- お役立ち記事
- Early warning system for supply chain risks that purchasing departments should pay attention to
月間76,176名の
製造業ご担当者様が閲覧しています*
*2025年3月31日現在のGoogle Analyticsのデータより
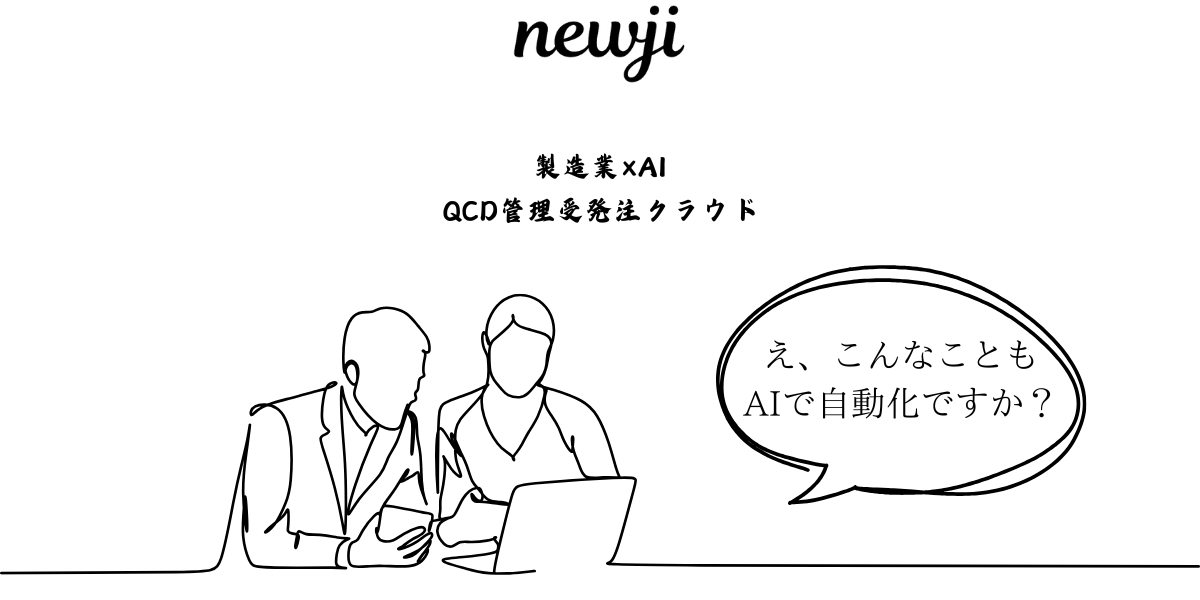
Early warning system for supply chain risks that purchasing departments should pay attention to
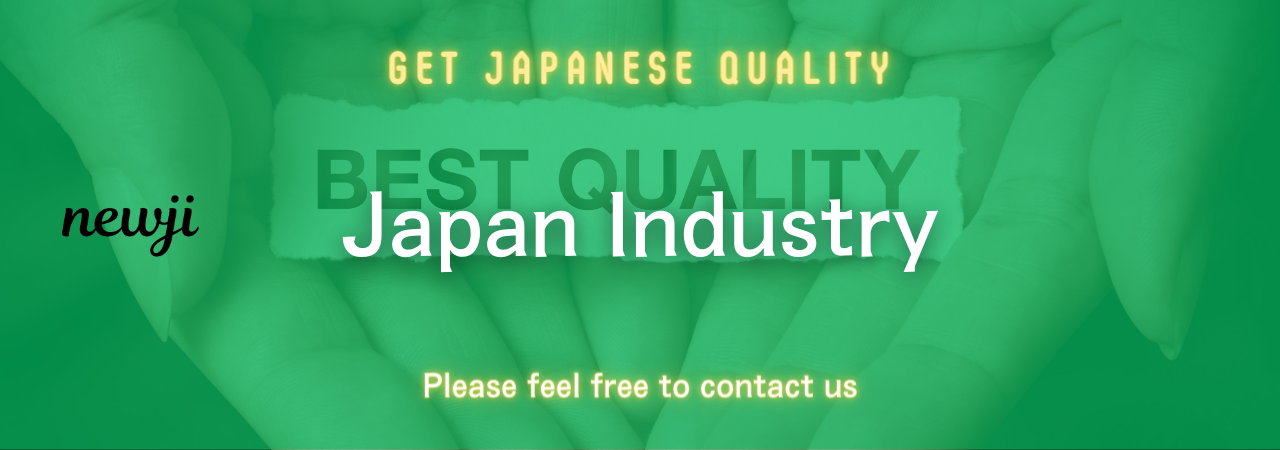
目次
Understanding Supply Chain Risks
Supply chain risks are potential problems that can arise at any point in a product’s lifecycle, from raw material procurement to final delivery to the consumer.
These risks can affect the timely and efficient flow of goods, leading to delays or disruptions.
For purchasing departments, understanding these risks is essential to avoid unexpected challenges and maintain smooth operations.
Common supply chain risks include natural disasters, supplier insolvency, geopolitical instability, and fluctuations in demand.
Why Early Warning Systems Matter
Early warning systems for supply chain risks are vital tools for purchasing departments.
They allow businesses to anticipate potential disruptions and take proactive measures to mitigate them.
By identifying potential threats early, companies can prevent or reduce the impact of these risks on their operations.
For instance, if a supplier is facing financial difficulties, an early warning system can alert the purchasing department, allowing them to find alternative suppliers in advance.
Components of an Effective Early Warning System
An effective early warning system incorporates several key components to ensure comprehensive risk management.
Firstly, it should include a robust data collection mechanism to gather information from various sources.
This data can come from market reports, supplier audits, news agencies, and industry trends.
Secondly, the system must include advanced analytics to interpret the collected data.
These analytics help identify patterns and trends that might indicate potential risks.
For example, a sudden increase in lead times or a decrease in product quality from a supplier may signal underlying problems.
The third component is a communication framework.
The system must effectively convey risk information to the relevant stakeholders within the organization.
By doing so, it ensures that the purchasing department, as well as other departments, can respond appropriately.
Benefits of Implementing Early Warning Systems
Implementing an early warning system provides numerous benefits to purchasing departments and the organization as a whole.
It enhances decision-making by providing accurate and timely information about potential risks.
This allows companies to implement contingency plans well in advance of any disruptions.
Moreover, early warning systems improve collaboration across departments.
They create a platform for sharing risk information, enabling different teams to work together in developing solutions.
This collaborative approach results in increased resilience and agility of the supply chain.
Another significant benefit is cost savings.
By foreseeing risks and acting promptly, companies can avoid the financial burdens associated with supply chain disruptions, such as expedited shipping charges, production delays, or the need to source emergency stock.
Implementing Early Warning Systems: Best Practices
To fully harness the effectiveness of early warning systems, purchasing departments should follow several best practices.
One crucial practice is to ensure ongoing data updating and monitoring.
Continuous data collection provides the most recent insights, allowing for timely identification of new risks.
Next, there should be close collaboration with suppliers and vendors to enhance information sharing.
Strong relationships with suppliers enable better information flow, leading to more accurate risk assessments.
Encourage suppliers to inform you about their own challenges, ensuring mutual support and transparency.
Additionally, companies should engage in regular scenario planning and testing.
Running simulations of potential disruptions helps prepare the organization for various situations.
These drills improve response times when actual risks occur.
Challenges in Developing Early Warning Systems
While early warning systems offer many advantages, developing them does come with certain challenges.
Data collection can be difficult, particularly when dealing with international suppliers.
Varying information standards and lack of communication infrastructure can hinder the accuracy of the data collected.
Furthermore, the implementation of advanced analytics requires investment in technology and personnel.
Training team members to interpret complex data is paramount to accurately assess risks.
Despite these challenges, investing in early warning systems is a worthwhile endeavor that offers great returns in terms of risk management and operational efficiency.
The Future of Early Warning Systems in Supply Chains
As technology continues to evolve, the future of early warning systems looks promising.
Machine learning and artificial intelligence are expected to play an increasingly significant role in risk prediction.
These technologies can process vast amounts of data to identify risks with greater precision.
Additionally, blockchain technology may enhance transparency and traceability, allowing businesses to gain better insights into their supply chains.
With more accurate and reliable data, early warning systems can become even more effective in preempting supply chain disruptions.
Conclusion
In conclusion, early warning systems for supply chain risks are invaluable to purchasing departments aiming to mitigate potential disruptions.
By understanding supply chain risks, implementing effective systems, and adopting best practices, companies can enhance their resilience and safeguard their operations.
Although challenges exist, the continually evolving technological landscape provides exciting opportunities for improving early warning systems.
Companies that invest in these systems position themselves for success in an ever-changing business environment.
資料ダウンロード
QCD管理受発注クラウド「newji」は、受発注部門で必要なQCD管理全てを備えた、現場特化型兼クラウド型の今世紀最高の受発注管理システムとなります。
ユーザー登録
受発注業務の効率化だけでなく、システムを導入することで、コスト削減や製品・資材のステータス可視化のほか、属人化していた受発注情報の共有化による内部不正防止や統制にも役立ちます。
NEWJI DX
製造業に特化したデジタルトランスフォーメーション(DX)の実現を目指す請負開発型のコンサルティングサービスです。AI、iPaaS、および先端の技術を駆使して、製造プロセスの効率化、業務効率化、チームワーク強化、コスト削減、品質向上を実現します。このサービスは、製造業の課題を深く理解し、それに対する最適なデジタルソリューションを提供することで、企業が持続的な成長とイノベーションを達成できるようサポートします。
製造業ニュース解説
製造業、主に購買・調達部門にお勤めの方々に向けた情報を配信しております。
新任の方やベテランの方、管理職を対象とした幅広いコンテンツをご用意しております。
お問い合わせ
コストダウンが利益に直結する術だと理解していても、なかなか前に進めることができない状況。そんな時は、newjiのコストダウン自動化機能で大きく利益貢献しよう!
(β版非公開)