- お役立ち記事
- Effective Approaches for Risk Management and Reliability Improvement Using FMEA
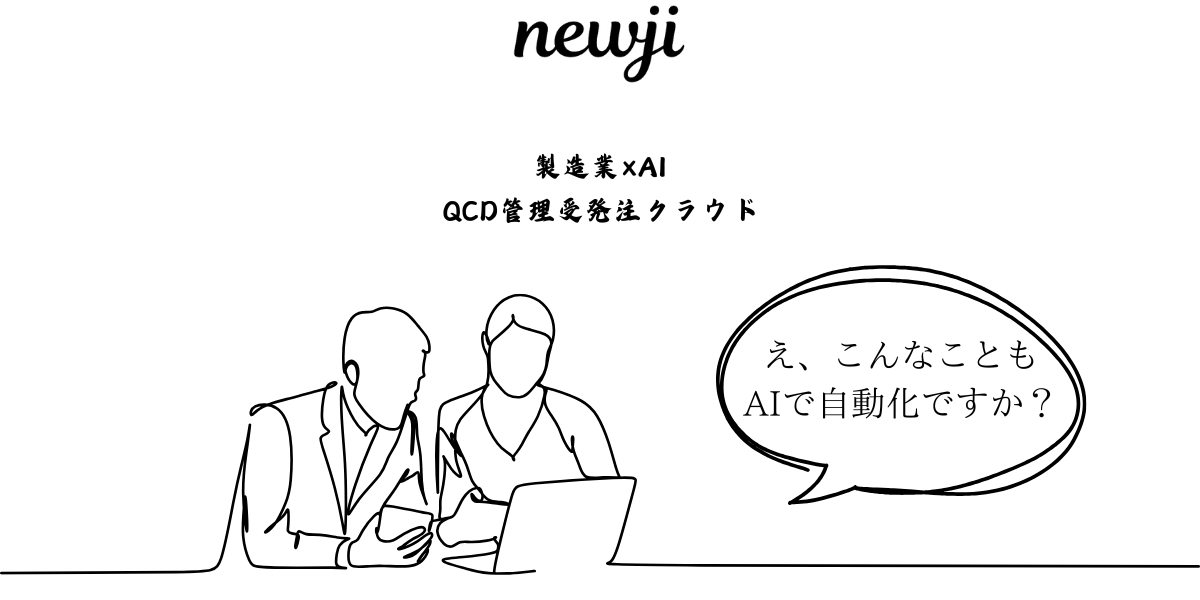
Effective Approaches for Risk Management and Reliability Improvement Using FMEA
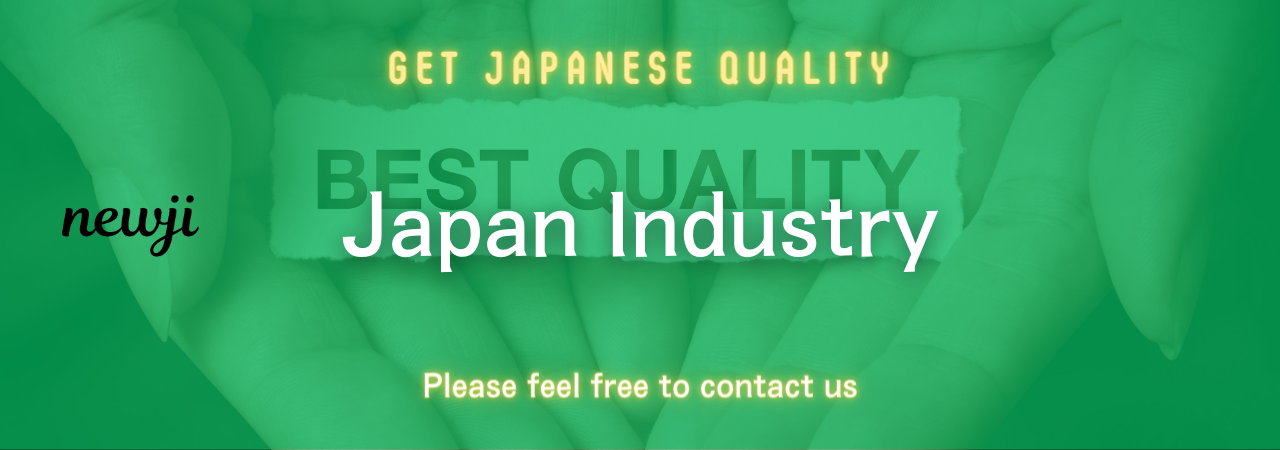
目次
Understanding FMEA: The First Step in Risk Management
Failure Mode and Effects Analysis (FMEA) is a systematic technique for identifying potential failures in a product or process.
It’s a crucial first step in risk management because it helps teams foresee the ways a product might fail and the effects of those failures.
By examining each component of a system, FMEA allows companies to pinpoint and prioritize risks, allowing them to address these potential issues efficiently.
The methodology behind FMEA involves dissecting a process into its individual elements.
Each element is then evaluated for ways it might fail, the consequences of a failure, the probability of occurrence, and how easily the failure can be detected.
Ultimately, it aids in delivering a deeper understanding of where reliability improvements are needed most.
Benefits of Implementing FMEA
One of the most significant benefits of implementing FMEA is its ability to improve the reliability of a product or process.
By systematically assessing potential failures, companies can proactively address them, thereby enhancing product quality and customer satisfaction.
Furthermore, FMEA aids in cost reduction.
By identifying failures before they occur, organizations can prevent costly repairs and ensure efficient use of resources.
This proactive approach can save considerable time and money in the long run.
Additionally, FMEA supports compliance with standards and regulations.
Many industries have stringent requirements for product quality and safety.
Adopting FMEA ensures that companies meet these requirements, reducing the risk of legal issues and maintaining their reputation.
Steps in Conducting an Effective FMEA
Conducting a successful FMEA involves several key steps.
First, it’s important to assemble a team with diverse expertise to capture comprehensive insights into the process or product being analyzed.
This typically includes engineers, project managers, and quality assurance personnel.
Next, the scope of FMEA must be defined.
This involves outlining the system, item, or process to be analyzed to ensure a focused and effective assessment.
Once the scope is established, teams should identify potential failure modes.
These are ways in which a process might fail to meet its desired functions.
Each failure mode is then analyzed for its effects, which help determine the severity of the failure.
The next step involves estimating the likelihood of occurrence for each failure and evaluating the ability to detect them before they cause harm.
The combination of severity, occurrence, and detection scores gives a risk priority number (RPN), indicating which failures need urgent attention.
Finally, teams need to devise action plans to address the most critical risks.
This includes implementing corrective measures and re-evaluating the system to verify the effectiveness of these measures.
FMEA in Different Industries
FMEA is applicable across various industries, each with unique challenges and requirements.
For example, in the automotive industry, FMEA is essential for ensuring vehicle safety and compliance with legal standards.
Meanwhile, in healthcare, it serves to enhance patient safety by identifying potential risks in medical devices or procedural workflows.
In the aerospace industry, where even minor failures can lead to catastrophic results, FMEA is a vital part of the engineering process.
Similarly, the electronics industry utilizes FMEA to address issues in circuit design and manufacturing processes, ensuring product reliability.
Integrating FMEA with Other Risk Management Tools
FMEA is most effective when integrated with other risk management tools.
Using FMEA alongside Root Cause Analysis (RCA) can provide comprehensive insights into why failures occur and facilitate the development of robust solutions.
Similarly, integrating FMEA with Design of Experiments (DOE) allows engineers to test and analyze various factors’ effects on product performance proactively.
This combination can help engineers understand and mitigate risks more effectively during the design phase.
Moreover, FMEA can be harmonized with Six Sigma methodologies, providing statistical tools to improve process quality by minimizing variability and defects.
Challenges and Limitations of FMEA
Despite its benefits, FMEA is not without challenges and limitations.
The process can be time-consuming and requires significant cross-functional collaboration.
Without effective communication and commitment from all participants, FMEA may not yield its full potential.
Moreover, FMEA relies heavily on the team’s expertise and experience.
If the team lacks in-depth knowledge of the product or process, crucial failure modes might be overlooked.
Additionally, FMEA’s focus on existing knowledge might limit its capacity to predict unknown risks or novel failures.
Finally, FMEA provides qualitative rather than quantitative results, which may be challenging for organizations looking for precise numerical evaluations of risk.
Conclusion
Incorporating FMEA into risk management processes significantly improves reliability and product quality.
By effectively identifying potential failures and their impacts, companies can take proactive measures to mitigate risks and enhance customer satisfaction.
Despite its challenges, when carried out correctly, FMEA serves as a cornerstone of a robust risk management strategy, ensuring industry compliance and cost efficiency.
Implementing FMEA requires careful planning and execution, but the benefits of improved reliability and risk management make it a worthwhile endeavor for any forward-thinking organization.
In a world where quality and safety standards are ever increasing, FMEA represents a vital tool for maintaining competitiveness and meeting the expectations of stakeholders and regulatory bodies.
資料ダウンロード
QCD調達購買管理クラウド「newji」は、調達購買部門で必要なQCD管理全てを備えた、現場特化型兼クラウド型の今世紀最高の購買管理システムとなります。
ユーザー登録
調達購買業務の効率化だけでなく、システムを導入することで、コスト削減や製品・資材のステータス可視化のほか、属人化していた購買情報の共有化による内部不正防止や統制にも役立ちます。
NEWJI DX
製造業に特化したデジタルトランスフォーメーション(DX)の実現を目指す請負開発型のコンサルティングサービスです。AI、iPaaS、および先端の技術を駆使して、製造プロセスの効率化、業務効率化、チームワーク強化、コスト削減、品質向上を実現します。このサービスは、製造業の課題を深く理解し、それに対する最適なデジタルソリューションを提供することで、企業が持続的な成長とイノベーションを達成できるようサポートします。
オンライン講座
製造業、主に購買・調達部門にお勤めの方々に向けた情報を配信しております。
新任の方やベテランの方、管理職を対象とした幅広いコンテンツをご用意しております。
お問い合わせ
コストダウンが利益に直結する術だと理解していても、なかなか前に進めることができない状況。そんな時は、newjiのコストダウン自動化機能で大きく利益貢献しよう!
(Β版非公開)