- お役立ち記事
- Effective methods of inventory management and supply and demand adjustment that purchasing departments should focus on
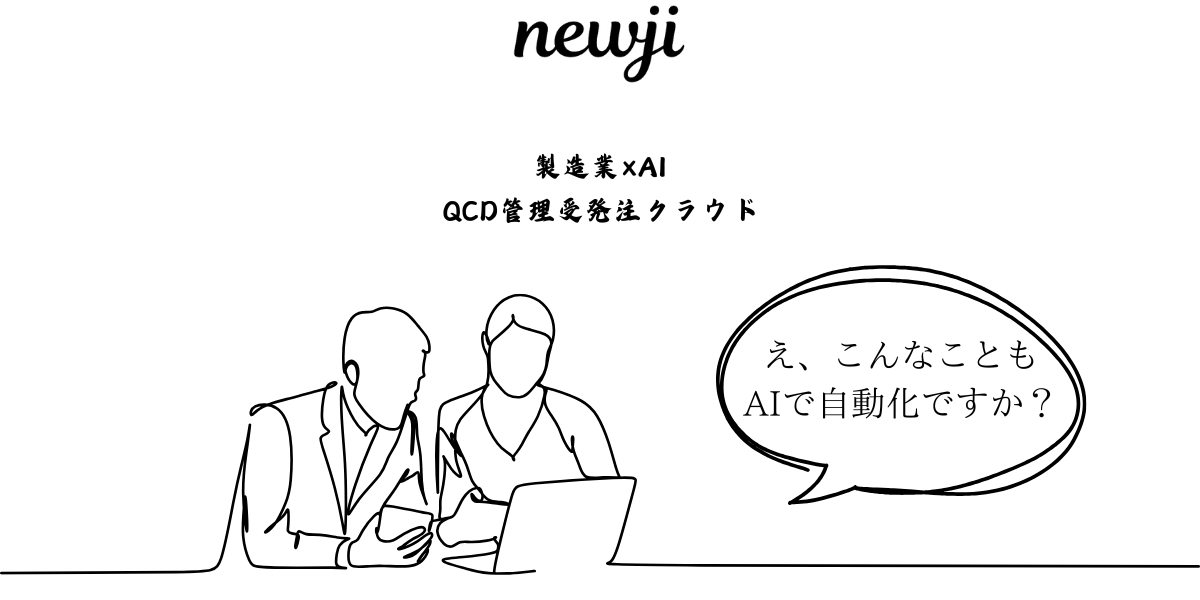
Effective methods of inventory management and supply and demand adjustment that purchasing departments should focus on
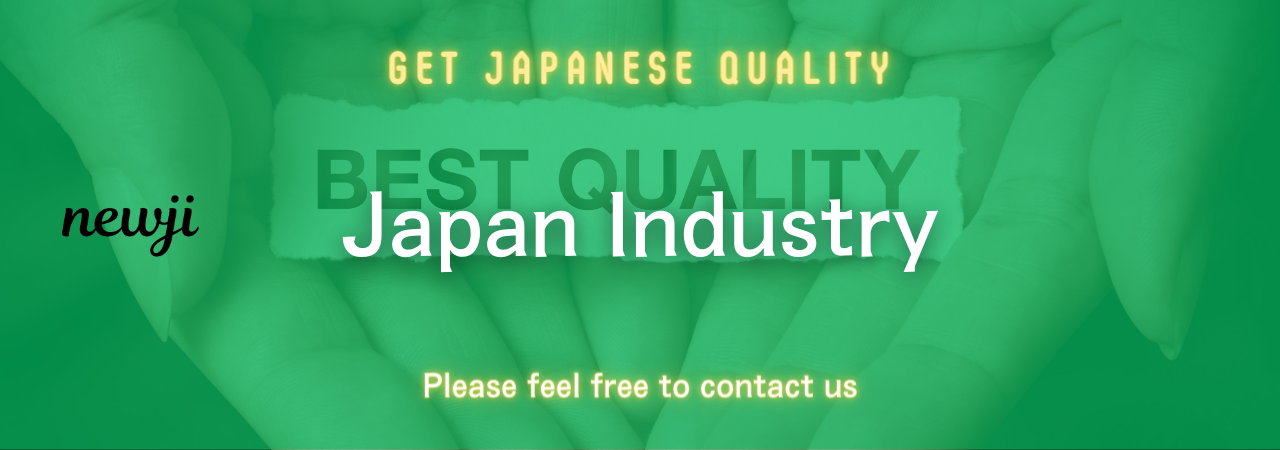
目次
Understanding Inventory Management
Inventory management refers to the process of ordering, storing, using, and selling a company’s inventory.
This includes the management of raw materials, components, and finished products, as well as warehousing and processing such items.
Effective inventory management is crucial for maintaining operational efficiency and ensuring a company can meet customer demands while minimizing costs.
The purchasing department plays a vital role in managing inventory, as it involves buying goods and services needed by the company.
By focusing on effective inventory management and supply and demand adjustment, the purchasing department can help optimize service levels and control costs.
Fundamentals of Supply and Demand Adjustment
Supply and demand adjustment entails aligning the availability of products with the needs of customers.
When done correctly, this process ensures that the inventory levels are sufficient to meet customer demand but not so excessive that it results in overstock, unnecessary storage costs, or obsolescence.
The purchasing department should focus on analyzing past sales data and market trends to accurately forecast future demand.
This analysis helps in making informed purchasing decisions that balance supply with expected demand levels.
Forecasting Demand
Accurate demand forecasting is one of the most effective methods for managing inventory.
Utilizing data analytics and software solutions can provide insights into market trends and customer behavior, allowing for better predictions of future demand.
This foresight enables purchasing departments to make informed decisions when ordering stock, thus reducing the risk of overstock or stockouts.
Setting Optimal Inventory Levels
Setting optimal inventory levels requires a fine balance between minimizing holding costs and meeting customer demand.
Using methods such as Economic Order Quantity (EOQ) can aid in determining the ideal order quantity that minimizes total inventory costs.
The EOQ model considers factors such as demand rate, ordering cost, and holding cost to find the most cost-effective quantity to order.
By implementing EOQ and other inventory management techniques, purchasing departments can optimize stock levels and reduce unnecessary expenses.
Strategies for Effective Inventory Management
Several strategies can be employed to ensure effective inventory management and supply and demand adjustment.
Just-in-Time (JIT) Inventory
Just-in-Time (JIT) inventory management aims to reduce waste and improve efficiency by receiving goods only as they are needed in the production process.
This approach minimizes inventory costs but requires accurate demand forecasting and a reliable supplier network to succeed.
Purchasing departments must work closely with suppliers to ensure timely deliveries, which mitigates the risks of stockouts.
ABC Analysis
ABC Analysis is an inventory categorization technique that divides items into three categories based on their importance:
– Category A: Items with the highest value and tightest control.
– Category B: Items with moderate value and control.
– Category C: Items with the lowest value and simple control.
By focusing greater attention and resources on Category A items, purchasing departments can ensure that high-value inventory is managed efficiently.
ABC Analysis helps in prioritizing management efforts and resource allocation to optimize inventory control.
Utilizing Technology and Automation
Technology and automation have revolutionized the way companies manage inventory.
Modern inventory management software can track inventory in real-time, alert managers to replenishment needs, and provide analytics to support smart decision-making.
Automation reduces the risk of human error and increases accuracy and efficiency in handling inventory-related tasks.
Purchasing departments should invest in up-to-date software tools to streamline inventory management processes and enhance overall productivity.
Enhancing Communication and Collaboration
Effective inventory management requires seamless communication and collaboration among different departments, such as sales, finance, and operations.
Integrated Planning
Integrating inventory management with other business operations ensures that all departments work towards common goals.
Sales forecasts, marketing campaigns, and production schedules should be shared with the purchasing department to create a cohesive plan.
This collaboration minimizes discrepancies between actual demand and stock availability, leading to more efficient inventory control.
Supplier Relationships
Building strong relationships with suppliers is crucial for ensuring timely and cost-effective procurement.
Open communication leads to better understanding of each party’s needs and capabilities.
A strategic partnership with suppliers allows for negotiation of favorable terms, quick adjustment to demand changes, and improved supply chain reliability.
Purchasing departments should cultivate effective supplier relationships to make the supply chain more responsive and adaptive.
Continuous Improvement and Evaluation
Regular evaluation and improvement of inventory management practices can lead to increased efficiency and cost savings over time.
Performance Metrics
To gauge the effectiveness of inventory management strategies, purchasing departments should track key performance indicators (KPIs) such as inventory turnover, order accuracy, and carrying costs.
Analyzing these metrics provides insights into areas for improvement and helps in setting realistic goals for inventory management.
Tracking and evaluating KPIs ensures that purchasing departments remain proactive in refining their processes.
Feedback Loops
Encouraging feedback from team members, customers, and suppliers can unveil opportunities to enhance inventory management practices.
Feedback loops create a culture of continuous improvement, allowing purchasing departments to adapt to changing market conditions and incorporate innovative solutions.
In conclusion, effective methods of inventory management and supply and demand adjustment are critical for purchasing departments to focus on.
By employing strategies such as accurate demand forecasting, Just-in-Time inventory, and utilizing technology, organizations can optimize their inventory levels, reduce costs, and enhance customer satisfaction.
Continual collaboration, evaluation, and improvement will ensure that inventory management processes stay relevant and efficient in an ever-changing market landscape.
資料ダウンロード
QCD調達購買管理クラウド「newji」は、調達購買部門で必要なQCD管理全てを備えた、現場特化型兼クラウド型の今世紀最高の購買管理システムとなります。
ユーザー登録
調達購買業務の効率化だけでなく、システムを導入することで、コスト削減や製品・資材のステータス可視化のほか、属人化していた購買情報の共有化による内部不正防止や統制にも役立ちます。
NEWJI DX
製造業に特化したデジタルトランスフォーメーション(DX)の実現を目指す請負開発型のコンサルティングサービスです。AI、iPaaS、および先端の技術を駆使して、製造プロセスの効率化、業務効率化、チームワーク強化、コスト削減、品質向上を実現します。このサービスは、製造業の課題を深く理解し、それに対する最適なデジタルソリューションを提供することで、企業が持続的な成長とイノベーションを達成できるようサポートします。
オンライン講座
製造業、主に購買・調達部門にお勤めの方々に向けた情報を配信しております。
新任の方やベテランの方、管理職を対象とした幅広いコンテンツをご用意しております。
お問い合わせ
コストダウンが利益に直結する術だと理解していても、なかなか前に進めることができない状況。そんな時は、newjiのコストダウン自動化機能で大きく利益貢献しよう!
(Β版非公開)