- お役立ち記事
- Effective planning of production plans using MRP that production control department leaders should know
Effective planning of production plans using MRP that production control department leaders should know
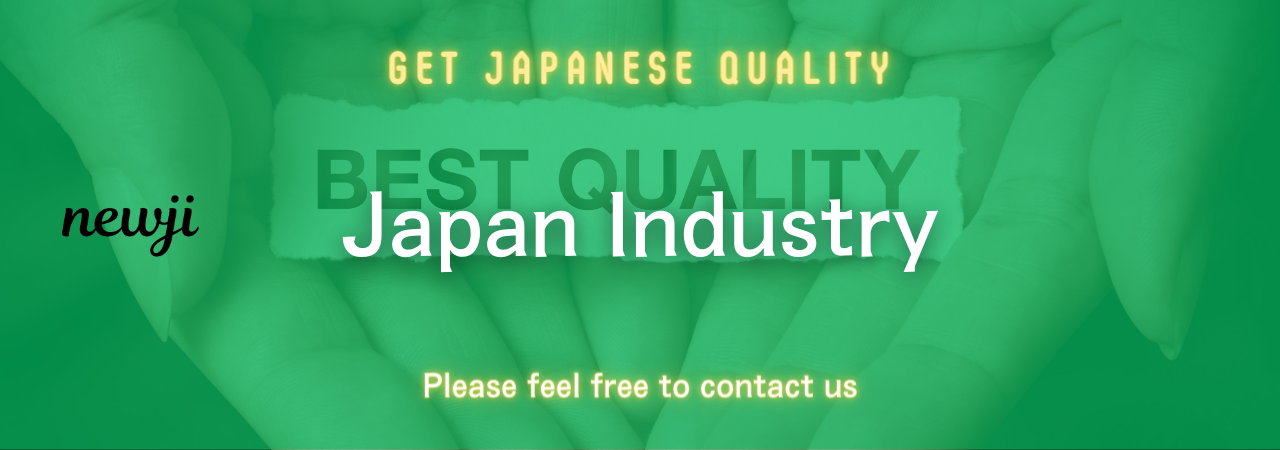
目次
Understanding MRP: A Fundamental Tool for Production Planning
Material Requirements Planning (MRP) is an essential tool in the manufacturing industry, particularly for those in the production control department.
MRP is a system that helps businesses manage manufacturing processes by estimating the quantity and timing of raw material purchases.
It ensures that the necessary materials are available when needed, thereby optimizing production efficiency and minimizing waste.
MRP systems operate on the basic principles of ensuring inventory is available for production and delivery to customers while maintaining the lowest possible inventory levels.
This balance is crucial for enhancing a company’s profitability and operational efficiency.
Understanding how MRP works is vital for production control leaders to make informed decisions and improve production planning.
The Basics of MRP
MRP systems are based on three primary objectives: ensuring material availability, maintaining the lowest possible inventory levels, and planning manufacturing activities, delivery schedules, and purchasing activities.
To achieve these objectives, MRP relies on several key inputs: the master production schedule, inventory status records, and bill of materials.
The master production schedule defines what needs to be produced, in what quantities, and when.
Inventory status records provide detailed information about current inventory levels, open orders, and lead times.
The bill of materials is a comprehensive list of all components, parts, and raw materials required to produce each item.
By analyzing these inputs, an MRP system can determine what materials are needed and when, helping production managers to schedule manufacturing activities efficiently.
Key Benefits of Using MRP in Production Planning
Implementing an effective MRP system within a production control department brings numerous benefits.
Improved Efficiency
MRP systems streamline manufacturing processes by ensuring materials are available just in time for production.
This reduces downtime and increases productivity, allowing businesses to meet customer demands more reliably.
Cost Reduction
By maintaining optimal inventory levels, MRP systems help reduce carrying costs associated with excess inventory.
This also lessens the need for emergency purchases, which can be more expensive.
Enhanced Decision-Making
With accurate data on material requirements and inventory levels, production managers can make better-informed decisions.
This improved planning capability helps prevent shortages and overproduction.
Better Customer Service
Consistent production schedules enabled by MRP help ensure timely delivery of products to customers.
This reliability enhances customer satisfaction and strengthens business relationships.
Steps to Implement an Effective MRP System
To optimize production planning using MRP, production control leaders should consider the following steps:
1. Define Clear Objectives
The first step in implementing MRP is to clearly define the objectives.
Understanding what the production control department aims to achieve, such as reducing waste or increasing production efficiency, will guide the customization of the MRP system.
2. Ensure Accurate Data Input
The effectiveness of an MRP system largely depends on the accuracy of the data inputs.
Ensure that the master production schedule, inventory status records, and bill of materials are accurate and up-to-date.
This foundation is critical for the MRP system to provide reliable outputs.
3. Train Personnel
Training is essential for personnel who will be using the MRP system.
Employees need to understand how the system works, how to input and extract data, and how to interpret the output for decision-making.
4. Monitor and Adjust
Once the MRP system is implemented, continuous monitoring is crucial to ensure it meets production objectives.
Regularly review system performance and make necessary adjustments to accommodate changes in production requirements or market conditions.
Challenges in MRP Implementation
While MRP systems offer numerous advantages, there are potential challenges that production control leaders may face.
Data Accuracy
The accuracy of MRP outputs is only as good as the inputs.
Companies may struggle with maintaining up-to-date and accurate data, which can lead to planning errors.
System Complexity
MRP systems can be complex and require significant understanding and expertise to operate effectively.
Companies may need to invest in employee training to overcome this hurdle.
Integration with Other Systems
MRP often needs to be integrated with other systems, such as ERP (Enterprise Resource Planning).
Poor integration can lead to data inconsistencies and hinder the effectiveness of the MRP system.
The Future of Production Planning with MRP
As technology advances, MRP systems are becoming more sophisticated.
These systems are now incorporating elements of Artificial Intelligence (AI) and Machine Learning (ML) to enhance predictive capabilities.
This evolution will further improve decision-making, efficiency, and responsiveness in production planning.
Moreover, the integration of cloud-based solutions allows for greater flexibility and real-time data access, making MRP tools more adaptable to changes in demand and supply chain disruptions.
As production control leaders look to the future, embracing these technological advancements can provide a competitive edge by optimizing production plans and aligning them more closely with business goals.
In summary, MRP systems are invaluable for planning production processes effectively.
A well-implemented MRP system can lead to improved efficiency, reduced costs, and enhanced customer satisfaction.
While challenges exist, they can be mitigated with careful planning, training, and the use of updated technology.
Production control leaders should prioritize understanding and utilizing MRP systems to drive success in their operations.
資料ダウンロード
QCD調達購買管理クラウド「newji」は、調達購買部門で必要なQCD管理全てを備えた、現場特化型兼クラウド型の今世紀最高の購買管理システムとなります。
ユーザー登録
調達購買業務の効率化だけでなく、システムを導入することで、コスト削減や製品・資材のステータス可視化のほか、属人化していた購買情報の共有化による内部不正防止や統制にも役立ちます。
NEWJI DX
製造業に特化したデジタルトランスフォーメーション(DX)の実現を目指す請負開発型のコンサルティングサービスです。AI、iPaaS、および先端の技術を駆使して、製造プロセスの効率化、業務効率化、チームワーク強化、コスト削減、品質向上を実現します。このサービスは、製造業の課題を深く理解し、それに対する最適なデジタルソリューションを提供することで、企業が持続的な成長とイノベーションを達成できるようサポートします。
オンライン講座
製造業、主に購買・調達部門にお勤めの方々に向けた情報を配信しております。
新任の方やベテランの方、管理職を対象とした幅広いコンテンツをご用意しております。
お問い合わせ
コストダウンが利益に直結する術だと理解していても、なかなか前に進めることができない状況。そんな時は、newjiのコストダウン自動化機能で大きく利益貢献しよう!
(Β版非公開)