- お役立ち記事
- DX in Line Balancing Reduces Production Losses and Improves Capacity Utilization
月間76,176名の
製造業ご担当者様が閲覧しています*
*2025年3月31日現在のGoogle Analyticsのデータより
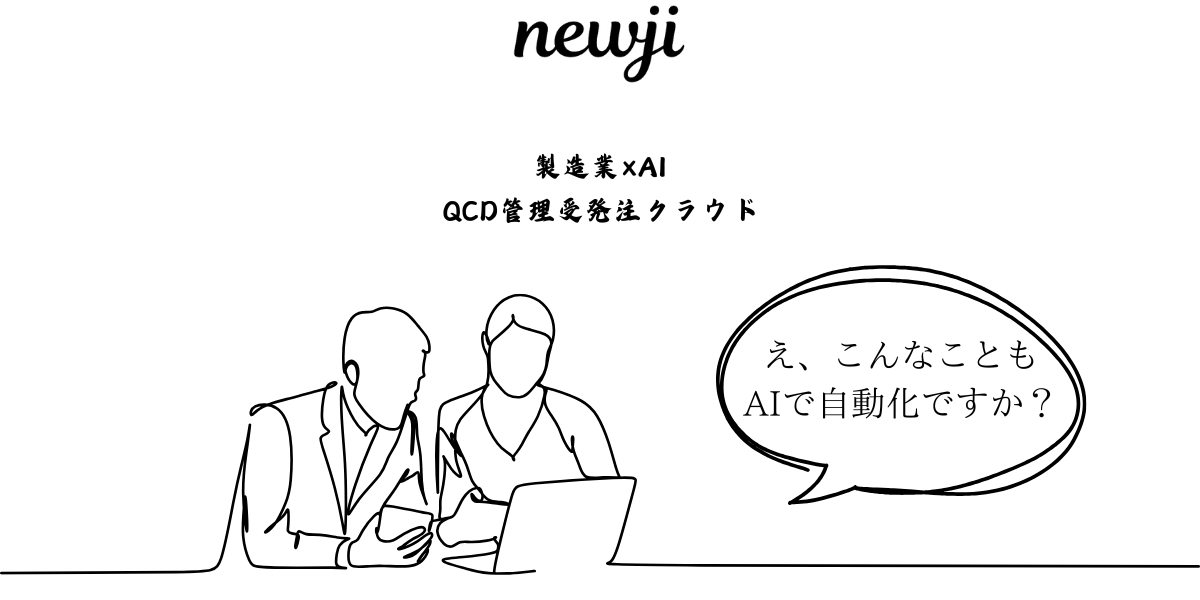
DX in Line Balancing Reduces Production Losses and Improves Capacity Utilization
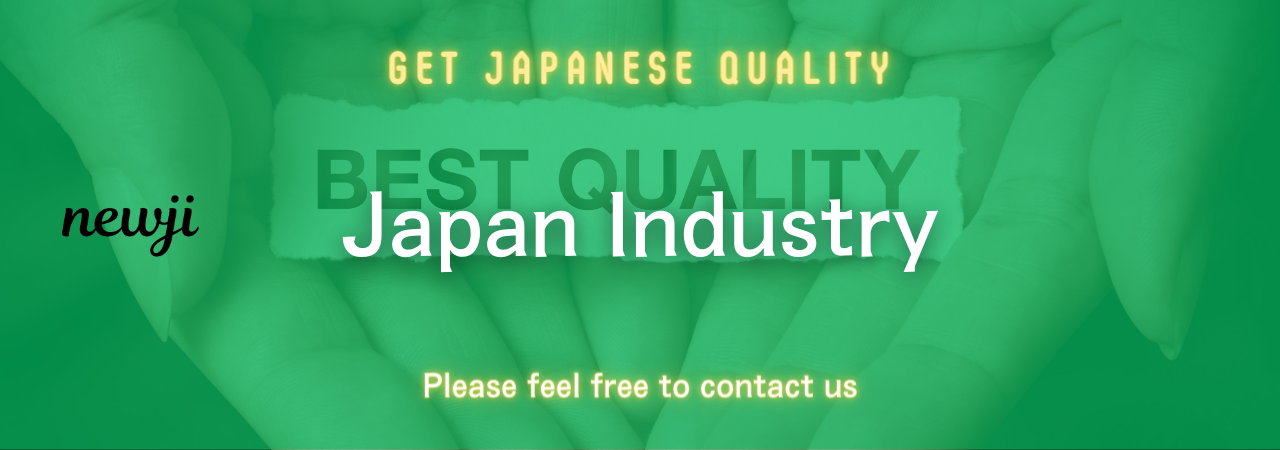
In today’s fast-paced manufacturing environment, it’s crucial to achieve optimal efficiency on the production line.
One approach to achieving this is through line balancing, a process that ensures all tasks are distributed evenly across the production line.
Digital Transformation, often abbreviated as DX, is revolutionizing how we approach line balancing by leveraging cutting-edge technology to optimize processes.
This article explores how DX in line balancing can reduce production losses and improve capacity utilization.
目次
What is Line Balancing?
Line balancing is the process of arranging a production sequence such that each workstation has an equal amount of workload.
The aim is to ensure that tasks are completed in a synchronized manner, thereby minimizing downtime and eliminating bottlenecks.
Proper line balancing allows for a smoother flow of operations and more efficient use of resources.
The Role of DX in Line Balancing
Digital Transformation involves integrating digital technologies into various aspects of business operations.
In the context of line balancing, DX employs tools like artificial intelligence (AI), machine learning, Internet of Things (IoT), and big data analytics.
These technologies offer data-driven insights that help managers make informed decisions on optimizing production lines.
Real-Time Data and Monitoring
One of the profound benefits of DX in line balancing is the ability to collect and analyze real-time data.
Sensors connected to the production line gather data related to machine performance, cycle times, and workforce efficiency.
This data is analyzed to provide actionable insights that help managers make real-time adjustments to the production process.
For instance, if a particular workstation is falling behind, real-time data allows supervisors to reallocate resources or adjust workloads promptly.
This minimizes downtime and helps maintain a balanced production line.
Predictive Analytics
Predictive analytics, powered by machine learning, is another significant benefit that DX brings to line balancing.
By analyzing historical data, predictive models can forecast potential bottlenecks and downtime before they occur.
Managers can then take preemptive measures to mitigate these issues, such as scheduling maintenance during non-peak hours or streamlining task sequences.
This proactive approach reduces unexpected disruptions and maintains steady production, which translates to better capacity utilization and reduced production losses.
Reducing Production Losses with DX
Production losses can occur due to various reasons, including machine downtime, inefficient workflows, and human error.
DX can mitigate these losses by enhancing transparency and operational efficiency.
Reducing Machine Downtime
With the help of IoT sensors and big data analytics, manufacturers can monitor machine health continuously.
Predictive maintenance algorithms can predict when a machine is likely to fail, allowing for scheduled maintenance that minimizes downtime.
This ensures that machines are operational when needed, thus maintaining a balanced workflow and reducing production losses.
Improving Workflow Efficiency
AI and machine learning algorithms can analyze production line data to identify inefficiencies.
For example, they can pinpoint steps in the production process where time is lost and propose solutions to eliminate these inefficiencies.
Machine learning models can also simulate different line configurations to determine the most efficient setup.
This helps in designing a balanced production line that maximizes throughput and minimizes delays.
Minimizing Human Error
Human error is another factor contributing to production losses.
Digital tools can assist workers by providing real-time feedback and step-by-step instructions.
Augmented Reality (AR) systems can overlay digital information onto the physical workspace, guiding operators through complex tasks accurately.
This reduces the likelihood of errors, enhances worker productivity, and contributes to a balanced production line.
Improving Capacity Utilization with DX
Capacity utilization refers to the extent to which a manufacturing unit’s potential output is being achieved.
Higher capacity utilization means better efficiency and profitability.
DX improves capacity utilization through various means.
Optimized Resource Allocation
AI and data analytics can analyze the overall production process to determine the best allocation of resources, including labor and machinery.
With optimized resource allocation, each part of the production line is utilized effectively, leading to higher capacity utilization.
This means that manufacturers can produce more with the same resources, thereby enhancing profitability.
Enhanced Flexibility
Digital tools make production lines more adaptable to changes.
For instance, if demand for a particular product increases, a DX-enabled production line can quickly adjust to produce more of that product without significant downtime.
This flexibility ensures that the production line is always aligned with market demand, maximizing capacity utilization.
Continuous Improvement
DX enables a culture of continuous improvement by providing ongoing insights into production line performance.
Managers can track key performance indicators (KPIs) and implement iterative improvements based on data-driven recommendations.
This continual optimization ensures that the production line is always performing at its best, enhancing capacity utilization over time.
Conclusion
Digital Transformation in line balancing is a game-changer for the manufacturing industry.
It reduces production losses and improves capacity utilization by leveraging real-time data, predictive analytics, and innovative technologies.
By adopting DX, manufacturers can achieve higher efficiency, increased output, and ultimately, greater profitability.
Integrating these technologies into your production line is not just an option but a necessity in today’s competitive landscape.
資料ダウンロード
QCD管理受発注クラウド「newji」は、受発注部門で必要なQCD管理全てを備えた、現場特化型兼クラウド型の今世紀最高の受発注管理システムとなります。
ユーザー登録
受発注業務の効率化だけでなく、システムを導入することで、コスト削減や製品・資材のステータス可視化のほか、属人化していた受発注情報の共有化による内部不正防止や統制にも役立ちます。
NEWJI DX
製造業に特化したデジタルトランスフォーメーション(DX)の実現を目指す請負開発型のコンサルティングサービスです。AI、iPaaS、および先端の技術を駆使して、製造プロセスの効率化、業務効率化、チームワーク強化、コスト削減、品質向上を実現します。このサービスは、製造業の課題を深く理解し、それに対する最適なデジタルソリューションを提供することで、企業が持続的な成長とイノベーションを達成できるようサポートします。
製造業ニュース解説
製造業、主に購買・調達部門にお勤めの方々に向けた情報を配信しております。
新任の方やベテランの方、管理職を対象とした幅広いコンテンツをご用意しております。
お問い合わせ
コストダウンが利益に直結する術だと理解していても、なかなか前に進めることができない状況。そんな時は、newjiのコストダウン自動化機能で大きく利益貢献しよう!
(β版非公開)