- お役立ち記事
- Effective Root Cause Analysis Techniques for Trouble Prevention
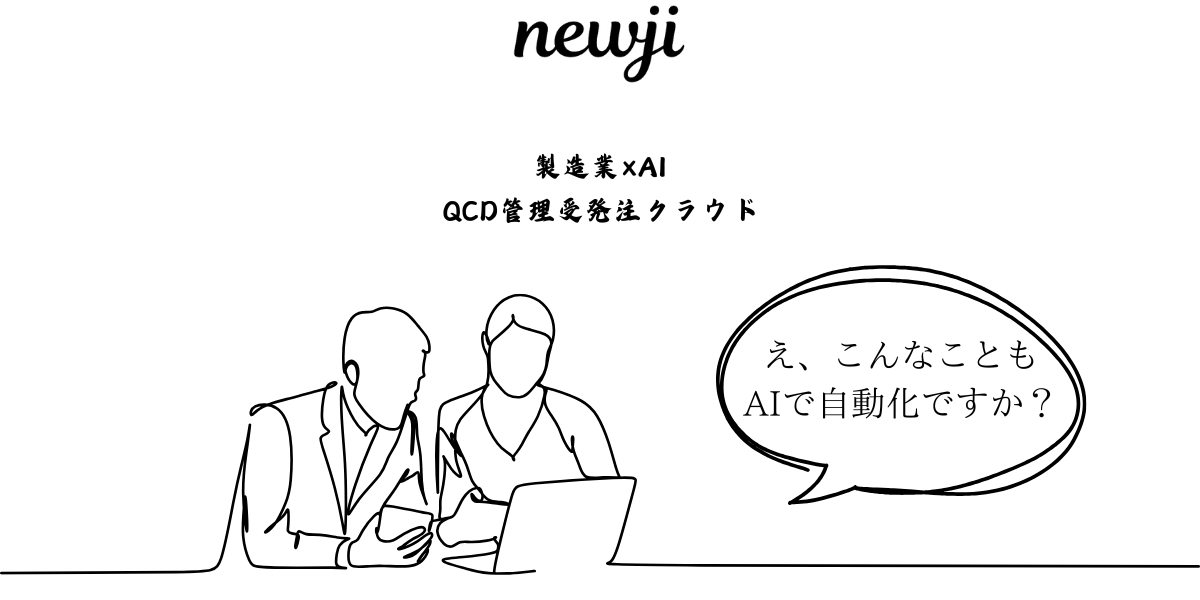
Effective Root Cause Analysis Techniques for Trouble Prevention
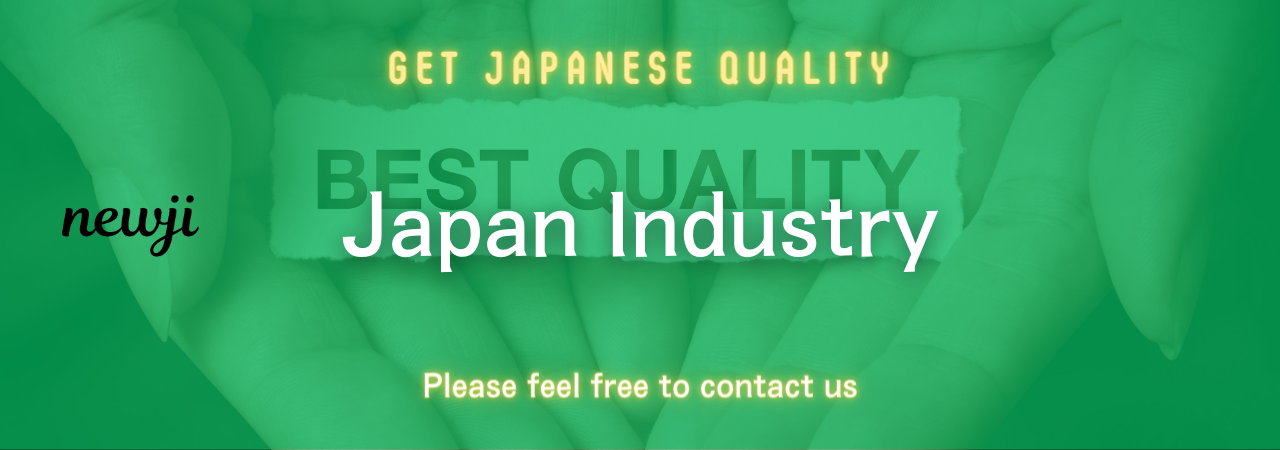
目次
Understanding Root Cause Analysis
Root cause analysis (RCA) is a critical process used to identify the underlying reasons for problems or incidents.
By understanding the root cause, organizations can implement effective solutions to prevent recurrence, rather than just addressing symptoms.
This approach is beneficial for improving processes, enhancing safety, and increasing overall productivity.
Root cause analysis is applicable across various industries, including manufacturing, healthcare, and information technology, and is a powerful tool for continuous improvement.
The Importance of Root Cause Analysis
Effective root cause analysis is vital because it helps organizations resolve issues permanently.
Instead of dealing with the same problems repeatedly, an organization can save resources by addressing the root cause.
This leads to improved efficiency, reduced downtime, and increased customer satisfaction.
Moreover, RCA fosters a proactive culture within an organization.
When employees understand the value of identifying and correcting root causes, they become more engaged in the problem-solving process.
This engagement boosts morale and encourages a positive organizational environment.
Key Steps in Root Cause Analysis
The root cause analysis process typically involves several key steps:
1. Define the Problem
Begin by precisely defining the problem.
A clear definition helps identify the scope of the issue and sets the direction for subsequent analysis.
Ensure the problem statement is specific and measurable.
2. Gather Data
Collect all relevant data related to the problem.
This includes details about what happened, when it happened, and the circumstances surrounding the incident.
Data can come from various sources such as logs, interviews, and observations.
3. Identify Possible Causes
Brainstorm potential causes of the problem.
This step involves a collaborative effort from various team members to generate a comprehensive list of possibilities.
Using techniques like fishbone diagrams or the 5 Whys can be helpful in this phase.
4. Analyze and Identify the Root Cause
With the list of potential causes, analyze each one to determine the most likely root cause.
This analysis may involve conducting tests or simulations to confirm the cause.
The aim is to identify the most fundamental issue that leads to the problem.
5. Develop and Implement Solutions
Once the root cause is identified, develop solutions aimed at preventing recurrence.
The solutions should be realistic, actionable, and sustainable.
After devising the solutions, implement them and communicate the changes throughout the organization.
6. Monitor and Review
After implementing solutions, monitor their effectiveness.
This involves tracking the progress and making adjustments if necessary.
Regular reviews ensure that the solutions remain effective over time and adapt to any changes in the environment.
Techniques for Effective Root Cause Analysis
There are several techniques used to conduct an effective root cause analysis:
Fishbone Diagram
Also known as the Ishikawa or cause-and-effect diagram, the fishbone diagram helps visualize the potential causes of a problem.
It categorizes causes into major groups and provides a systematic way to explore all possible causes.
The 5 Whys
This technique involves asking “why” multiple times until the root cause is found.
By repeatedly questioning why something happened, you delve deeper into the layers of the problem, eventually uncovering the root cause.
Failure Mode and Effects Analysis (FMEA)
FMEA is a systematic method for evaluating processes to identify where and how they might fail and assessing the impact of different failures.
It helps prioritize potential causes based on their risks and effects.
Fault Tree Analysis (FTA)
Fault tree analysis is a top-down, deductive approach to identifying possible causes of system failures.
It involves tracing the hierarchy of faults and their relationships to one another to determine the root cause.
Challenges in Root Cause Analysis
Root cause analysis can be challenging for several reasons.
Data Quality
Quality data is crucial for a successful RCA.
Poor or incomplete data can lead to incorrect conclusions, making it difficult to identify the true root cause.
Complex Systems
In complex systems, multiple factors may contribute to a problem, complicating the analysis.
It may be difficult to isolate a single root cause due to the interconnected nature of modern organizational processes.
Human Error
Human factors often play a role in problems, and addressing them can be sensitive.
It requires a culture of transparency and non-punitive reporting to ensure staff are comfortable participating in RCAs.
Resistance to Change
Implementing solutions may encounter resistance within the organization.
Change can be difficult, and ensuring buy-in from stakeholders is essential for successful implementation.
Conclusion
Effective root cause analysis techniques are essential for trouble prevention in any organization.
By identifying and addressing the fundamental causes of issues, organizations can prevent recurrence, save resources, and promote a culture of continuous improvement.
While challenges exist, using systematic methods like fishbone diagrams, the 5 Whys, FMEA, and FTA can enhance the analysis process.
Ultimately, a commitment to thorough analysis and proactive problem-solving will make a significant difference in organizational success.
資料ダウンロード
QCD調達購買管理クラウド「newji」は、調達購買部門で必要なQCD管理全てを備えた、現場特化型兼クラウド型の今世紀最高の購買管理システムとなります。
ユーザー登録
調達購買業務の効率化だけでなく、システムを導入することで、コスト削減や製品・資材のステータス可視化のほか、属人化していた購買情報の共有化による内部不正防止や統制にも役立ちます。
NEWJI DX
製造業に特化したデジタルトランスフォーメーション(DX)の実現を目指す請負開発型のコンサルティングサービスです。AI、iPaaS、および先端の技術を駆使して、製造プロセスの効率化、業務効率化、チームワーク強化、コスト削減、品質向上を実現します。このサービスは、製造業の課題を深く理解し、それに対する最適なデジタルソリューションを提供することで、企業が持続的な成長とイノベーションを達成できるようサポートします。
オンライン講座
製造業、主に購買・調達部門にお勤めの方々に向けた情報を配信しております。
新任の方やベテランの方、管理職を対象とした幅広いコンテンツをご用意しております。
お問い合わせ
コストダウンが利益に直結する術だと理解していても、なかなか前に進めることができない状況。そんな時は、newjiのコストダウン自動化機能で大きく利益貢献しよう!
(Β版非公開)