- お役立ち記事
- Effective and efficient method of reliability testing of electronic equipment and parts, accelerated testing and failure analysis technology
月間77,185名の
製造業ご担当者様が閲覧しています*
*2025年2月28日現在のGoogle Analyticsのデータより
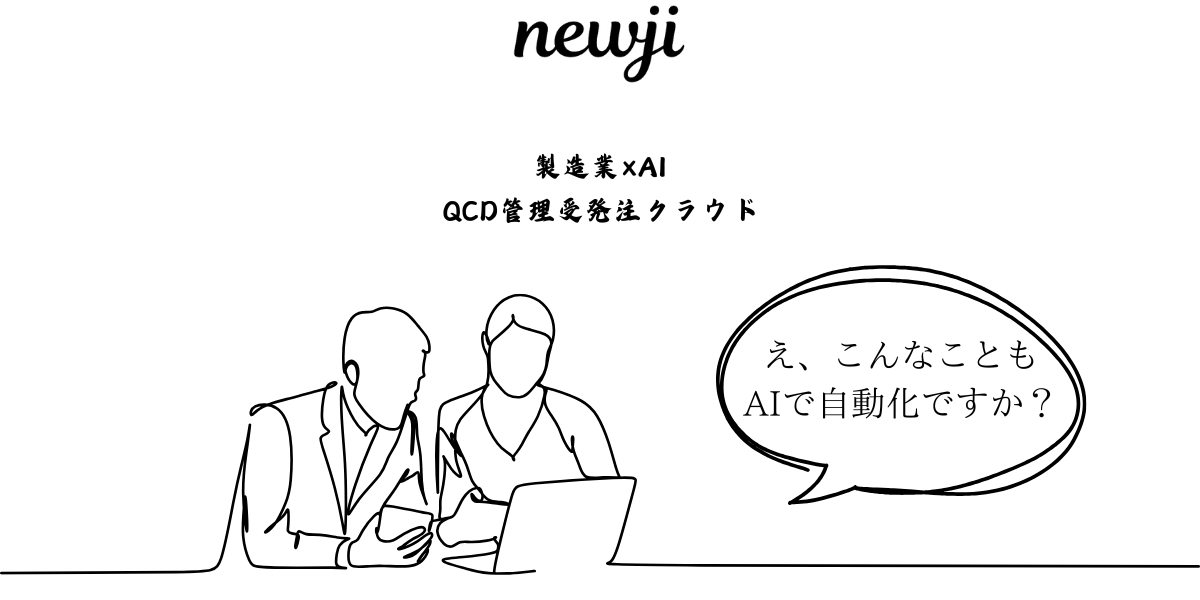
Effective and efficient method of reliability testing of electronic equipment and parts, accelerated testing and failure analysis technology
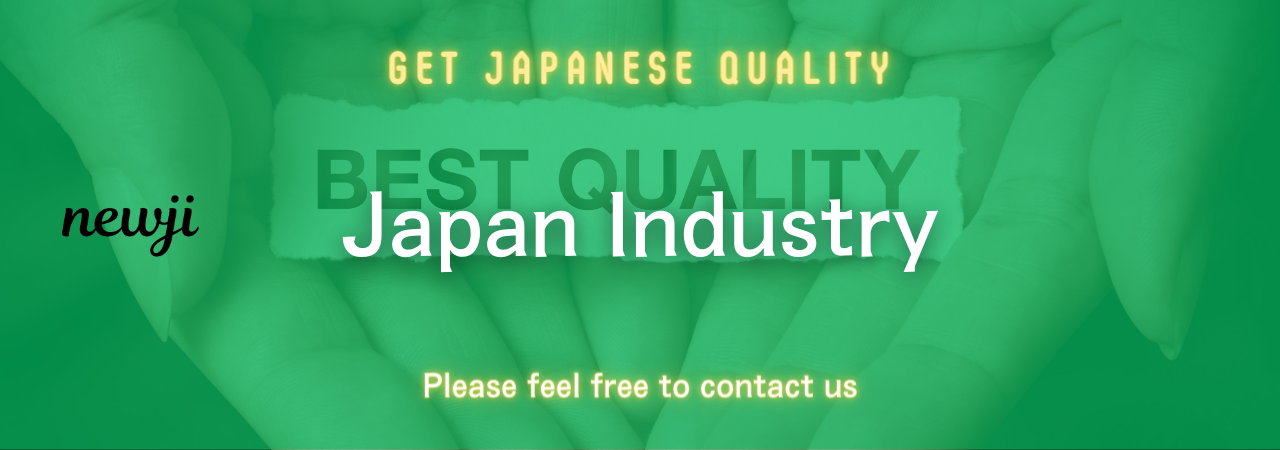
目次
Understanding Reliability Testing
Reliability testing is a critical process in the development of electronic equipment and components.
It ensures that a product will perform as expected over its intended lifespan.
The primary goal is to identify potential points of failure and rectify them before the product reaches the consumer.
Reliability testing involves exposing a device or component to a set of conditions that simulate real-world usage.
Electronic components undergo rigorous tests to determine their ability to withstand stress.
This helps manufacturers understand how their products will fare in both everyday use and under extreme conditions.
For electronic devices, reliability is not just about longevity but also about consistent performance over time.
Methods of Reliability Testing
Reliability testing includes several different methods, each designed to evaluate a different aspect of performance.
Environmental Testing
Environmental testing subjects electronic equipment to various conditions such as temperature extremes, humidity, vibration, and mechanical shock.
This testing helps ensure that a device can function accurately and reliably in different environments.
For example, electronic devices used in industrial machinery or automotive applications need to endure harsh conditions without malfunctioning.
Life Testing
Life testing involves running a device continuously at normal operational levels to determine its lifespan.
The test’s objective is to observe how the device performs over time and identify any gradual wear or degradation.
HALT (Highly Accelerated Life Testing)
HALT is designed to push a product to its operational limits rapidly.
It identifies potential failure modes by exposing the device to extreme temperatures, rapid temperature cycling, and excessive vibration.
HALT is not intended to estimate product life span but to uncover areas where a product is vulnerable.
HASS (Highly Accelerated Stress Screening)
HASS is a production screens testing, used to detect manufacturing defects before products are shipped.
It relies on heightened levels of stress, based on parameters defined by HALT, to find defects that could cause failures in the field.
Accelerated Testing Techniques
Accelerated testing involves putting electronic components through severe conditions to fast-track the ageing process.
This approach helps manufacturers predict how long a device will last under normal conditions.
Temperature Cycling
Temperature cycling subjects components to rapid changes in temperature to determine how they respond to thermal stress.
This method quickly reveals defects such as material expansion or contraction that could lead to device failure.
Load Testing
Load testing evaluates how a component performs under continuous heavy load.
It helps identify weaknesses in the design or manufacturing process that could lead to breakdowns under intense usage.
Pressure Testing
For equipment like pressure sensors or devices operating in pressurized environments, pressure testing assesses their ability to withstand pressure fluctuations.
Failure Analysis Technology
Failure analysis is a crucial part of reliability testing and involves determining the root cause of a failure.
By understanding why a product failed, engineers can develop solutions to prevent similar issues.
Non-Destructive Testing (NDT)
NDT techniques allow engineers to inspect a component without causing damage.
Methods like X-ray analysis, ultrasonic testing, and magnetic particle testing are used to detect internal defects.
Destructive Testing
Sometimes, understanding a failure requires taken the component apart for detailed inspection.
Methods include fracture analysis and stress testing, which assess how materials and structures respond to force.
Root Cause Analysis (RCA)
RCA is a systematic process for identifying the primary cause of failure.
It involves gathering data, reconstructing failure conditions, identifying potential causes, and verifying the actual cause through testing.
The Benefits of Effective Reliability Testing
Conducting thorough reliability testing brings numerous benefits to manufacturers and consumers alike.
It reduces the likelihood of product recalls and enhances the reputation of a brand by ensuring customers receive high-quality, reliable products.
Moreover, it helps in refining the design process, leading to innovations and improvements in future products.
Reliability testing saves costs in the long run by identifying issues early in the product development cycle, reducing the need for corrective action post-launch.
It contributes to customer satisfaction, builds trust, and establishes brand loyalty by delivering dependable electronic devices.
Conclusion
Reliability testing, accelerated testing, and failure analysis are integral to developing robust electronic equipment and parts.
These processes not only ensure product durability but also foster innovation by pinpointing areas for improvement.
Throughout the testing process, manufacturers can gain a comprehensive understanding of their products’ strengths and weaknesses.
The end result is electronic devices that meet industry standards and exceed consumer expectations, providing them with reliable performance over time.
資料ダウンロード
QCD管理受発注クラウド「newji」は、受発注部門で必要なQCD管理全てを備えた、現場特化型兼クラウド型の今世紀最高の受発注管理システムとなります。
ユーザー登録
受発注業務の効率化だけでなく、システムを導入することで、コスト削減や製品・資材のステータス可視化のほか、属人化していた受発注情報の共有化による内部不正防止や統制にも役立ちます。
NEWJI DX
製造業に特化したデジタルトランスフォーメーション(DX)の実現を目指す請負開発型のコンサルティングサービスです。AI、iPaaS、および先端の技術を駆使して、製造プロセスの効率化、業務効率化、チームワーク強化、コスト削減、品質向上を実現します。このサービスは、製造業の課題を深く理解し、それに対する最適なデジタルソリューションを提供することで、企業が持続的な成長とイノベーションを達成できるようサポートします。
製造業ニュース解説
製造業、主に購買・調達部門にお勤めの方々に向けた情報を配信しております。
新任の方やベテランの方、管理職を対象とした幅広いコンテンツをご用意しております。
お問い合わせ
コストダウンが利益に直結する術だと理解していても、なかなか前に進めることができない状況。そんな時は、newjiのコストダウン自動化機能で大きく利益貢献しよう!
(β版非公開)