- お役立ち記事
- DX of etching process realizes miniaturization of semiconductors and productivity improvement
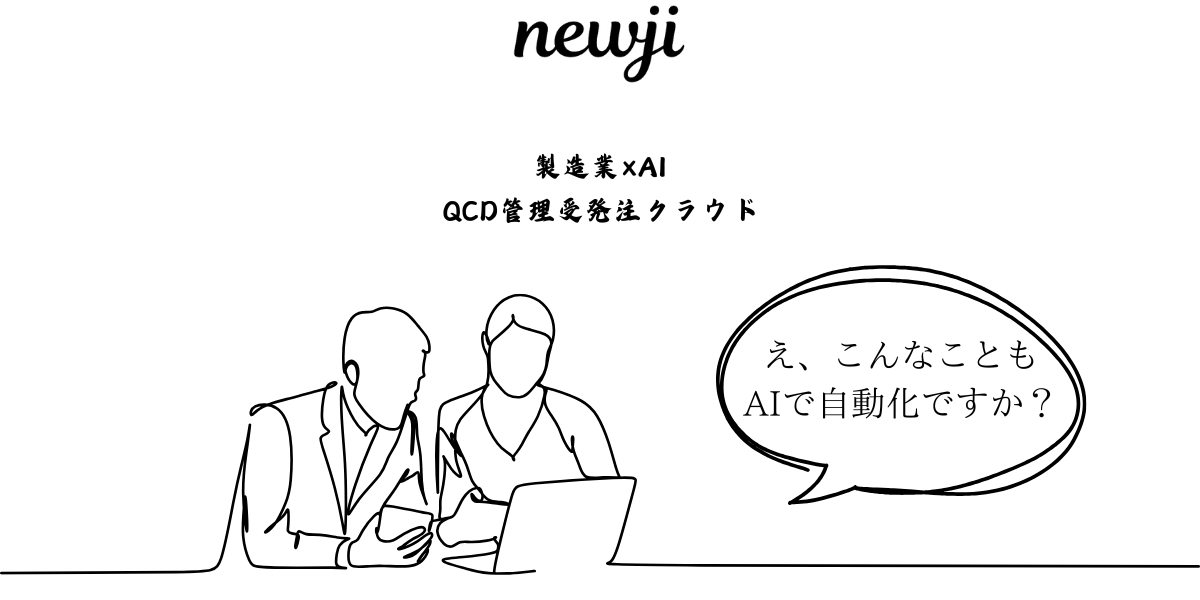
DX of etching process realizes miniaturization of semiconductors and productivity improvement
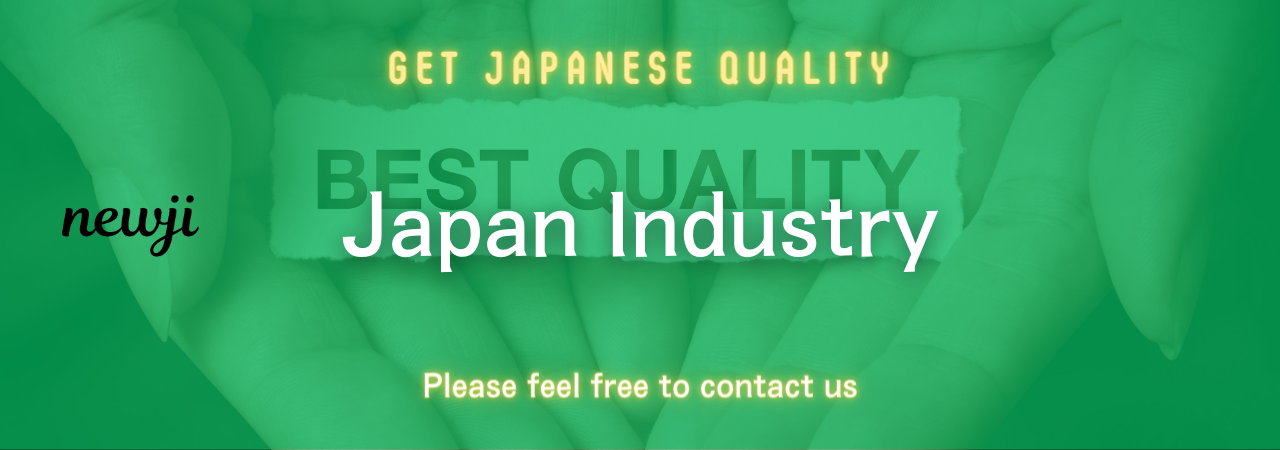
The world we live in today is powered by technology. From the smartphones in our pockets to the computers sitting on our desks, and the servers in vast data centers around the globe—semiconductors are at the heart of all these devices. As our society becomes more digitally driven, the demand for smaller, faster, and more powerful electronics is skyrocketing. This is where the Digital Transformation (DX) of etching processes comes into play, revolutionizing how semiconductors are made and helping us build the future of technology.
The etching process is a critical step in manufacturing semiconductors. It involves removing specific layers from the material to create intricate patterns and structures essential for semiconductor functionality. Traditionally, this process has been somewhat labor-intensive and time-consuming, making it challenging to keep up with the fast-paced demands of today’s technological advancements. However, with the advent of Digital Transformation, the etching process has become more efficient, precise, and capable of producing smaller semiconductor components.
Digital Transformation in etching has numerous advantages. For starters, it integrates advanced technologies such as artificial intelligence (AI), machine learning (ML), and automation into the production process. These technologies ensure consistency, quality, and speed, which are paramount in today’s semiconductor industry.
One of the critical benefits of DX in the etching process is miniaturization. As electronic devices continue to shrink in size while their functionalities expand, the demand for smaller semiconductor components grows. Automated etching systems, powered by AI and ML, can achieve incredibly high precision at the nanoscale level. By using advanced algorithms, these systems can predict and rectify errors in real-time, ensuring every semiconductor chip meets exact specifications. This means we can now produce chips that are not only smaller but also more powerful and efficient than ever before.
At the same time, Digital Transformation leads to significant improvements in productivity. Traditional etching methods often involve multiple steps and human intervention, leading to potential errors, slower production times, and higher costs. However, automated systems can operate continuously with minimal human supervision. By integrating IoT (Internet of Things) devices, manufacturers can monitor the process remotely and in real-time, making adjustments as needed. This reduces downtime and ensures that the production line runs smoothly, contributing to higher overall productivity.
Another area where DX of the etching process shows great promise is in improving quality control. Advanced sensors and imaging technologies can detect even the most minute defects in the semiconductor wafers during the etching process. By incorporating automated inspection systems, manufacturers can catch these defects early, reducing the number of defective products that reach the market. This ensures higher product quality and reliability, essential for maintaining consumer trust and meeting industry standards.
Moreover, the application of big data analytics in the DX process plays a crucial role. By collecting and analyzing vast amounts of data generated during the etching process, manufacturers can identify patterns and trends that may not be immediately apparent. This information can be used to fine-tune the etching process, optimize resource usage, and predict maintenance needs, leading to cost savings and enhanced performance.
Environmental sustainability is another vital aspect that the DX of the etching process addresses. Traditional semiconductor manufacturing processes can be resource-intensive and generate substantial waste. By optimizing the etching process through DX, manufacturers can reduce resource consumption and waste generation. For example, more precise etching reduces the need for raw materials and energy, while real-time monitoring helps in immediately detecting and fixing leaks or inefficiencies. This not only results in cost savings but also contributes to a greener production process, aligning with global environmental goals.
The DX of etching processes is also fueling innovation. With the ability to produce smaller and more complex semiconductor components, new possibilities are unlocked in various fields such as healthcare, automotive, and communications. For instance, in the healthcare sector, miniaturized semiconductor components are enabling the development of advanced medical devices and wearable technology, leading to better patient outcomes and more efficient healthcare delivery. In the automotive industry, smaller and more powerful semiconductors are paving the way for the development of autonomous vehicles and enhanced safety features, pushing the boundaries of what is possible. Communications technology is also benefiting, with more compact and efficient semiconductor components leading to faster and more reliable connectivity, an essential aspect of our increasingly connected world.
Furthermore, the DX of the etching process fosters collaboration and knowledge sharing within the industry. As manufacturers adopt new technologies and methods, they often work together to overcome challenges and share best practices. This collaborative approach accelerates technological advancements and helps the industry stay ahead of the curve in a competitive global market.
To keep pace with these transformations, companies need to invest in workforce training and development. The integration of advanced technologies in the etching process requires a skilled workforce capable of managing and optimizing these systems. Continuous training and upskilling programs ensure that employees remain knowledgeable and competent in the face of evolving technologies, helping companies maintain their competitive edge and drive innovation.
In conclusion, the Digital Transformation of the etching process is a game-changer for the semiconductor industry. By leveraging advanced technologies such as AI, ML, automation, IoT, and big data analytics, manufacturers can achieve unprecedented levels of precision, productivity, and quality in semiconductor production. This not only meets the growing demand for smaller and more powerful electronic devices but also drives innovation across various sectors. Additionally, the focus on environmental sustainability and workforce development ensures that the industry moves forward in a responsible and future-ready manner. As we continue to explore the possibilities of DX, the semiconductor industry will undoubtedly play a crucial role in shaping the technological landscape of tomorrow.
資料ダウンロード
QCD調達購買管理クラウド「newji」は、調達購買部門で必要なQCD管理全てを備えた、現場特化型兼クラウド型の今世紀最高の購買管理システムとなります。
ユーザー登録
調達購買業務の効率化だけでなく、システムを導入することで、コスト削減や製品・資材のステータス可視化のほか、属人化していた購買情報の共有化による内部不正防止や統制にも役立ちます。
NEWJI DX
製造業に特化したデジタルトランスフォーメーション(DX)の実現を目指す請負開発型のコンサルティングサービスです。AI、iPaaS、および先端の技術を駆使して、製造プロセスの効率化、業務効率化、チームワーク強化、コスト削減、品質向上を実現します。このサービスは、製造業の課題を深く理解し、それに対する最適なデジタルソリューションを提供することで、企業が持続的な成長とイノベーションを達成できるようサポートします。
オンライン講座
製造業、主に購買・調達部門にお勤めの方々に向けた情報を配信しております。
新任の方やベテランの方、管理職を対象とした幅広いコンテンツをご用意しております。
お問い合わせ
コストダウンが利益に直結する術だと理解していても、なかなか前に進めることができない状況。そんな時は、newjiのコストダウン自動化機能で大きく利益貢献しよう!
(Β版非公開)