- お役立ち記事
- Easy-to-use and effective why-why analysis tips and points for internal deployment learned from Honda
月間76,176名の
製造業ご担当者様が閲覧しています*
*2025年3月31日現在のGoogle Analyticsのデータより
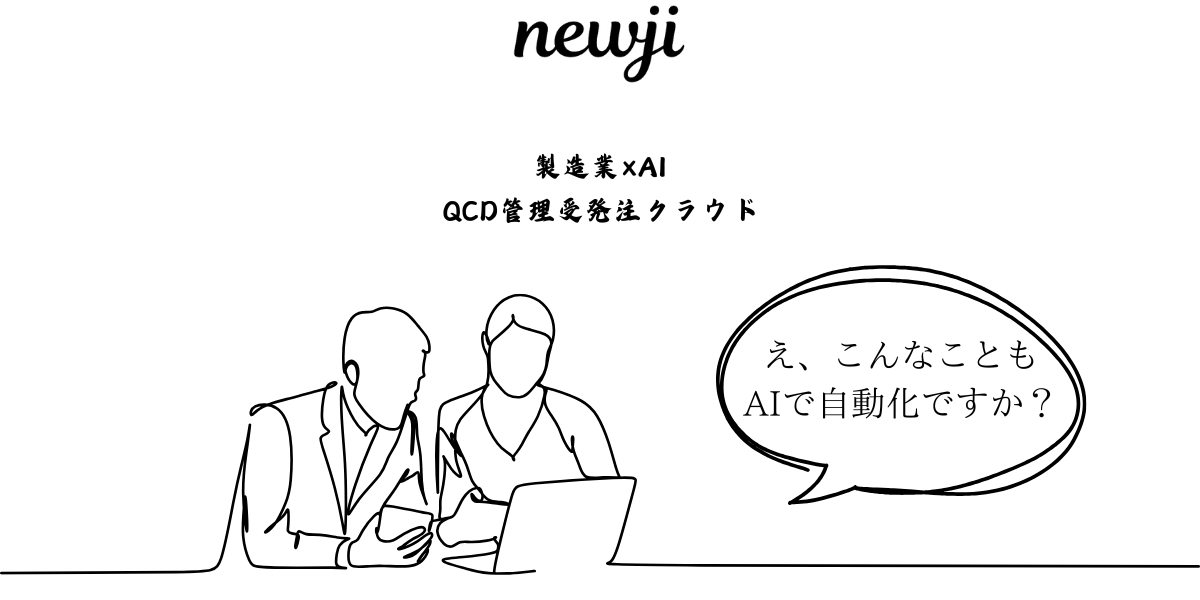
Easy-to-use and effective why-why analysis tips and points for internal deployment learned from Honda
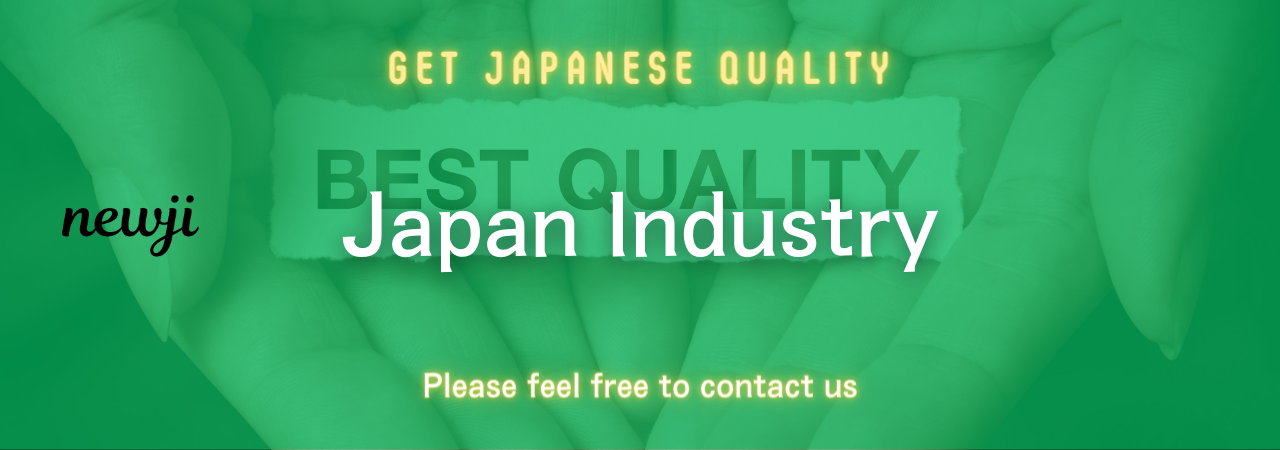
目次
Understanding Why-Why Analysis
Why-why analysis is a problem-solving method that helps identify the root cause of an issue by repeatedly asking the question “Why?”
This process helps teams and individuals dig deeper into problems to reveal underlying causes rather than just addressing surface-level issues.
Originating from Toyota and other automotive industries, why-why analysis today is widely used in various fields for improving processes and outcomes.
Honda, one of the pioneers of this method in the auto industry, has demonstrated the effectiveness of why-why analysis to increase efficiency and innovation.
Their approach shows that asking the right questions can lead to fundamental solutions that enhance product quality and operational success.
Benefits of Adopting Why-Why Analysis
One of the most significant benefits of using why-why analysis is its simplicity.
Since it involves asking straightforward questions, this method can be easily understood and implemented by any team member.
This accessibility fosters inclusivity and allows everyone to participate in the problem-solving process.
Another advantage is that it promotes critical thinking by encouraging teams to look beyond obvious answers.
Through this iterative questioning process, individuals are compelled to think about problems in-depth, potentially uncovering hidden barriers to improvement.
Additionally, implementing why-why analysis can lead to more sustainable solutions.
By resolving root causes, organizations can prevent recurrence and save resources that would otherwise be spent on addressing problems repeatedly.
How to Conduct a Why-Why Analysis
Conducting a why-why analysis involves a structured process that teams should follow to ensure effectiveness.
Here’s a step-by-step guide to facilitate this method:
1. Identify the Problem
Start by clearly defining the problem or issue you wish to solve.
It’s crucial that the problem statement is specific and clear, as this will guide the rest of the analysis.
For example, instead of stating “There are delays in delivery,” specify “Shipments are delayed by two days on average.”
2. Assemble the Right Team
Gather a diverse group with knowledge relevant to the issue, including those who experience or are knowledgeable about the problem firsthand.
Their insights are invaluable and can provide different perspectives to impart a comprehensive view of the problem.
3. Ask the First “Why?”
Pose the first “Why?” regarding the problem statement.
Ensure that answers are factual and based on evidence rather than assumptions or opinions.
Document each response carefully for later analysis.
4. Repeat the Process
Continue asking “Why?” based on the previous answer.
Typically, a minimum of five levels of questioning is recommended to arrive at the root cause, although this could vary depending on the complexity of the problem.
5. Identify the Root Cause
Once the questioning process unveils the root cause, you’ll be in a better position to develop strategic solutions that address underlying issues.
Document the findings for all team members to review and understand.
Tips for Successful Implementation
While the why-why analysis is a straightforward method, successfully implementing it in your organization requires some finesse and attention to detail.
Encourage Open Communication
Promote an environment where team members feel comfortable sharing insights and opinions.
For why-why analysis to be effective, it’s essential to create a space where everyone can contribute without fear of judgment or censure.
Avoid Premature Judgments
Avoid jumping to conclusions or making assumptions early in the process.
Premature judgments can prevent teams from uncovering accurate root causes and may lead to ineffective solutions.
Stay patient and let the questioning process naturally unfold to reveal genuine insights.
Leverage Data
Support findings with available data to enhance credibility.
Historically, data should guide the questioning process and confirm the validity of the answers obtained.
Utilize reports, records, and empirical evidence to back up analysis for more compelling outcomes.
Monitor and Review
After implementing solutions based on your why-why analysis, continue to monitor the situation to ensure the problem is solved sustainably.
Review outcomes periodically and be prepared to adapt solutions if recurrence is observed.
Common Challenges and How to Overcome Them
Implementing a why-why analysis might come with challenges that you should be prepared to address.
Lack of Team Engagement
Sometimes, teams may not be fully engaged in the process due to a lack of understanding or interest.
To overcome this, provide clear explanations on the benefits and importance of the analysis.
Engage team members early and maintain their interest by demonstrating the analysis’s potential impact.
Finding Accurate Answers
Determining factual reasons can be challenging, especially with complex problems.
Encourage thorough exploration backed up by data and promote cross-departmental collaboration for more holistic insights.
Surface-Level Solutions
Teams may settle for surface-level solutions instead of investigating deeper causes.
Address this by emphasizing the value of uncovering root causes and the long-term benefits of focused problem-solving.
Conclusion
Drawing from Honda’s experience and expertise, implementing why-why analysis can transform the way organizations address issues.
This tool is simple yet powerful in leading to genuine improvements and innovation.
By understanding its principles, following structured steps, and anticipating challenges, your organization can also deploy why-why analysis effectively to achieve quality solutions and improved processes.
Through patience, teamwork, and diligence, anyone can harness the full potential of why-why analysis for current and future successes.
資料ダウンロード
QCD管理受発注クラウド「newji」は、受発注部門で必要なQCD管理全てを備えた、現場特化型兼クラウド型の今世紀最高の受発注管理システムとなります。
ユーザー登録
受発注業務の効率化だけでなく、システムを導入することで、コスト削減や製品・資材のステータス可視化のほか、属人化していた受発注情報の共有化による内部不正防止や統制にも役立ちます。
NEWJI DX
製造業に特化したデジタルトランスフォーメーション(DX)の実現を目指す請負開発型のコンサルティングサービスです。AI、iPaaS、および先端の技術を駆使して、製造プロセスの効率化、業務効率化、チームワーク強化、コスト削減、品質向上を実現します。このサービスは、製造業の課題を深く理解し、それに対する最適なデジタルソリューションを提供することで、企業が持続的な成長とイノベーションを達成できるようサポートします。
製造業ニュース解説
製造業、主に購買・調達部門にお勤めの方々に向けた情報を配信しております。
新任の方やベテランの方、管理職を対象とした幅広いコンテンツをご用意しております。
お問い合わせ
コストダウンが利益に直結する術だと理解していても、なかなか前に進めることができない状況。そんな時は、newjiのコストダウン自動化機能で大きく利益貢献しよう!
(β版非公開)