- お役立ち記事
- DX of etching process dramatically improves accuracy and productivity
月間76,176名の
製造業ご担当者様が閲覧しています*
*2025年3月31日現在のGoogle Analyticsのデータより
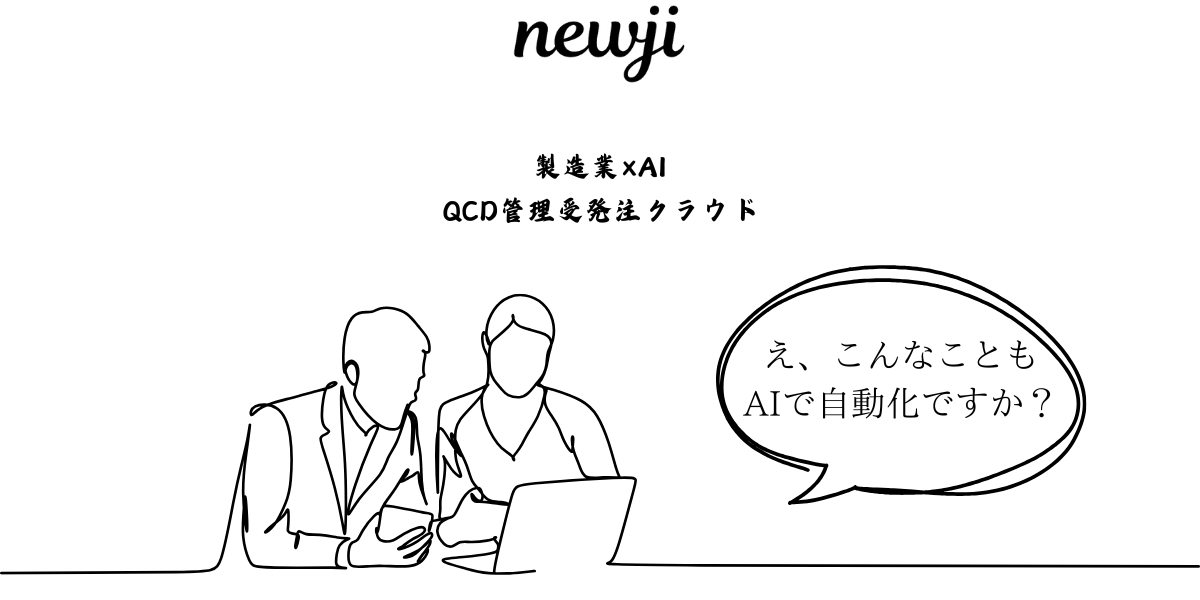
DX of etching process dramatically improves accuracy and productivity
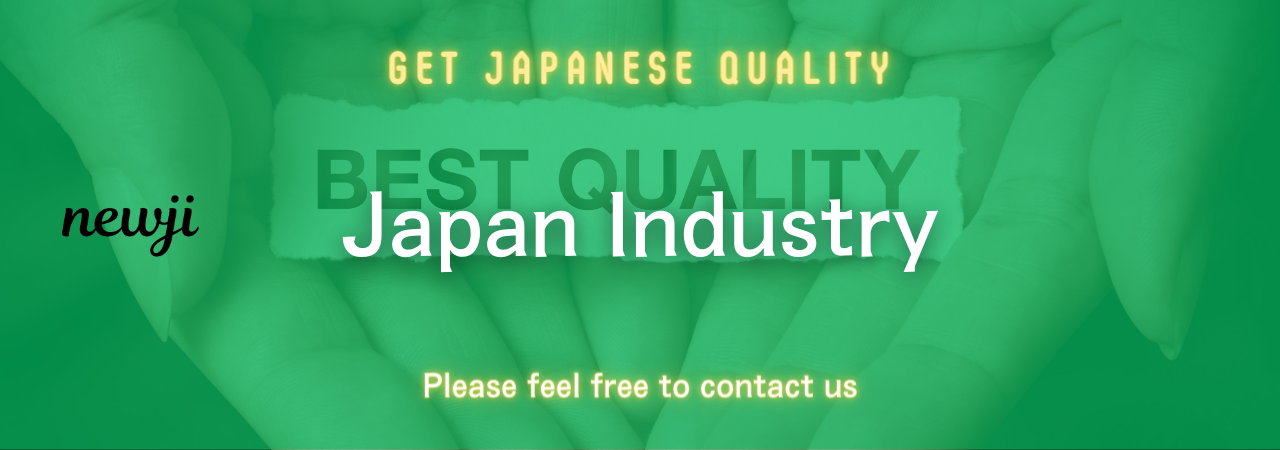
In recent years, the digital transformation (DX) of the etching process has brought significant improvements in both accuracy and productivity in the manufacturing industry.
As technology continues to evolve, factories are adopting advanced digital tools and techniques to enhance various stages of production, including etching.
This article will explore how DX is transforming the etching process and its impact on operational efficiency.
目次
Understanding the Etching Process
Etching is a crucial process in manufacturing that involves removing material from a surface to create a desired pattern or design.
It is commonly used in industries such as electronics, aerospace, and automotive to produce intricate components with high precision.
Traditional etching methods often rely on manual labor and chemical processes, which can be time-consuming and prone to errors.
Types of Etching Methods
There are several types of etching methods, each with its own advantages and applications.
Some of the most common methods include:
1. **Wet Etching:**
This method involves using chemical solutions to dissolve the material.
It is widely used due to its simplicity and cost-effectiveness.
2. **Dry Etching:**
In this method, plasma or reactive gases are used to remove material.
Dry etching offers higher precision and control compared to wet etching.
3. **Laser Etching:**
This technique utilizes laser beams to vaporize the material.
It is highly accurate and is commonly used for intricate designs and patterns.
The Role of Digital Transformation in Etching
Digital transformation in the etching process involves integrating modern technologies such as automation, data analytics, and the Internet of Things (IoT) into traditional manufacturing practices.
By leveraging these technologies, manufacturers can achieve greater efficiency, accuracy, and productivity.
Automation
Automation plays a critical role in the DX of the etching process.
Automated etching machines are capable of performing complex tasks with minimal human intervention.
This reduces the risk of human error and ensures consistent quality in the final product.
Automated systems can also operate continuously, leading to significant time savings and increased production volumes.
Data Analytics
Data analytics is another key component of digital transformation in etching.
By collecting and analyzing data from various stages of the etching process, manufacturers can gain valuable insights into performance and areas for improvement.
Advanced analytics tools can identify patterns and trends, enabling manufacturers to optimize processes and reduce waste.
Predictive analytics can also be used to anticipate equipment failures and schedule maintenance, minimizing downtime and improving overall efficiency.
Internet of Things (IoT)
The IoT connects etching machines and other equipment to a central network, allowing real-time monitoring and control.
IoT-enabled devices can communicate with each other, providing a seamless flow of information and enhancing coordination across the production line.
This connectivity enables manufacturers to respond quickly to changes in the production environment and make data-driven decisions to improve outcomes.
Benefits of DX in the Etching Process
The integration of digital tools and technologies in the etching process offers several benefits, including:
Enhanced Accuracy
The use of advanced technologies such as laser etching and automated systems ensures high precision and accuracy in the etching process.
This is particularly important for industries that require intricate designs and complex patterns.
With digital tools, manufacturers can achieve tighter tolerances and produce components with consistent quality.
Increased Productivity
Automation and data analytics significantly boost productivity by streamlining workflows and eliminating bottlenecks.
Automated etching machines can operate around the clock, leading to higher production rates and faster turnaround times.
Data-driven insights help optimize processes, reducing cycle times and improving overall efficiency.
Cost Savings
By reducing errors and minimizing waste, digital transformation helps lower production costs.
Automated systems require less manual labor, resulting in labor cost savings.
Predictive maintenance reduces downtime and extends the lifespan of equipment, further contributing to cost savings.
Improved Flexibility
Digital tools enable manufacturers to quickly adapt to changes in design specifications or production requirements.
Advanced software allows for easy adjustments to etching parameters, ensuring flexibility in meeting customer demands.
IoT-enabled systems provide real-time feedback, allowing manufacturers to make immediate adjustments and maintain optimal production conditions.
Challenges and Considerations
While the benefits of digital transformation in the etching process are substantial, there are also challenges that manufacturers need to consider.
Implementing new technologies requires significant investment in equipment and training.
Manufacturers need to ensure that their workforce is adequately trained to operate and maintain advanced systems.
Cybersecurity is another important consideration.
With the increased connectivity of IoT devices, manufacturers must protect their systems and data from potential cyber threats.
Robust security measures and protocols are essential to safeguard sensitive information and maintain the integrity of the production process.
Finally, manufacturers must carefully plan the integration of digital tools to ensure compatibility with existing systems.
A phased approach to implementation can help minimize disruption and ensure a smooth transition to new technologies.
The Future of DX in Etching
The digital transformation of the etching process is still in its early stages, and there is significant potential for further advancements.
As technology continues to evolve, we can expect to see even greater improvements in accuracy, productivity, and flexibility.
Future developments may include the use of artificial intelligence (AI) and machine learning to further enhance process optimization and decision-making.
AI algorithms can analyze vast amounts of data to identify patterns and predict outcomes, enabling even more precise control over the etching process.
Additionally, advancements in materials science and nanotechnology may lead to new etching techniques with unprecedented accuracy and capabilities.
Conclusion
The digital transformation of the etching process is revolutionizing the manufacturing industry by enhancing accuracy, productivity, and cost efficiency.
By leveraging advanced technologies such as automation, data analytics, and the Internet of Things, manufacturers can achieve significant improvements in their operations.
While there are challenges to consider, the benefits far outweigh the risks, making digital transformation a worthwhile investment.
As we look to the future, continued innovation in digital tools and techniques will drive further advancements, ensuring that the etching process remains a critical component of modern manufacturing.
資料ダウンロード
QCD管理受発注クラウド「newji」は、受発注部門で必要なQCD管理全てを備えた、現場特化型兼クラウド型の今世紀最高の受発注管理システムとなります。
ユーザー登録
受発注業務の効率化だけでなく、システムを導入することで、コスト削減や製品・資材のステータス可視化のほか、属人化していた受発注情報の共有化による内部不正防止や統制にも役立ちます。
NEWJI DX
製造業に特化したデジタルトランスフォーメーション(DX)の実現を目指す請負開発型のコンサルティングサービスです。AI、iPaaS、および先端の技術を駆使して、製造プロセスの効率化、業務効率化、チームワーク強化、コスト削減、品質向上を実現します。このサービスは、製造業の課題を深く理解し、それに対する最適なデジタルソリューションを提供することで、企業が持続的な成長とイノベーションを達成できるようサポートします。
製造業ニュース解説
製造業、主に購買・調達部門にお勤めの方々に向けた情報を配信しております。
新任の方やベテランの方、管理職を対象とした幅広いコンテンツをご用意しております。
お問い合わせ
コストダウンが利益に直結する術だと理解していても、なかなか前に進めることができない状況。そんな時は、newjiのコストダウン自動化機能で大きく利益貢献しよう!
(β版非公開)