- お役立ち記事
- DX of electrodeposition coating process maximizes coating film quality and production efficiency
DX of electrodeposition coating process maximizes coating film quality and production efficiency
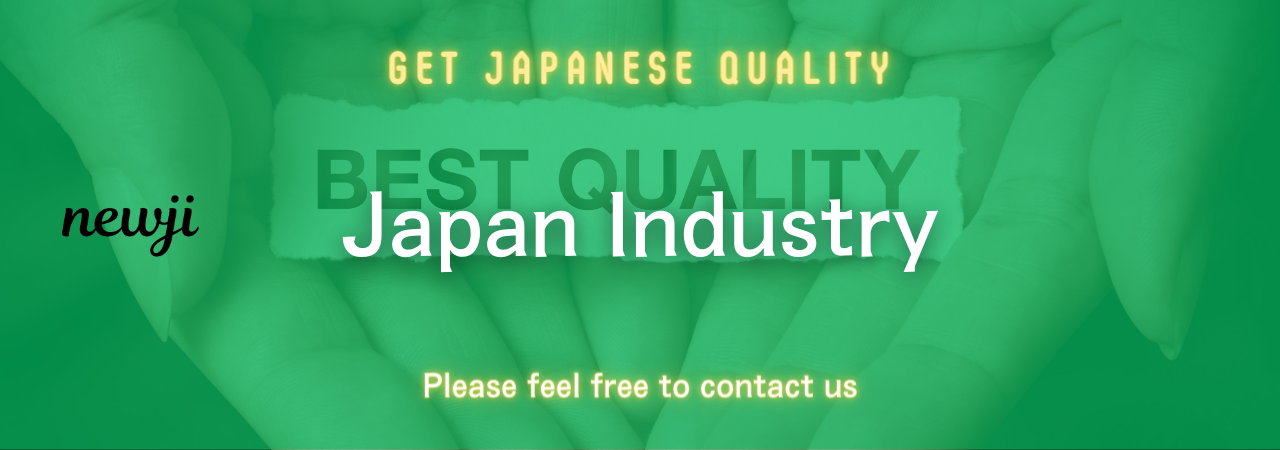
The process of electrodeposition coating, often abbreviated as E-coating, is fundamental in various industries, including automotive, electronics, and appliances.
The goal is to deliver high-quality coating films that improve corrosion resistance and aesthetic appeal while ensuring durability.
With the advent of digital transformation (DX), manufacturing and production processes, including electrodeposition coating, have seen significant improvements.
DX refers to integrating digital technologies into all areas of a business, fundamentally changing how it operates and delivers value to customers.
目次
The Role of Digital Transformation in Electrodeposition Coating
Digital transformation brings a new level of precision and control to the electrodeposition coating process.
It involves utilizing advanced technologies such as the Internet of Things (IoT), machine learning, and big data analytics.
These technologies help monitor and optimize various parameters that affect the coating process.
Enhanced Monitoring and Control
One of the most evident benefits of digital transformation in the electrodeposition coating process is the enhanced ability to monitor and control every aspect of the operation.
Sensors and IoT devices can be installed throughout the production line to collect real-time data.
This data includes temperature, voltage, current, pH levels, and bath composition.
Operators can monitor these parameters via dashboards, making it easier to maintain optimal conditions.
Improvement in Coating Film Quality
Quality is paramount when it comes to electrodeposition coating.
Digital transformation enables precise control over the coating parameters, leading to consistent and high-quality coating films.
Advanced analytics can detect even the slightest deviations from the desired norms, allowing for immediate corrective actions.
Machine learning algorithms can predict potential issues and suggest solutions before any defects occur.
This predictive maintenance ensures minimal downtime and high coating quality.
Production Efficiency Maximized
The introduction of digital technologies into the electrodeposition coating process leads to significant enhancements in production efficiency.
This transformation involves not only the optimization of existing processes but also the invention of new, more efficient methodologies.
Optimized Resource Utilization
With real-time monitoring and analytics, manufacturers can optimize the use of resources such as raw materials, energy, and labor.
For instance, IoT sensors can detect when the coating bath requires replenishment or when the power settings need adjustment.
Such prompt actions reduce waste and help in utilizing resources effectively.
The real-time feedback loop ensures that resources are used to their maximum potential, leading to cost savings.
Reduced Production Time
Automation facilitated by digital transformation speeds up the electrodeposition coating process.
Robotic arms and automated systems can perform tasks faster and more accurately than human operators.
For example, automated handling systems can quickly immerse and remove parts from the coating bath.
Furthermore, artificial intelligence can streamline workflow management, ensuring that each production phase is executed in the optimal order and with minimal delay. The cumulative effect is a significant reduction in overall production time.
Data-Driven Decision Making
Digital transformation paves the way for data-driven decision-making, enabling manufacturers to make informed choices based on real-time and historical data.
Predictive Analytics
Predictive analytics is a cornerstone of digital transformation in electrodeposition coating.
By analyzing historical data, machine learning models can predict future outcomes and trends.
For instance, they can identify patterns that indicate when equipment is likely to fail.
Manufacturers can then perform maintenance before breakdowns occur, reducing downtime and maintaining steady production rates.
Customized Production
With data-driven insights, manufacturers can customize production processes to meet specific customer requirements.
This can include adjusting coating thickness, color, or other attributes to match customer specifications.
Such flexibility enhances customer satisfaction and opens up new market opportunities.
Sustainability and Compliance
Sustainability has become a critical concern for modern manufacturers.
Digital transformation contributes significantly to sustainable practices in electrodeposition coating.
Energy Efficiency
Optimizing energy consumption is a key benefit of digital transformation.
Advanced systems can monitor energy use in real time and identify areas where improvements can be made.
For instance, adjusting the power supplied to the coating bath based on real-time data can save energy without compromising the quality.
Over time, these incremental improvements lead to substantial energy savings.
Compliance with Regulations
Manufacturers must comply with various environmental and safety regulations.
Digital systems can ensure that all processes adhere to these regulations.
For example, real-time monitoring of emissions and waste products ensures that they remain within permissible limits.
Compliance reports can be generated automatically, reducing the administrative burden and ensuring transparency.
Implementation Challenges and Solutions
While the benefits of digital transformation in electrodeposition coating are clear, implementing these technologies comes with challenges.
Initial Investment
The initial investment required for digital transformation can be high.
This includes the cost of sensors, IoT devices, data analytics software, and training for personnel.
However, the long-term benefits such as reduced waste, improved quality, and increased production efficiency often outweigh the initial costs.
Integration with Existing Systems
Another challenge is integrating new digital technologies with existing systems.
Many manufacturing facilities operate with legacy systems that may not be compatible with modern digital solutions.
A phased approach, starting with pilot projects, can help in smooth integration.
Data Security
With the increased use of digital technologies, data security becomes a critical concern.
Implementing robust cybersecurity measures is essential to protect sensitive information.
Regular audits and updates can help in safeguarding against cyber threats.
In conclusion, the digital transformation of the electrodeposition coating process offers substantial benefits, including enhanced quality, improved efficiency, data-driven decision-making, and sustainability.
However, careful planning and execution are essential to overcome the challenges associated with implementation.
By leveraging advanced technologies, manufacturers can remain competitive and meet the ever-evolving demands of their customers.
資料ダウンロード
QCD調達購買管理クラウド「newji」は、調達購買部門で必要なQCD管理全てを備えた、現場特化型兼クラウド型の今世紀最高の購買管理システムとなります。
ユーザー登録
調達購買業務の効率化だけでなく、システムを導入することで、コスト削減や製品・資材のステータス可視化のほか、属人化していた購買情報の共有化による内部不正防止や統制にも役立ちます。
NEWJI DX
製造業に特化したデジタルトランスフォーメーション(DX)の実現を目指す請負開発型のコンサルティングサービスです。AI、iPaaS、および先端の技術を駆使して、製造プロセスの効率化、業務効率化、チームワーク強化、コスト削減、品質向上を実現します。このサービスは、製造業の課題を深く理解し、それに対する最適なデジタルソリューションを提供することで、企業が持続的な成長とイノベーションを達成できるようサポートします。
オンライン講座
製造業、主に購買・調達部門にお勤めの方々に向けた情報を配信しております。
新任の方やベテランの方、管理職を対象とした幅広いコンテンツをご用意しております。
お問い合わせ
コストダウンが利益に直結する術だと理解していても、なかなか前に進めることができない状況。そんな時は、newjiのコストダウン自動化機能で大きく利益貢献しよう!
(Β版非公開)