- お役立ち記事
- DX of TPM (Total Production Maintenance) improves facility utilization rate and productivity
DX of TPM (Total Production Maintenance) improves facility utilization rate and productivity
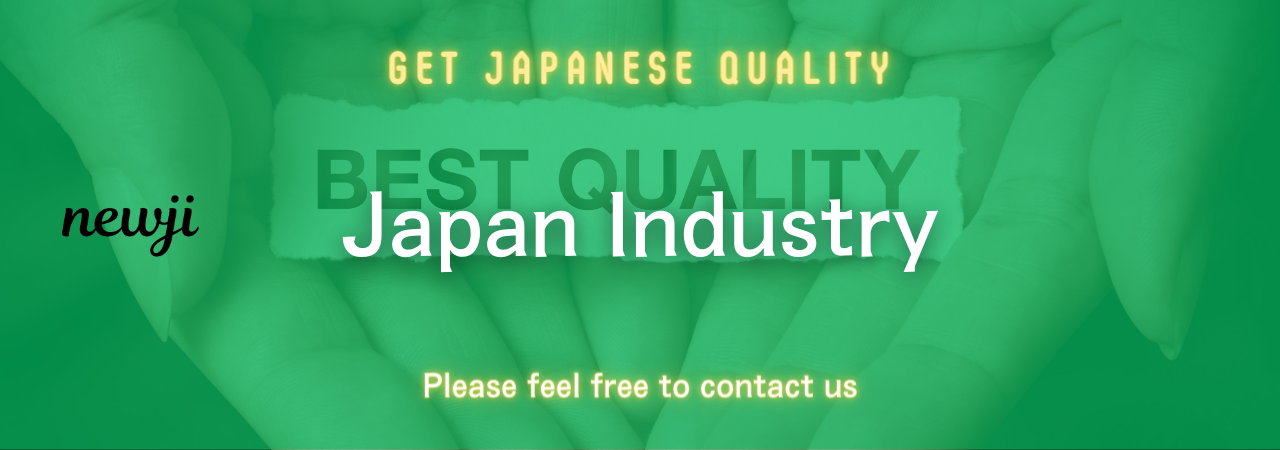
In today’s fast-paced manufacturing world, standing still can mean falling behind.
That’s where the concept of Digital Transformation (DX) of Total Productive Maintenance (TPM) comes into play.
By leveraging advanced technologies, companies can greatly improve facility utilization rates and productivity.
目次
Understanding Total Productive Maintenance (TPM)
Total Productive Maintenance is a thorough system for maintaining and improving production and the quality of systems through machines, equipment, processes, and employees.
It involves eight pillars which are each designed to add value to the production process:
1. Autonomous Maintenance.
2. Planned Maintenance.
3. Quality Maintenance.
4. Focused Improvement.
5. Early Equipment Management.
6. Training and Education.
7. Safety, Health, and Environment.
8. TPM in Administration.
Leveraging these pillars can help in minimizing downtime and increasing the efficiency of machinery.
The Role of Digital Transformation (DX) in TPM
Digital Transformation involves integrating digital technology into all areas of a business, fundamentally changing how you operate and deliver value to customers.
When applied to TPM, DX can take maintenance practices to the next level by utilizing technologies such as sensors, IoT, AI, and big data analytics.
Enhanced Predictive Maintenance
The traditional approach to maintenance often involves scheduled inspections and repairs.
This method, while better than reactive maintenance, can still cause unplanned downtime.
Predictive maintenance, powered by advanced sensors and IoT, monitors machine conditions in real-time.
Data collected can predict when a piece of equipment might fail, allowing timely interventions.
This approach helps in better planning of maintenance schedules, ultimately reducing downtime and enhancing productivity.
Real-Time Monitoring and Data Analysis
One of the big challenges in traditional TPM is the lack of real-time data.
Digital tools enable real-time monitoring and provide actionable insights.
For instance, dashboards can offer a birds-eye view of all equipment, making it easier to identify issues before they become serious problems.
Moreover, big data analytics can sift through vast amounts of data to identify patterns and anomalies.
This is crucial for preemptive actions, which can save both time and money.
Improved Resource Management
Optimizing resource utilization is another benefit of digitalizing TPM.
Labor and materials can be tracked and managed effectively, ensuring that resources are not wasted.
Software solutions can help in planning resources more efficiently, thus reducing costs and improving overall efficiency.
Benefits of DX in TPM
Increased Facility Utilization
Better maintenance schedules and predictive capabilities mean machines are running more and are less likely to break down.
This leads to higher facility utilization.
When machines are functioning smoothly, the entire production line is more efficient, leading to better output and less waste.
Boosted Productivity
By minimizing downtime, every aspect of production can proceed without interruption.
Real-time data can also optimize process flows, making production faster and more efficient.
With digital tools, issues can be resolved quickly, boosting the overall productivity of the plant.
Cost Savings
Reducing unplanned downtime and improving resource management naturally lead to significant cost savings.
Moreover, predictive maintenance technologies can extend the life of equipment, reducing the need for frequent replacements.
Better Quality Control
Maintaining machinery in optimal condition helps in producing higher-quality products.
Automated systems can quickly identify and rectify issues before they affect the production quality.
This leads to consistent product quality, reducing customer complaints and returns.
Implementing DX in TPM
Steps for Successful Implementation
1. **Assessment and Planning**: Evaluate current maintenance processes and identify areas for improvement through digital tools.
2. **Choosing the Right Technologies**: Select appropriate technologies that align with your business goals and existing infrastructure.
3. **Training and Education**: Equip your workforce with the necessary skills to operate new technologies.
4. **Integration and Testing**: Gradually integrate the new digital solutions while regularly testing and troubleshooting.
5. **Monitoring and Optimization**: Continually monitor the system’s performance and make necessary adjustments to optimize effectiveness.
Challenges to Consider
While DX of TPM promises numerous benefits, it’s essential to be aware of potential challenges.
The initial investment in technology can be high, but the long-term savings and increased efficiency generally outweigh the costs.
Additionally, the workforce may resist changes due to unfamiliarity.
Effective training and communication are crucial to overcoming this.
Finally, data security is a significant concern.
Implement robust security measures to protect sensitive information.
Conclusion
The DX of TPM is not just a trend but a necessity for modern manufacturing facilities aiming to improve their efficiency and productivity.
Through enhanced predictive maintenance, real-time monitoring, and better resource management, companies can significantly increase facility utilization rates and productivity.
Although initial investments and training are required, the long-term benefits make it a worthwhile endeavor.
By adopting a strategic approach, manufacturers can harness the power of digital technologies to propel their maintenance strategies and overall production capabilities.
資料ダウンロード
QCD調達購買管理クラウド「newji」は、調達購買部門で必要なQCD管理全てを備えた、現場特化型兼クラウド型の今世紀最高の購買管理システムとなります。
ユーザー登録
調達購買業務の効率化だけでなく、システムを導入することで、コスト削減や製品・資材のステータス可視化のほか、属人化していた購買情報の共有化による内部不正防止や統制にも役立ちます。
NEWJI DX
製造業に特化したデジタルトランスフォーメーション(DX)の実現を目指す請負開発型のコンサルティングサービスです。AI、iPaaS、および先端の技術を駆使して、製造プロセスの効率化、業務効率化、チームワーク強化、コスト削減、品質向上を実現します。このサービスは、製造業の課題を深く理解し、それに対する最適なデジタルソリューションを提供することで、企業が持続的な成長とイノベーションを達成できるようサポートします。
オンライン講座
製造業、主に購買・調達部門にお勤めの方々に向けた情報を配信しております。
新任の方やベテランの方、管理職を対象とした幅広いコンテンツをご用意しております。
お問い合わせ
コストダウンが利益に直結する術だと理解していても、なかなか前に進めることができない状況。そんな時は、newjiのコストダウン自動化機能で大きく利益貢献しよう!
(Β版非公開)