- お役立ち記事
- DX Solution to Prevent Splatter Optimization of the Coating Process
DX Solution to Prevent Splatter Optimization of the Coating Process
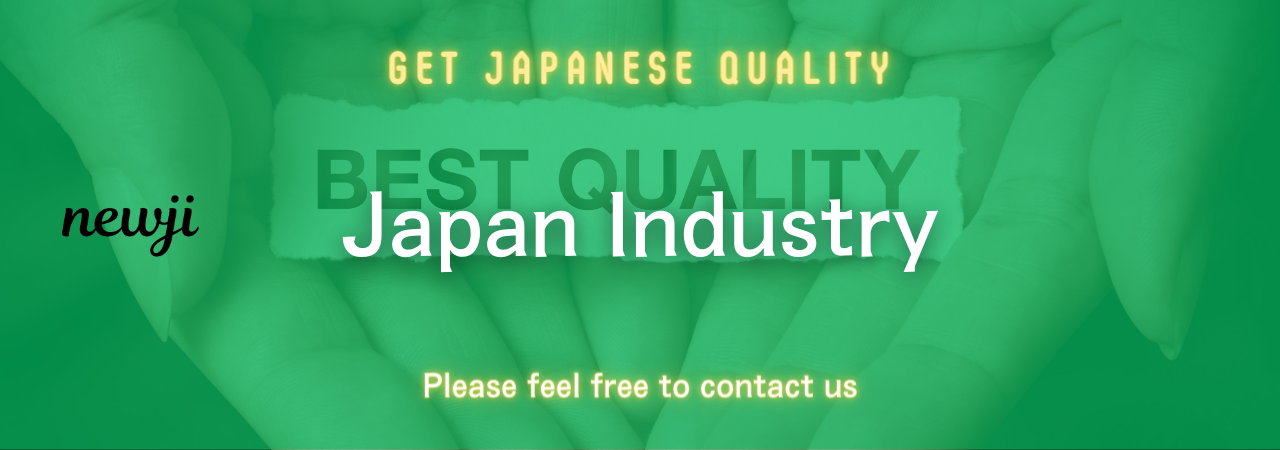
In today’s fast-paced industrial environment, optimizing the coating process plays a crucial role in ensuring product quality and consistency.
Digital transformation (DX) solutions have made significant strides in preventing splatter during the coating process.
This article discusses how leveraging modern technology can lead to better outcomes in manufacturing operations.
目次
Understanding the Coating Process and Its Challenges
The coating process is essential in many industries, including automotive, aerospace, and consumer goods.
It involves applying a layer of material to the surface of a product to enhance its appearance, protect it from the elements, or impart certain properties.
While the benefits of coating are significant, the process itself can be fraught with challenges.
One of the primary issues in the coating process is splatter.
Splatter occurs when droplets of the coating material scatter in an uncontrolled manner, leading to uneven application and wastage.
This not only affects the final product quality but also increases material costs and leads to potential rework, thus impacting overall efficiency.
The Role of Digital Transformation in Coating
Digital transformation involves integrating digital technology into various aspects of a business to improve processes and outcomes.
In the context of the coating process, DX solutions can bring about several improvements, helping to mitigate issues like splatter.
Real-Time Monitoring and Data Analysis
One of the vital components of DX solutions is real-time monitoring.
Using sensors and IoT (Internet of Things) devices, manufacturers can continuously track variables like temperature, pressure, and viscosity of the coating material.
This data is then analyzed to detect any anomalies that could lead to splatter.
For example, if a sensor detects a sudden change in the viscosity of the coating material, the system can automatically adjust the spray pattern to compensate.
This ensures a more uniform application and reduces the chances of splatter.
Automation and Robotics
Automated systems and robotics are becoming increasingly prevalent in manufacturing.
In the coating process, automation can significantly reduce human error, which is a common cause of splatter.
Robotic arms equipped with precise nozzles can ensure that the coating is applied consistently.
Moreover, these automated systems can be programmed with advanced algorithms to adjust their movements in real-time, responding to changes in the environment or material properties.
This level of precision is difficult to achieve with manual application, making automation a key element in preventing splatter.
Predictive Maintenance and Machine Learning
Predictive maintenance is another advantage brought about by digital transformation.
By leveraging machine learning algorithms, manufacturers can predict when equipment is likely to fail or when maintenance is required.
This approach helps in maintaining the optimal condition of coating equipment.
For instance, if the machinery used for spraying starts showing signs of wear, it could lead to an uneven application, causing splatter.
With predictive maintenance, such issues can be addressed before they escalate, ensuring continuous, high-quality output.
Implementing DX Solutions in the Coating Process
While the benefits of DX solutions are clear, effective implementation requires a strategic approach.
Here are some steps to follow:
Assess the Current Process
Before implementing any new technology, it’s crucial to understand the current coating process.
Identify areas where splatter occurs most frequently and which variables tend to fluctuate.
This assessment provides a foundation for integrating digital solutions tailored to specific needs.
Choose the Right Technology
Select technologies that align with your goals.
For real-time monitoring, ensure that you have the appropriate sensors and IoT devices.
For automation, invest in reliable robotic systems.
Choosing the right technology is pivotal for successful integration and achieving desired outcomes.
Train the Workforce
Even the best technology will fail if the workforce is not adequately trained.
Ensure that employees understand how to use new systems and are aware of the benefits.
Training programs should cover both the technical aspects and the practical implications of the technology.
Continuous Improvement
Digital transformation is not a one-time event.
It’s an ongoing process that requires continuous improvement.
Regularly review the performance of the new systems and make necessary adjustments.
Collect feedback from the workforce and incorporate it into future updates.
Benefits of Preventing Splatter in the Coating Process
Implementing DX solutions to prevent splatter can yield substantial benefits:
Improved Product Quality
A consistent and even coating application ensures that the final product meets desired quality standards.
It reduces defects caused by uneven coating and enhances the overall appearance.
Cost Savings
Reducing splatter means less wastage of coating material.
This directly translates into cost savings as fewer resources are required.
Additionally, minimizing rework and rejects leads to more efficient production.
Enhanced Efficiency
With automation and real-time monitoring, the coating process becomes more streamlined.
It reduces downtime caused by manual errors and equipment failures, leading to enhanced operational efficiency.
Environmental Benefits
Efficient use of coating material means lower consumption, which is environmentally beneficial.
It reduces the environmental footprint of the manufacturing process by minimizing wastage and emissions.
Conclusion
Digital transformation offers a robust solution to prevent splatter in the coating process.
By leveraging real-time monitoring, automation, and predictive maintenance, manufacturers can achieve consistent quality, reduce costs, and enhance efficiency.
Implementing DX solutions requires a strategic approach, but the benefits make it a worthwhile investment.
As industries continue to evolve, adopting these advanced technologies will be key to staying competitive and achieving sustainable growth.
資料ダウンロード
QCD調達購買管理クラウド「newji」は、調達購買部門で必要なQCD管理全てを備えた、現場特化型兼クラウド型の今世紀最高の購買管理システムとなります。
ユーザー登録
調達購買業務の効率化だけでなく、システムを導入することで、コスト削減や製品・資材のステータス可視化のほか、属人化していた購買情報の共有化による内部不正防止や統制にも役立ちます。
NEWJI DX
製造業に特化したデジタルトランスフォーメーション(DX)の実現を目指す請負開発型のコンサルティングサービスです。AI、iPaaS、および先端の技術を駆使して、製造プロセスの効率化、業務効率化、チームワーク強化、コスト削減、品質向上を実現します。このサービスは、製造業の課題を深く理解し、それに対する最適なデジタルソリューションを提供することで、企業が持続的な成長とイノベーションを達成できるようサポートします。
オンライン講座
製造業、主に購買・調達部門にお勤めの方々に向けた情報を配信しております。
新任の方やベテランの方、管理職を対象とした幅広いコンテンツをご用意しております。
お問い合わせ
コストダウンが利益に直結する術だと理解していても、なかなか前に進めることができない状況。そんな時は、newjiのコストダウン自動化機能で大きく利益貢献しよう!
(Β版非公開)