- お役立ち記事
- DX of CVD processes maximizes semiconductor performance and yield
月間77,185名の
製造業ご担当者様が閲覧しています*
*2025年2月28日現在のGoogle Analyticsのデータより
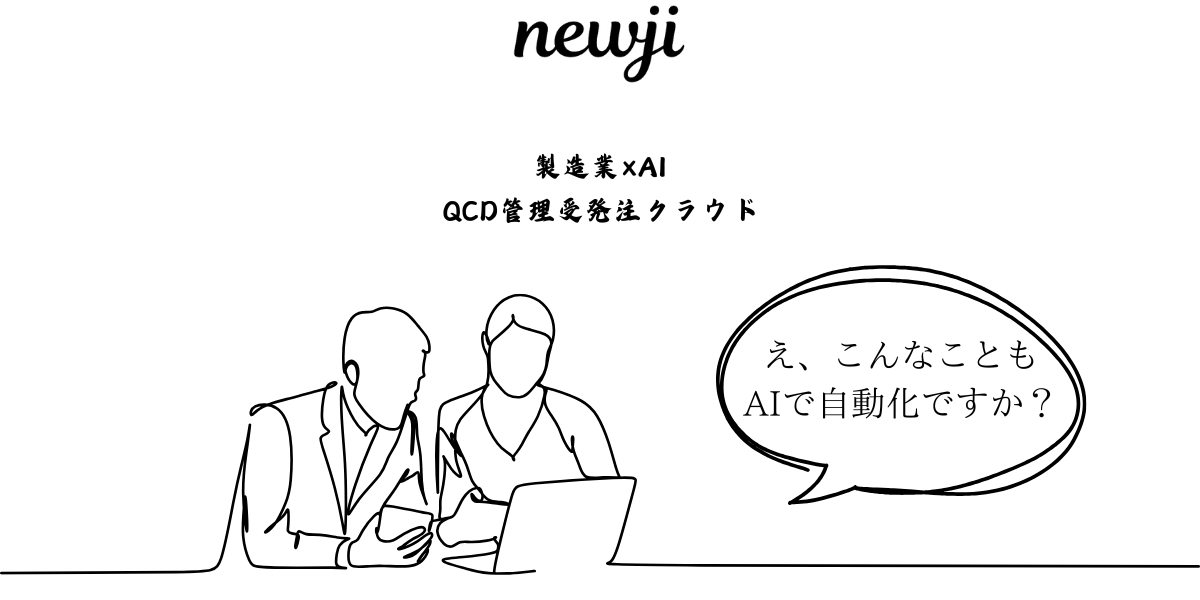
DX of CVD processes maximizes semiconductor performance and yield
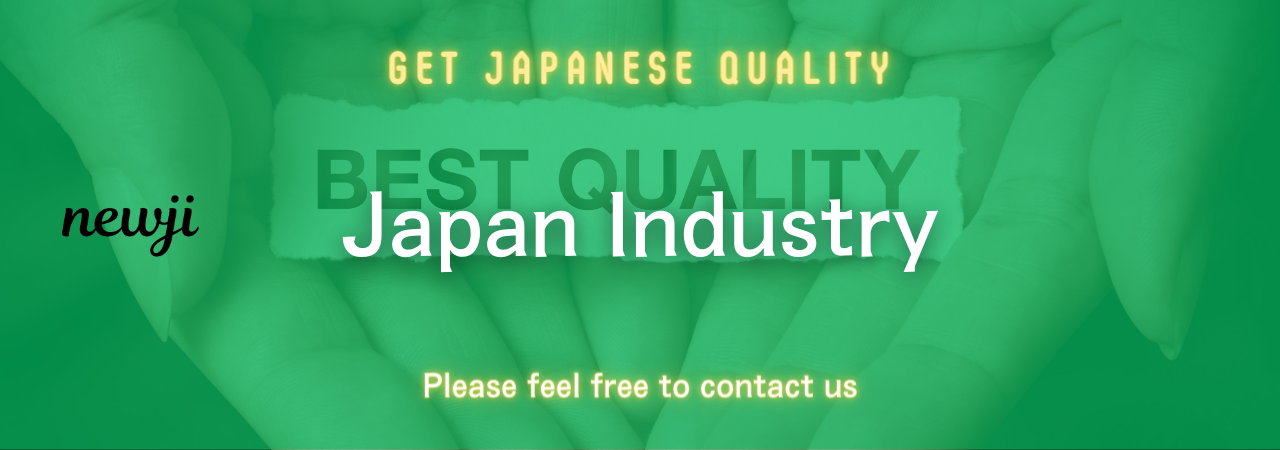
In today’s rapidly evolving technological landscape, the digital transformation (DX) of chemical vapor deposition (CVD) processes plays a crucial role in enhancing the performance and yield of semiconductors.
Understanding how DX impacts these processes can help companies stay competitive and innovative.
In this article, we’ll explore how digital transformation can be harnessed to maximize semiconductor performance and yield.
目次
What is Digital Transformation (DX)?
Digital transformation, or DX, refers to the integration of digital technologies into various aspects of a business.
It goes beyond mere digitization, involving fundamental changes in business operations, culture, and customer experiences.
DX aims to improve efficiency, foster innovation, and create value for stakeholders.
When applied to semiconductor manufacturing, digital transformation can significantly enhance processes such as chemical vapor deposition (CVD).
Understanding Chemical Vapor Deposition (CVD)
Chemical Vapor Deposition (CVD) is a vital process in semiconductor manufacturing.
It involves the deposition of thin films onto substrates through chemical reactions of vapor-phase precursors.
CVD is used to create various layers, such as insulating, conductive, or semiconducting films.
These layers are crucial for the functioning and performance of semiconductor devices.
Types of CVD Processes
There are several types of CVD processes, including:
1. **Thermal CVD**: This method uses heat to decompose gaseous precursors, forming the desired film on the substrate.
2. **Plasma-Enhanced CVD (PECVD)**: In this process, plasma is used to enhance the chemical reactions at lower temperatures.
3. **Metal-Organic CVD (MOCVD)**: This technique uses metal-organic precursors to deposit thin films, often used in compound semiconductor manufacturing.
Understanding these different CVD techniques is essential when considering how digital transformation can optimize these processes.
The Role of DX in CVD Processes
Digital transformation can revolutionize CVD processes in several ways, improving performance and yield in semiconductor manufacturing.
Process Monitoring and Control
By integrating advanced sensors and data analytics, digital transformation allows for real-time monitoring and control of CVD processes.
This level of oversight ensures that the processes are operating within optimal parameters, reducing the likelihood of defects and variations.
For instance, temperature, pressure, and gas flow rates can be continuously monitored and adjusted to maintain consistent film quality.
Predictive Maintenance
Digital transformation enables predictive maintenance, which can significantly reduce downtime and maintenance costs.
By analyzing historical and real-time data from CVD equipment, predictive algorithms can identify potential issues before they become critical.
This proactive approach minimizes disruptions and maintains seamless production flows.
Data-Driven Decision Making
The adoption of big data and machine learning in CVD processes facilitates data-driven decision making.
Manufacturers can analyze vast amounts of data generated during the deposition process to identify trends, correlations, and anomalies.
This information helps engineers make informed decisions to optimize parameters, improve film uniformity, and reduce errors.
Maximizing Semiconductor Performance
High-performance semiconductors are essential for modern electronic devices. Digital transformation of CVD processes can directly impact semiconductor performance in several ways.
Enhanced Film Quality
By implementing digital technologies, manufacturers can achieve more precise control over deposition conditions.
This precision results in films with superior thickness uniformity, better material properties, and fewer defects.
Consequently, the performance of semiconductor devices, such as transistors and memory chips, is significantly improved.
Reduced Contamination
Contamination during CVD processes can degrade semiconductor performance.
Digital transformation allows for real-time contamination monitoring and control.
Advanced sensors can detect the presence of contaminants, enabling immediate corrective actions to maintain a pristine deposition environment.
Process Optimization
Digital transformation facilitates the continuous optimization of CVD parameters.
Machine learning algorithms can analyze process data to identify optimal conditions for specific film properties.
This iterative optimization leads to higher-performing films, which in turn improve the overall performance of semiconductor devices.
Boosting Yield in Semiconductor Manufacturing
Yield is a critical factor in semiconductor manufacturing, affecting both production costs and profitability.
Digital transformation of CVD processes can help boost yield in several ways.
Defect Reduction
By continuously monitoring and controlling CVD processes, digital transformation minimizes the occurrence of defects.
Sensors and analytics can identify variations in real-time, allowing for instant corrections.
As a result, fewer defective wafers are produced, increasing the overall yield.
Enhanced Reproducibility
Reproducibility is vital in semiconductor manufacturing to ensure consistent quality across batches.
Digital transformation enables the precise replication of optimal CVD parameters, leading to more uniform and higher-quality films.
This consistency results in higher yields and reduced waste.
Efficient Resource Utilization
Digital transformation allows for efficient resource utilization in CVD processes.
Real-time data analytics optimize the usage of precursors, gases, and energy.
This efficiency not only lowers production costs but also contributes to higher yields by minimizing waste and improving process efficiency.
Conclusion
The digital transformation of chemical vapor deposition processes holds immense potential for maximizing semiconductor performance and yield.
By integrating advanced sensors, data analytics, and machine learning, manufacturers can achieve precise control, predictive maintenance, and data-driven decision-making.
These advancements lead to enhanced film quality, reduced contamination, and optimized processes.
Ultimately, digital transformation enables semiconductor manufacturers to stay competitive, innovate continuously, and deliver high-performance devices to meet the demands of the modern world.
資料ダウンロード
QCD管理受発注クラウド「newji」は、受発注部門で必要なQCD管理全てを備えた、現場特化型兼クラウド型の今世紀最高の受発注管理システムとなります。
ユーザー登録
受発注業務の効率化だけでなく、システムを導入することで、コスト削減や製品・資材のステータス可視化のほか、属人化していた受発注情報の共有化による内部不正防止や統制にも役立ちます。
NEWJI DX
製造業に特化したデジタルトランスフォーメーション(DX)の実現を目指す請負開発型のコンサルティングサービスです。AI、iPaaS、および先端の技術を駆使して、製造プロセスの効率化、業務効率化、チームワーク強化、コスト削減、品質向上を実現します。このサービスは、製造業の課題を深く理解し、それに対する最適なデジタルソリューションを提供することで、企業が持続的な成長とイノベーションを達成できるようサポートします。
製造業ニュース解説
製造業、主に購買・調達部門にお勤めの方々に向けた情報を配信しております。
新任の方やベテランの方、管理職を対象とした幅広いコンテンツをご用意しております。
お問い合わせ
コストダウンが利益に直結する術だと理解していても、なかなか前に進めることができない状況。そんな時は、newjiのコストダウン自動化機能で大きく利益貢献しよう!
(β版非公開)