- お役立ち記事
- Effective implementation points for DRBFM and FMEA
月間76,176名の
製造業ご担当者様が閲覧しています*
*2025年3月31日現在のGoogle Analyticsのデータより
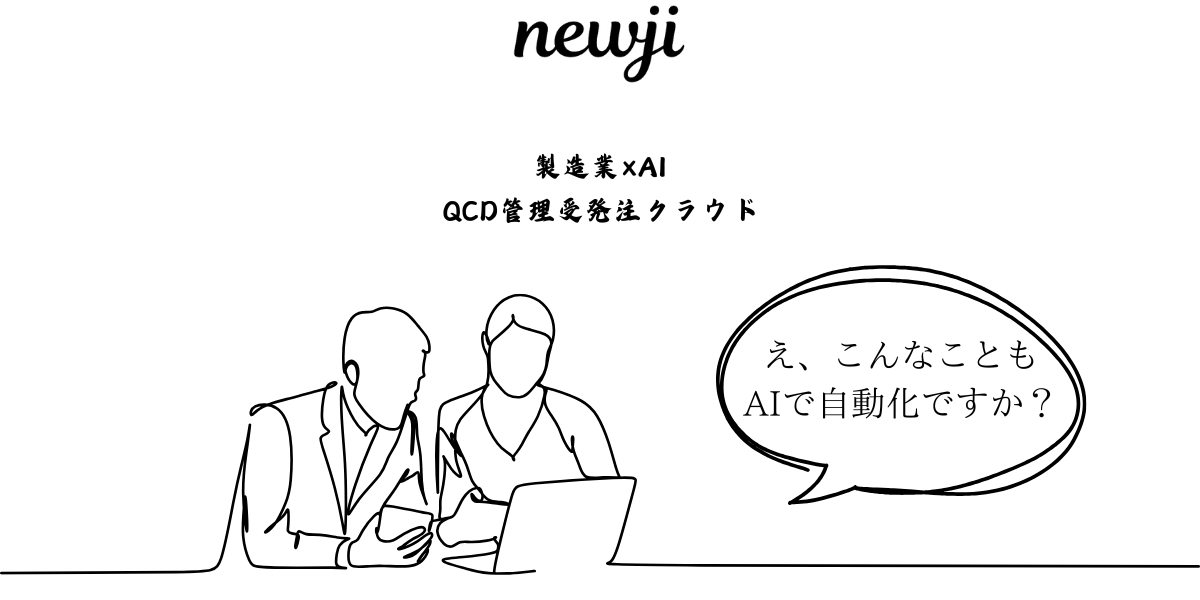
Effective implementation points for DRBFM and FMEA
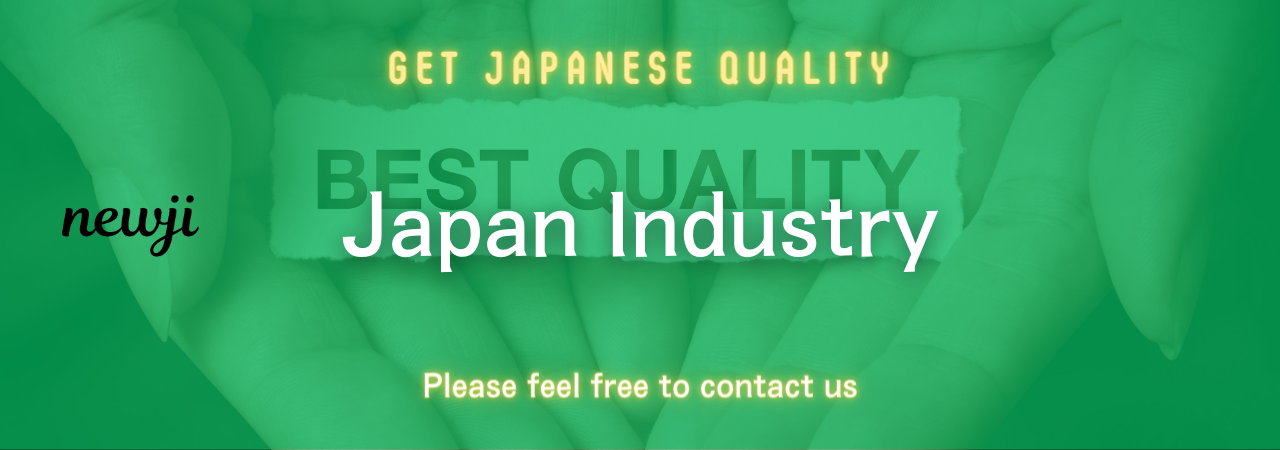
目次
Understanding DRBFM and FMEA
Design Review Based on Failure Mode (DRBFM) and Failure Modes and Effects Analysis (FMEA) are systematic approaches in product development and quality management.
Both methodologies aim to identify potential issues and improve product performance and reliability.
While FMEA is more widespread and older, DRBFM offers a fresh perspective by focusing on understanding and addressing the specific changes made to an existing design.
DRBFM encourages team discussions to uncover potential problems by analyzing changes, even minor ones, in a design.
On the other hand, FMEA is about systematically identifying potential failure modes and their effects to mitigate risks throughout the entire design process.
These tools, when used effectively, can significantly help in minimizing vulnerabilities and enhancing product quality.
The Importance of Effective Implementation
Implementing DRBFM and FMEA effectively is crucial for achieving high product reliability and customer satisfaction.
Both methodologies support proactive problem-solving approaches, allowing teams to foresee potential issues and address them before they materialize.
Effective implementation minimizes costs associated with product recalls, warranty claims, and ensures compliance with industry standards.
Proper integration of DRBFM and FMEA methodologies within the product development process enhances a team’s ability to adapt quickly to design changes and market demands.
They foster a culture of continuous improvement by highlighting areas of potential enhancement and ensuring all elements of the design and production stage are scrutinized effectively.
Steps for Implementing FMEA
Define the Scope
The first step in implementing FMEA is defining the scope.
Identify the system, subsystem, or components to be analyzed.
A clear understanding of the project’s boundaries ensures a comprehensive risk assessment.
Assemble the Team
FMEA is a collaborative process that requires input from various disciplines.
Assemble a cross-functional team with expertise in design, manufacturing, quality assurance, and user experience.
Diverse perspectives can uncover potential failure modes that might be overlooked by a single department.
Identify Failure Modes
During this step, the team identifies potential failure modes, their causes, and effects.
The idea is to brainstorm all possible ways a system or component can fail and document these findings.
Use brainstorming techniques and historical data from similar products to enrich the analysis.
Analyze Effects and Prioritize Risks
Determine the effects of each failure mode on the system’s operation, safety, and customer satisfaction.
The team should prioritize failure modes based on their severity, occurrence, and detectability.
This process helps in focusing resources on the most critical issues.
Develop Action Plans
Once risks are prioritized, develop action plans to mitigate or eliminate the most critical failure modes.
Assign responsibilities to team members to implement these action plans efficiently.
Implementing changes may involve design modifications, process improvements, or enhanced testing protocols.
Review and Update
FMEA is not a one-time activity.
Regularly review and update the analysis as the design progresses and new information becomes available.
Continuous assessment ensures that risk management remains relevant and efficient throughout the product lifecycle.
Steps for Implementing DRBFM
Conduct Change Point Analysis
Identify the changes in the design from existing models or concepts.
Conduct a detailed analysis to understand the implications of these changes on the overall product.
This analysis helps in pinpointing areas that require detailed examination to prevent new failure modes.
Form a Cross-Functional Team
As with FMEA, assemble a team with varied expertise to conduct DRBFM.
The team should engage in open and focused discussions regarding change points to capture insights from all relevant departments.
A collaborative approach enhances the depth and breadth of the failure mode analysis related to the changes.
Facilitate Design Reviews
Conduct structured design reviews that center around exploring and understanding the implications of design changes.
Each review session should critically examine how these changes can affect product functionality or introduce new risks.
Encourage the team to ask “what-if” questions to stimulate dialogue and deeper analysis.
Focus on Action Plans
Once potential issues are identified, develop detailed action plans to address these concerns.
Assign tasks to appropriate team members for implementation.
Ensure the action plans are specific, achievable, and time-bound to facilitate effective execution.
Iterate and Validate
DRBFM should be an iterative process, with continuous validation of design changes.
Test the implemented changes rigorously to confirm that they effectively mitigate identified issues.
Iterate the design and review process as required to ensure product reliability and safety.
Integrating DRBFM and FMEA
Both DRBFM and FMEA can be integrated to complement each other.
While FMEA offers a comprehensive risk analysis across the entire design lifecycle, DRBFM focuses on specific changes, making it an ideal tool for handling design iterations.
By combining both methods, teams can leverage the holistic view of FMEA with the change-focused approach of DRBFM, resulting in superior quality management practices.
Challenges and Tips for Successful Implementation
Implementing DRBFM and FMEA can be challenging due to the need for thorough documentation, team coordination, and management support.
Resistance to change, limited resources, and lack of expertise can hinder the effectiveness of these methodologies.
To overcome these challenges, it is important to provide adequate training and resources to all team members.
Ensure management buy-in to emphasize the importance of these methodologies in achieving quality products.
Regularly communicate progress and findings to maintain engagement and transparency.
Equip teams with digital tools and software to streamline the documentation and analysis process.
These tools can enhance efficiency and accuracy, making it easier to manage complex data and traceability requirements.
In conclusion, the effective implementation of DRBFM and FMEA can lead to significant improvements in product reliability and customer satisfaction.
By following structured steps and integrating these methodologies, organizations can enhance their ability to manage risks and deliver high-quality products consistently.
資料ダウンロード
QCD管理受発注クラウド「newji」は、受発注部門で必要なQCD管理全てを備えた、現場特化型兼クラウド型の今世紀最高の受発注管理システムとなります。
ユーザー登録
受発注業務の効率化だけでなく、システムを導入することで、コスト削減や製品・資材のステータス可視化のほか、属人化していた受発注情報の共有化による内部不正防止や統制にも役立ちます。
NEWJI DX
製造業に特化したデジタルトランスフォーメーション(DX)の実現を目指す請負開発型のコンサルティングサービスです。AI、iPaaS、および先端の技術を駆使して、製造プロセスの効率化、業務効率化、チームワーク強化、コスト削減、品質向上を実現します。このサービスは、製造業の課題を深く理解し、それに対する最適なデジタルソリューションを提供することで、企業が持続的な成長とイノベーションを達成できるようサポートします。
製造業ニュース解説
製造業、主に購買・調達部門にお勤めの方々に向けた情報を配信しております。
新任の方やベテランの方、管理職を対象とした幅広いコンテンツをご用意しております。
お問い合わせ
コストダウンが利益に直結する術だと理解していても、なかなか前に進めることができない状況。そんな時は、newjiのコストダウン自動化機能で大きく利益貢献しよう!
(β版非公開)