- お役立ち記事
- Effective MBD Implementation and Strategies for Preventing Rework
Effective MBD Implementation and Strategies for Preventing Rework
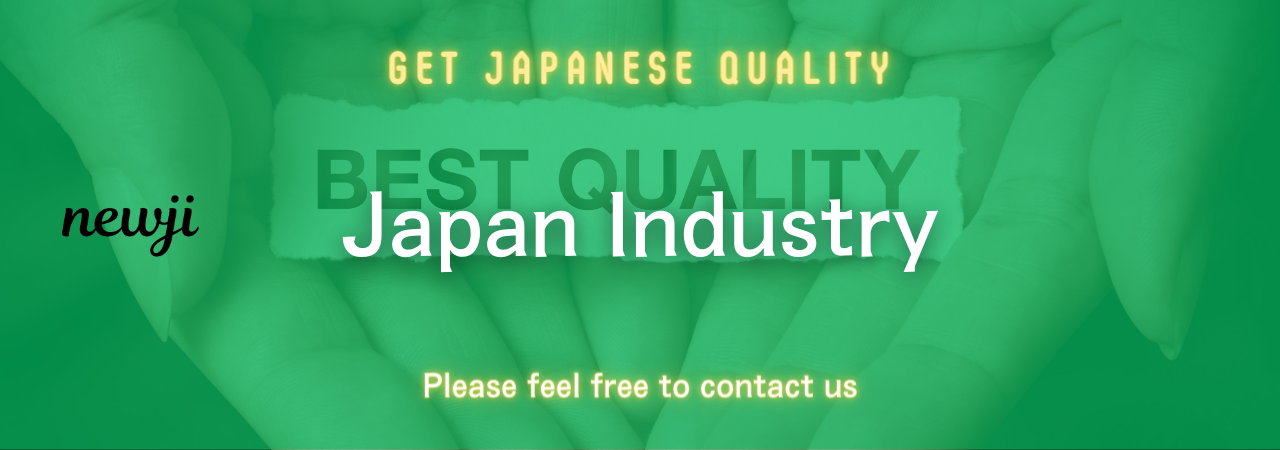
目次
Understanding Model-Based Definition (MBD)
Model-Based Definition, commonly abbreviated as MBD, is a method used to define product specifications directly within a 3D CAD model.
This approach serves as an alternative to traditional 2D drawings by embedding all necessary information, such as dimensions, tolerances, and annotations, within the 3D model itself.
MBD helps streamline the design and manufacturing processes by providing a single, authoritative source for product data.
This methodology is crucial for industries aiming to accelerate their production cycles and reduce errors.
The Importance of MBD Implementation
Implementing MBD effectively can bring about significant improvements in efficiency and communication across different departments.
One of the main benefits of MBD is the elimination of discrepancies that often arise from interpreting 2D drawings.
By using a single digital model, all team members—from design through to manufacturing—operate on consistent information, minimizing misunderstandings.
Additionally, MBD can enhance product quality.
By leveraging precise digital models, companies can carry out more accurate simulations and analyses, leading to better-engineered products.
Moreover, embracing MBD can foster innovation by freeing up time and resources that would otherwise be spent on updating and managing multiple document versions.
Common Challenges in MBD Adoption
While the advantages of MBD are clear, its adoption comes with challenges.
One of the major obstacles is the transition from traditional 2D drawings to 3D models, which can be resource-intensive in terms of both time and training.
Organizations must ensure that their workforce is proficient in the tools and methodologies associated with MBD to fully leverage its benefits.
Data management is another hurdle.
With MBD, companies must invest in robust data management solutions to handle the complex and large files that 3D models generate.
Properly organizing and securing these digital models is essential to prevent information loss and unauthorized access.
Moreover, integrating MBD into existing workflows requires careful planning.
Companies must address any compatibility issues between new MBD systems and legacy processes to ensure a smooth transition.
Strategies for Successful MBD Implementation
To implement MBD effectively and prevent rework, organizations should consider a phased approach.
Begin with a pilot project to test MBD on a small scale, allowing teams to learn and adapt to the new system without overwhelming organizational resources.
This pilot will serve as a learning platform, helping identify potential issues and refine the implementation strategy.
Comprehensive training is essential.
Ensure that all relevant employees receive training on 3D modeling tools, MBD principles, and data management practices.
This investment in human capital is crucial for a smooth transition and maximizing the potential of MBD.
Collaboration across departments should be encouraged to streamline communication.
Set up cross-functional teams that include members from design, manufacturing, and IT to coordinate the MBD rollout and address any obstacles.
Furthermore, selecting the right software tools is critical.
Evaluate various MBD solutions to find one that fits the organization’s specific needs.
Factors such as scalability, user-friendliness, and compatibility with existing systems should be considered.
Technological Integration and Data Management
When it comes to technological integration, companies should ensure that their MBD software seamlessly integrates with existing CAD, PLM, and ERP systems.
This interoperability will enable smoother transitions and more efficient workflows.
Moreover, integrated systems reduce the potential for errors during data transfer between different platforms.
Implementing a strong data management strategy is equally important.
Organizations need to establish processes for consistent data entry, storage, and retrieval to ensure that teams are always working with the most accurate and up-to-date information.
Regular audits should be conducted to maintain data integrity and address any emerging issues promptly.
Leveraging Industry Standards and Best Practices
Adopting industry standards and best practices is another key strategy for effective MBD implementation.
Standards such as ASME Y14.41 and ISO 16792 provide guidelines on how to apply MBD across different industries.
Familiarizing teams with these standards can assist organizations in developing consistent and reliable MBD practices.
Networking with other companies and participating in industry conferences can also be beneficial.
These interactions provide valuable insights into best practices, common pitfalls, and emerging trends in MBD.
Such knowledge sharing can help your organization refine its approach and stay ahead of the curve.
Preventing Rework Through MBD
One of the primary goals of MBD is to reduce the need for rework, which is a common source of wasted resources and extended timelines in product development.
Rework often results from errors or miscommunications in product specifications, which MBD seeks to eliminate by providing a single, accurate source of truth.
To further prevent rework, establish processes for regular reviews and validation of the 3D models at various stages of the design and manufacturing processes.
Incorporate feedback loops to detect and rectify potential discrepancies early on.
Encouraging a culture of continuous improvement is also beneficial.
By regularly reviewing processes and seeking ways to enhance MBD implementation, organizations can prevent issues from occurring repeatedly.
This proactive approach helps maintain high standards of product quality and efficiency.
Conclusion
Effective MBD implementation and strategies for preventing rework require a thoughtful, phased approach.
By adopting MBD, organizations can improve efficiency, accuracy, and product quality while minimizing errors.
With proper planning, training, and technology integration, companies can overcome the challenges associated with MBD adoption and reap its many benefits.
In the long run, implementing robust data management practices and leveraging industry best practices will position organizations for success.
By emphasizing collaboration and continuous improvement, companies can prevent rework and improve overall operational efficiency.
資料ダウンロード
QCD調達購買管理クラウド「newji」は、調達購買部門で必要なQCD管理全てを備えた、現場特化型兼クラウド型の今世紀最高の購買管理システムとなります。
ユーザー登録
調達購買業務の効率化だけでなく、システムを導入することで、コスト削減や製品・資材のステータス可視化のほか、属人化していた購買情報の共有化による内部不正防止や統制にも役立ちます。
NEWJI DX
製造業に特化したデジタルトランスフォーメーション(DX)の実現を目指す請負開発型のコンサルティングサービスです。AI、iPaaS、および先端の技術を駆使して、製造プロセスの効率化、業務効率化、チームワーク強化、コスト削減、品質向上を実現します。このサービスは、製造業の課題を深く理解し、それに対する最適なデジタルソリューションを提供することで、企業が持続的な成長とイノベーションを達成できるようサポートします。
オンライン講座
製造業、主に購買・調達部門にお勤めの方々に向けた情報を配信しております。
新任の方やベテランの方、管理職を対象とした幅広いコンテンツをご用意しております。
お問い合わせ
コストダウンが利益に直結する術だと理解していても、なかなか前に進めることができない状況。そんな時は、newjiのコストダウン自動化機能で大きく利益貢献しよう!
(Β版非公開)