- お役立ち記事
- DXing of line production methods directly improves production lead time and quality
月間76,176名の
製造業ご担当者様が閲覧しています*
*2025年3月31日現在のGoogle Analyticsのデータより
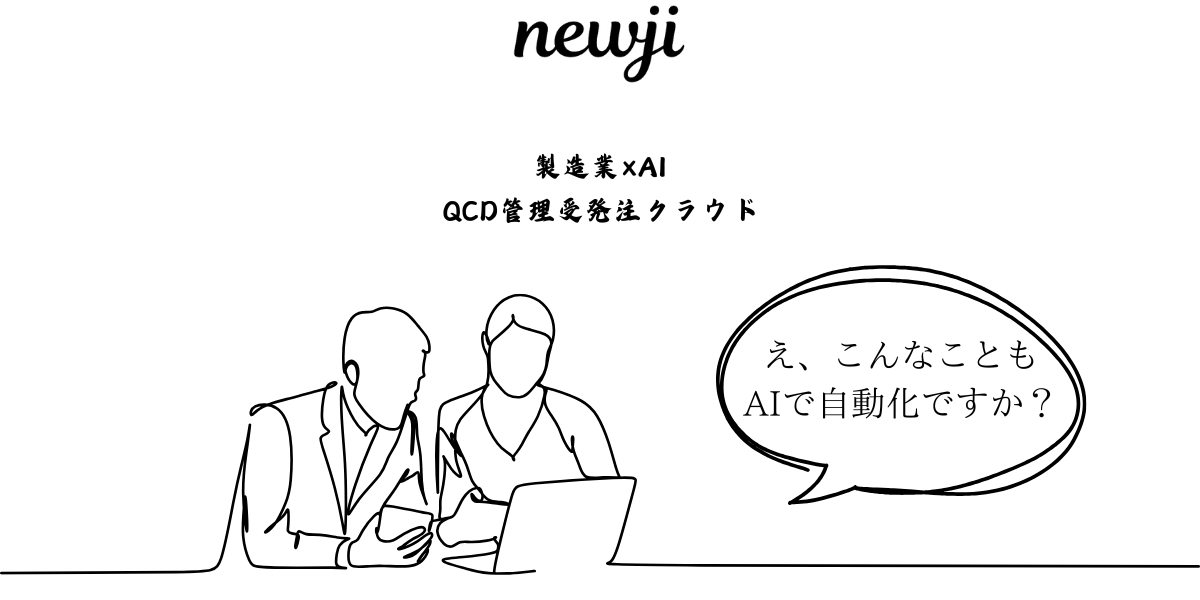
DXing of line production methods directly improves production lead time and quality
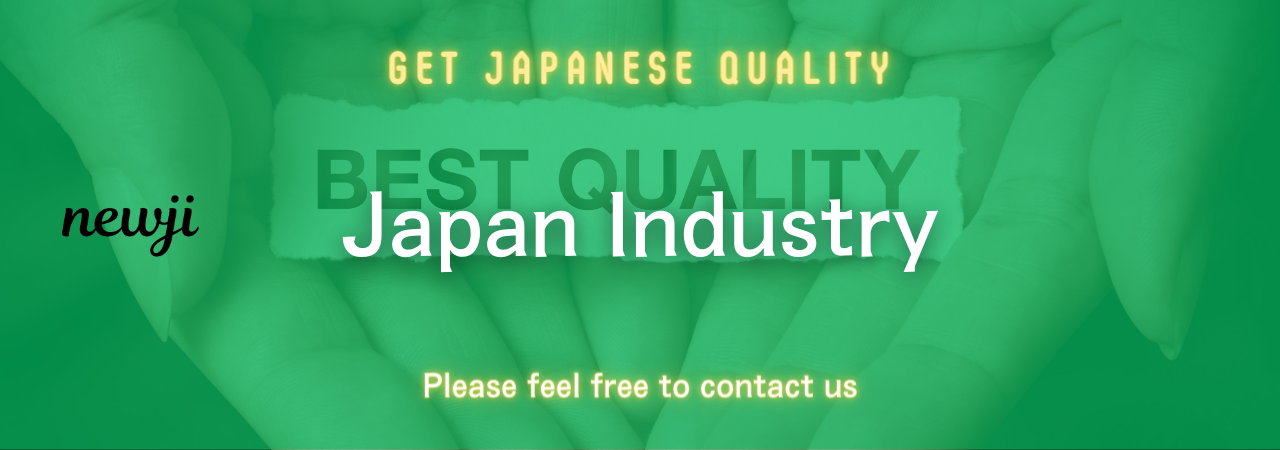
In today’s fast-paced manufacturing landscape, companies are continuously seeking ways to enhance their operations to keep up with competition and customer demand.
One such strategy is the digital transformation (DX) of line production methods.
In simpler terms, this means adopting digital tools and technologies to improve how things are made in a factory.
This article will explore how DXing line production methods can directly improve production lead times and quality.
目次
What is Digital Transformation in Manufacturing?
Digital transformation involves integrating digital technology into all aspects of a business, fundamentally changing how it operates and delivers value to customers.
In manufacturing, this means modernizing traditional production lines with advanced technologies like the Internet of Things (IoT), artificial intelligence (AI), and robotics.
By doing so, factories can operate more efficiently and produce higher-quality products in less time.
How DXing Production Methods Reduces Lead Time
Real-time Data Monitoring
One of the most significant benefits of digital transformation is the ability to monitor production processes in real-time.
Sensors and connected devices collect data from every part of the production line, providing managers with insights into performance and potential issues.
These real-time analytics allow for immediate adjustments to be made, reducing downtime and speeding up production.
Predictive Maintenance
Downtime due to equipment failure can severely impact production lead times.
With digital transformation, manufacturers can employ predictive maintenance strategies.
Predictive maintenance uses data from equipment sensors and historical patterns to predict when a machine is likely to fail.
This allows for maintenance to be scheduled before the failure occurs, minimizing unexpected downtime and keeping the production line running smoothly.
Automation and Robotics
Automation and robotics can significantly reduce the time it takes to produce items.
By automating repetitive and time-consuming tasks, factories can increase their output without the need for additional human labor.
Robots can work continuously without breaks, further enhancing productivity and reducing lead times.
Improving Product Quality through Digital Transformation
Enhanced Quality Control
Digital transformation introduces advanced quality control measures that were not possible with traditional methods.
Using technologies like AI and machine learning, manufacturers can identify defects and anomalies in real-time.
Automated inspection systems can continuously review products and immediately flag any inconsistencies from the set standards, ensuring that only products that meet the highest quality are shipped to customers.
Traceability and Transparency
Traceability is the ability to track every component and material used in the production process.
With digital transformation, companies can implement comprehensive traceability systems using IoT and blockchain technologies.
This allows them to have full visibility over their supply chain and production line.
If a quality issue arises, they can quickly identify and address the root cause, preventing defective products from reaching customers.
Improved Design and Prototyping
DXing also improves the design and prototyping phases of manufacturing.
With digital twins and 3D modeling, designers can create accurate virtual models of products and test them under various conditions.
This ensures that any potential design flaws are identified and corrected before production begins, leading to better quality end products.
Case Studies of Successful Digital Transformation
Company A: Automotive Manufacturing
Company A, an automotive manufacturer, implemented IoT sensors throughout their production line.
By collecting and analyzing data in real-time, they managed to reduce their production lead time by 20%.
Additionally, predictive maintenance strategies reduced unexpected equipment failures, further boosting productivity and reducing costs.
Company B: Electronics Manufacturing
Company B, a leading electronics manufacturer, adopted machine learning algorithms for quality control.
The system can detect defects with 99% accuracy, drastically improving product quality.
They also implemented a blockchain system for traceability, ensuring full transparency of their supply chain.
As a result, customer satisfaction and brand reputation significantly improved.
Steps to Begin the Digital Transformation Journey
Assess Current Capabilities
Begin by evaluating your existing production capabilities and identifying areas that need improvement.
Understand what technologies are currently being used and where gaps exist.
Set Clear Objectives
Establish clear goals for what you want to achieve with digital transformation.
Whether it’s reducing lead times, improving product quality, or both, having defined objectives will guide your implementation strategy.
Invest in the Right Technologies
Research and invest in digital tools and technologies that align with your objectives.
Consider IoT devices for real-time monitoring, AI for quality control, and automation systems for increased efficiency.
Train Your Workforce
Ensure that your team is well-prepared for the digital transformation.
Invest in training programs to equip them with the necessary skills to operate and manage new technologies.
Challenges and Considerations
While the benefits of digital transformation are significant, it’s essential to be aware of potential challenges.
These include the initial cost of investment, integrating new technologies with existing systems, and ensuring cybersecurity.
However, with careful planning and execution, these challenges can be managed to achieve a successful transformation.
In conclusion, DXing line production methods offers substantial benefits in reducing production lead times and improving product quality.
By adopting advanced digital technologies, manufacturers can streamline their operations, enhance efficiency, and maintain a competitive edge in the market.
With the right approach and investments, digital transformation can pave the way for a more productive and high-quality manufacturing process.
資料ダウンロード
QCD管理受発注クラウド「newji」は、受発注部門で必要なQCD管理全てを備えた、現場特化型兼クラウド型の今世紀最高の受発注管理システムとなります。
ユーザー登録
受発注業務の効率化だけでなく、システムを導入することで、コスト削減や製品・資材のステータス可視化のほか、属人化していた受発注情報の共有化による内部不正防止や統制にも役立ちます。
NEWJI DX
製造業に特化したデジタルトランスフォーメーション(DX)の実現を目指す請負開発型のコンサルティングサービスです。AI、iPaaS、および先端の技術を駆使して、製造プロセスの効率化、業務効率化、チームワーク強化、コスト削減、品質向上を実現します。このサービスは、製造業の課題を深く理解し、それに対する最適なデジタルソリューションを提供することで、企業が持続的な成長とイノベーションを達成できるようサポートします。
製造業ニュース解説
製造業、主に購買・調達部門にお勤めの方々に向けた情報を配信しております。
新任の方やベテランの方、管理職を対象とした幅広いコンテンツをご用意しております。
お問い合わせ
コストダウンが利益に直結する術だと理解していても、なかなか前に進めることができない状況。そんな時は、newjiのコストダウン自動化機能で大きく利益貢献しよう!
(β版非公開)