- お役立ち記事
- Effective promotion of design review, FMEA, and DRBFM and application to prevent quality problems
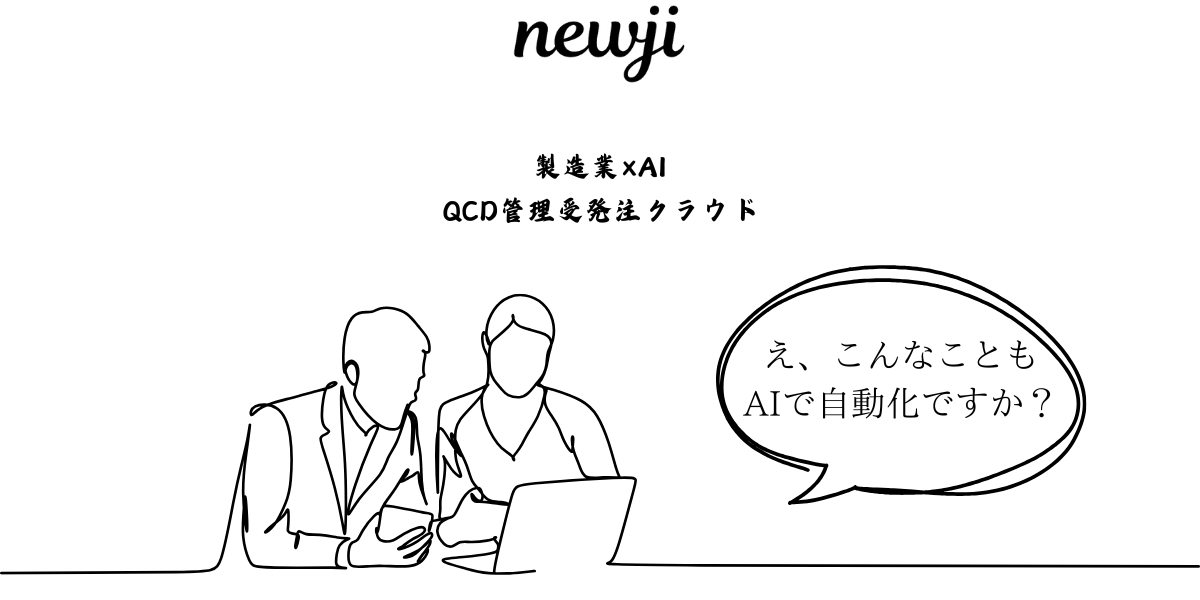
Effective promotion of design review, FMEA, and DRBFM and application to prevent quality problems
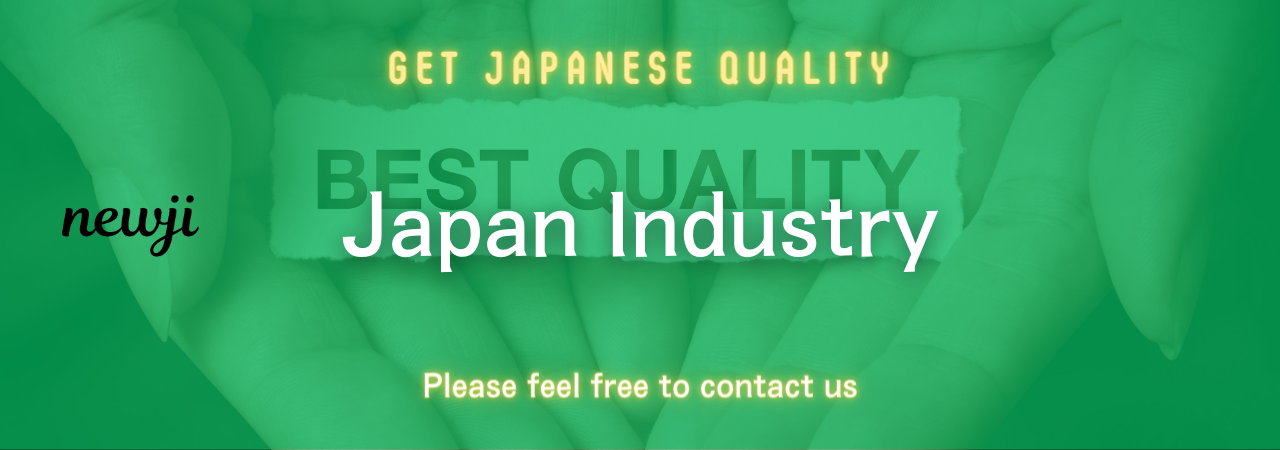
目次
Understanding Design Review, FMEA, and DRBFM
Design reviews, Failure Mode and Effects Analysis (FMEA), and Design Review Based on Failure Modes (DRBFM) are essential components in the landscape of product development and quality assurance.
Each plays a crucial role in identifying potential issues before they become significant problems, thus ensuring a high-quality product.
Design review is a systematic evaluation process where design team members and stakeholders assess the design to ensure that it meets all required standards and objectives.
FMEA is a structured approach to identifying all possible failures in a design, manufacturing process, or product.
It evaluates the potential impact of failures, their causes, and the likelihood of their occurrence.
DRBFM, on the other hand, builds on the principles of FMEA but focuses on changes made to a design.
It emphasizes understanding how even small modifications can affect overall performance and reliability.
The Importance of Design Review
Design reviews are integral to the product development lifecycle.
They provide a platform for stakeholders to discuss various design elements, ensuring adherence to user requirements, industry standards, and regulatory constraints.
Conducting effective design reviews can lead to:
– Improved product quality: Identifying and addressing potential issues early can prevent costly redesigns.
– Enhanced collaboration: Facilitating communication among cross-functional teams can lead to innovative solutions.
– Accelerated time to market: Efficient design reviews allow for quicker identification and resolution of potential roadblocks.
Implementing FMEA for Quality Assurance
FMEA is a proactive method used to anticipate potential points of failure in a design or process.
This method involves several key steps:
1. Identifying possible failure modes: Discuss all the ways a product or process might fail.
2. Evaluating the effects of each failure: Determine the impact on the user or subsequent processes.
3. Analyzing root causes: Identify why each failure might occur.
4. Assigning risk priority numbers (RPN): Evaluate failures based on severity, occurrence, and detection to prioritize which require attention.
5. Developing action plans: Create strategies to mitigate high-risk failure modes.
By systematically evaluating risks, FMEA helps teams focus on areas that need improvement or redesign.
Ultimately, this leads to products that are not only robust but also reliable under various conditions.
The Benefits of DRBFM
DRBFM expands upon the FMEA process by deeply analyzing how design changes influence product performance.
It is particularly useful when:
– Variants of existing products are being developed.
– Enhancements or updates to existing product lines are considered.
The DRBFM process involves a detailed review of the design changes to uncover potential failure modes that may arise.
The key benefits include:
– Precision in change management: Ensures that every design change undergoes a thorough risk assessment.
– Increased accountability: Encourages engineers to take responsibility for their design changes.
– Enhanced reliability: Reduces the risk of unforeseen issues after the implementation of changes.
Strategies for Effective Implementation
Successful integration of design reviews, FMEA, and DRBFM into the product development process requires careful planning and execution.
Creating a Collaborative Environment
A collaborative environment enhances the effectiveness of these methodologies.
Encourage open communication among stakeholders to freely express concerns and suggestions during reviews.
Include cross-functional team members who bring varied perspectives, from engineering to marketing, to enrich the discussion and analysis.
Establishing Clear Procedures
The efficacy of design reviews, FMEA, and DRBFM is contingent upon well-defined procedures.
Establish guidelines covering the frequency, participants, agenda, and documentation requirements for each session.
This structure ensures thoroughness and consistency across reviews.
Investing in Training
Training is vital for the successful adoption of these methodologies.
Offer regular workshops and learning sessions to ensure participants understand the principles and can utilize them efficiently.
Training should not only cover the technical aspects but also emphasize the collaborative nature of the process.
Utilizing Specialized Tools
Software tools can facilitate the FMEA and DRBFM processes.
Choose tools that offer functionalities such as risk assessment, documentation, and change management support.
These tools streamline tracking and ensure thoroughness in analyzing design nuances.
Addressing Common Challenges
Despite their benefits, implementing these strategies can present challenges.
Handling Resistance to Change
Team members may be resistant to adopting new methodologies.
To overcome this, demonstrate the benefits, such as reduced rework or improved product reliability, that come with effective design reviews, FMEA, and DRBFM.
Managing Time Constraints
These activities can be time-intensive.
Ensure that timelines account for the additional time required for comprehensive evaluations.
Adopt a phased implementation approach to gradually integrate these methodologies into existing workflows.
Ensuring Continuous Improvement
Even after integrating these methodologies, there is a need for continual assessment and improvement.
Regularly review process outcomes and feedback to refine and adapt the methodologies to the evolving needs of the organization and its products.
Conclusion
The effective promotion and application of design reviews, FMEA, and DRBFM are critical for preventing quality problems and ensuring robust product development.
By fostering a collaborative environment, establishing clear procedures, investing in training, and utilizing the right tools, organizations can mitigate risks and drive innovation.
These methodologies not only improve product quality but also enhance customer satisfaction and maintain competitive advantage in the marketplace.
資料ダウンロード
QCD調達購買管理クラウド「newji」は、調達購買部門で必要なQCD管理全てを備えた、現場特化型兼クラウド型の今世紀最高の購買管理システムとなります。
ユーザー登録
調達購買業務の効率化だけでなく、システムを導入することで、コスト削減や製品・資材のステータス可視化のほか、属人化していた購買情報の共有化による内部不正防止や統制にも役立ちます。
NEWJI DX
製造業に特化したデジタルトランスフォーメーション(DX)の実現を目指す請負開発型のコンサルティングサービスです。AI、iPaaS、および先端の技術を駆使して、製造プロセスの効率化、業務効率化、チームワーク強化、コスト削減、品質向上を実現します。このサービスは、製造業の課題を深く理解し、それに対する最適なデジタルソリューションを提供することで、企業が持続的な成長とイノベーションを達成できるようサポートします。
オンライン講座
製造業、主に購買・調達部門にお勤めの方々に向けた情報を配信しております。
新任の方やベテランの方、管理職を対象とした幅広いコンテンツをご用意しております。
お問い合わせ
コストダウンが利益に直結する術だと理解していても、なかなか前に進めることができない状況。そんな時は、newjiのコストダウン自動化機能で大きく利益貢献しよう!
(Β版非公開)