- お役立ち記事
- Effective Use of FMEA and DR for Preventive Activities
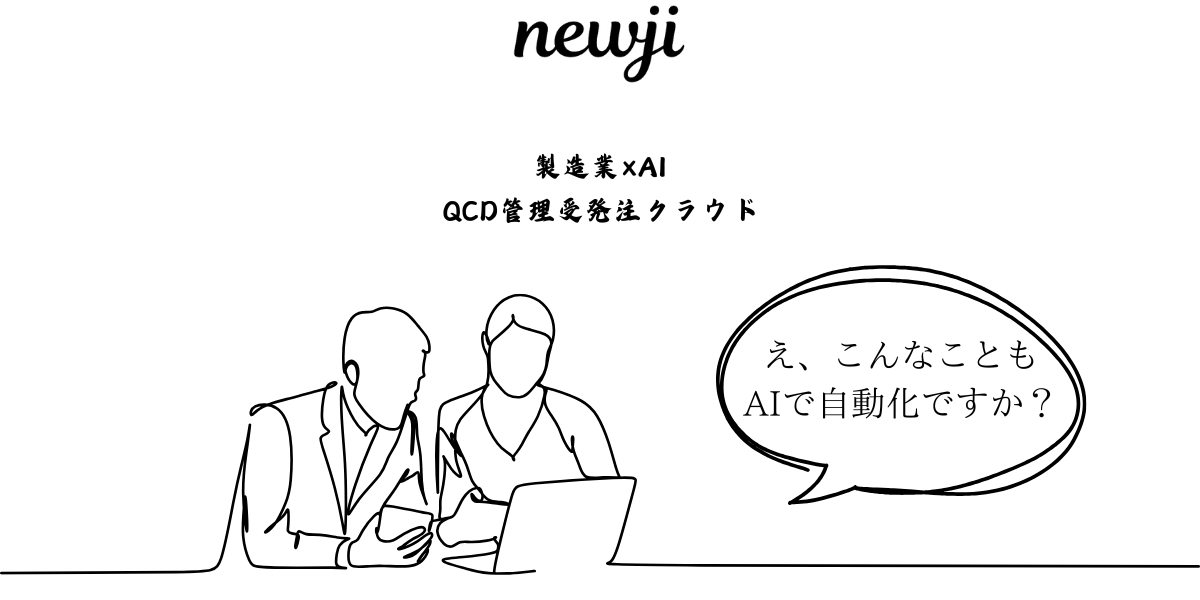
Effective Use of FMEA and DR for Preventive Activities
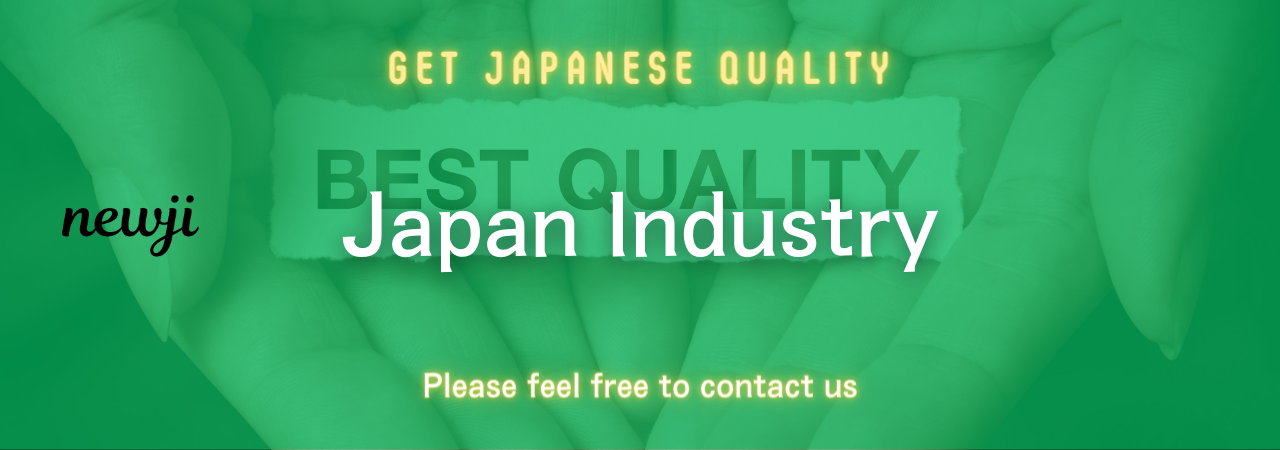
Failure Modes and Effects Analysis (FMEA) and Design Review (DR) are both essential tools in ensuring that products and processes meet safety and quality standards.
By using these practices effectively, you can prevent potential issues that could arise during the development and production phases.
This collaborative and structured approach helps in identifying potential risks, enhancing reliability, and improving customer satisfaction.
目次
Understanding FMEA
Failure Modes and Effects Analysis (FMEA) is a systematic method for evaluating processes to identify where and how they might fail.
It assesses the relative impact of these failures to prioritize the needed actions to reduce them.
Types of FMEA
There are several types of FMEA:
* Design FMEA (DFMEA) focuses on potential failures in product design.
* Process FMEA (PFMEA) centers on potential failures in manufacturing and assembly processes.
* System FMEA considers potential failures within the larger system environment, including interactions between subsystems.
Each type plays a crucial role in assessing different aspects of your product and system comprehensively.
Steps in FMEA
The FMEA process typically involves the following steps: defining the system, identifying potential failure modes, determining the effects of these failures, establishing the cause, and evaluating the risks associated with the failures.
You then prioritize the risks based on their severity, occurrence, and detectability.
This prioritization helps in deciding which risks need immediate attention and which can be monitored over time.
Benefits of FMEA
Using FMEA can provide several benefits:
* It enhances product reliability and quality by foreseeing potential problems.
* It helps improve customer satisfaction by reducing failures.
* It aids in regulatory compliance by proactively identifying and addressing risks.
* It strengthens communication and collaboration within teams by involving members from different disciplines in identifying and solving potential issues.
Understanding Design Review (DR)
Design Review (DR) is another crucial activity in product development and quality assurance.
It is a formal, documented review of a design conducted at various stages to ensure the product meets its requirements and specifications.
Key Phases of Design Review
Design Reviews are usually conducted in three major phases:
* Preliminary Design Review (PDR) – This phase verifies that the initial design meets the necessary requirements and sets a path for the detailed design phase.
* Critical Design Review (CDR) – This phase ensures that the design meets all system requirements with an acceptable level of risk and that the product’s performance, cost, and schedule commitments can be met.
* Final Design Review (FDR) – This phase validates the final design, ensuring that it meets the requirements and is ready for production.
Steps in Design Review
The steps in conducting a DR typically include preparation, review, and follow-up.
During the preparation stage, the team gathers all necessary documents and data.
The review phase involves a structured meeting where the design is evaluated against criteria, and feedback is documented.
Follow-up ensures that any issues identified during the review are addressed.
Benefits of Design Review
Implementing regular Design Reviews brings several benefits:
* It helps identify and rectify issues early, reducing costly rework.
* It ensures that the design meets all specified requirements, improving product quality.
* It enhances team communication and alignment.
* It facilitates better decision-making through documented feedback and recommendations.
Integrating FMEA and Design Review for Preventive Activities
To maximize the benefits of both FMEA and DR, it is essential to integrate these processes effectively.
Here are some strategies for combining these activities to enhance preventive measures:
Concurrent Application
Applying FMEA and DR concurrently can provide a comprehensive view of potential issues.
While FMEA identifies potential failures and their effects, DR ensures that the design meets the necessary standards and requirements.
Working together, they provide a robust framework for identifying, evaluating, and addressing risks.
Cross-Disciplinary Teams
Involving cross-disciplinary teams in both FMEA and DR processes ensures that different perspectives are considered.
Team members from engineering, quality assurance, manufacturing, and supply chain can offer unique insights, leading to more thorough evaluation and comprehensive solutions.
Continuous Improvement
Both FMEA and DR should be viewed as ongoing processes rather than one-time activities.
Regular updates and reviews help in continuously identifying and addressing new risks as the product and process evolve.
This proactive approach fosters an environment of continuous improvement and risk management.
Documentation and Follow-Up
Documentation plays a crucial role in both FMEA and DR.
Maintaining detailed records of identified risks, mitigation actions, and review feedbacks ensures that all actions are tracked and implemented.
Regular follow-up on these actions ensures that risks are adequately managed and mitigated.
Training and Awareness
Providing training on FMEA and DR processes to all relevant team members ensures that everyone understands their importance and knows how to apply them effectively.
Raising awareness about the benefits of these methods fosters a culture of proactive risk management and quality improvement.
Conclusion
The effective use of Failure Modes and Effects Analysis (FMEA) and Design Review (DR) plays a critical role in identifying and resolving potential issues in product design and development.
By integrating these processes, you can proactively manage risks, enhance product quality, and achieve higher customer satisfaction.
Encouraging a culture of continuous improvement and cross-disciplinary collaboration ensures that these preventive activities are successfully implemented, leading to better outcomes for your projects and products.
資料ダウンロード
QCD調達購買管理クラウド「newji」は、調達購買部門で必要なQCD管理全てを備えた、現場特化型兼クラウド型の今世紀最高の購買管理システムとなります。
ユーザー登録
調達購買業務の効率化だけでなく、システムを導入することで、コスト削減や製品・資材のステータス可視化のほか、属人化していた購買情報の共有化による内部不正防止や統制にも役立ちます。
NEWJI DX
製造業に特化したデジタルトランスフォーメーション(DX)の実現を目指す請負開発型のコンサルティングサービスです。AI、iPaaS、および先端の技術を駆使して、製造プロセスの効率化、業務効率化、チームワーク強化、コスト削減、品質向上を実現します。このサービスは、製造業の課題を深く理解し、それに対する最適なデジタルソリューションを提供することで、企業が持続的な成長とイノベーションを達成できるようサポートします。
オンライン講座
製造業、主に購買・調達部門にお勤めの方々に向けた情報を配信しております。
新任の方やベテランの方、管理職を対象とした幅広いコンテンツをご用意しております。
お問い合わせ
コストダウンが利益に直結する術だと理解していても、なかなか前に進めることができない状況。そんな時は、newjiのコストダウン自動化機能で大きく利益貢献しよう!
(Β版非公開)