を目指す請負開発型のコンサルティングサービスです。AI、iPaaS、および先端の技術を駆使して、製造プロセスの効率化、業務効率化、チームワーク強化、コスト削減、品質向上を実現します。このサービスは、製造業の課題を深く理解し、それに対する最適なデジタルソリューションを提供することで、企業が持続的な成長とイノベーションを達成できるようサポートします。
オンライン講座
製造業、主に購買・調達部門にお勤めの方々に向けた情報を配信しております。
新任の方やベテランの方、管理職を対象とした幅広いコンテンツをご用意しております。
お問い合わせ
コストダウンが利益に直結する術だと理解していても、なかなか前に進めることができない状況。そんな時は、newjiのコストダウン自動化機能で大きく利益貢献しよう!
(Β版非公開)