- お役立ち記事
- Effective use of QFD, DRBFM, and design verification and application to prevent design defects
月間76,176名の
製造業ご担当者様が閲覧しています*
*2025年3月31日現在のGoogle Analyticsのデータより
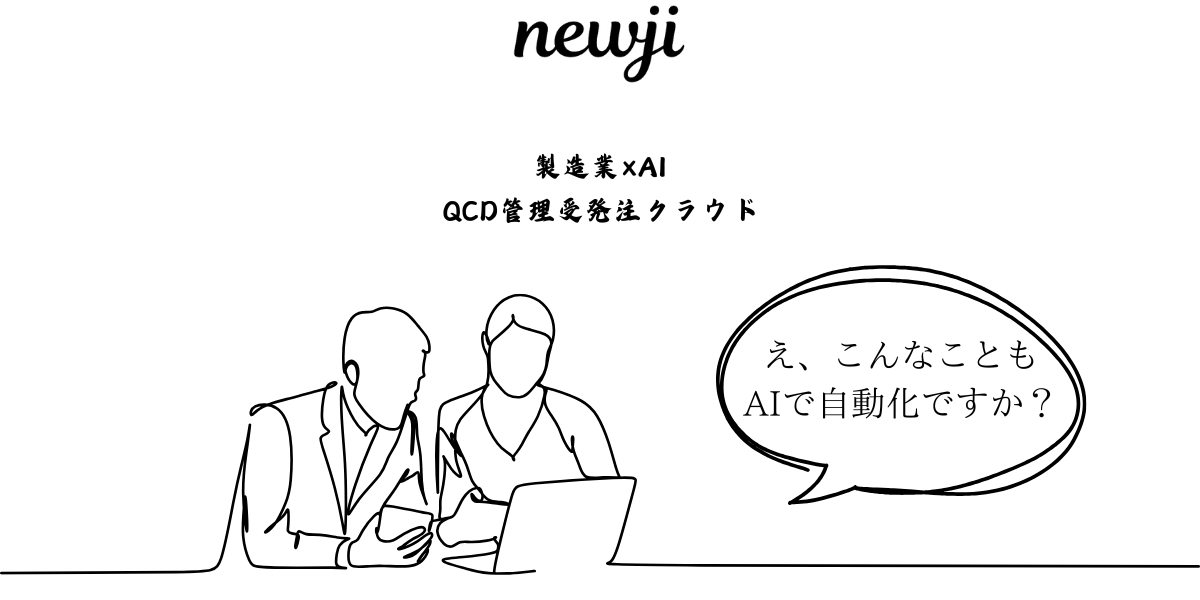
Effective use of QFD, DRBFM, and design verification and application to prevent design defects
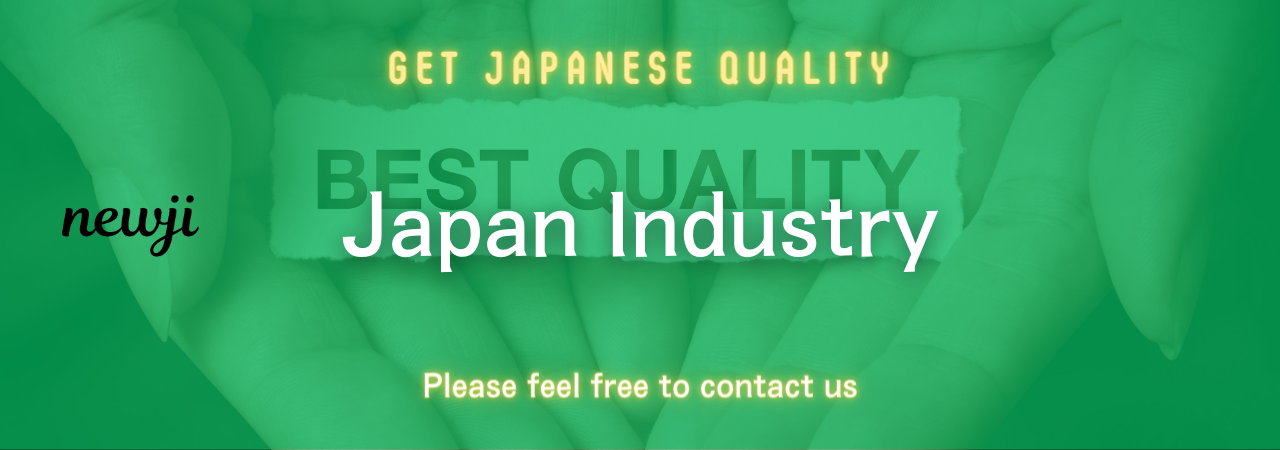
目次
Understanding QFD: Quality Function Deployment
Quality Function Deployment (QFD) is a structured method that is instrumental in transforming user requirements into detailed design specifications.
This systematic approach ensures that the voice of the customer is integrated into every aspect of product development.
By utilizing QFD, companies can ensure they are meeting customer needs effectively, thus minimizing the potential for design defects.
QFD begins with identifying customer demands and translating them into engineering attributes.
This process involves developing a House of Quality matrix, which helps in prioritizing customer needs based on their impact on product features.
By using QFD, designers and engineers can establish a clear linkage between what customers want and how the design will fulfill those needs.
One of the primary advantages of QFD is its ability to improve communication among all stakeholders involved in the design process.
By creating a detailed blueprint of customer requirements, everyone from marketing teams to engineers can stay aligned on the project goals.
This cohesive approach helps in reducing discrepancies that might arise during the design phase.
The Role of DRBFM: Design Review Based on Failure Mode
Design Review Based on Failure Mode (DRBFM) is another crucial tool used to prevent design defects.
DRBFM focuses on the identification and examination of potential failure modes in a design.
By analyzing these failure modes, the process helps in ensuring that potential issues are addressed before they become actual defects.
The DRBFM process begins with a detailed review of design changes and their implications.
This involves scrutinizing every aspect of the design to predict and prevent failures.
The approach encourages designers to question the design thoroughly, focusing on the details that might lead to potential problems.
One of the key benefits of DRBFM is its ability to drive continuous improvement in the design process.
By fostering a culture of questioning and detailed examination, DRBFM helps teams to innovate and refine their designs continuously.
This proactive stance plays a significant role in preventing defects and ensuring a high level of product reliability.
Design Verification: Ensuring Design Integrity
Design Verification is a critical step in the design process, ensuring that the end product meets all specified requirements.
It involves a series of tests and evaluations to confirm that the design functions as intended under specified conditions.
By identifying discrepancies between expected outcomes and real-world performance, design verification helps in rectifying issues before mass production.
The design verification process typically involves several stages, including prototype testing, simulation, and validation.
Each stage is designed to ensure that the design meets quality standards and is free from defects.
The completion of these stages provides confidence that the product will perform reliably once it reaches the market.
Effective design verification requires collaboration between different teams, including design, engineering, and quality assurance.
By working together, these teams can ensure that the product meets customer expectations and complies with regulatory requirements.
Through comprehensive testing, design verification provides assurance that the product will function safely and effectively.
Integrating QFD, DRBFM, and Design Verification
Integrating QFD, DRBFM, and design verification processes can significantly enhance the prevention of design defects.
Each of these methodologies offers unique strengths that, when combined, create a robust framework for ensuring product quality.
QFD sets the foundation by translating customer requirements into actionable design considerations.
DRBFM builds on this by identifying potential failure modes and encouraging thorough examination of the design.
Finally, design verification ensures that the design meets all specified requirements, confirming its reliability before full-scale production.
By employing a holistic approach that combines these methodologies, companies can streamline the design process and enhance product quality.
This integration not only reduces the likelihood of defects but also fosters innovation and encourages a proactive approach to design challenges.
Practical Application to Prevent Design Defects
To effectively apply these methodologies, businesses should create a structured plan that aligns QFD, DRBFM, and design verification with their overall design processes.
Here are some practical steps to ensure successful implementation:
1. Cross-functional Collaboration
Engage teams from diverse backgrounds such as engineering, marketing, and customer service.
This collaboration ensures that customer needs are accurately captured and addressed throughout the design process.
2. Develop a Comprehensive Roadmap
Outline a clear roadmap that incorporates QFD, DRBFM, and design verification at different stages of the design lifecycle.
This roadmap should specify roles, responsibilities, and timelines for each phase.
3. Foster a Culture of Continuous Improvement
Encourage teams to adopt a mindset geared towards continuous improvement.
Regularly review processes and outcomes to identify areas for enhancement and innovation.
4. Embrace Feedback and Adaptation
Collect feedback from all stakeholders, including customers, during and after the design phase.
Use this feedback to make necessary adjustments and improvements to the design.
By effectively integrating these methodologies, companies can not only prevent design defects but also deliver high-quality, reliable products that meet customer expectations.
This comprehensive approach ensures that products are designed with precision and attention to detail, leading to enhanced satisfaction and market success.
資料ダウンロード
QCD管理受発注クラウド「newji」は、受発注部門で必要なQCD管理全てを備えた、現場特化型兼クラウド型の今世紀最高の受発注管理システムとなります。
ユーザー登録
受発注業務の効率化だけでなく、システムを導入することで、コスト削減や製品・資材のステータス可視化のほか、属人化していた受発注情報の共有化による内部不正防止や統制にも役立ちます。
NEWJI DX
製造業に特化したデジタルトランスフォーメーション(DX)の実現を目指す請負開発型のコンサルティングサービスです。AI、iPaaS、および先端の技術を駆使して、製造プロセスの効率化、業務効率化、チームワーク強化、コスト削減、品質向上を実現します。このサービスは、製造業の課題を深く理解し、それに対する最適なデジタルソリューションを提供することで、企業が持続的な成長とイノベーションを達成できるようサポートします。
製造業ニュース解説
製造業、主に購買・調達部門にお勤めの方々に向けた情報を配信しております。
新任の方やベテランの方、管理職を対象とした幅広いコンテンツをご用意しております。
お問い合わせ
コストダウンが利益に直結する術だと理解していても、なかなか前に進めることができない状況。そんな時は、newjiのコストダウン自動化機能で大きく利益貢献しよう!
(β版非公開)