- お役立ち記事
- Effective use of DLC technology and the latest technology to achieve ultra-low friction
Effective use of DLC technology and the latest technology to achieve ultra-low friction
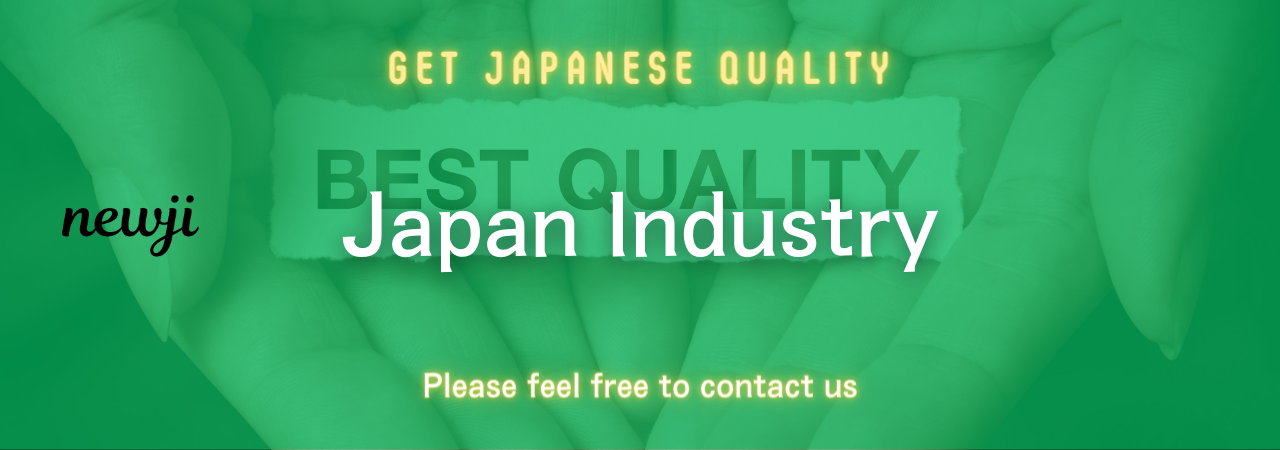
目次
Understanding DLC Technology
Diamond-Like Carbon (DLC) technology has been a groundbreaking advancement in material science.
It refers to a class of amorphous carbon material that displays some of the typical properties of diamond, such as hardness and slickness.
DLC coatings are used extensively in the industry to reduce friction, wear, and extend the lifespan of components.
The ultra-low friction qualities are particularly beneficial in mechanical systems where minimizing energy loss and wear is crucial.
DLC coatings can significantly reduce friction due to their unique surface properties.
They provide a hard, slick surface that minimizes contact resistance.
This makes them perfect for applications where longevity and reliability are paramount.
For instance, DLC coatings are often used in the automotive and aerospace industries to enhance the performance and durability of engine components and moving parts.
The Role of Friction in Various Industries
Friction is a force that opposes motion, and it plays a pivotal role in various industrial applications.
In machinery, friction leads to wear and energy loss, which can impact operational efficiency and increase maintenance costs.
In contrast, reducing friction can enhance performance, reduce the frequency of maintenance, and extend the lifespan of machinery components.
In industries like automotive, reduced friction can contribute to more efficient fuel consumption.
In electronics, reduced friction leads to better performance and longer-lasting devices due to less wear and tear on moving parts.
Thus, the effective use of DLC technology is essential across various sectors aiming for ultra-low friction.
Latest Technological Advancements Complementing DLC
Recent advancements in technology have bolstered the applications and effectiveness of DLC coatings.
One of the latest technologies includes advancements in coating deposition methods.
Traditional methods like Physical Vapor Deposition (PVD) and Chemical Vapor Deposition (CVD) have been refined to improve the uniformity and adhesion of DLC layers, resulting in more durable coatings.
Additionally, researchers are exploring the use of nanocomposites to further enhance the lubricious properties of DLC coatings.
By incorporating nanoparticles, the coatings’ structural integrity and friction-reducing properties are increased, opening up new applications for DLC technology.
Another exciting development is the use of machine learning and AI algorithms to optimize the DLC coating process.
These technologies are leveraged to predict the behavior of different materials and deposition conditions, allowing for more efficient production and higher-quality coatings.
The Importance of Surface Finish and Texture
The surface finish and texture of a material play a significant role in its frictional characteristics.
Advancements in surface engineering have provided new ways to modify the finish and texture of DLC-coated surfaces, further enhancing their friction-reducing properties.
Micro-texturing of DLC surfaces can lead to a significant reduction in friction.
This involves creating tiny patterns or grooves on the surface, which can trap lubricants and reduce the contact area.
The combination of DLC coatings and optimized surface texturing proves to be highly effective in applications demanding ultra-low friction.
Applications Benefiting from Ultra-Low Friction
The impact of ultra-low friction through DLC technology is transformative across many fields.
In the automotive industry, reducing friction in engines and transmissions can improve fuel efficiency and reduce emissions.
This not only lowers the carbon footprint but also meets stringent government regulations and customer expectations for environmentally friendly vehicles.
In the medical field, DLC coatings on surgical instruments and implants can significantly increase their lifespan and reliability.
Reduced friction in medical devices ensures smoother operation and less wear over time, contributing to better patient outcomes.
The aerospace industry benefits greatly from ultra-low friction technologies.
DLC-coated parts in aircraft engines and other mechanical systems help reduce wear and the risk of mechanical failure, which is crucial for safety and efficiency in aviation.
Challenges and Future of DLC Technology
Despite its advantages, DLC technology faces challenges that need addressing.
One of the main issues is the high cost of deposition and fabrication processes.
Researchers are constantly working to develop more cost-effective methods to make DLC coatings feasible for a broader range of applications.
Another challenge is the adherence of DLC coatings to certain substrates.
Improving adhesion while maintaining the material’s ultra-low friction quality is an ongoing research area.
Looking ahead, the future of DLC technology appears promising.
With continued research and technological advancements, the cost and scalability issues can be overcome.
As a result, the application of DLC coatings is expected to proliferate across industries, providing sustainable solutions for friction reduction.
Conclusion
The effective utilization of DLC technology, combined with cutting-edge advancements, allows for achieving ultra-low friction in various applications.
From automotive and aerospace to medical devices, the impact of reduced friction is evident in enhanced performance, increased efficiency, and longer component life.
As technology progresses, the promise of DLC technology continues to unfold, offering even greater potential for improving industrial applications.
With ongoing research and development, the future of DLC will likely bring innovative solutions to reduce friction even further, benefiting industries worldwide.
資料ダウンロード
QCD調達購買管理クラウド「newji」は、調達購買部門で必要なQCD管理全てを備えた、現場特化型兼クラウド型の今世紀最高の購買管理システムとなります。
ユーザー登録
調達購買業務の効率化だけでなく、システムを導入することで、コスト削減や製品・資材のステータス可視化のほか、属人化していた購買情報の共有化による内部不正防止や統制にも役立ちます。
NEWJI DX
製造業に特化したデジタルトランスフォーメーション(DX)の実現を目指す請負開発型のコンサルティングサービスです。AI、iPaaS、および先端の技術を駆使して、製造プロセスの効率化、業務効率化、チームワーク強化、コスト削減、品質向上を実現します。このサービスは、製造業の課題を深く理解し、それに対する最適なデジタルソリューションを提供することで、企業が持続的な成長とイノベーションを達成できるようサポートします。
オンライン講座
製造業、主に購買・調達部門にお勤めの方々に向けた情報を配信しております。
新任の方やベテランの方、管理職を対象とした幅広いコンテンツをご用意しております。
お問い合わせ
コストダウンが利益に直結する術だと理解していても、なかなか前に進めることができない状況。そんな時は、newjiのコストダウン自動化機能で大きく利益貢献しよう!
(Β版非公開)