- お役立ち記事
- Effective prevention of defective trouble recurrence through why-why analysis and its key points
月間76,176名の
製造業ご担当者様が閲覧しています*
*2025年3月31日現在のGoogle Analyticsのデータより
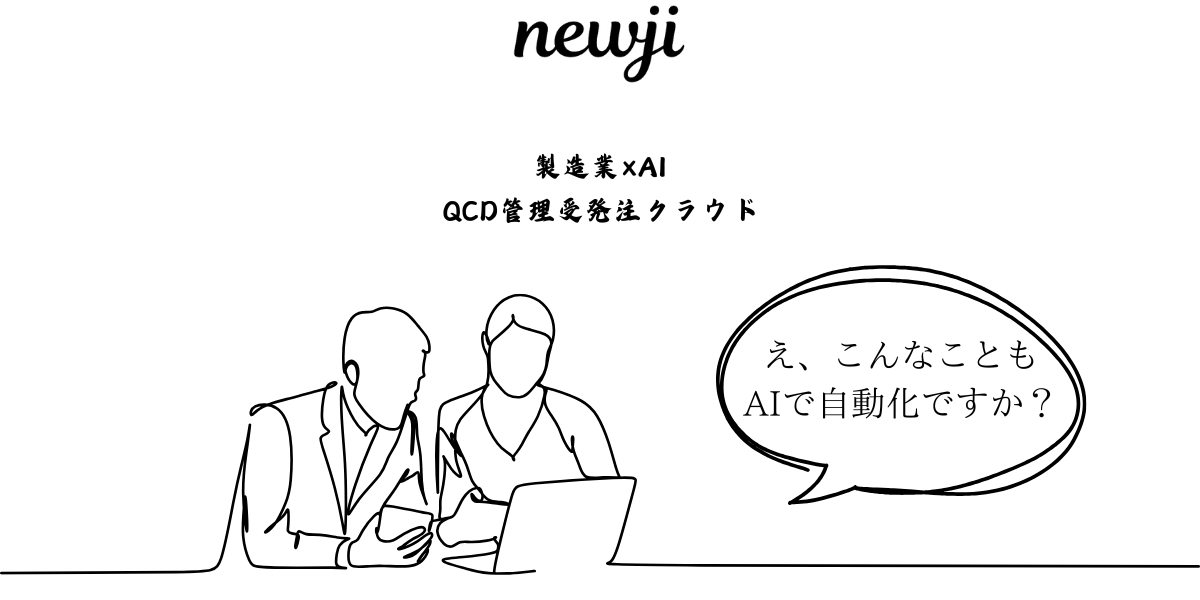
Effective prevention of defective trouble recurrence through why-why analysis and its key points
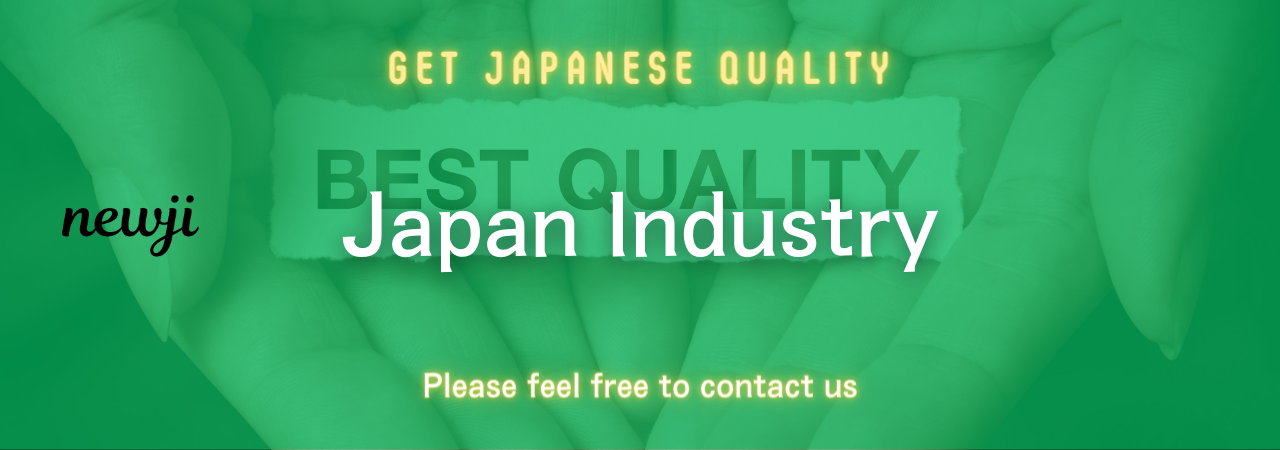
目次
Understanding Why-Why Analysis
Why-Why Analysis is an investigative technique that helps organizations identify the root cause of a defect or problem.
It involves repeatedly asking the question “Why?” to drill down into the underlying issue, rather than simply addressing superficial symptoms.
This method is valuable for uncovering the core reasons behind a problem, allowing for effective solutions and the prevention of future recurrence.
The process often involves a team tasked with exploring the problem, starting with the immediate issue and asking “why” it occurred.
The answer to each “why” leads to further investigation, forming a cascade of inquiries until reaching the fundamental cause.
This can be seen as layers of issues, starting from the apparent symptoms to reach the core problem.
The Importance of Preventing Defective Trouble Recurrence
Preventive measures play a crucial role in maintaining product quality and operational efficiency within any organization.
By identifying and addressing the underlying causes of defects, companies can avoid the recurrence of these issues, saving time, resources, and protecting their reputation.
Consistently dealing with the same problems can lead to increased costs, reduced customer satisfaction, and a loss of competitive edge.
When defective troubles recur, they not only drain resources but also highlight weaknesses in an organization’s processes.
The Why-Why Analysis is a proactive measure to eliminate these issues once and for all.
By understanding the fundamental problems, businesses can implement lasting solutions that enhance overall performance.
Steps in Conducting a Why-Why Analysis
To effectively employ Why-Why Analysis, organizations should follow a structured approach.
Step 1: Define the Problem Clearly
The first step involves clearly defining the problem.
It is essential for everyone involved in the analysis to have a shared understanding of the issue.
This can be achieved by articulating the problem statement concisely and ensuring all team members agree on it.
Step 2: Assemble a Diverse Team
Form a team of individuals from various departments and levels within the organization.
Diverse perspectives bring different insights, enriching the analysis process.
Involving a range of expertise helps ensure that all potential causes are explored.
Step 3: Begin the Why-Why Process
With the problem defined and the team assembled, begin the Why-Why analysis.
Start by asking why the problem occurred and document the answers.
For each response, continue asking “why” until the team arrives at the root cause.
This process typically takes five iterations of “why,” although the actual number may vary.
Step 4: Identify the Root Cause
Once the root cause is identified, confirm that it directly contributes to the problem.
It should be actionable and within the control of the organization to address.
Avoid focusing on symptoms or factors beyond the organization’s influence.
Step 5: Develop Actionable Solutions
With the root cause pinpointed, develop actionable strategies to address it.
These solutions should aim to eliminate the root cause and prevent recurrence.
Ensure that proposed actions are feasible and align with the organization’s resources and capabilities.
Step 6: Implement and Monitor the Solutions
Implement the selected solutions and closely monitor their effectiveness.
Track progress and adjust strategies as necessary.
Ensure that the team remains committed to continual improvement and learning from the analysis process.
Key Points for Successful Why-Why Analysis
To achieve the best results from a Why-Why Analysis, certain key points should be considered.
Involve Stakeholders and Ensure Buy-in
Securing support and involvement from key stakeholders throughout the organization is vital.
This ensures that the solutions developed have backing and can be implemented successfully.
Communicating the importance and benefits of the analysis also helps foster a culture of problem-solving and continuous improvement.
Maintain Objectivity
The analysis should be free from blame and focused on process improvement.
Encourage team members to remain impartial and solution-oriented.
Creating a safe environment where individuals can contribute without fear of reprisal is essential for honest investigation and innovation.
Document the Process
Thorough documentation of the Why-Why Analysis process is crucial.
It provides a clear record of the steps taken, the reasoning behind decisions, and proposed solutions.
This documentation serves as a valuable resource for future reference and training.
Encourage Open Communication
Fostering open communication within the team allows for the sharing of ideas and perspectives.
Encourage team members to voice their thoughts, question assumptions, and collaborate effectively.
This leads to a more comprehensive understanding of the problem and robust solutions.
Conclusion
Why-Why Analysis is a powerful tool for uncovering the root causes of defects and preventing their recurrence.
By systematically exploring the reasons behind issues, organizations can develop effective solutions that enhance their operational efficiency and quality assurance.
Employing this analysis requires a structured approach, diverse teamwork, and commitment to continuous improvement.
With these key points in mind, businesses can significantly reduce defective troubles and improve their overall performance.
資料ダウンロード
QCD管理受発注クラウド「newji」は、受発注部門で必要なQCD管理全てを備えた、現場特化型兼クラウド型の今世紀最高の受発注管理システムとなります。
ユーザー登録
受発注業務の効率化だけでなく、システムを導入することで、コスト削減や製品・資材のステータス可視化のほか、属人化していた受発注情報の共有化による内部不正防止や統制にも役立ちます。
NEWJI DX
製造業に特化したデジタルトランスフォーメーション(DX)の実現を目指す請負開発型のコンサルティングサービスです。AI、iPaaS、および先端の技術を駆使して、製造プロセスの効率化、業務効率化、チームワーク強化、コスト削減、品質向上を実現します。このサービスは、製造業の課題を深く理解し、それに対する最適なデジタルソリューションを提供することで、企業が持続的な成長とイノベーションを達成できるようサポートします。
製造業ニュース解説
製造業、主に購買・調達部門にお勤めの方々に向けた情報を配信しております。
新任の方やベテランの方、管理職を対象とした幅広いコンテンツをご用意しております。
お問い合わせ
コストダウンが利益に直結する術だと理解していても、なかなか前に進めることができない状況。そんな時は、newjiのコストダウン自動化機能で大きく利益貢献しよう!
(β版非公開)