- お役立ち記事
- DXing of process approaches is indispensable for strengthening the competitiveness of the manufacturing industry
DXing of process approaches is indispensable for strengthening the competitiveness of the manufacturing industry
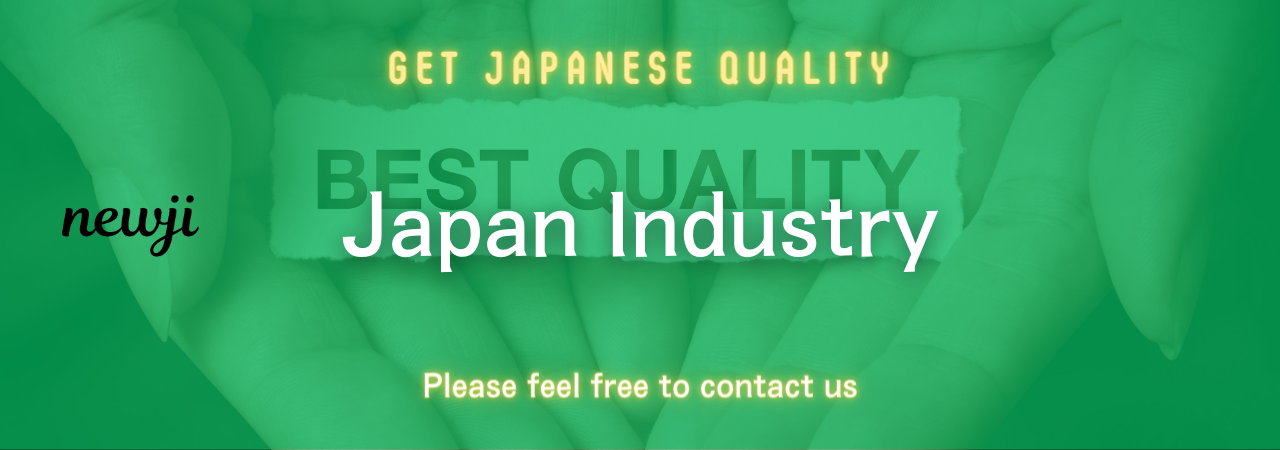
In the fast-changing world of manufacturing, staying ahead means embracing digital transformation and updating how processes are approached. This transformation is known as the digital change of process approaches or DXing. By integrating advanced technologies into every step of the manufacturing process, companies can not only keep up with the competition but also leap ahead. Here’s why DXing is essential and how it bolsters the competitiveness of the manufacturing industry.
Manufacturing has always been at the forefront of technological advancements. From the steam engine in the industrial revolution to the assembly line methods popularized by Henry Ford, every major leap has been about making processes more efficient and effective. Today, digital transformation is the next big step. It’s about incorporating digital technologies to revamp how manufacturing tasks are done, ultimately aiming for enhanced efficiency and better product quality.
The principal benefit of digital transformation in manufacturing is efficiency. Traditional manufacturing processes often involve a lot of manual work, which can be time-consuming and prone to errors. Digital tools, such as artificial intelligence, machine learning, and robotics, can streamline these processes. For instance, robots can handle repetitive tasks with high precision, reducing the likelihood of human error, while AI can analyze data to optimize workflows. This increased efficiency means faster production times and lower operational costs, a win-win for manufacturers.
Another critical advantage of DXing in manufacturing is the improvement in product quality. Quality control is paramount in the manufacturing industry, and digital transformation can enhance this aspect significantly. With advanced sensors and real-time data analytics, manufacturers can monitor their production lines closely and catch defects early. Predictive maintenance tools can also alert when machinery needs servicing, thus preventing breakdowns that could jeopardize product quality. Enhanced quality control not only ensures customer satisfaction but also reduces waste and rework costs.
Supply chain management is another area where digital transformation proves its worth. The supply chain is the backbone of manufacturing, and any disruption can have far-reaching consequences. Digital tools can provide real-time visibility into the supply chain, allowing manufacturers to track parts and materials from the supplier to the final product. This transparency helps identify potential bottlenecks and allows for quick adjustments. Furthermore, digital integration with suppliers and distributors can facilitate better collaboration and more efficient logistics, ensuring timely delivery of products to the end customers.
DXing also offers significant environmental benefits, which are becoming increasingly important in today’s environmentally conscious world. By optimizing processes, manufacturers can reduce their energy consumption and minimize waste. For instance, smart grids and IoT devices can monitor energy usage and suggest ways to cut down on unnecessary consumption. Similarly, sustainable manufacturing practices like 3D printing and additive manufacturing not only reduce waste materials but also allow for the use of eco-friendly substances. These practices contribute to a greener planet while also appealing to a more environmentally aware consumer base.
Incorporating digital transformation in manufacturing often involves a shift towards data-driven decision-making. Manufacturing processes generate a vast amount of data, from machine performance to supply chain logistics. By leveraging big data analytics, manufacturers can gain deeper insights into every aspect of their operations. This intelligence can drive informed decisions, identify areas for improvement, and uncover new opportunities for growth. Predictive analytics, for example, can forecast demand trends, helping companies to adjust production schedules and inventory levels accordingly.
Employee empowerment is another critical outcome of digital transformation. While there might be a misconception that automation and digital tools could replace human labor, the reality is that these technologies often complement and enhance human capabilities. By adopting digital tools, workers can focus on more strategic tasks rather than mundane ones. For instance, augmented reality (AR) can assist in training employees by providing real-time, hands-on guidance. Additionally, collaboration tools can foster better teamwork and communication, boosting overall productivity.
While the benefits are immense, the road to successful digital transformation in manufacturing isn’t without challenges. It’s more than just implementing new technologies; it requires a cultural shift within the organization. Leadership must drive this change, ensuring that all team members are on board and adequately trained for the new tools and processes. Cybersecurity also becomes a major concern as more operations go online. Protecting sensitive data and maintaining the integrity of digital systems against potential cyber threats is paramount.
Cost is another factor that might be a hurdle for smaller manufacturing firms. Investing in advanced technologies isn’t cheap, and the return on investment might take time to materialize. However, with proper planning and phased implementation, even small manufacturers can gradually transition to more digital methods, reaping the long-term benefits. Government subsidies, grants, and partnerships can also aid in easing the financial burden of digital transformation.
Ultimately, the manufacturing industry stands at the brink of another revolutionary change. The incorporation of digital transformation through DXing of process approaches is not just an option but a necessity to remain competitive. Companies that embrace these changes can expect enhanced efficiency, superior product quality, better supply chain management, reduced environmental impact, empowered employees, and data-driven decision-making. Though challenges exist, the long-term benefits far outweigh the initial obstacles, ensuring a brighter future for forward-thinking manufacturers. As the old saying goes, those who adapt to change are the ones who thrive, and in the digital age, this adage is truer than ever for the manufacturing industry.
資料ダウンロード
QCD調達購買管理クラウド「newji」は、調達購買部門で必要なQCD管理全てを備えた、現場特化型兼クラウド型の今世紀最高の購買管理システムとなります。
ユーザー登録
調達購買業務の効率化だけでなく、システムを導入することで、コスト削減や製品・資材のステータス可視化のほか、属人化していた購買情報の共有化による内部不正防止や統制にも役立ちます。
NEWJI DX
製造業に特化したデジタルトランスフォーメーション(DX)の実現を目指す請負開発型のコンサルティングサービスです。AI、iPaaS、および先端の技術を駆使して、製造プロセスの効率化、業務効率化、チームワーク強化、コスト削減、品質向上を実現します。このサービスは、製造業の課題を深く理解し、それに対する最適なデジタルソリューションを提供することで、企業が持続的な成長とイノベーションを達成できるようサポートします。
オンライン講座
製造業、主に購買・調達部門にお勤めの方々に向けた情報を配信しております。
新任の方やベテランの方、管理職を対象とした幅広いコンテンツをご用意しております。
お問い合わせ
コストダウンが利益に直結する術だと理解していても、なかなか前に進めることができない状況。そんな時は、newjiのコストダウン自動化機能で大きく利益貢献しよう!
(Β版非公開)