- お役立ち記事
- DX in Tapping Machining Holds the Key to High Precision and Unmanned Operation
DX in Tapping Machining Holds the Key to High Precision and Unmanned Operation
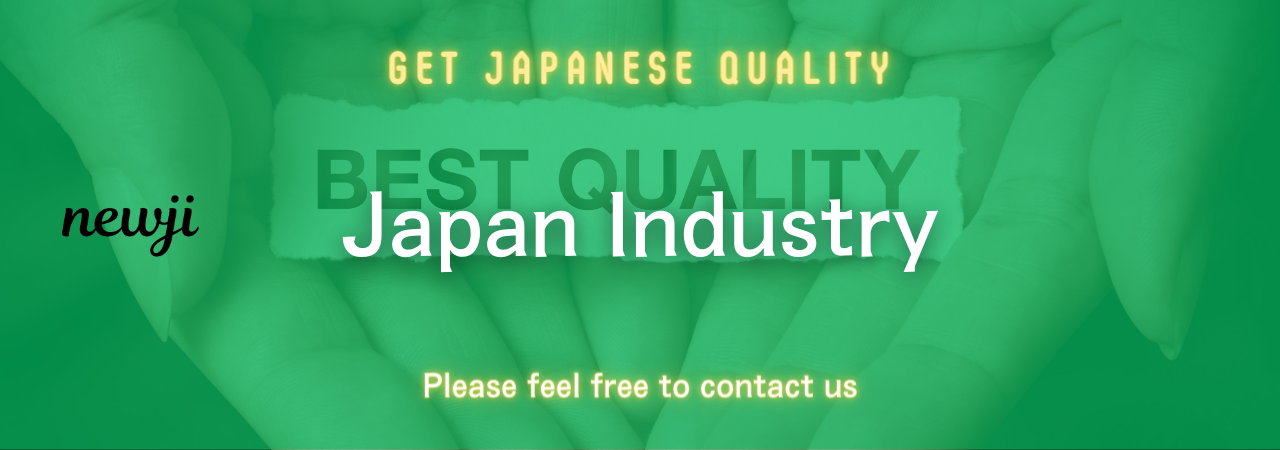
In today’s fast-paced industrial landscape, precision and efficiency are crucial for companies to stay competitive. One area where technological advancements are making a significant impact is in tapping machining.
Digital transformation (DX) in tapping machining involves integrating advanced digital technology into the manufacturing process, resulting in high precision and the possibility of unmanned operations.
This shift is paving the way for a new era in the machining industry where accuracy and automation go hand in hand.
目次
Understanding Tapping Machining
Tapping machining is a process used to create internal threads in holes.
It is a crucial step in manufacturing various components, from automotive parts to electronic devices.
The success of this process depends largely on precision and consistency.
Traditional methods often rely on manual adjustments, which can lead to inconsistencies and errors.
The Role of DX in Modern Machining
Digital transformation in tapping machining introduces a new level of accuracy and efficiency.
By integrating computer-aided design (CAD) and computer-aided manufacturing (CAM) systems, manufacturers can achieve precise control over the tapping process.
These digital tools allow for pre-programmed settings, reducing the potential for human error and ensuring consistency across production runs.
Automation and Unmanned Operations
One of the biggest advantages of DX in tapping machining is the move towards unmanned operations.
Automated systems can perform repetitive tasks with high precision, reducing the reliance on skilled operators and minimizing human errors.
This not only increases productivity but also lowers labor costs and enhances safety in the workplace.
High Precision with Digital Technology
Precision is paramount in tapping machining.
Even minor deviations can lead to defects in the final product.
Digital technology enhances precision by enabling real-time monitoring and adjustments.
Sensors and feedback systems provide constant data on the machining process, allowing for immediate corrections if any issues arise.
This level of control ensures that each thread is cut to exact specifications, resulting in higher quality products.
Enhanced Monitoring and Quality Control
With digital transformation, manufacturers can implement advanced monitoring systems that track every aspect of the tapping process.
This includes monitoring tool wear, cutting forces, and temperature variations.
By analyzing this data, manufacturers can predict potential issues before they become critical, leading to proactive maintenance and reducing downtime.
Quality control is also improved as digital systems can detect deviations in real-time and make adjustments accordingly.
Integration with Other Manufacturing Processes
DX in tapping machining does not operate in isolation.
It integrates seamlessly with other manufacturing processes, creating a cohesive and efficient production environment.
For example, data from the tapping process can be fed into a larger manufacturing execution system (MES), providing a holistic view of the entire production line.
This integration ensures that all processes are synchronized, further enhancing precision and efficiency.
Case Studies and Real-World Applications
Several companies have already embraced digital transformation in their tapping machining operations, seeing remarkable results.
For instance, a leading automotive parts manufacturer implemented an automated tapping system with real-time monitoring.
The result was a significant reduction in defects, increased production speed, and lower operational costs.
Similarly, an electronics manufacturer integrated DX into their tapping process, enabling them to produce high-precision components with minimal human intervention.
These real-world examples highlight the tangible benefits of adopting digital technology in tapping machining.
The Future of Tapping Machining
The future of tapping machining lies in continued innovation and integration of digital technologies.
As artificial intelligence (AI) and machine learning (ML) become more advanced, we can expect further improvements in precision and automation.
AI algorithms can analyze vast amounts of data to optimize the tapping process, predicting the best settings for different materials and conditions.
Additionally, advancements in robotics will enhance unmanned operations, making them even more efficient and reliable.
Overcoming Challenges
Despite the many advantages, adopting DX in tapping machining is not without challenges.
One of the main barriers is the initial investment required for new technology and equipment.
However, the long-term benefits often outweigh the upfront costs, with increased productivity and reduced defects leading to a higher return on investment.
Another challenge is the need for workforce training.
Employees must be skilled in operating and maintaining digital systems, which requires ongoing education and support.
Conclusion
Digital transformation in tapping machining is revolutionizing the manufacturing industry.
By integrating advanced digital technologies, companies can achieve high precision and the potential for unmanned operations.
This shift not only enhances productivity but also improves product quality and reduces operational costs.
As the technology continues to evolve, we can expect even greater advancements in the future.
For manufacturers looking to stay competitive, embracing DX in tapping machining is no longer optional but a necessity.
The key to high precision and efficiency lies in the ongoing pursuit of digital innovation.
資料ダウンロード
QCD調達購買管理クラウド「newji」は、調達購買部門で必要なQCD管理全てを備えた、現場特化型兼クラウド型の今世紀最高の購買管理システムとなります。
ユーザー登録
調達購買業務の効率化だけでなく、システムを導入することで、コスト削減や製品・資材のステータス可視化のほか、属人化していた購買情報の共有化による内部不正防止や統制にも役立ちます。
NEWJI DX
製造業に特化したデジタルトランスフォーメーション(DX)の実現を目指す請負開発型のコンサルティングサービスです。AI、iPaaS、および先端の技術を駆使して、製造プロセスの効率化、業務効率化、チームワーク強化、コスト削減、品質向上を実現します。このサービスは、製造業の課題を深く理解し、それに対する最適なデジタルソリューションを提供することで、企業が持続的な成長とイノベーションを達成できるようサポートします。
オンライン講座
製造業、主に購買・調達部門にお勤めの方々に向けた情報を配信しております。
新任の方やベテランの方、管理職を対象とした幅広いコンテンツをご用意しております。
お問い合わせ
コストダウンが利益に直結する術だと理解していても、なかなか前に進めることができない状況。そんな時は、newjiのコストダウン自動化機能で大きく利益貢献しよう!
(Β版非公開)