- お役立ち記事
- Effective Management of Hold Pressure Processes That SMEs Should Know
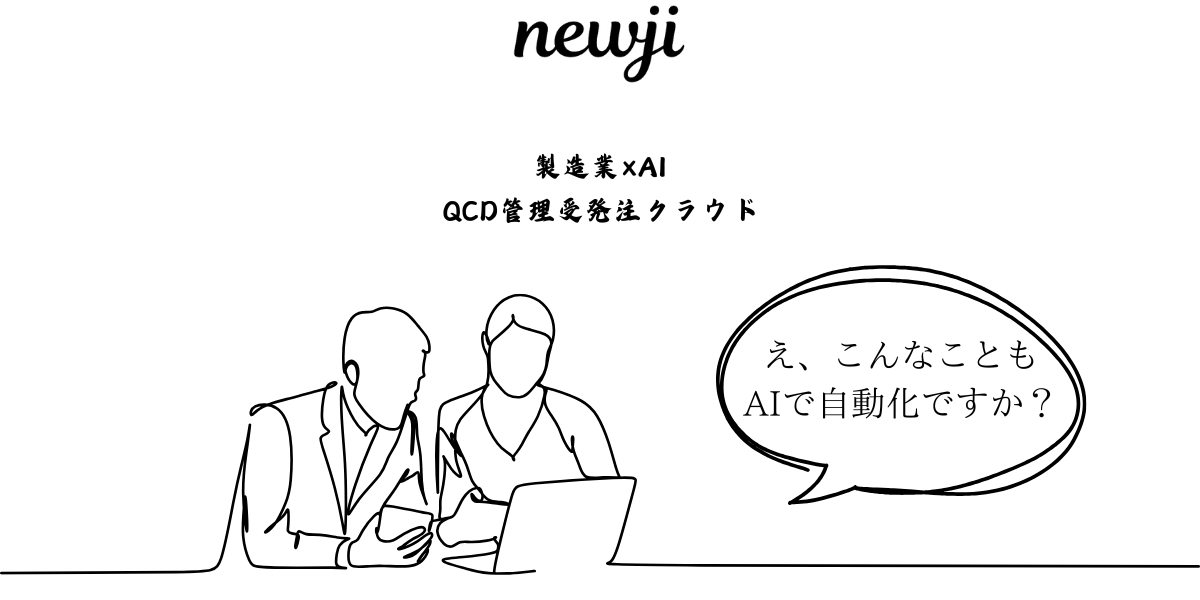
Effective Management of Hold Pressure Processes That SMEs Should Know
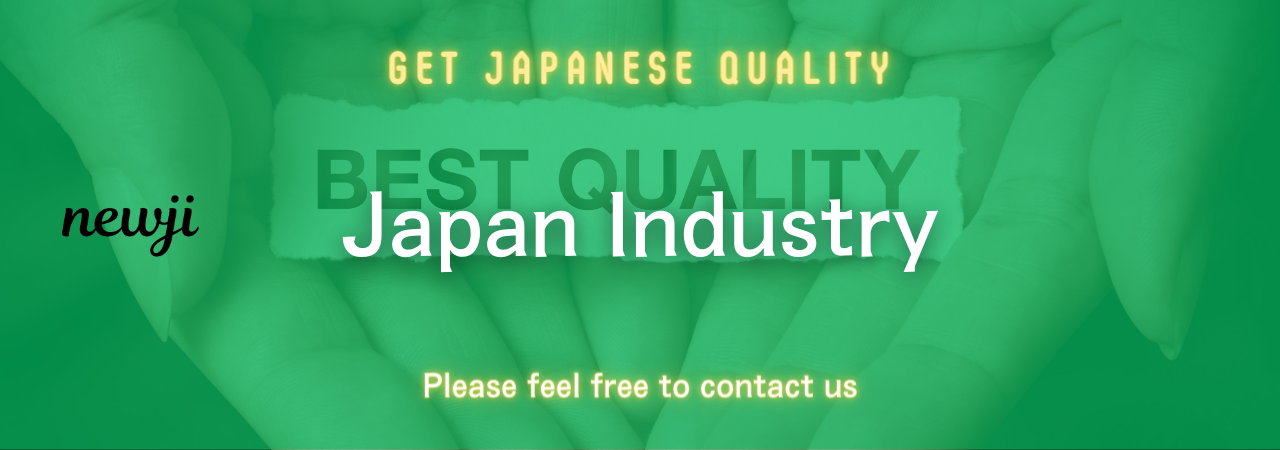
目次
Understanding the Concept of Hold Pressure
Hold pressure is a crucial aspect of the manufacturing process, particularly in industries involved in injection molding and similar production methods.
It refers to the pressure applied to the molten material after it has been injected into the mold cavity.
The purpose of maintaining this pressure is to ensure that the product retains its precise shape and size as the material cools and solidifies.
For small and medium-sized enterprises (SMEs), effective management of hold pressure processes can lead to enhanced production quality, minimized waste, and improved economic efficiency.
Understanding hold pressure is the first step towards optimizing its management.
The Importance of Hold Pressure in Manufacturing
In the realm of manufacturing, particularly in processes like injection molding, hold pressure becomes fundamental for several reasons.
It aids in compensating for material shrinkage as it cools, ensuring the final product meets design specifications.
Without adequate hold pressure, parts may end up with sink marks, warping, or internal stress, reducing their reliability and functionality.
For SMEs, maintaining high standards of product quality is imperative for customer satisfaction and competitiveness.
Proper hold pressure management contributes directly to these standards, promoting precision and consistency across production batches.
Quality Control
During production, inconsistencies in hold pressure can lead to defects.
For SMEs, this translates to increased rejection rates and higher costs due to material waste and rework requirements.
Maintaining consistent and calculated hold pressure ensures that each product meets the desired quality parameters from the outset.
This control reduces waste, optimizes material usage, and ensures customer satisfaction with fewer defects and recalls.
Economic Efficiency
In smaller operations where resources are limited, efficient use of materials and time is crucial.
Optimizing hold pressure reduces the risk of over-using materials, thereby lowering costs.
Additionally, well-managed hold pressure processes usually result in faster cycle times, as cooling and solidification occurs more predictably, allowing SMEs to increase throughput and productivity.
Techniques to Optimize Hold Pressure Processes
To effectively manage hold pressure, SMEs should consider a strategic approach that involves several techniques.
Utilize Advanced Monitoring Tools
Investing in advanced monitoring and control systems can significantly help SMEs enhance their hold pressure procedures.
These tools provide real-time data and insights into the conditions and variables affecting the injection molding process, allowing operators to make timely adjustments and maintain desired pressure levels throughout production.
By harnessing data analytics, SMEs can predict and mitigate potential issues before they lead to production downtimes or defects.
Material Selection
The choice of material influences how it reacts under pressure.
SMEs must select materials that align well with their production needs and desired product characteristics.
Understanding the properties of different thermoplastics and thermosets and how they behave under hold pressure is essential in achieving the best results.
By choosing the right materials, the process of holding pressure can be optimized, leading to better structural integrity and fewer defects in the final products.
Regular Maintenance and Calibration
Equipment maintenance and calibration are critical when managing hold pressure effectively.
Regular inspections and servicing of machines ensure that they operate within desired parameters.
Calibration is particularly important to guarantee that measurement tools provide correct data, allowing accurate control over pressure settings.
Consistent maintenance practices help avoid unexpected machine failures and maintain stability in production quality.
Training and Skill Development
Educating the workforce on the importance and methods of hold pressure management is crucial.
Operators who understand the science behind the process are more adept at spotting potential issues and executing precise control over equipment.
Providing continuous education, workshops, and training can empower staff, making them more proactive and efficient in responding to production challenges.
Challenges SMEs May Face
Despite its importance, managing hold pressure can pose challenges, especially for SMEs.
Unlike larger corporations, SMEs may have constraints in terms of budget, technology access, and skilled personnel.
Limited Resources
Resource limitations can restrict SMEs from investing in advanced technologies that larger companies might employ.
Additionally, the cost of acquiring and implementing new equipment can be a significant barrier.
SMEs need to balance their resource allocation carefully and consider incremental upgrades and collaborations with technology providers to mitigate these issues.
Skilled Workforce Shortage
Finding skilled personnel who understand the intricacies of hold pressure processes can be challenging.
SMEs might struggle to attract talent, competing against larger firms with more lucrative offers.
Developing in-house training programs and partnering with local educational institutions can be effective strategies to bridge this gap.
Conclusion
For SMEs, mastering the management of hold pressure processes is crucial for sustainability and growth within competitive markets.
By prioritizing quality control, economic efficiency, and continuous improvement through advanced techniques and workforce development, SMEs can enhance their production capabilities significantly.
While challenges exist, strategic planning and flexible adaptation to emerging technologies can empower SMEs to refine their manufacturing processes and boost their overall productivity and customer satisfaction.
資料ダウンロード
QCD調達購買管理クラウド「newji」は、調達購買部門で必要なQCD管理全てを備えた、現場特化型兼クラウド型の今世紀最高の購買管理システムとなります。
ユーザー登録
調達購買業務の効率化だけでなく、システムを導入することで、コスト削減や製品・資材のステータス可視化のほか、属人化していた購買情報の共有化による内部不正防止や統制にも役立ちます。
NEWJI DX
製造業に特化したデジタルトランスフォーメーション(DX)の実現を目指す請負開発型のコンサルティングサービスです。AI、iPaaS、および先端の技術を駆使して、製造プロセスの効率化、業務効率化、チームワーク強化、コスト削減、品質向上を実現します。このサービスは、製造業の課題を深く理解し、それに対する最適なデジタルソリューションを提供することで、企業が持続的な成長とイノベーションを達成できるようサポートします。
オンライン講座
製造業、主に購買・調達部門にお勤めの方々に向けた情報を配信しております。
新任の方やベテランの方、管理職を対象とした幅広いコンテンツをご用意しております。
お問い合わせ
コストダウンが利益に直結する術だと理解していても、なかなか前に進めることができない状況。そんな時は、newjiのコストダウン自動化機能で大きく利益貢献しよう!
(Β版非公開)