- お役立ち記事
- DX in the dicing process significantly improves semiconductor yield
DX in the dicing process significantly improves semiconductor yield
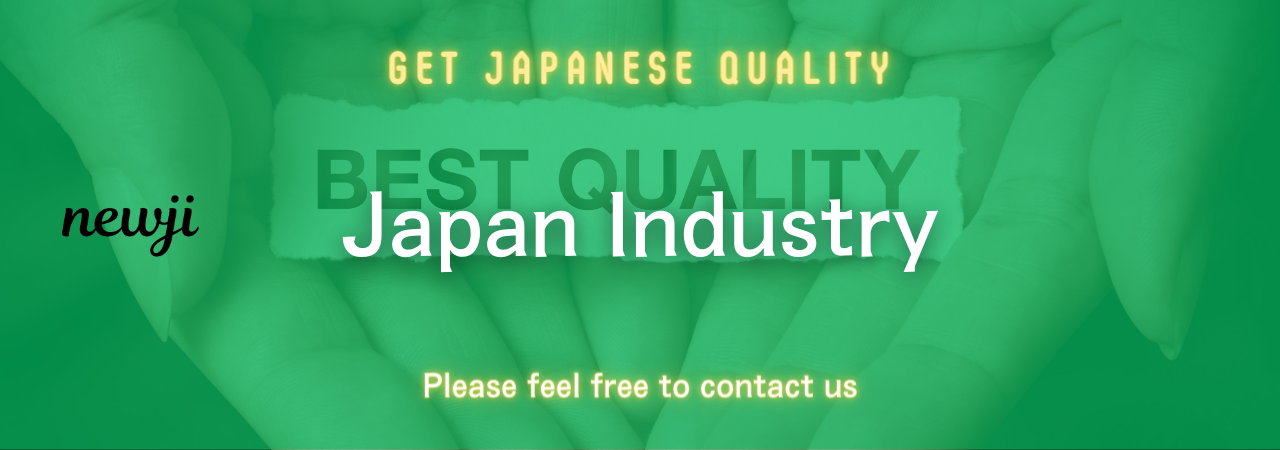
Digital Transformation (DX) in the Dicing Process Significantly Improves Semiconductor Yield
In the ever-evolving world of technology, the semiconductor industry stands as a cornerstone, driving innovations and advancements across numerous fields. Among the myriad processes involved in semiconductor manufacturing, dicing plays a pivotal role. Dicing, the process of cutting semiconductor wafers into individual chips, is vital for ensuring the precise and efficient production of semiconductors. With the advent of Digital Transformation (DX), this process has experienced significant improvements, leading to enhanced semiconductor yield, efficiency, and precision.
Understanding the Dicing Process
Before delving into how DX revolutionizes the dicing process, it is essential to understand what dicing involves. In semiconductor manufacturing, dicing refers to the cutting of silicon wafers into separate dies or chips. These chips are then packaged to create microprocessors, memory units, and other critical components used in various electronic devices.
Traditionally, the dicing process has relied on mechanical methods such as saw dicing and laser dicing. Saw dicing involves using a fine blade to cut the wafer, whereas laser dicing utilizes focused laser beams to achieve the same goal. While these methods have been effective, they come with their own set of challenges, including potential damage to the wafer, precision limitations, and wastage.
The Role of Digital Transformation (DX)
Digital Transformation (DX) encompasses the integration of digital technology into all aspects of business operations, leading to fundamental changes in how companies operate and deliver value to customers. In the context of semiconductor manufacturing and dicing, DX leverages advanced technologies such as artificial intelligence (AI), machine learning (ML), big data analytics, and the Internet of Things (IoT) to optimize the dicing process.
1. Enhanced Precision and Accuracy
One of the most significant benefits of DX in the dicing process is the enhanced precision and accuracy it brings. Traditional dicing methods often struggle with maintaining consistent quality across all chips, leading to variations and defects. With the integration of AI and ML algorithms, manufacturers can achieve unparalleled precision. These algorithms analyze a multitude of parameters in real-time, such as wafer thickness, cutting speed, and laser intensity, to ensure that each cut is made with pinpoint accuracy. This not only reduces defects but also increases the overall yield of usable chips from each wafer.
2. Predictive Maintenance and Reduced Downtime
DX also enables predictive maintenance, a game-changer for semiconductor manufacturers. By leveraging IoT sensors and big data analytics, manufacturers can monitor the health and performance of dicing equipment in real-time. These sensors collect data on factors such as vibration, temperature, and machine wear, which is then analyzed using AI algorithms to predict potential failures before they occur. This proactive approach allows for timely maintenance and repairs, minimizing unexpected downtime and ensuring that the dicing process remains smooth and uninterrupted.
3. Improved Yield and Reduced Wastage
Semiconductor yield, the percentage of functional chips obtained from a wafer, is a critical metric for manufacturers. Higher yields translate to increased profitability and reduced production costs. DX has a profound impact on yield improvement by optimizing various aspects of the dicing process. For instance, machine learning algorithms can identify patterns and correlations in the data collected during dicing, helping manufacturers fine-tune their processes for maximum efficiency. Additionally, DX enables real-time monitoring and adjustment of dicing parameters, ensuring that each wafer is utilized to its fullest potential, thereby reducing wastage.
4. Quality Control and Defect Detection
Maintaining high-quality standards is paramount in semiconductor manufacturing. Defects in the dicing process can lead to malfunctioning chips, which can have far-reaching consequences in the final products they power. DX offers advanced quality control mechanisms that surpass traditional visual inspection methods. Computer vision systems enhanced with AI can identify even the tiniest defects, ensuring that only chips meeting stringent quality criteria proceed to packaging. This level of precision significantly reduces the chances of defective chips making their way into the market.
5. Process Optimization and Cost Savings
DX drives process optimization by providing valuable insights into every step of the dicing process. Through data analysis and AI-driven recommendations, manufacturers can identify inefficiencies and implement corrective measures. For example, real-time data analysis can highlight areas where cutting speeds can be optimized without compromising quality, leading to substantial cost savings. Furthermore, the ability to remotely monitor and control dicing processes through digital platforms enhances operational efficiency, allowing manufacturers to make informed decisions swiftly.
6. Customization and Flexibility
Every semiconductor manufacturer operates under unique conditions and requirements. DX allows for a high degree of customization and flexibility in the dicing process. AI-driven systems can adapt to varying wafer materials, sizes, and complexities, ensuring that manufacturers can meet diverse customer demands. This adaptability is particularly crucial in today’s fast-paced technological landscape, where product variations and customizations are commonplace.
7. Data-Driven Decision Making
Perhaps one of the most transformative aspects of DX is its emphasis on data-driven decision making. The dicing process generates vast amounts of data, ranging from equipment performance metrics to environmental conditions. DX leverages this data to provide meaningful insights that guide strategic decisions. By analyzing historical and real-time data, manufacturers can identify trends, forecast demand, and make informed choices that optimize production schedules, resources, and overall efficiency.
Conclusion
Digital Transformation (DX) has revolutionized the semiconductor manufacturing industry, particularly in the critical dicing process. By harnessing the power of AI, machine learning, big data analytics, and IoT, manufacturers can achieve unprecedented levels of precision, efficiency, and yield. The benefits of DX extend beyond immediate improvements, paving the way for a more sustainable, cost-effective, and adaptable semiconductor manufacturing ecosystem. As technology continues to evolve, embracing DX in the dicing process is no longer an option but a necessity for staying competitive and meeting the demands of an increasingly complex and dynamic market.
資料ダウンロード
QCD調達購買管理クラウド「newji」は、調達購買部門で必要なQCD管理全てを備えた、現場特化型兼クラウド型の今世紀最高の購買管理システムとなります。
ユーザー登録
調達購買業務の効率化だけでなく、システムを導入することで、コスト削減や製品・資材のステータス可視化のほか、属人化していた購買情報の共有化による内部不正防止や統制にも役立ちます。
NEWJI DX
製造業に特化したデジタルトランスフォーメーション(DX)の実現を目指す請負開発型のコンサルティングサービスです。AI、iPaaS、および先端の技術を駆使して、製造プロセスの効率化、業務効率化、チームワーク強化、コスト削減、品質向上を実現します。このサービスは、製造業の課題を深く理解し、それに対する最適なデジタルソリューションを提供することで、企業が持続的な成長とイノベーションを達成できるようサポートします。
オンライン講座
製造業、主に購買・調達部門にお勤めの方々に向けた情報を配信しております。
新任の方やベテランの方、管理職を対象とした幅広いコンテンツをご用意しております。
お問い合わせ
コストダウンが利益に直結する術だと理解していても、なかなか前に進めることができない状況。そんな時は、newjiのコストダウン自動化機能で大きく利益貢献しよう!
(Β版非公開)