- お役立ち記事
- DX in the knapping process ensures high efficiency and quality stability
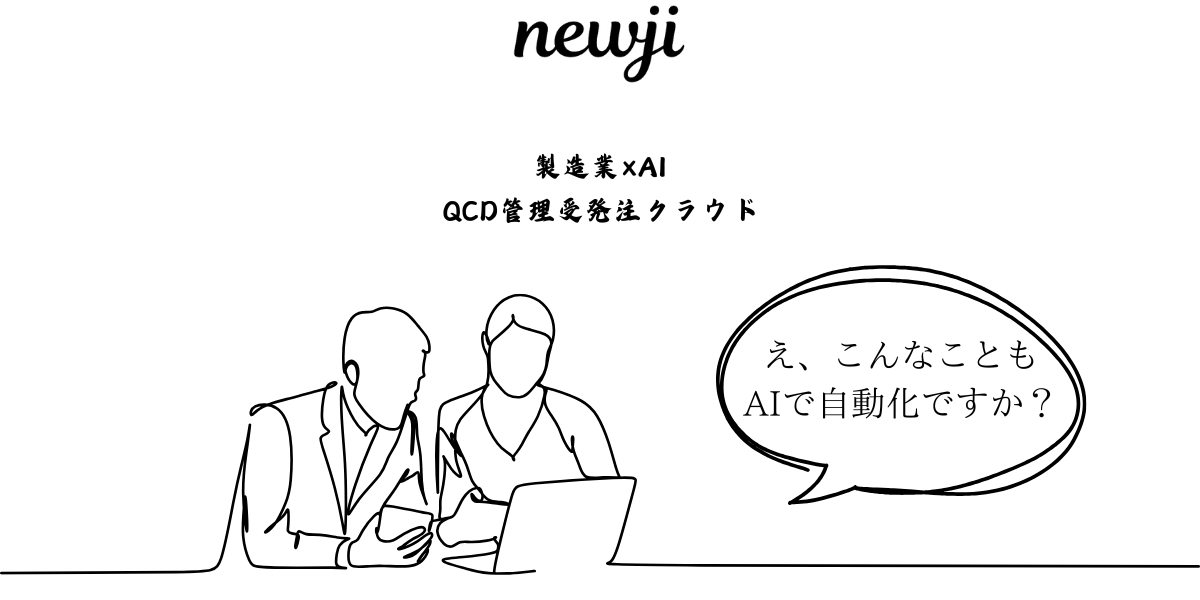
DX in the knapping process ensures high efficiency and quality stability
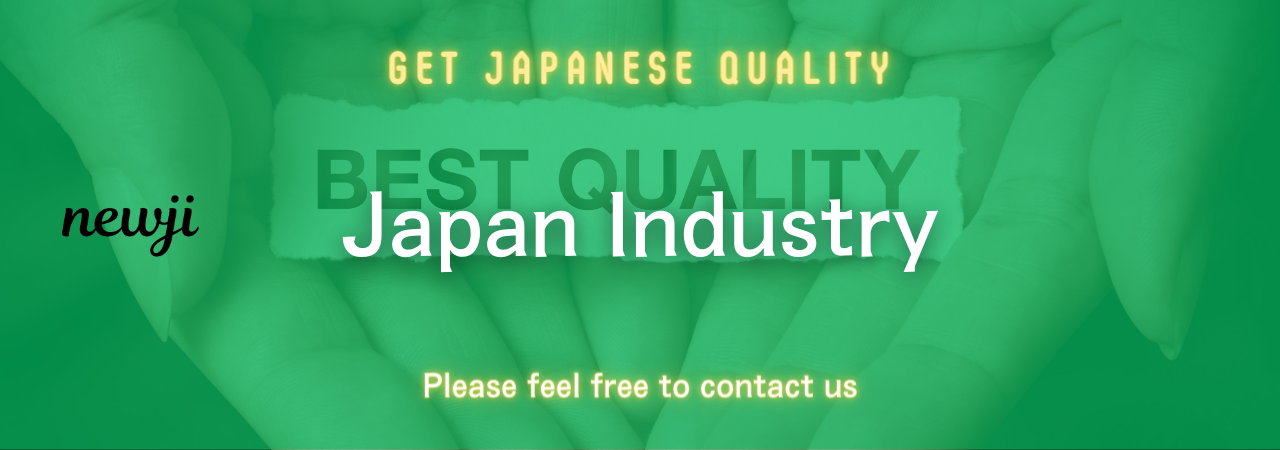
In today’s rapidly evolving technological landscape, industries across the board are seeking ways to enhance efficiency and maintain consistent quality. One such industry that has seen significant advances is the manufacturing sector, particularly in processes like knapping. Digital Transformation, or DX, is proving to be a game-changer in this field. Let’s delve into how DX in the knapping process ensures high efficiency and quality stability.
目次
Understanding Knapping in Manufacturing
Knapping is a meticulous process that involves shaping materials through controlled removal. Traditionally applied to stone, this technique has expanded to metals and other materials in modern manufacturing. Evident in creating tools, blades, and even artistic pieces, knapping requires precision and skill. However, the traditional methods, while effective, are time-consuming and often inconsistent.
The Role of Digital Transformation (DX)
Digital Transformation involves integrating digital technology into various operations to improve processes and outcomes. In the context of knapping, DX means employing advanced tools and software to revolutionize the traditional process. This shift not only streamlines the workflow but also introduces unprecedented levels of precision and consistency.
Automation and Robotics
One of the most impactful elements of DX in knapping is automation. Robotics equipped with high-precision tools can replicate the knapping process with utmost accuracy. Unlike human hands, robots do not tire, ensuring a uniform quality and finish across all products. This automation reduces the margin for error, significantly enhancing the overall quality.
Computer-Aided Design (CAD)
CAD technology plays a crucial role in modernizing the knapping process. Designers can create detailed digital blueprints that outline every cut and contour. These blueprints serve as the basis for automated machinery, ensuring every product meets the exact specifications. The use of CAD reduces waste and speeds up production, enhancing efficiency.
Real-Time Monitoring and Adjustments
DX also introduces the ability to monitor the knapping process in real time. Sensors and other monitoring tools can detect any deviations from the desired process. This data is analyzed instantly, allowing for quick adjustments. As a result, the likelihood of producing defective pieces is minimized, ensuring consistent quality.
Benefits of DX in the Knapping Process
Implementing DX in the knapping process brings numerous advantages. These benefits span from improved efficiency to enhanced quality control, profoundly impacting the bottom line.
Increased Production Speed
With automated tools and precise planning through CAD, the knapping process becomes significantly faster. What once took hours can now be accomplished in a fraction of the time. This increased production speed means businesses can meet higher demands without compromising quality.
Consistency and Quality Control
Human error is a common issue in manual knapping. With DX, every product produced is consistent with the one before it. Automated systems follow the exact same process every time, resulting in fewer defects. This consistency is crucial for maintaining a high-quality standard, especially in industries where precision is paramount.
Cost Efficiency
While the initial investment in digital tools and technologies may seem high, the long-term savings are substantial. Reduced labor costs, minimized waste, and higher production speeds contribute to significant cost savings. Over time, these savings outweigh the initial costs, making DX a financially sound investment.
Case Studies and Real-World Applications
Several industries have already embraced DX in their knapping processes, witnessing remarkable improvements.
Aerospace Industry
In the aerospace sector, the need for precision and consistency cannot be overstated. DX technologies ensure that components are manufactured to exact specifications. This precision is crucial for safety and performance in aerospace applications. Companies have reported faster production times and enhanced component quality, leading to safer and more reliable aircraft.
Healthcare and Medical Devices
Medical devices must meet stringent quality standards. DX in knapping allows for the production of accurate and reliable tools and devices. The ability to maintain consistent quality ensures these devices function as intended, contributing to better patient outcomes.
Art and Craftsmanship
Even in areas like art and craftsmanship, DX is making a mark. Artists can use digital tools to plan their work meticulously, ensuring every piece created meets their vision. This blend of technology and traditional craftsmanship brings a new level of precision and creativity to the art world.
Challenges and Considerations
While the benefits are clear, the transition to DX in the knapping process is not without challenges. Businesses must consider several factors to ensure a smooth and successful transformation.
Initial Investment
The cost of implementing digital technologies can be high. Businesses must weigh these initial expenses against the long-term benefits. Careful planning and budgeting are essential to manage these costs effectively.
Training and Adaptation
Employees must be trained to work with new technologies. This transition period can be challenging, as workers adapt to the new systems. Ongoing training and support are crucial to ensure smooth adaptation and to maximize the benefits of DX.
Maintenance and Upkeep
Digital systems require regular maintenance and updates. Businesses must have plans in place for ongoing technical support. Regular maintenance ensures the systems function optimally, preventing downtime and maintaining efficiency.
The Future of DX in Knapping
The integration of digital technology in knapping is just beginning. As technology continues to evolve, we can expect even more significant advancements. Future innovations may include more sophisticated AI systems, advanced robotics, and even greater precision tools. These technologies will continue to push the boundaries of what is possible, further enhancing efficiency and quality in the knapping process.
In conclusion, the incorporation of Digital Transformation in the knapping process marks a pivotal shift towards higher efficiency and quality stability. As businesses invest in these technologies, they unlock new potentials, setting new standards in their respective industries. The future of knapping, powered by DX, promises a landscape where precision and efficiency lead the way, driving innovation and success.
資料ダウンロード
QCD調達購買管理クラウド「newji」は、調達購買部門で必要なQCD管理全てを備えた、現場特化型兼クラウド型の今世紀最高の購買管理システムとなります。
ユーザー登録
調達購買業務の効率化だけでなく、システムを導入することで、コスト削減や製品・資材のステータス可視化のほか、属人化していた購買情報の共有化による内部不正防止や統制にも役立ちます。
NEWJI DX
製造業に特化したデジタルトランスフォーメーション(DX)の実現を目指す請負開発型のコンサルティングサービスです。AI、iPaaS、および先端の技術を駆使して、製造プロセスの効率化、業務効率化、チームワーク強化、コスト削減、品質向上を実現します。このサービスは、製造業の課題を深く理解し、それに対する最適なデジタルソリューションを提供することで、企業が持続的な成長とイノベーションを達成できるようサポートします。
オンライン講座
製造業、主に購買・調達部門にお勤めの方々に向けた情報を配信しております。
新任の方やベテランの方、管理職を対象とした幅広いコンテンツをご用意しております。
お問い合わせ
コストダウンが利益に直結する術だと理解していても、なかなか前に進めることができない状況。そんな時は、newjiのコストダウン自動化機能で大きく利益貢献しよう!
(Β版非公開)