- お役立ち記事
- Effective implementation methods of JIT (Just In Time) production systems
Effective implementation methods of JIT (Just In Time) production systems
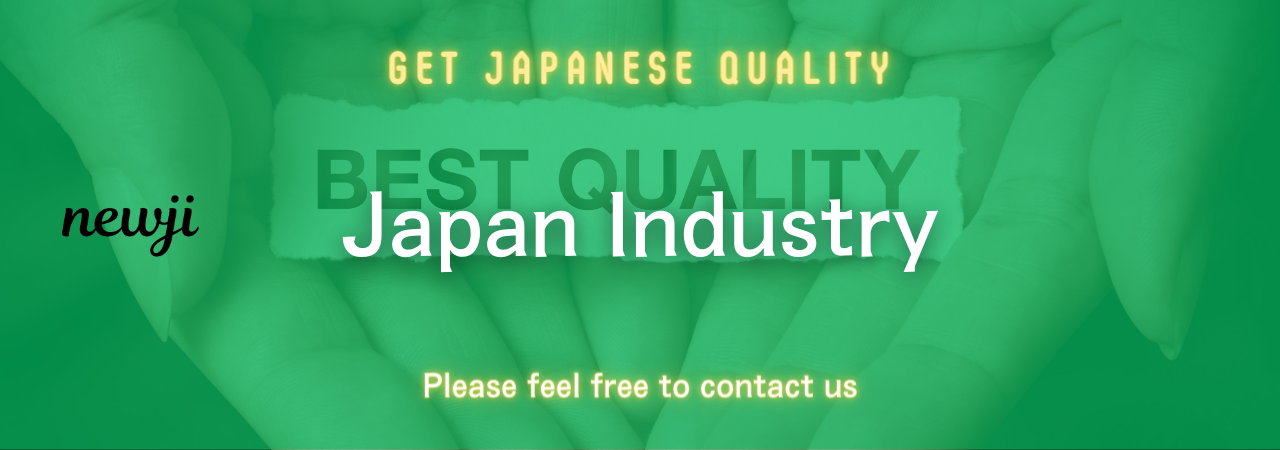
Implementing Just-In-Time (JIT) production systems can transform the efficiency and effectiveness of manufacturing processes.
JIT focuses on reducing waste by ensuring that parts and materials are produced and provided just when they are needed.
This method minimizes inventory costs and improves overall workflow.
In this article, we’ll explore effective methods for implementing JIT production systems.
目次
Understanding JIT Production
Just-In-Time production, often abbreviated as JIT, is a strategy that strives to improve a business’s return on investment by reducing in-process inventory and associated carrying costs.
The main goal is to produce only what is needed, when it is needed, and in the amount needed.
JIT originated from Toyota’s manufacturing processes in Japan.
Now, it is widely adopted by companies worldwide to enhance production efficiency and reduce waste.
Benefits of JIT Production Systems
Implementing JIT production systems offers several advantages:
Reduced Inventory Costs
One of the primary benefits of JIT is the dramatic reduction in inventory levels.
With JIT, materials and components are ordered and produced only as needed, which decreases storage costs and minimizes the risk of excess or obsolete inventory.
Increased Efficiency
JIT production systems promote a streamlined process.
By eliminating unnecessary steps and ensuring a smooth flow of materials, companies can achieve higher efficiency in their production operations.
Improved Quality
JIT emphasizes producing parts and products right the first time.
Continuous improvement and quality control are integral to JIT, leading to higher quality products and fewer defects.
Enhanced Supplier Relationships
With JIT, companies often work closely with their suppliers to ensure timely delivery of materials and components.
This collaboration can lead to stronger relationships and better communication with suppliers, ultimately benefiting both parties.
Steps to Implement JIT Production Systems
To effectively implement a JIT production system, companies should follow these steps:
Assess Current Processes
Before implementing JIT, it’s crucial to evaluate the current production processes.
Identify areas of waste, inefficiencies, and bottlenecks.
This assessment will provide a baseline for improvement and help pinpoint where JIT principles can be most beneficial.
Streamline Workflows
Simplify and streamline workflows to eliminate unnecessary steps and ensure a smooth production process.
Kaizen, or continuous improvement, plays a significant role in JIT.
Encourage employees to identify inefficiencies and suggest improvements.
Implement Pull Systems
JIT relies on pull systems rather than push systems.
In a pull system, production is driven by customer demand rather than forecasted demand.
This means manufacturing only what the customer has ordered and not based on predicted requirements.
Develop Strong Supplier Relationships
Reliable and timely delivery of materials is essential for JIT to work effectively.
Establish strong relationships with suppliers and work with them to ensure they can meet your needs.
This may involve providing forecasts and sharing demand information to help suppliers plan better.
Train Employees
Employee training is vital for successful JIT implementation.
Ensure that workers understand JIT principles and how to apply them in their daily tasks.
Training should emphasize the importance of teamwork, communication, and problem-solving.
Adopt Technology and Automation
Utilizing modern technology and automation can significantly enhance JIT production systems.
Implement software and tools that help monitor and manage inventory, production schedules, and quality control.
Automation can also help streamline repetitive tasks and reduce the likelihood of human error.
Overcoming Challenges in JIT Implementation
Implementing JIT production systems is not without challenges.
Here are some common obstacles and how to overcome them:
Fluctuating Customer Demand
One of the main challenges in JIT is dealing with fluctuating customer demand.
To manage this, companies can adopt flexible production schedules and maintain a small buffer stock.
This approach ensures they can quickly respond to changing customer needs without holding excessive inventory.
Supply Chain Disruptions
Supply chain disruptions can severely impact a JIT system due to its reliance on timely material delivery.
Establishing strong supplier relationships and having backup suppliers can mitigate this risk.
Additionally, maintain open communication channels with suppliers to stay informed about potential disruptions.
Employee Resistance
Employees may resist changes to existing processes, especially if they are unfamiliar with JIT principles.
To overcome this, provide thorough training and involve employees in the implementation process.
Encourage open communication and feedback to address concerns and suggestions.
Quality Control
Maintaining high-Quality standards is essential for JIT success.
Implementing robust quality control measures and regularly inspecting products at various production stages can help ensure that defects are identified and addressed promptly.
Measuring the Success of JIT Implementation
Once JIT production systems are implemented, it’s important to measure their success.
Consider the following metrics:
Inventory Levels
Monitor inventory levels before and after JIT implementation.
A successful JIT system should result in lower inventory levels while meeting production demands.
Lead Time
Measure the time taken from order placement to product delivery.
JIT should reduce lead times, resulting in faster order fulfillment and improved customer satisfaction.
Production Efficiency
Evaluate production efficiency by comparing output rates and waste levels.
A successful JIT implementation should increase productivity and reduce waste.
Quality Standards
Track defect rates and product returns.
Improved quality control measures in JIT should lead to a reduction in defects and higher-Quality products.
Conclusion
Implementing JIT production systems can significantly benefit a company by reducing inventory costs, increasing efficiency, and improving product quality.
By following the outlined steps and overcoming potential challenges, businesses can effectively adopt JIT and enhance their production processes.
Remember that continuous improvement and employee involvement are key to long-term success.
With the right approach, JIT can transform your manufacturing operations and provide a substantial competitive advantage.
資料ダウンロード
QCD調達購買管理クラウド「newji」は、調達購買部門で必要なQCD管理全てを備えた、現場特化型兼クラウド型の今世紀最高の購買管理システムとなります。
ユーザー登録
調達購買業務の効率化だけでなく、システムを導入することで、コスト削減や製品・資材のステータス可視化のほか、属人化していた購買情報の共有化による内部不正防止や統制にも役立ちます。
NEWJI DX
製造業に特化したデジタルトランスフォーメーション(DX)の実現を目指す請負開発型のコンサルティングサービスです。AI、iPaaS、および先端の技術を駆使して、製造プロセスの効率化、業務効率化、チームワーク強化、コスト削減、品質向上を実現します。このサービスは、製造業の課題を深く理解し、それに対する最適なデジタルソリューションを提供することで、企業が持続的な成長とイノベーションを達成できるようサポートします。
オンライン講座
製造業、主に購買・調達部門にお勤めの方々に向けた情報を配信しております。
新任の方やベテランの方、管理職を対象とした幅広いコンテンツをご用意しております。
お問い合わせ
コストダウンが利益に直結する術だと理解していても、なかなか前に進めることができない状況。そんな時は、newjiのコストダウン自動化機能で大きく利益貢献しよう!
(Β版非公開)