- お役立ち記事
- DX of semiconductor wafers promotes high precision and high value-added
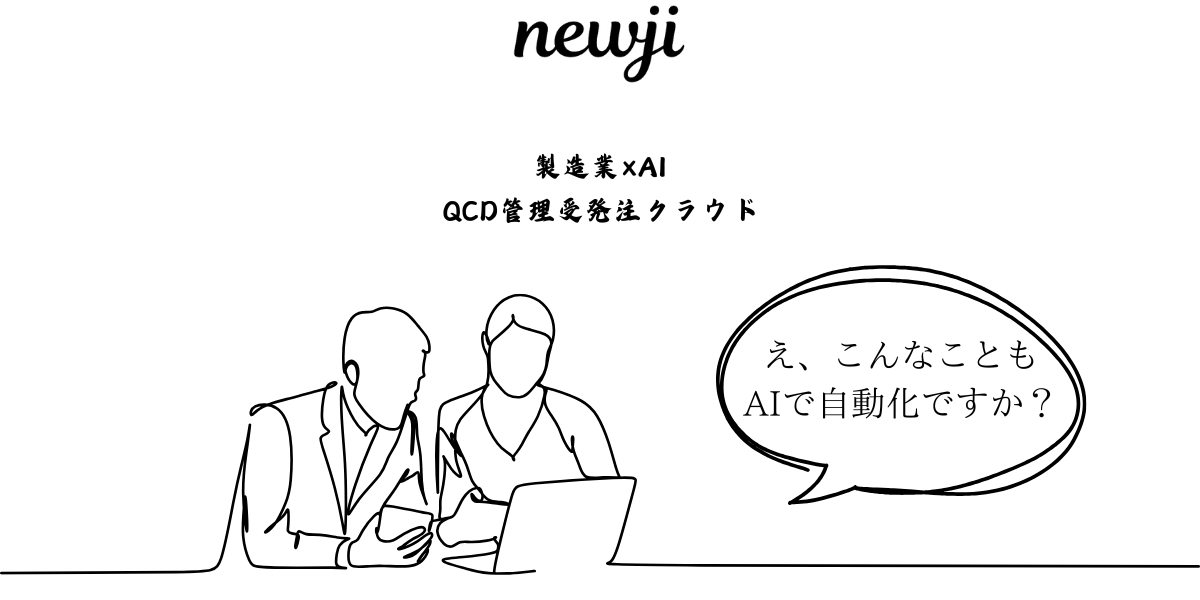
DX of semiconductor wafers promotes high precision and high value-added
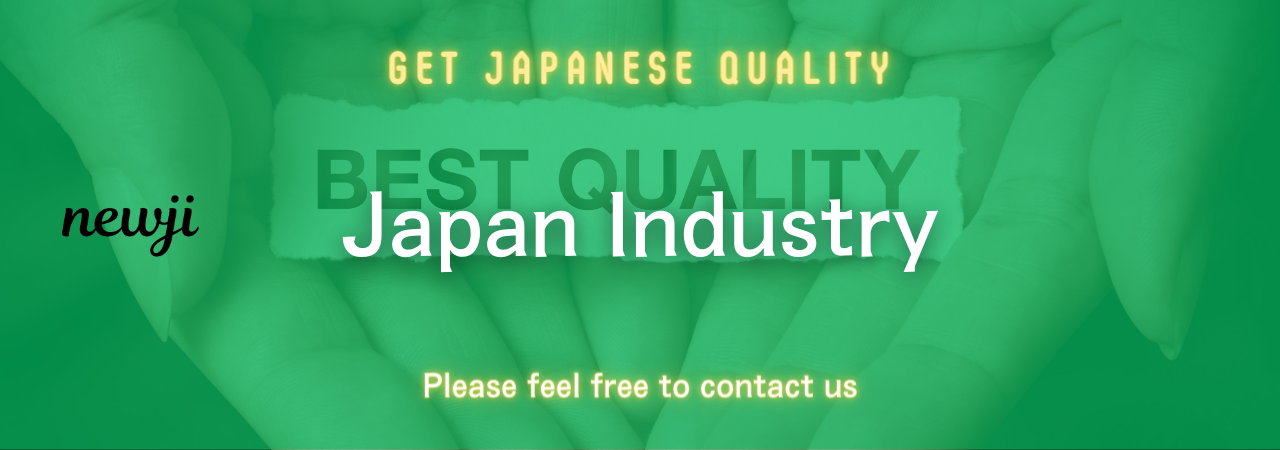
目次
Understanding DX in Semiconductor Wafers
Digital Transformation, often abbreviated as DX, is revolutionizing various industries.
One significant area where DX is making a substantial impact is in semiconductor wafers.
Semiconductor wafers are the foundation of numerous electronic devices, including computers, smartphones, and even advanced medical equipment.
With the advent of DX, the production and refinement of these wafers are now achieving higher precision and greater value-added benefits.
The Importance of Semiconductor Wafers
Before delving into how DX is promoting advancements, let’s understand the critical role semiconductor wafers play.
Semiconductor wafers are thin slices of semiconductor material, usually silicon, which serve as the substrate for microelectronic circuits.
These circuits are integral to almost every electronic device we use daily.
As technology progresses, the demand for more efficient, powerful, and smaller devices increases.
Thus, ensuring that semiconductor wafers are manufactured with the highest precision is essential for the progress of technology.
Traditional Methods vs. Digital Transformation
Traditionally, the manufacturing of semiconductor wafers involved several steps that required meticulous attention.
These steps included crystal growth, wafer slicing, polishing, and intricate etching processes.
Manual inspection and adjustments were standard practices, leading to potential human errors and inconsistencies.
However, with DX, many of these steps are now automated, which minimizes errors and maximizes efficiency.
Enhanced Precision through Automation
One of the standout benefits of DX in semiconductor wafers is enhanced precision.
Automation plays a pivotal role in achieving this.
Robotic arms and advanced machinery equipped with sensors can handle wafer materials with extreme accuracy.
The margin for error is significantly reduced as machines can consistently perform tasks without fatigue.
Precision in manufacturing leads to better performance of the end products, meeting the high standards of modern technology.
Smart Manufacturing Processes
DX brings smart manufacturing processes into the picture.
These processes integrate Internet of Things (IoT) devices and advanced analytics to monitor and control the production line.
Sensors embedded in machines collect real-time data, allowing for instant feedback and adjustments.
For instance, if a slight deviation in temperature during the wafer production is detected, the smart system can promptly correct it, ensuring optimal conditions are maintained.
Such real-time control dramatically improves the quality of the semiconductor wafers.
High Value-Added Benefits
Aside from precision, DX offers several value-added benefits that enhance the overall semiconductor wafer industry.
These benefits span from cost savings to innovation in new product development.
Reduced Costs and Enhanced Productivity
The integration of digital technologies helps in reducing operational costs.
Automation and smart manufacturing processes shorten production times and decrease material wastage.
Moreover, predictive maintenance made possible by IoT devices ensures machines function optimally.
By predicting when a machine is likely to fail, maintenance can be performed proactively, thus avoiding costly downtimes and repairs.
These efficiencies contribute significantly to cost savings while enhancing productivity.
Innovation in New Products
DX also fosters innovation.
By leveraging big data and advanced analytics, manufacturers can gain deeper insights into their processes.
These insights can drive innovation in new semiconductor products.
For example, data analytics might reveal potential improvements in wafer designs or materials that can lead to more energy-efficient or faster devices.
Artificial intelligence (AI) can simulate and predict outcomes of various manufacturing scenarios, accelerating the innovation cycle.
This continual innovation ensures that the semiconductor industry can meet the ever-evolving demands of the digital age.
Sustainability Considerations
Sustainability is another critical value-added benefit of DX.
Eco-friendly practices are becoming essential for modern industries, and DX helps semiconductor manufacturers in this regard.
By optimizing production processes and reducing waste, DX supports greener manufacturing practices.
Energy-efficient machines and processes not only save costs but also reduce the carbon footprint of semiconductor production.
Challenges and Future Prospects
While DX offers numerous benefits, it also presents some challenges that need to be addressed.
Integration Complexity
Implementing DX in semiconductor manufacturing requires the integration of various advanced technologies.
This integration can be complex and costly.
However, the long-term benefits often outweigh the initial investment.
Working with experienced technology providers and investing in workforce training can help mitigate integration challenges.
Data Security Concerns
With the proliferation of IoT devices and data analytics, data security becomes a significant concern.
Ensuring that sensitive information about manufacturing processes and intellectual property is secure is crucial.
Employing robust cybersecurity measures and protocols is essential to protect against data breaches.
The Road Ahead
The future of DX in semiconductor wafers looks promising.
Continuous advancements in technology and increasing demand for high-performance devices will drive further innovation.
Collaborative efforts between technology providers and semiconductor manufacturers will pave the way for more effective and efficient production processes.
As DX continues to evolve, the quality, precision, and value-added benefits of semiconductor wafers will undoubtedly keep improving, significantly impacting the wider technology landscape.
In conclusion, Digital Transformation in semiconductor wafers is not just a trend but a necessary evolution.
It promotes high precision, enhances value, and drives the industry forward.
By embracing DX, semiconductor manufacturers can stay ahead in an ever-competitive market, ensuring that they contribute to the development of the next generation of electronic devices.
資料ダウンロード
QCD調達購買管理クラウド「newji」は、調達購買部門で必要なQCD管理全てを備えた、現場特化型兼クラウド型の今世紀最高の購買管理システムとなります。
ユーザー登録
調達購買業務の効率化だけでなく、システムを導入することで、コスト削減や製品・資材のステータス可視化のほか、属人化していた購買情報の共有化による内部不正防止や統制にも役立ちます。
NEWJI DX
製造業に特化したデジタルトランスフォーメーション(DX)の実現を目指す請負開発型のコンサルティングサービスです。AI、iPaaS、および先端の技術を駆使して、製造プロセスの効率化、業務効率化、チームワーク強化、コスト削減、品質向上を実現します。このサービスは、製造業の課題を深く理解し、それに対する最適なデジタルソリューションを提供することで、企業が持続的な成長とイノベーションを達成できるようサポートします。
オンライン講座
製造業、主に購買・調達部門にお勤めの方々に向けた情報を配信しております。
新任の方やベテランの方、管理職を対象とした幅広いコンテンツをご用意しております。
お問い合わせ
コストダウンが利益に直結する術だと理解していても、なかなか前に進めることができない状況。そんな時は、newjiのコストダウン自動化機能で大きく利益貢献しよう!
(Β版非公開)