- お役立ち記事
- DX of the shaving process contributes to higher product precision
DX of the shaving process contributes to higher product precision
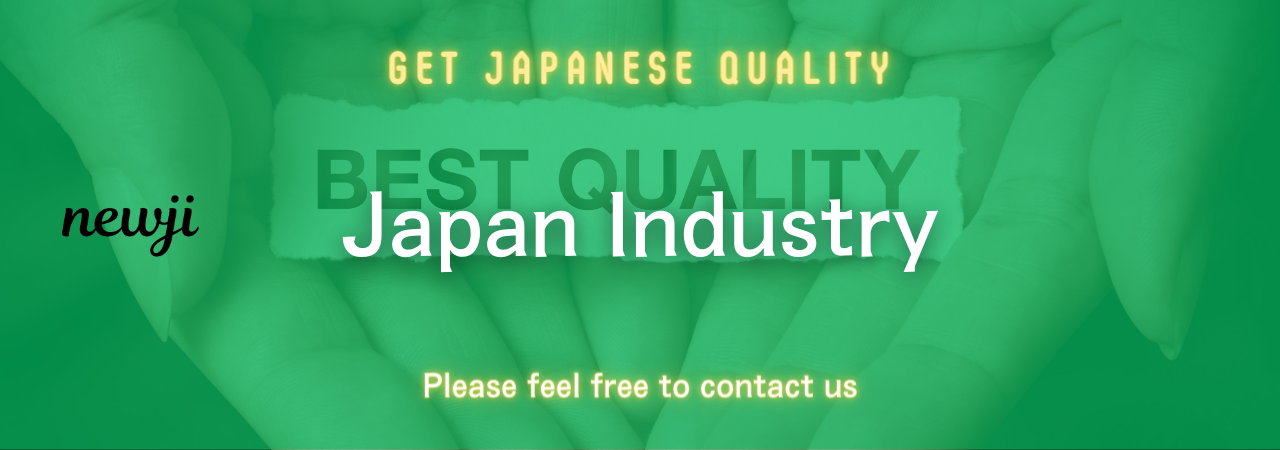
The Digital Transformation (DX) of the shaving process is creating a significant impact on the precision of manufactured products.
By leveraging advanced technology and automation, companies can now achieve greater accuracy and consistency in their shaving processes.
This not only enhances the quality of the finished product but also streamlines production, reducing waste and increasing efficiency.
目次
Understanding the Shaving Process
Before diving into how DX contributes to higher product precision, it is essential to understand the shaving process itself.
Shaving, in the industrial context, refers to the fine finishing of surfaces, typically using razor-sharp tools to shave minuscule layers of material off a workpiece.
This process is crucial in industries like automotive, aerospace, and manufacturing where parts with tight tolerances are required.
The goal is to achieve a smooth, precise, and accurate surface that meets stringent specifications.
Traditional Shaving Methods
Traditionally, the shaving process has relied on manual operations and semi-automated machinery.
Operators would use their experience and skill to manage the tooling, making adjustments as necessary to achieve the desired finish.
While experienced operators can achieve high precision, several challenges are inherent in traditional methods:
1. Human Error: Despite the skill of operators, manual processes are susceptible to human error.
2. Inconsistency: Variations in the manual operation can lead to inconsistency in product quality.
3. Time-Consuming: Traditional shaving is often a time-consuming process, affecting production efficiency.
The Role of DX in Modern Shaving Processes
The advent of digital transformation is revolutionizing the shaving process.
From integrating advanced sensors to deploying AI and machine learning algorithms, companies are adopting DX strategies to enhance precision and efficiency.
Benefits of Digital Transformation in Shaving
Implementing DX in the shaving process brings several benefits that collectively contribute to higher product precision.
Enhanced Precision and Accuracy
One of the most significant advantages of DX is the enhanced precision and accuracy it introduces to the shaving process.
Advanced CNC (Computer Numerical Control) machines equipped with high-resolution sensors can measure and control cutting parameters with incredible exactness.
This level of control ensures consistent quality and enables manufacturers to meet tighter tolerances than ever before.
Real-Time Monitoring and Feedback
Digital tools allow for real-time monitoring and feedback during the shaving process.
Sensors collect data on parameters such as tool wear, cutting speed, and surface smoothness.
This information is fed into a central system, where algorithms analyze it to make instant adjustments.
Real-time feedback loops help in correcting any discrepancies as they occur, preventing defects and ensuring consistent product precision.
Predictive Maintenance
Predictive maintenance, powered by DX technologies, plays a vital role in maintaining tool and machine health.
By analyzing data from sensors and historical performance metrics, predictive algorithms can forecast when a tool or machine is likely to fail or require maintenance.
This approach minimizes unplanned downtime and maintains optimal machine performance, leading to precise and accurate shaving operations.
Automated Quality Control
Automation is a key component of DX, and automated quality control systems are transforming the way industries ensure product precision.
Advanced vision systems and laser scanners inspect the shaved surfaces at various stages of production.
Automated systems can detect imperfections that a human eye might miss, ensuring that only products that meet the highest standards move forward in the production line.
Steps to Implement DX in Shaving Processes
Transforming traditional shaving processes through digital means requires a strategic approach.
Here are critical steps to consider:
Assessment and Planning
The first step is a thorough assessment of the existing shaving processes.
Identify key areas where digital tools can make a significant impact.
Develop a comprehensive plan that outlines the goals, required technologies, and the implementation timeline.
Invest in Advanced Technologies
Invest in advanced machinery and digital tools such as CNC machines, high-resolution sensors, and AI-driven analytics platforms.
Ensure that these technologies are compatible and can be integrated into one cohesive system.
Training and Skill Development
Equip your workforce with the skills needed to leverage new technologies effectively.
Provide training programs that cover both the operation of advanced machinery and the analysis of data generated by digital tools.
Skilled operators can better manage and interpret data, leading to more effective use of digital solutions.
Continuous Improvement
Implementing DX is not a one-time effort.
Regularly review the performance of the new shaving process, gather feedback, and make necessary adjustments.
Continuous improvement practices ensure that the process remains efficient and continues to deliver high product precision.
Case Study: DX in Automotive Shaving Processes
To illustrate the impact of DX, consider the automotive industry’s shaving processes.
Automotive manufacturers require high-precision parts for optimal vehicle performance and safety.
A leading automotive company decided to digitize its shaving process to improve the accuracy of its engine components.
The company invested in advanced CNC machines with integrated sensors and real-time monitoring capabilities.
AI algorithms analyzed the data, providing instant feedback and making adjustments to ensure each part met precise specifications.
The outcome was remarkable.
The company saw a significant reduction in defects and rework, leading to cost savings and increased production efficiency.
The overall quality of the engine components improved, contributing to better vehicle performance and customer satisfaction.
Conclusion
The Digital Transformation of the shaving process is a game-changer for industries requiring high precision and accuracy.
By adopting advanced technologies such as CNC machines, sensors, and AI-driven analytics, companies can enhance the quality of their products while also improving production efficiency.
As more industries embrace DX, the shaving process will continue to evolve, offering even greater precision and consistency in manufacturing.
Investing in digital transformation is not just about staying ahead of the competition but also ensuring the highest standards of quality and precision in today’s demanding market.
資料ダウンロード
QCD調達購買管理クラウド「newji」は、調達購買部門で必要なQCD管理全てを備えた、現場特化型兼クラウド型の今世紀最高の購買管理システムとなります。
ユーザー登録
調達購買業務の効率化だけでなく、システムを導入することで、コスト削減や製品・資材のステータス可視化のほか、属人化していた購買情報の共有化による内部不正防止や統制にも役立ちます。
NEWJI DX
製造業に特化したデジタルトランスフォーメーション(DX)の実現を目指す請負開発型のコンサルティングサービスです。AI、iPaaS、および先端の技術を駆使して、製造プロセスの効率化、業務効率化、チームワーク強化、コスト削減、品質向上を実現します。このサービスは、製造業の課題を深く理解し、それに対する最適なデジタルソリューションを提供することで、企業が持続的な成長とイノベーションを達成できるようサポートします。
オンライン講座
製造業、主に購買・調達部門にお勤めの方々に向けた情報を配信しております。
新任の方やベテランの方、管理職を対象とした幅広いコンテンツをご用意しております。
お問い合わせ
コストダウンが利益に直結する術だと理解していても、なかなか前に進めることができない状況。そんな時は、newjiのコストダウン自動化機能で大きく利益貢献しよう!
(Β版非公開)