- お役立ち記事
- Effective manufacturing process improvement by changing the linear type of dicing blade
月間77,185名の
製造業ご担当者様が閲覧しています*
*2025年2月28日現在のGoogle Analyticsのデータより
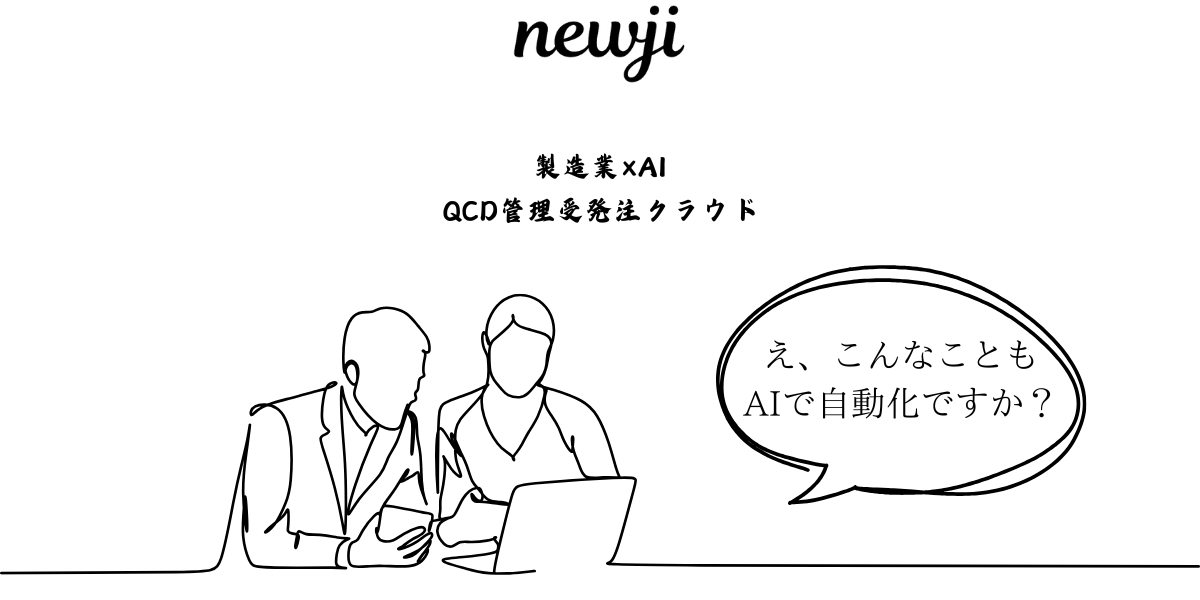
Effective manufacturing process improvement by changing the linear type of dicing blade
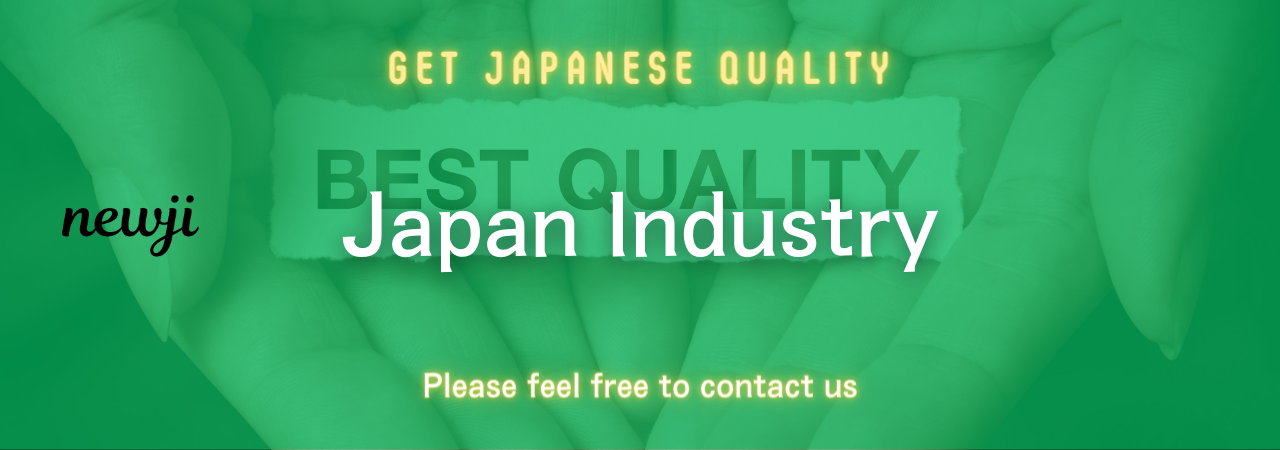
目次
Introduction to Dicing Blades in Manufacturing
In the world of manufacturing, precision plays a crucial role in ensuring the quality and efficiency of production processes.
Among the many tools used for this task, dicing blades are fundamental.
These blades are specialized cutting tools used to dice semiconductor wafers, glass, ceramics, and other materials into smaller, precise pieces.
Choosing the right dicing blade can significantly impact the final product’s quality and the efficiency of the manufacturing process.
What Are Linear Type Dicing Blades?
Linear type dicing blades are a specific kind of blade with a straightforward design.
They are constructed in a linear pattern, allowing them to make precise, straight cuts on various materials.
These blades are widely used for their simplicity and effectiveness in straightforward cutting tasks.
However, as manufacturing requirements evolve, the need to optimize dicing blades for specific applications has become more prominent.
Challenges of Using Linear Type Dicing Blades
While linear type dicing blades are effective, they are not without challenges.
They can be limiting in terms of versatility and sometimes fall short in delivering high precision for complex cutting tasks.
Linear designs, by nature, are less adaptable to irregular shapes or complex geometries.
Manufacturers often find themselves facing limitations regarding speed and accuracy.
Additionally, linear type blades might not be the best choice for materials that require intricate or circular cuts, potentially leading to inefficiencies.
The Need for Improvement in the Manufacturing Process
The global manufacturing industry is always on the lookout for improvements that can enhance productivity and product quality.
Improving the manufacturing process by upgrading tools such as dicing blades is one such avenue.
Effective process enhancement involves identifying limitations and finding innovative solutions that minimize waste, reduce downtime, and increase output rates.
Innovative Solutions: Changing the Blade Design
One effective way to improve manufacturing processes is by changing the design of the dicing blades.
Moving away from traditional linear designs to more advanced blade styles can enhance cutting precision and overall efficiency.
Advanced dicing blades often incorporate specialized designs such as circular patterns, zigzag edges, or varying tooth shapes.
These designs offer improved adaptability to diverse cutting tasks, thereby optimizing the manufacturing process.
Benefits of Advanced Dicing Blade Designs
Utilizing advanced dicing blade designs can offer numerous benefits.
Firstly, they significantly improve precision due to their enhanced cutting capabilities.
This precision directly results in a higher yield of quality products.
Secondly, these blades can cut through a wider variety of materials and shapes, thus broadening the scope of manufacturing possibilities.
Another key benefit is reduced downtime and maintenance costs, as advanced blades are often designed to be more durable and efficient than their linear counterparts.
This ultimately translates to cost savings for manufacturers.
Implementing Changes in the Manufacturing Process
Integrating new blade designs into existing manufacturing processes requires careful planning.
The transition involves examining the existing setup, understanding specific manufacturing needs, and selecting the right blades for the job.
Consulting with blade manufacturers and conducting trials can help identify the most suitable blade type and design for specific applications.
Steps for Effective Implementation
1. **Analyze Current Processes**: Understand the current limitations and requirements of your manufacturing process.
2. **Research and Selection**: Research available dicing blade options and select those that meet your specific needs.
3. **Consultation and Testing**: Work with blade experts and test different blades to find the optimal design.
4. **Training and Integration**: Train staff on the new equipment and integrate the blades into your process with minimal disruption.
5. **Monitor and Adjust**: After implementation, closely monitor performance to identify areas for further improvement and make adjustments as necessary.
Challenges in Implementation
Implementing changes can pose certain challenges.
There may be initial setup costs and time constraints as workers adapt to new tools.
Moreover, identifying the correct blade type for specific materials requires expertise, which might necessitate additional training or consultation.
However, the long-term benefits of increased efficiency and product quality outweigh these initial obstacles.
Conclusion
Improving the manufacturing process by transitioning from linear to advanced dicing blade designs presents significant opportunities.
By making strategic changes to blade selection, manufacturers can achieve greater precision, reduced waste, and overall cost savings.
While the implementation may come with initial challenges, the long-term benefits can lead to a more streamlined and effective production process.
As technology advances, embracing innovative solutions in manufacturing ensures a competitive edge and high-quality output.
資料ダウンロード
QCD管理受発注クラウド「newji」は、受発注部門で必要なQCD管理全てを備えた、現場特化型兼クラウド型の今世紀最高の受発注管理システムとなります。
ユーザー登録
受発注業務の効率化だけでなく、システムを導入することで、コスト削減や製品・資材のステータス可視化のほか、属人化していた受発注情報の共有化による内部不正防止や統制にも役立ちます。
NEWJI DX
製造業に特化したデジタルトランスフォーメーション(DX)の実現を目指す請負開発型のコンサルティングサービスです。AI、iPaaS、および先端の技術を駆使して、製造プロセスの効率化、業務効率化、チームワーク強化、コスト削減、品質向上を実現します。このサービスは、製造業の課題を深く理解し、それに対する最適なデジタルソリューションを提供することで、企業が持続的な成長とイノベーションを達成できるようサポートします。
製造業ニュース解説
製造業、主に購買・調達部門にお勤めの方々に向けた情報を配信しております。
新任の方やベテランの方、管理職を対象とした幅広いコンテンツをご用意しております。
お問い合わせ
コストダウンが利益に直結する術だと理解していても、なかなか前に進めることができない状況。そんな時は、newjiのコストダウン自動化機能で大きく利益貢献しよう!
(β版非公開)