- お役立ち記事
- DX in Wire EDM Processes Enables High Precision Machining
DX in Wire EDM Processes Enables High Precision Machining
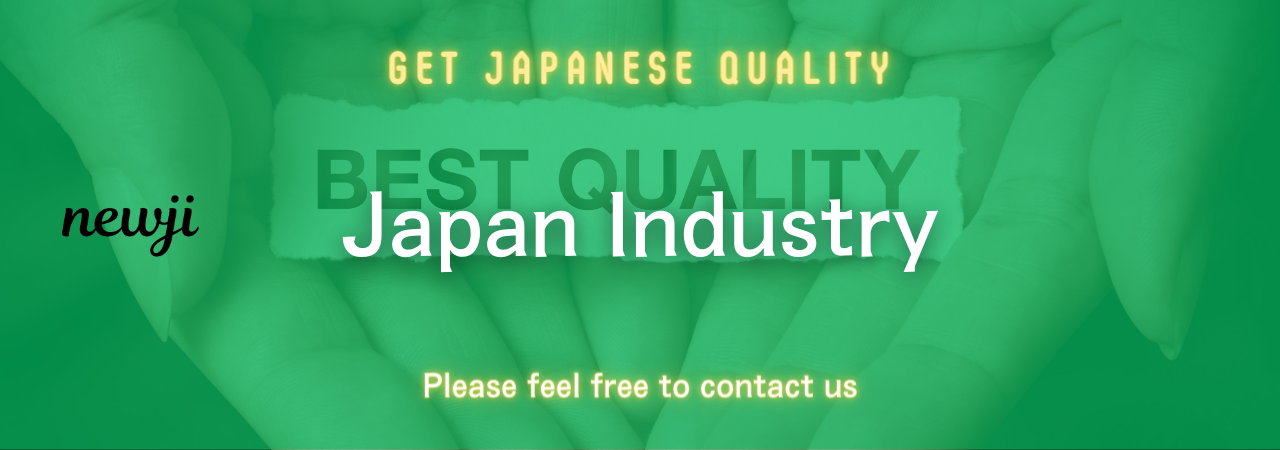
Wire Electrical Discharge Machining, or Wire EDM as it’s often called, is a technology that has revolutionized how we create precision parts today.
By using a thin wire and electrical discharges, Wire EDM can cut intricate shapes and complex structures with incredible accuracy.
Recently, the concept of “Digital Transformation” (DX) has begun playing a significant role in further enhancing this already advanced technology.
In this article, we explore how DX is enabling high precision machining through Wire EDM processes.
目次
What is Digital Transformation (DX)?
Digital Transformation refers to the use of digital technology to radically change how businesses operate and deliver value to customers.
In the context of Wire EDM, it involves integrating advanced software, IoT (Internet of Things) devices, automation, and data analytics into the manufacturing process.
These innovations help yield better quality parts, reduce waste, and increase production efficiency.
The Role of DX in Wire EDM
Enhanced Precision and Accuracy
With the help of digital tools like CAD (Computer-Aided Design) and CAM (Computer-Aided Manufacturing) software, Wire EDM machines can achieve levels of precision that were previously impossible.
These tools allow for better visualization and planning of the cuts, ensuring that every detail is captured.
Furthermore, advanced algorithms can optimize the cutting path to minimize errors and achieve a higher degree of accuracy.
Improved Monitoring and Control
IoT devices can be integrated into Wire EDM machines to monitor various parameters in real-time.
These include the wire tension, electrical discharge rate, and the working environment.
With this data, operators can make immediate adjustments, ensuring consistently high-quality output.
Additionally, predictive maintenance algorithms can forecast machine failures, reducing downtime and increasing overall efficiency.
Data-Driven Decision Making
Data analytics plays a pivotal role in DX for Wire EDM.
By analyzing historical data, manufacturers can identify patterns and trends that may affect the quality or efficiency of the machining process.
For instance, data can reveal the optimal settings for different materials or identify potential issues before they become significant problems.
This information can be used to make informed decisions that improve both the process and the final product.
Applications of DX in Wire EDM
Aerospace Industry
In aerospace manufacturing, the demand for parts with extremely tight tolerances is high.
DX in Wire EDM helps meet these demands by providing precise and accurate machining capabilities.
For example, turbine blades and other critical components can be produced with exact specifications, ensuring the safety and performance of aircraft.
Medical Device Manufacturing
Medical devices often require complex shapes and minuscule details to function correctly.
DX in Wire EDM helps manufacturers create these intricate parts with high precision.
Whether it’s surgical instruments or implants, digital transformation ensures that every piece meets strict quality standards.
Tool and Die Making
The tool and die industry benefits greatly from the precision enabled by DX in Wire EDM processes.
Molds and dies need to be exact to ensure the proper formation of products.
Digital tools and real-time monitoring capabilities ensure that these components are produced with unmatched accuracy.
Challenges and Future Prospects
While the advantages of DX in Wire EDM are numerous, there are challenges that need to be addressed.
Integration Costs
The initial cost of integrating digital tools and IoT devices can be high.
For small and medium-sized enterprises, these costs can be a significant barrier.
However, the long-term benefits often outweigh the initial investment, especially when considering the improvements in efficiency and quality.
Skilled Workforce
Another challenge is the need for a skilled workforce that can operate and manage these advanced systems.
Training and development programs are essential to equip workers with the required skills.
As the technology evolves, continuous learning will be necessary to keep up with advancements.
Future Prospects
Despite these challenges, the future of DX in Wire EDM is promising.
Ongoing advancements in AI (Artificial Intelligence) and machine learning will likely yield even more refined algorithms for optimizing the machining process.
Cloud computing solutions could provide easier access to advanced analytics, making these tools more accessible to smaller manufacturers.
Conclusion
Digital Transformation is playing a crucial role in enhancing the capabilities of Wire EDM processes.
From improved precision and accuracy to real-time monitoring and data-driven decision making, the benefits are substantial.
While challenges such as integration costs and the need for a skilled workforce exist, the long-term prospects are promising.
As DX continues to evolve, the potential for Wire EDM to achieve even higher levels of precision and efficiency will only grow.
The integration of these advanced technologies ensures that Wire EDM remains a vital tool for industries requiring high precision machining.
資料ダウンロード
QCD調達購買管理クラウド「newji」は、調達購買部門で必要なQCD管理全てを備えた、現場特化型兼クラウド型の今世紀最高の購買管理システムとなります。
ユーザー登録
調達購買業務の効率化だけでなく、システムを導入することで、コスト削減や製品・資材のステータス可視化のほか、属人化していた購買情報の共有化による内部不正防止や統制にも役立ちます。
NEWJI DX
製造業に特化したデジタルトランスフォーメーション(DX)の実現を目指す請負開発型のコンサルティングサービスです。AI、iPaaS、および先端の技術を駆使して、製造プロセスの効率化、業務効率化、チームワーク強化、コスト削減、品質向上を実現します。このサービスは、製造業の課題を深く理解し、それに対する最適なデジタルソリューションを提供することで、企業が持続的な成長とイノベーションを達成できるようサポートします。
オンライン講座
製造業、主に購買・調達部門にお勤めの方々に向けた情報を配信しております。
新任の方やベテランの方、管理職を対象とした幅広いコンテンツをご用意しております。
お問い合わせ
コストダウンが利益に直結する術だと理解していても、なかなか前に進めることができない状況。そんな時は、newjiのコストダウン自動化機能で大きく利益貢献しよう!
(Β版非公開)