- お役立ち記事
- Effective drawing inspection method and design error prevention measures that make effective use of check sheets
月間77,185名の
製造業ご担当者様が閲覧しています*
*2025年2月28日現在のGoogle Analyticsのデータより
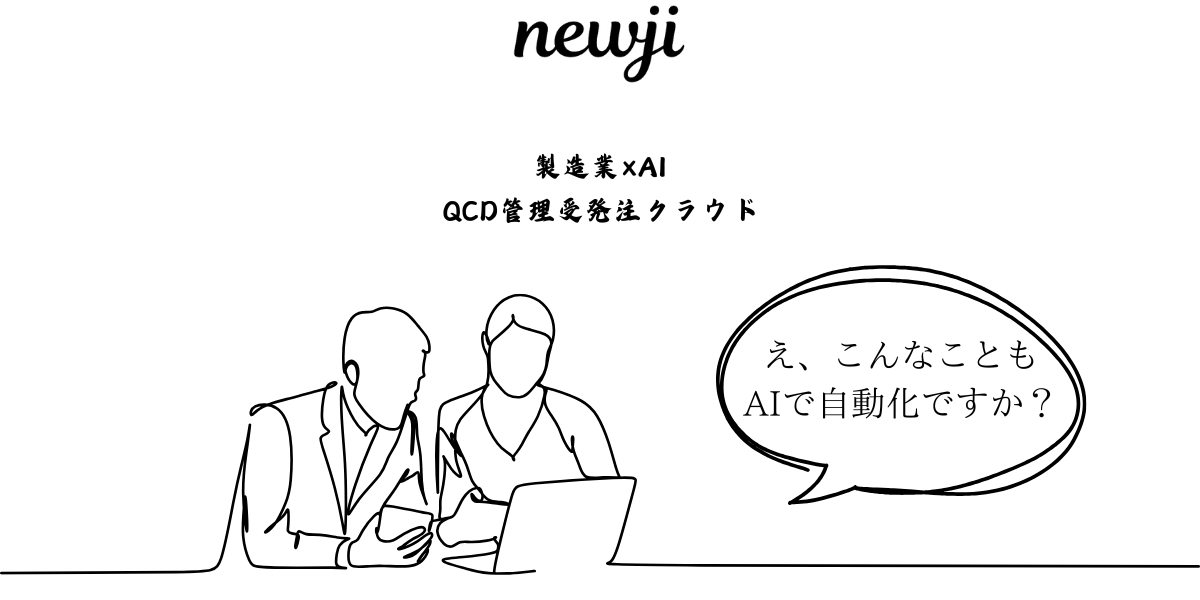
Effective drawing inspection method and design error prevention measures that make effective use of check sheets
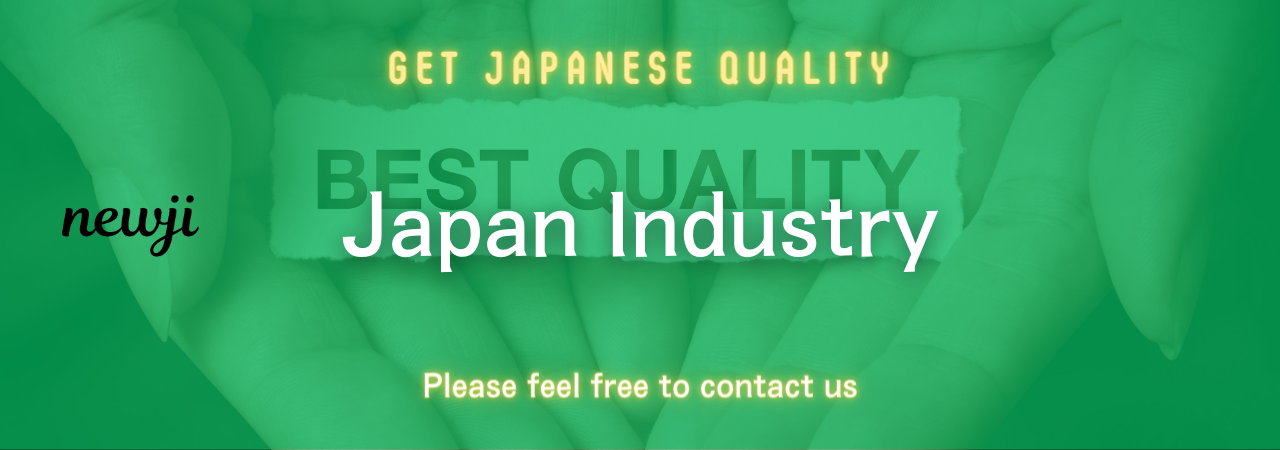
目次
Understanding the Importance of Drawing Inspection
The drawing inspection process plays a critical role in ensuring that technical designs are both accurate and functional.
This process involves evaluating engineering drawings for potential errors or inconsistencies.
When done effectively, drawing inspections can help identify defects at an early stage, preventing costly deviations and errors from escalating into major issues during production or construction.
By utilizing a structured inspection, companies can save time and resources, enhance product quality, and ensure compliance with industry standards.
The Role of Check Sheets in Drawing Inspections
Check sheets are essential tools in the inspection process.
They serve as structured formats that guide inspectors in systematically reviewing specific aspects of a drawing.
By using check sheets, inspectors can focus on critical features and ensure that no element is overlooked.
Check sheets not only help in acquiring complete and precise data but also in maintaining consistency across different inspections.
This makes them valuable for both quality control and process improvement.
Creating an Effective Check Sheet for Drawing Inspections
An effective check sheet should be clear, organized, and comprehensive.
It starts with identifying the key components and standards that need evaluation.
These might include design specifications, dimensional accuracy, material selection, and compliance with safety requirements.
The check sheet should have a clear layout, allowing inspectors to quickly navigate through the checklist without missing any steps.
Additionally, providing space for comments or observations can facilitate more detailed reporting and communication among team members.
Components to Include in a Check Sheet
– **Specifications Verification**: Ensure all dimensions, scales, and tolerances are recorded correctly.
– **Material Assessment**: Confirm that appropriate materials and finishes are specified.
– **Compliance Check**: Verify that the drawing meets relevant safety and industry standards.
– **Design Consistency**: Review for consistency within the drawing and with other related documents.
– **Approval Status**: Note whether the drawing has been reviewed and approved by relevant authorities.
Steps to Perform a Structured Drawing Inspection
1. **Preparation**: Gather all the necessary drawings, specifications, and related documents.
2. **Review Check Sheet**: Familiarize yourself with the checklist items and criteria.
3. **Thorough Inspection**: Methodically go through each checklist point, marking affirmations where applicable.
4. **Document Findings**: Use the comments section to note any discrepancies or potential issues.
5. **Report Outcomes**: Compile the inspection results into a report for review by engineers or project managers.
6. **Feedback Loop**: Communicate findings to the design team, providing them opportunities for correction or improvement.
Benefits of Using Check Sheets in Drawing Inspections
The implementation of check sheets in the inspection process results in a more organized and effective evaluation.
Check sheets allow for the standardization of procedures, which improves reliability and repeatability of inspections.
Additionally, they provide a reliable record of accountability and transparency, as each inspection’s outcomes are documented and can be traced back for future reference.
Utilizing check sheets also enhances communication by creating a common understanding of the inspection criteria and results among team members.
Design Error Prevention Measures
Identifying and correcting design errors early through structured reviews and inspections is crucial for effective project management.
Integrating prevention measures in the design phase helps mitigate risks associated with production delays, increased costs, and compromised safety.
Software tools for modeling and simulation can be valuable in detecting potential flaws before physical production begins.
Additionally, fostering a culture of collaboration and continuous learning in design teams encourages innovation and reduces the likelihood of repeated mistakes.
Design Review Practices
– **Peer Reviews**: Involve colleagues in the review process to gain diverse insights and objective feedback.
– **Simulation Tools**: Use simulation software to predict the performance and limitations of the design under different scenarios.
– **Prototyping**: Develop functional prototypes to test and refine the design before full-scale production.
Conclusion
Incorporating effective drawing inspection methods and design error prevention measures establishes a solid foundation for successful engineering and manufacturing projects.
By leveraging tools like check sheets, companies can streamline their processes, ensure higher quality standards, and mitigate risks associated with design errors.
Ultimately, the proactive approach in managing design and inspection leads to better products, satisfied customers, and a strong competitive edge in the market.
資料ダウンロード
QCD管理受発注クラウド「newji」は、受発注部門で必要なQCD管理全てを備えた、現場特化型兼クラウド型の今世紀最高の受発注管理システムとなります。
ユーザー登録
受発注業務の効率化だけでなく、システムを導入することで、コスト削減や製品・資材のステータス可視化のほか、属人化していた受発注情報の共有化による内部不正防止や統制にも役立ちます。
NEWJI DX
製造業に特化したデジタルトランスフォーメーション(DX)の実現を目指す請負開発型のコンサルティングサービスです。AI、iPaaS、および先端の技術を駆使して、製造プロセスの効率化、業務効率化、チームワーク強化、コスト削減、品質向上を実現します。このサービスは、製造業の課題を深く理解し、それに対する最適なデジタルソリューションを提供することで、企業が持続的な成長とイノベーションを達成できるようサポートします。
製造業ニュース解説
製造業、主に購買・調達部門にお勤めの方々に向けた情報を配信しております。
新任の方やベテランの方、管理職を対象とした幅広いコンテンツをご用意しております。
お問い合わせ
コストダウンが利益に直結する術だと理解していても、なかなか前に進めることができない状況。そんな時は、newjiのコストダウン自動化機能で大きく利益貢献しよう!
(β版非公開)