- お役立ち記事
- DX of cutting process maximizes product life and production efficiency
DX of cutting process maximizes product life and production efficiency
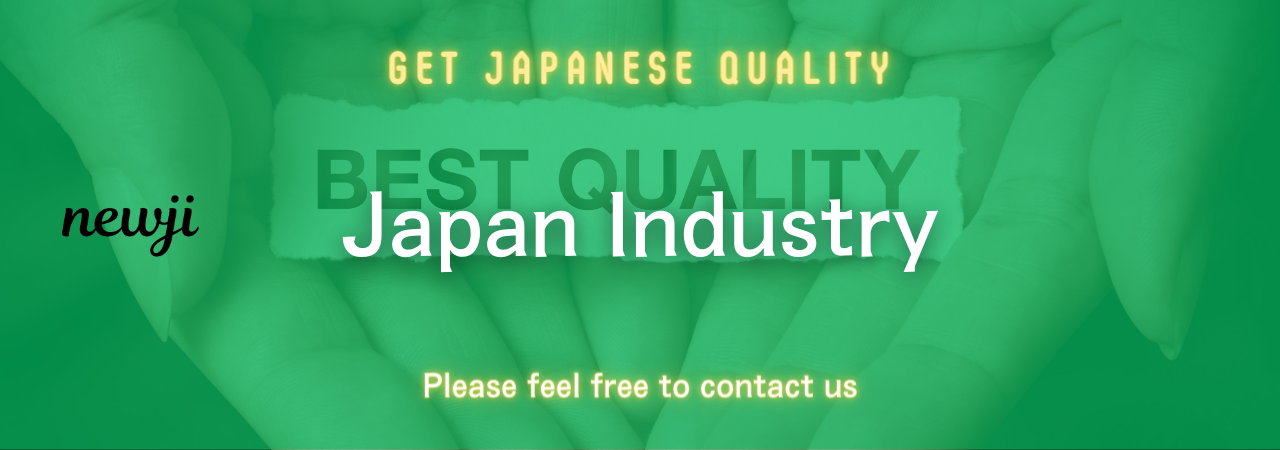
Digital transformation (DX) is revolutionizing various industries, and one area where it is proving to be a game-changer is the cutting process in manufacturing.
By embracing DX, businesses can significantly maximize product life and enhance production efficiency.
This article will explore how DX in the cutting process can benefit your business and provide a competitive edge.
目次
Understanding the Cutting Process
The cutting process in manufacturing involves the removal of material from a workpiece to achieve the desired shape and size.
It is a critical step in the production of various components, ranging from simple tools to complex machinery parts.
The traditional cutting process heavily relies on manual labor and conventional machinery, which can be time-consuming and prone to errors.
The Role of Digital Transformation
Digital transformation leverages digital technologies to innovate and improve business processes.
When applied to the cutting process, DX can transform traditional methods into more efficient and precise operations.
By integrating advanced software, automation, and data analytics, manufacturers can optimize their cutting processes.
Automation and Robotics
One of the most significant advancements brought about by DX is the use of automation and robotics.
Automated cutting machines, such as CNC (Computer Numerical Control) machines, can perform precise and complex cuts with minimal human intervention.
These machines can be programmed to follow intricate designs, ensuring consistent and accurate results.
This not only reduces the risk of human error but also increases production speed.
Data-Driven Decision Making
Digital transformation enables manufacturers to collect and analyze vast amounts of data from the cutting process.
By utilizing data analytics and machine learning algorithms, businesses can gain valuable insights into their operations.
For example, data analytics can identify patterns and trends in cutting performance, allowing manufacturers to make informed decisions.
This can lead to improved process efficiency and reduced downtime.
Benefits of DX in Cutting Processes
Embracing digital transformation in cutting processes offers numerous benefits to manufacturers.
Let’s explore some of these advantages in detail.
Increased Precision and Accuracy
Digital technologies provide unparalleled precision and accuracy in cutting operations.
Automated machines can consistently produce high-quality cuts, reducing the likelihood of defects.
This level of precision ensures that each component meets the required specifications, minimizing waste and rework.
Enhanced Productivity
Automation streamlines the cutting process, leading to increased productivity.
With automated machines, manufacturers can achieve higher production rates, as these machines can operate continuously without fatigue.
This results in faster turnaround times and improved overall efficiency.
Cost Savings
Digital transformation can lead to significant cost savings in various ways.
Firstly, automation reduces the need for manual labor, lowering labor costs.
Secondly, the improved precision and accuracy minimize material waste, reducing expenses on raw materials.
Additionally, predictive maintenance based on data analytics can prevent breakdowns and costly repairs.
Extended Tool Life
Digital technologies can optimize cutting parameters, such as speed and feed rates, to minimize tool wear and tear.
By using real-time data, manufacturers can adjust these parameters to extend the life of cutting tools.
This reduces the frequency of tool replacements, leading to cost savings and uninterrupted production.
Quality Control and Traceability
Digital transformation enables better quality control throughout the cutting process.
By monitoring and recording data at each stage, manufacturers can trace any issues back to their source.
This traceability ensures that any defects can be identified and addressed promptly, maintaining product quality standards.
Implementing Digital Transformation
While the benefits of DX in cutting processes are clear, implementing it requires careful planning and execution.
Here are some steps to consider for a successful DX implementation.
Assess Current Processes
Before embarking on a digital transformation journey, it is essential to assess your current cutting processes.
Identify areas where improvements are needed and determine the specific goals you want to achieve with DX.
This assessment will help you prioritize and allocate resources effectively.
Invest in Technology
To leverage DX, invest in advanced cutting machinery and software.
CNC machines, automation systems, and data analytics tools are some of the key technologies to consider.
Ensure that these technologies are compatible with your existing infrastructure and can be seamlessly integrated.
Train and Upskill Workforce
Digital transformation requires a skilled workforce capable of operating and maintaining advanced machinery.
Provide training and upskilling programs for your employees to ensure they can effectively use the new technologies.
This will also boost employee morale and foster a culture of innovation.
Data Collection and Analysis
Implement data collection systems to gather valuable information from the cutting process.
Install sensors and monitoring devices to capture real-time data on machine performance, tool wear, and other critical parameters.
Utilize data analytics software to analyze this data and derive actionable insights.
Continuous Improvement
Digital transformation is an ongoing process that requires continuous improvement.
Regularly review and analyze data to identify areas for optimization.
Implement feedback loops to gather input from employees and stakeholders, and make necessary adjustments to enhance efficiency further.
Conclusion
Digital transformation is reshaping the cutting process in manufacturing, offering numerous benefits to businesses.
By embracing automation, data-driven decision-making, and advanced technologies, manufacturers can achieve increased precision, productivity, and cost savings.
Implementing DX requires careful planning, investment in technology, and upskilling the workforce.
However, the long-term benefits make it a worthwhile endeavor.
Embrace digital transformation in your cutting processes to maximize product life and production efficiency, and stay ahead in today’s competitive market.
資料ダウンロード
QCD調達購買管理クラウド「newji」は、調達購買部門で必要なQCD管理全てを備えた、現場特化型兼クラウド型の今世紀最高の購買管理システムとなります。
ユーザー登録
調達購買業務の効率化だけでなく、システムを導入することで、コスト削減や製品・資材のステータス可視化のほか、属人化していた購買情報の共有化による内部不正防止や統制にも役立ちます。
NEWJI DX
製造業に特化したデジタルトランスフォーメーション(DX)の実現を目指す請負開発型のコンサルティングサービスです。AI、iPaaS、および先端の技術を駆使して、製造プロセスの効率化、業務効率化、チームワーク強化、コスト削減、品質向上を実現します。このサービスは、製造業の課題を深く理解し、それに対する最適なデジタルソリューションを提供することで、企業が持続的な成長とイノベーションを達成できるようサポートします。
オンライン講座
製造業、主に購買・調達部門にお勤めの方々に向けた情報を配信しております。
新任の方やベテランの方、管理職を対象とした幅広いコンテンツをご用意しております。
お問い合わせ
コストダウンが利益に直結する術だと理解していても、なかなか前に進めることができない状況。そんな時は、newjiのコストダウン自動化機能で大きく利益貢献しよう!
(Β版非公開)