- お役立ち記事
- DX of the handing process achieves lean and optimal production
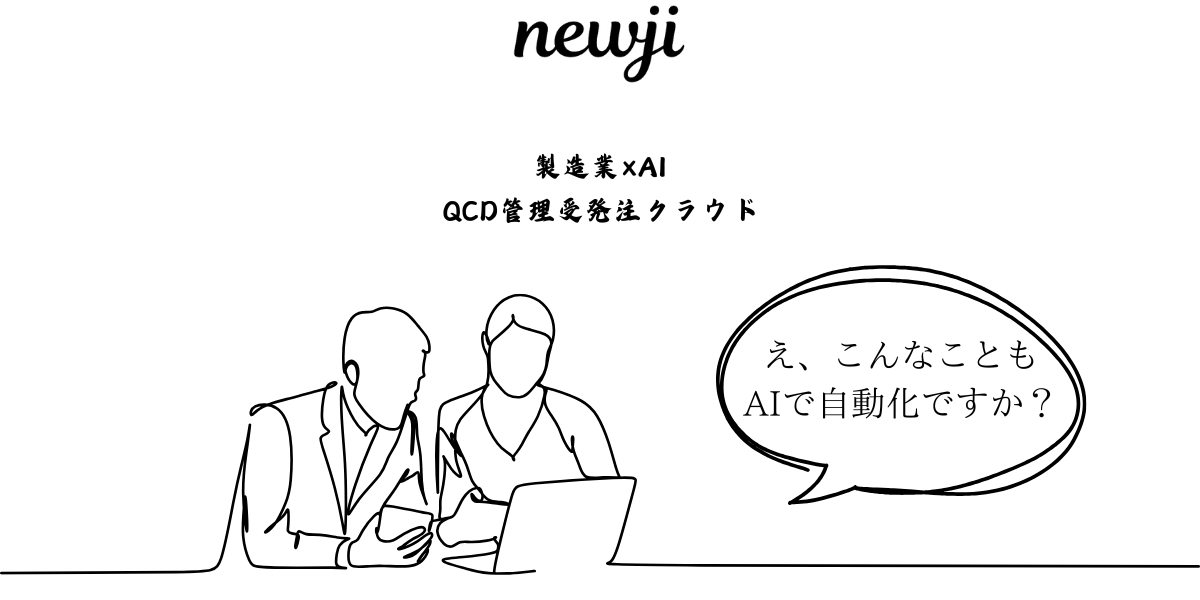
DX of the handing process achieves lean and optimal production
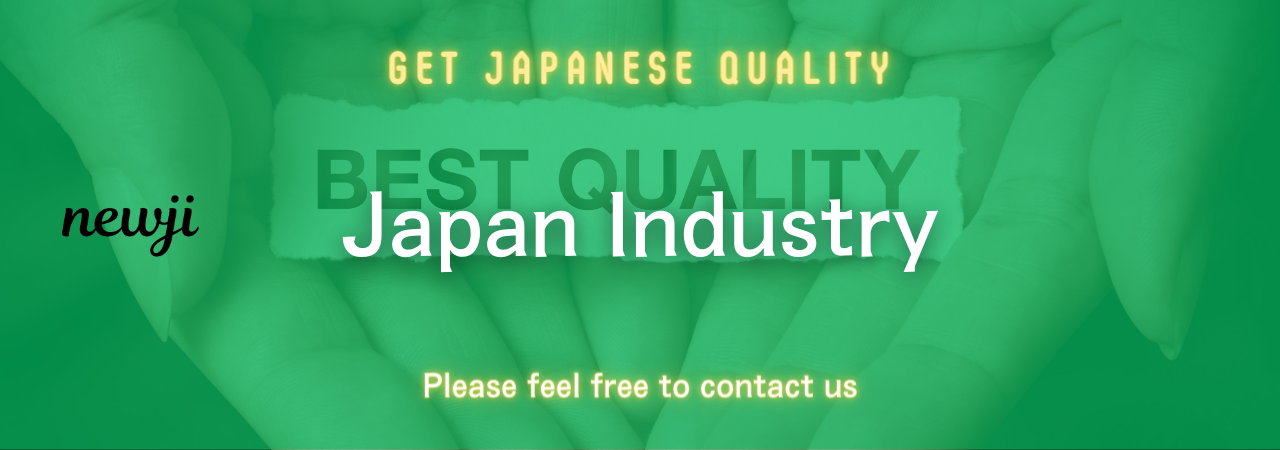
In today’s fast-paced manufacturing world, embracing digital transformation (DX) is not just an option, but a necessity.
One of the key areas where DX can drive significant improvements is the handing process.
This article will explore how digital transformation in the handing process can lead to lean and optimal production, enhancing efficiency and productivity.
目次
Understanding the Handing Process
The handing process, in a manufacturing context, refers to the transfer and movement of materials, components, and products within a factory.
This includes everything from the initial receipt of raw materials to the movement of finished products to storage or shipping areas.
Efficiency in this process is crucial, as any delays or errors can significantly impact overall production timelines and costs.
Challenges in Traditional Handing Process
Traditional handing processes often involve manual tasks, which are prone to human error.
Misplacements, delays in locating materials, and inefficient routing can disrupt production schedules.
Additionally, manual processes lack real-time visibility, making it difficult for management to monitor and optimize operations.
The Role of Digital Transformation
Digital transformation involves integrating digital technologies into various aspects of a business to streamline operations and improve efficiency.
In the context of the handing process, DX can revolutionize how materials are moved and managed within a factory.
Automation and Robotics
One of the primary ways DX can enhance the handing process is through automation and robotics.
Automated Guided Vehicles (AGVs) and robots can be used to transport materials efficiently and accurately.
These machines can follow pre-determined routes and schedules, minimizing the risk of human error and ensuring timely delivery of components.
Robotic systems can also be adapted to handle various types of materials, making them versatile tools in any production environment.
Real-Time Tracking and Monitoring
With digital transformation, real-time tracking and monitoring of materials become possible.
By using technologies such as RFID (Radio Frequency Identification) and IoT (Internet of Things), manufacturers can gain visibility into the location and status of materials at any given time.
This transparency allows for better inventory management, reducing the chances of overstocking or stockouts.
Moreover, real-time data can help identify bottlenecks and inefficiencies, enabling prompt corrective actions.
Benefits of Digital Transformation in Handing Process
The integration of digital technologies in the handing process yields several benefits that contribute to lean and optimal production.
Increased Efficiency
Digital tools and automation significantly reduce the time required for material handling.
AGVs and robots work faster and more accurately compared to manual labor.
This increase in speed and precision translates to shorter production cycles and higher throughput.
Cost Savings
While the initial investment in digital technologies may be significant, the long-term cost savings are substantial.
Automation reduces labor costs, and real-time inventory management minimizes waste and overproduction.
Additionally, improved efficiency leads to lower energy consumption, further cutting costs.
Enhanced Flexibility
Digital technologies offer greater flexibility in production processes.
Automated systems can be quickly reprogrammed to handle different tasks or routes, making it easier to adapt to changing production needs.
This agility is especially valuable in a market where demand can fluctuate rapidly.
Improved Safety
Automating the handing process enhances workplace safety by reducing the need for human workers to perform dangerous tasks.
Robots can handle heavy lifting and operate in hazardous environments, decreasing the risk of workplace injuries.
Implementing Digital Transformation
Embarking on the journey of digital transformation requires careful planning and execution.
Assess Current Processes
Start by thoroughly assessing your current handing processes.
Identify pain points and areas where inefficiencies are most prevalent.
This analysis will guide your DX strategy and help prioritize which technologies to implement first.
Select the Right Technologies
Not all digital tools will be suitable for every manufacturing environment.
Consider factors such as the type of materials handled, the size of your facility, and your budget.
Consult with technology providers to choose solutions that align with your specific needs and goals.
Train Your Workforce
Introducing new technologies will require training for your staff.
Ensure that your team understands how to operate and maintain the new systems.
Continuous training and support will help maximize the benefits of digital transformation.
Monitor and Optimize
Digital transformation is an ongoing process.
Regularly monitor the performance of your new systems and gather feedback from your team.
Use this data to make continuous improvements and ensure that your handing process remains lean and optimal.
The Future of Handing Processes in Manufacturing
As technology continues to evolve, the opportunities for further enhancing the handing process will expand.
Advancements in artificial intelligence, machine learning, and data analytics will enable even more sophisticated and efficient systems.
Manufacturers who stay ahead of these trends will benefit from greater competitiveness and the ability to meet customer demands more effectively.
Digital transformation of the handing process is a critical step towards achieving lean and optimal production.
By leveraging automation, real-time tracking, and other digital technologies, manufacturers can significantly improve efficiency, reduce costs, and enhance safety and flexibility.
Implementing DX requires careful planning and ongoing optimization, but the long-term benefits make it a worthwhile investment for any forward-thinking manufacturing business.
資料ダウンロード
QCD調達購買管理クラウド「newji」は、調達購買部門で必要なQCD管理全てを備えた、現場特化型兼クラウド型の今世紀最高の購買管理システムとなります。
ユーザー登録
調達購買業務の効率化だけでなく、システムを導入することで、コスト削減や製品・資材のステータス可視化のほか、属人化していた購買情報の共有化による内部不正防止や統制にも役立ちます。
NEWJI DX
製造業に特化したデジタルトランスフォーメーション(DX)の実現を目指す請負開発型のコンサルティングサービスです。AI、iPaaS、および先端の技術を駆使して、製造プロセスの効率化、業務効率化、チームワーク強化、コスト削減、品質向上を実現します。このサービスは、製造業の課題を深く理解し、それに対する最適なデジタルソリューションを提供することで、企業が持続的な成長とイノベーションを達成できるようサポートします。
オンライン講座
製造業、主に購買・調達部門にお勤めの方々に向けた情報を配信しております。
新任の方やベテランの方、管理職を対象とした幅広いコンテンツをご用意しております。
お問い合わせ
コストダウンが利益に直結する術だと理解していても、なかなか前に進めることができない状況。そんな時は、newjiのコストダウン自動化機能で大きく利益貢献しよう!
(Β版非公開)