- お役立ち記事
- DX Monitoring of Compounding Improves Quality of High Performance Compounds
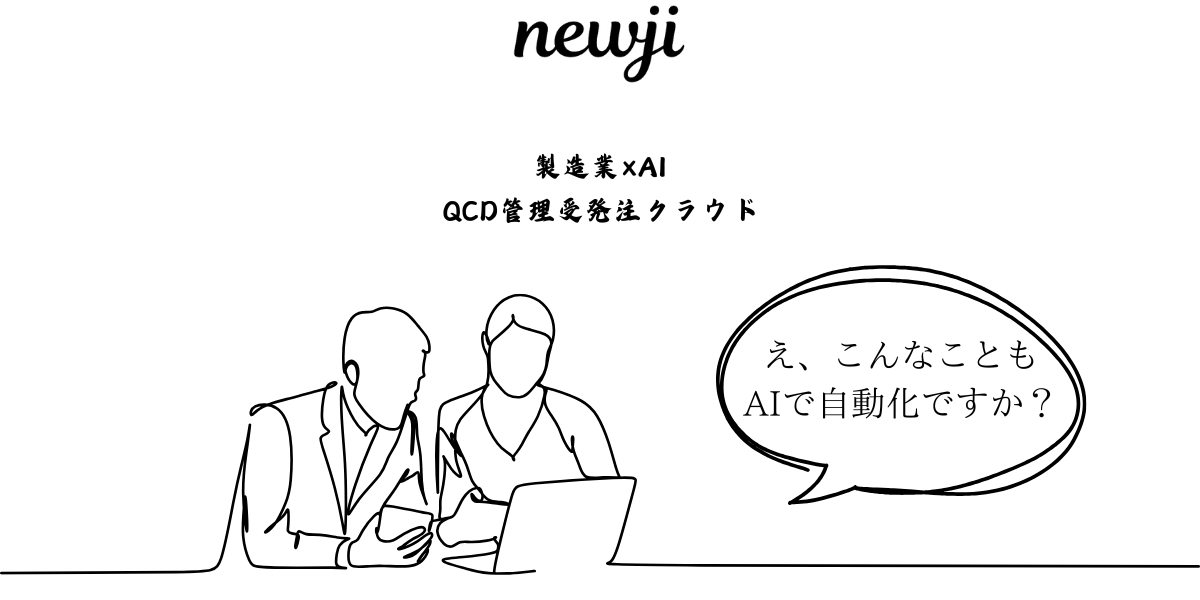
DX Monitoring of Compounding Improves Quality of High Performance Compounds
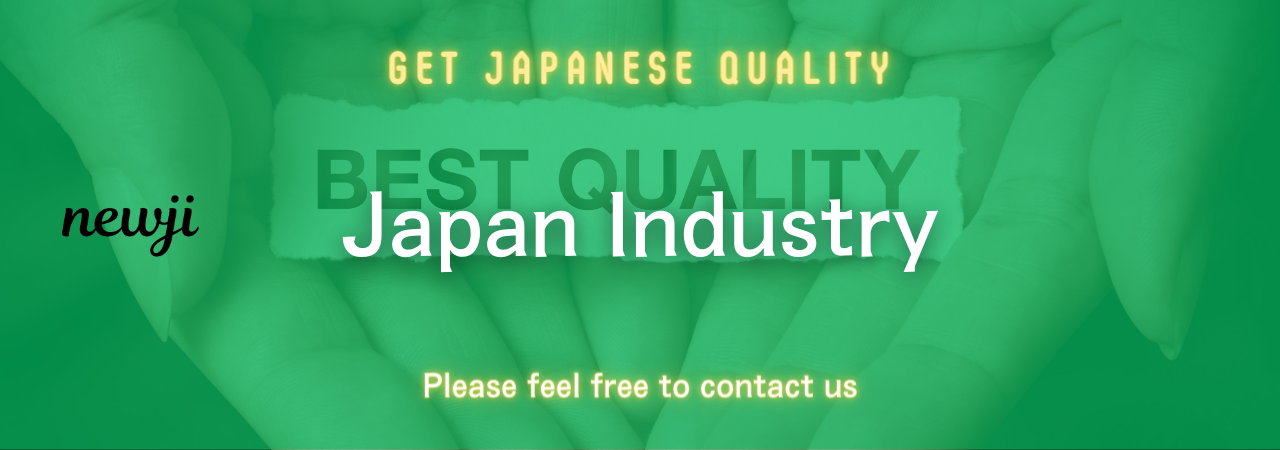
In today’s fast-paced world, industries are constantly seeking ways to improve the quality and efficiency of their processes.
One such area that has seen significant advancements is the compounding of high-performance materials.
With the integration of digital transformation (DX) technologies, monitoring the compounding process has become more precise, leading to the production of superior quality compounds.
This transformation not only enhances the performance of the materials but also streamlines operations, reduces waste, and cuts costs.
目次
Understanding DX Monitoring in Compounding
Digital transformation (DX) refers to the integration of digital technologies into all areas of a business.
In the context of compounding, DX monitoring employs advanced sensors, data analytics, and machine learning to oversee the compounding process.
These technologies collect real-time data on various parameters such as temperature, pressure, mixing speed, and ingredient concentrations.
By analyzing this data, operators can make informed decisions to optimize the process, ensuring the end product meets the desired specifications.
The Importance of Quality in High-Performance Compounds
High-performance compounds are used in a wide range of applications, from automotive components to medical devices.
The quality of these compounds directly impacts the performance, safety, and longevity of the final products.
Even minor deviations in the formulation or processing conditions can lead to significant disparities in the compound’s properties.
Therefore, maintaining stringent quality control throughout the compounding process is crucial.
DX monitoring ensures that each batch produced adheres to the highest standards, minimizing the risk of defects and inconsistencies.
Benefits of DX Monitoring in Compounding
Enhanced Precision and Consistency
One of the primary benefits of DX monitoring is the ability to achieve enhanced precision and consistency in the compounding process.
Traditional methods relied heavily on manual measurements and adjustments, which were prone to human error.
With DX monitoring, automated systems continuously track and adjust process parameters in real-time, ensuring optimal conditions are maintained throughout the batch.
This results in a more uniform and consistent product.
Data-Driven Insights
The wealth of data generated by DX monitoring provides valuable insights into the compounding process.
By analyzing this data, operators can identify trends, detect anomalies, and predict potential issues before they occur.
For instance, if a particular batch shows signs of deviation, operators can trace the root cause by reviewing the data.
This proactive approach not only prevents defects but also helps in fine-tuning the process for future batches.
Cost Savings and Efficiency
Implementing DX monitoring can lead to significant cost savings and increased efficiency.
The ability to detect and address issues in real-time reduces the amount of waste generated, as defective batches can be identified and corrected early in the process.
Moreover, the automation of monitoring tasks frees up operators to focus on other critical areas, improving overall productivity.
The reduction in waste and rework also translates to lower material and labor costs, contributing to a more efficient operation.
Applications and Case Studies
Automotive Industry
In the automotive industry, high-performance compounds are used in various components, such as engine parts, seals, and gaskets.
DX monitoring has enabled manufacturers to produce compounds with exceptional thermal and mechanical properties, ensuring reliability and longevity.
For example, a leading automotive parts supplier implemented DX monitoring in their compounding process, resulting in a 20% reduction in defects and a 15% increase in production efficiency.
Medical Devices
The medical device industry relies heavily on high-performance compounds for applications like prosthetics, implants, and medical tubing.
The stringent quality requirements in this industry make DX monitoring indispensable.
A case study of a medical device manufacturer revealed that using DX monitoring led to a 25% improvement in product quality and a 10% reduction in production costs.
The real-time data allowed the company to ensure that each batch met the strict regulatory standards, minimizing the risk of product recalls.
Challenges and Future Trends
Initial Investment
While the benefits of DX monitoring are substantial, the initial investment required for implementing the technology can be a challenge for some companies.
The cost of sensors, data analytics software, and integration with existing systems can be significant.
However, the long-term gains in terms of quality, efficiency, and cost savings often outweigh the initial expenses.
Data Security
With the increasing reliance on digital technologies, data security becomes a critical concern.
Ensuring the confidentiality, integrity, and availability of the data collected is paramount.
Companies must invest in robust cybersecurity measures to protect sensitive information from potential breaches.
Future Trends
Looking ahead, we can expect to see further advancements in DX monitoring technologies.
Emerging trends such as the Internet of Things (IoT), artificial intelligence (AI), and machine learning will continue to drive innovation in this field.
These technologies will enable even more precise monitoring and control of the compounding process, leading to higher quality compounds and more efficient operations.
In conclusion, the integration of DX monitoring in the compounding process has revolutionized the production of high-performance compounds.
By leveraging advanced technologies, companies can achieve superior quality, consistency, and efficiency.
While challenges exist, the long-term benefits make it a worthwhile investment. As digital transformation continues to evolve, the future looks promising for industries relying on high-performance compounds.
資料ダウンロード
QCD調達購買管理クラウド「newji」は、調達購買部門で必要なQCD管理全てを備えた、現場特化型兼クラウド型の今世紀最高の購買管理システムとなります。
ユーザー登録
調達購買業務の効率化だけでなく、システムを導入することで、コスト削減や製品・資材のステータス可視化のほか、属人化していた購買情報の共有化による内部不正防止や統制にも役立ちます。
NEWJI DX
製造業に特化したデジタルトランスフォーメーション(DX)の実現を目指す請負開発型のコンサルティングサービスです。AI、iPaaS、および先端の技術を駆使して、製造プロセスの効率化、業務効率化、チームワーク強化、コスト削減、品質向上を実現します。このサービスは、製造業の課題を深く理解し、それに対する最適なデジタルソリューションを提供することで、企業が持続的な成長とイノベーションを達成できるようサポートします。
オンライン講座
製造業、主に購買・調達部門にお勤めの方々に向けた情報を配信しております。
新任の方やベテランの方、管理職を対象とした幅広いコンテンツをご用意しております。
お問い合わせ
コストダウンが利益に直結する術だと理解していても、なかなか前に進めることができない状況。そんな時は、newjiのコストダウン自動化機能で大きく利益貢献しよう!
(Β版非公開)