- お役立ち記事
- Effective implementation procedures of FMEA/FTA and utilization to prevent quality problems
月間76,176名の
製造業ご担当者様が閲覧しています*
*2025年3月31日現在のGoogle Analyticsのデータより
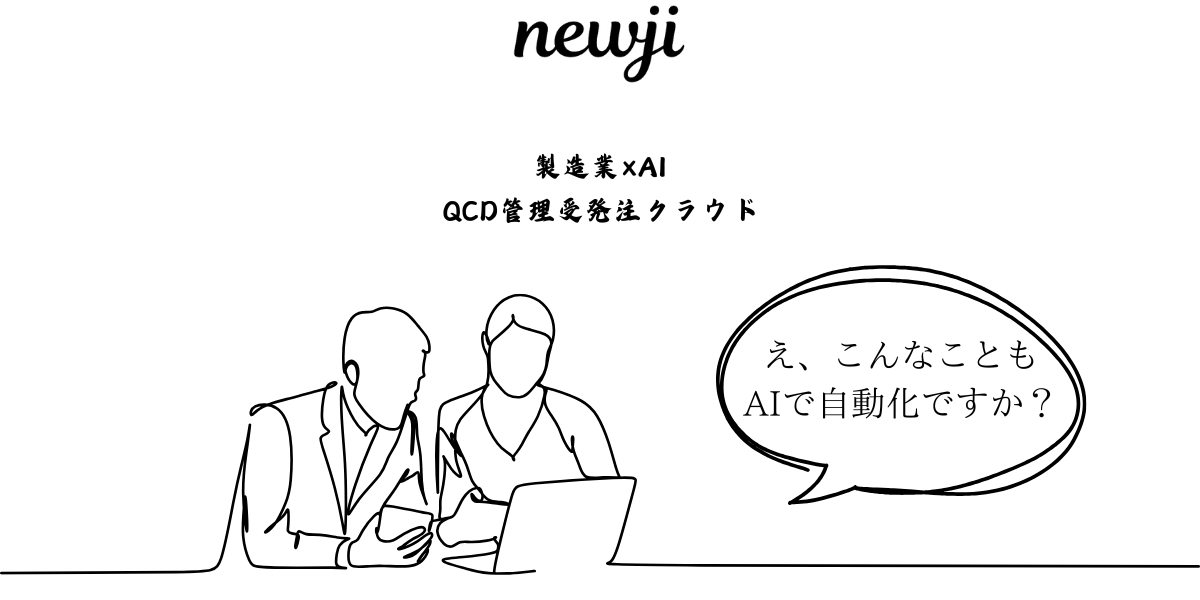
Effective implementation procedures of FMEA/FTA and utilization to prevent quality problems
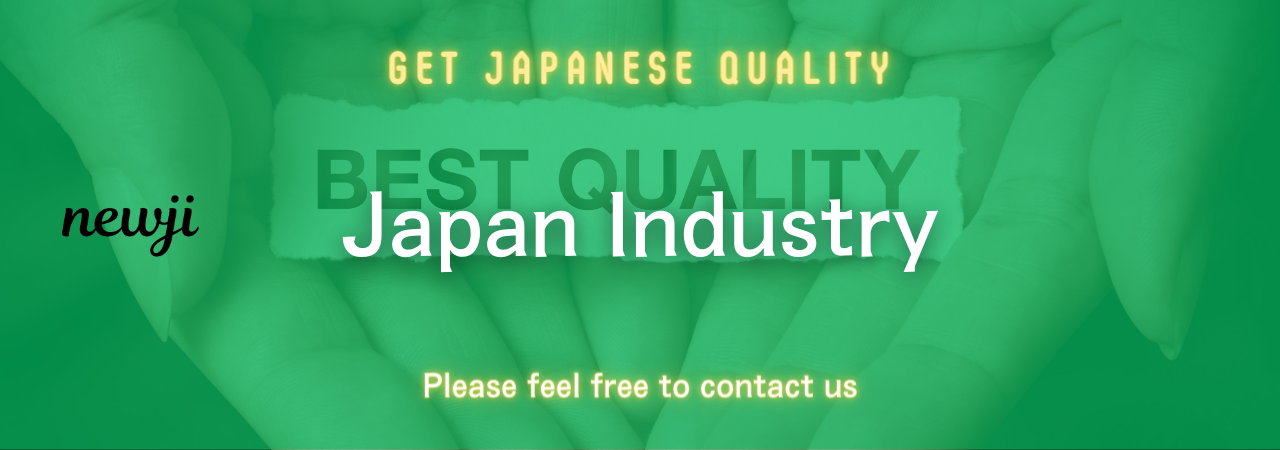
目次
Understanding FMEA and FTA
Failure Modes and Effects Analysis (FMEA) and Fault Tree Analysis (FTA) are crucial methodologies used in identifying potential failures in a product or process.
These techniques help organizations anticipate and reduce the risk of failure, thereby improving product quality and safety.
FMEA focuses on analyzing and preventing potential failure modes within a system, whereas FTA is used to identify the root causes of a specific failure or undesired event.
FMEA begins by identifying all possible failure modes of each component in a system.
Each mode is then evaluated for its effect on the system and the likelihood of its occurrence.
This analysis helps prioritize potential failures for corrective actions.
FTA, on the other hand, uses a top-down approach by starting with a major failure or event.
The analysis works backward to map out all potential causes, represented in a tree-like diagram, making it easier to visualize the root causes and interactions leading to a failure.
Key Steps in Implementing FMEA
Assemble a Cross-Functional Team
The first step in implementing FMEA is to assemble a team comprising individuals from various specialties.
This diverse team brings together different perspectives, ensuring a comprehensive analysis of potential failure modes.
Define the Scope and Objectives
It is critical to define the boundaries and objectives of the FMEA process.
The team should determine which processes, components, or systems are included and identify key objectives, such as improving safety, enhancing reliability, or reducing costs.
Identify Potential Failure Modes
The next step is to systematically list all potential failure modes for each component or process.
It’s essential to be thorough, covering all likely failure scenarios, including those related to material, design, assembly, and usage.
Analyze Failure Effects and Causes
Each identified failure mode should be analyzed to understand its effect on the overall system.
The analysis should also delve into the root causes of each failure to target effective remedial measures.
Assign Severity, Occurrence, and Detection Ratings
FMEA involves rating each failure mode based on severity (impact on the system), occurrence (likelihood of happening), and detection (effectiveness of current controls).
These ratings help prioritize areas for improvement.
Prioritize and Plan Mitigation Actions
Based on the calculated Risk Priority Number (RPN), which is a product of the severity, occurrence, and detection ratings, the team should prioritize failure modes that require immediate action.
An effort should be made to reduce these RPN values through targeted mitigation actions.
Implement and Monitor Corrective Actions
After planning corrective actions, the next step is implementation.
The team should monitor these actions to ensure their effectiveness and make necessary adjustments over time.
Implementing an Effective FTA Process
Define the Top-Level Event
In FTA, start by clearly defining the undesired event or failure you aim to analyze.
This helps set a clear direction for the analysis and focuses efforts on identifying relevant root causes.
Construct the Fault Tree
The next step is to construct the fault tree diagram, starting from the top-level event.
Map out all possible contributing events or failures using logical gates, such as AND, OR, and NOT, to show their relationships.
Analyze Root Causes
After building the fault tree, the team should analyze each branch to identify root causes.
This involves evaluating each event’s probability of occurrence and its contribution to the top-level failure.
Quantify and Prioritize Risks
Assess the probability and impact of each root cause to determine its risk priority.
Focus on the causes with the highest priority when planning corrective actions.
Develop and Implement Solutions
Based on the prioritized list, create actionable solutions aimed at mitigating or eliminating root causes.
Implement these solutions while ensuring they are integrated into current processes efficiently.
Integrating FMEA and FTA for Optimal Results
FMEA and FTA can be integrated to maximize their effectiveness in preventing quality problems.
While FMEA is more detailed in identifying failure modes at a component level, FTA targets specific failures or undesired events at a higher level.
Combining these tools provides both depth and breadth in analysis, enabling a more comprehensive approach to risk management.
Sequential Use of FMEA and FTA
Using FMEA to first identify potential failure modes and then applying FTA to analyze the highest-risk modes can maximize efficiency.
This approach pinpoints critical areas where in-depth root cause analysis and solutions are needed.
Real-World Application and Continuous Improvement
Implementing FMEA and FTA is not a one-time task.
Organizations should integrate these methodologies into their quality management systems to ensure continual improvement.
Regular reviews and updates after each implementation phase help adapt to changes in processes, products, or market expectations, maintaining high-quality standards over time.
資料ダウンロード
QCD管理受発注クラウド「newji」は、受発注部門で必要なQCD管理全てを備えた、現場特化型兼クラウド型の今世紀最高の受発注管理システムとなります。
ユーザー登録
受発注業務の効率化だけでなく、システムを導入することで、コスト削減や製品・資材のステータス可視化のほか、属人化していた受発注情報の共有化による内部不正防止や統制にも役立ちます。
NEWJI DX
製造業に特化したデジタルトランスフォーメーション(DX)の実現を目指す請負開発型のコンサルティングサービスです。AI、iPaaS、および先端の技術を駆使して、製造プロセスの効率化、業務効率化、チームワーク強化、コスト削減、品質向上を実現します。このサービスは、製造業の課題を深く理解し、それに対する最適なデジタルソリューションを提供することで、企業が持続的な成長とイノベーションを達成できるようサポートします。
製造業ニュース解説
製造業、主に購買・調達部門にお勤めの方々に向けた情報を配信しております。
新任の方やベテランの方、管理職を対象とした幅広いコンテンツをご用意しております。
お問い合わせ
コストダウンが利益に直結する術だと理解していても、なかなか前に進めることができない状況。そんな時は、newjiのコストダウン自動化機能で大きく利益貢献しよう!
(β版非公開)