- お役立ち記事
- Effective use of quality function deployment (QFD) and efficient application of FMEA/DRBFM to prevent quality problems
月間76,176名の
製造業ご担当者様が閲覧しています*
*2025年3月31日現在のGoogle Analyticsのデータより
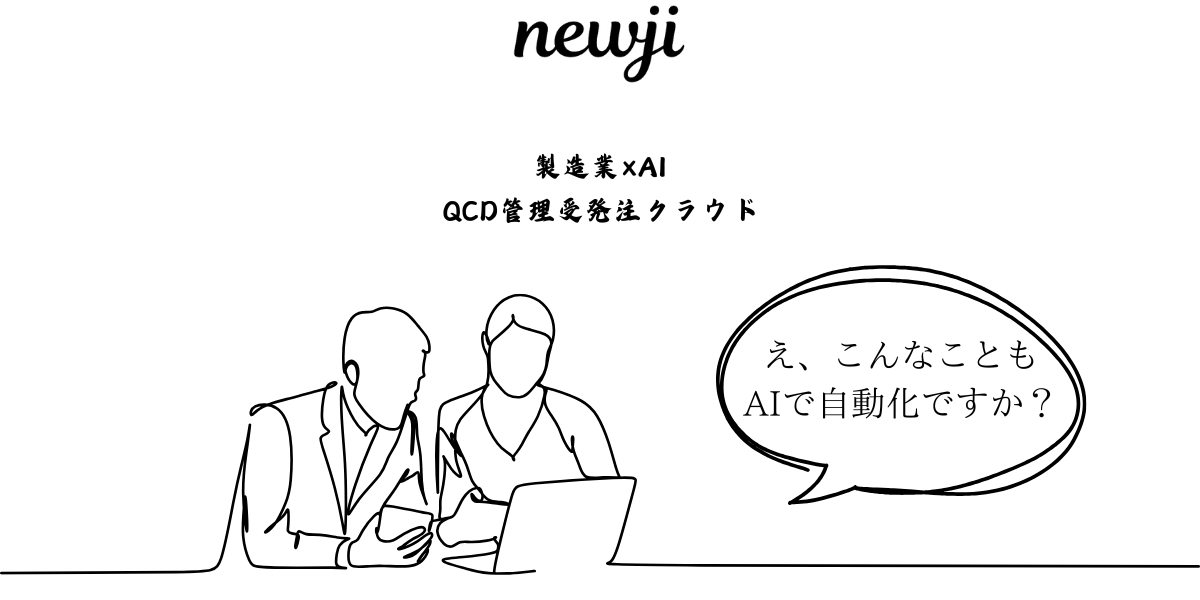
Effective use of quality function deployment (QFD) and efficient application of FMEA/DRBFM to prevent quality problems
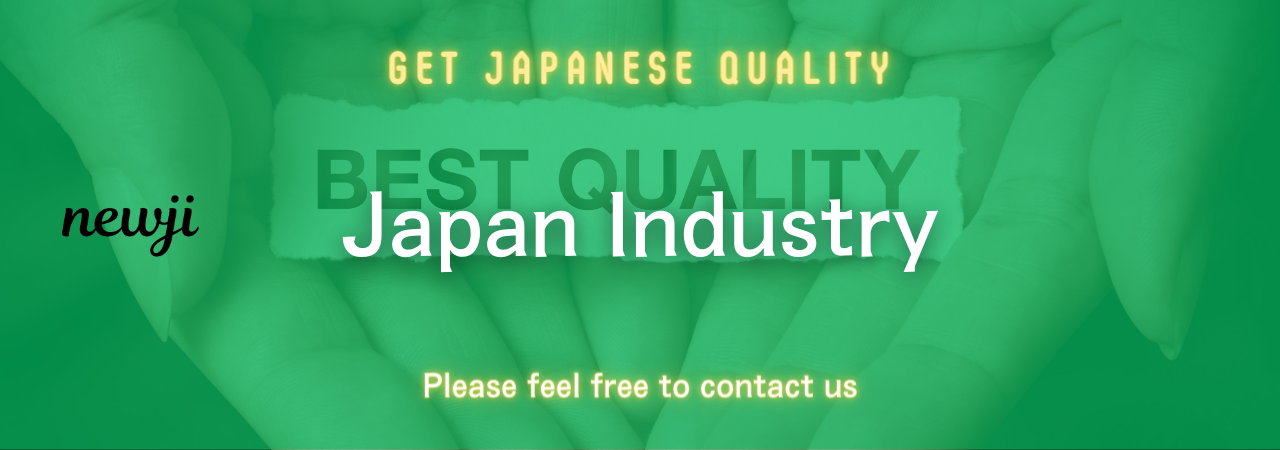
目次
Understanding Quality Function Deployment (QFD)
Quality Function Deployment (QFD) is a structured approach used by businesses to transform customer needs into specific engineering requirements and measurable performance criteria.
Originating from the manufacturing sector, particularly in the automotive industry, QFD has now found applications in various fields due to its effectiveness.
The main objective of QFD is to ensure that the final product or service aligns closely with customer expectations.
By linking the voice of the customer with design, production, and service processes, organizations can significantly improve quality outcomes.
The Four Phases of QFD
QFD is typically divided into four distinct phases:
**Phase 1: Product Planning**
In the product planning phase, customer needs and desires are identified and translated into product characteristics.
This initial phase is often visualized in a tool called the House of Quality, a matrix that helps teams focus on customer priorities and benchmark against competitors.
**Phase 2: Product Design**
The product design phase takes the output from product planning and turns it into specific product components.
During this phase, engineers and designers work together to translate product characteristics into concrete specifications.
**Phase 3: Process Planning**
Process planning involves determining how to manufacture the product in the most efficient way possible while maintaining quality.
Detailed charts and procedures are developed to ensure that each component is produced to specification.
**Phase 4: Process Control**
In this final phase, focus shifts to quality assurance and control, ensuring that the manufacturing process consistently produces products that meet quality standards.
This may involve statistical process control, testing, and validation procedures.
The Benefits of Implementing QFD
When implemented effectively, QFD offers several benefits.
It enhances communication across various departments, ensuring everyone is aligned with the customer’s requirements.
QFD can also reduce development time and costs by preventing costly redesigns and modifications.
Additionally, focusing on customer satisfaction from the onset can significantly increase customer loyalty and market success.
An Introduction to Failure Mode and Effect Analysis (FMEA)
Failure Mode and Effect Analysis (FMEA) is a systematic method for identifying potential failure modes within a process, product, or system and finding ways to mitigate or eliminate risks associated with these failures.
This tool is crucial in developing a proactive approach to risk management.
Types of FMEA
**Design FMEA (DFMEA)**
DFMEA focuses on potential failure modes within the product’s design, assessing whether all potential failures have been addressed before production.
This type of FMEA aims to enhance product reliability and design robustness.
**Process FMEA (PFMEA)**
PFMEA, on the other hand, targets potential failures in the manufacturing and assembly processes.
It aims to identify issues that could cause product defects, thereby ensuring smooth production and high-quality output.
The Role of Design Review Based on Failure Mode (DRBFM)
Design Review Based on Failure Mode (DRBFM) is an extension of FMEA that emphasizes the importance of reviewing design changes and their potential impact on product performance.
Whereas FMEA might focus broadly on failure modes, DRBFM zooms in on changes and evaluates how they could introduce new failure modes.
The DRBFM process includes structured reviews with multidisciplinary teams to scrutinize every aspect of the change.
Efficiency of Using FMEA/DRBFM
By integrating FMEA/DRBFM into the design and manufacturing stages, companies can anticipate and mitigate risks more effectively.
These tools help ensure that potential problems are identified early, reducing failures and downtime after product launch.
Furthermore, they facilitate continuous improvement by fostering a culture of proactive problem-solving and quality enhancement.
Combining QFD with FMEA/DRBFM for Optimal Results
Using QFD alongside FMEA and DRBFM provides a comprehensive framework for quality management and improvement.
QFD ensures that customer needs drive product development, while FMEA and DRBFM provide robust risk management and quality assurance throughout the process.
Steps to Combine QFD with FMEA/DRBFM
1. **Start with Customer Requirements**
Use QFD to capture detailed customer requirements and ensure these guide every stage of product development.
2. **Implement FMEA Early**
Apply FMEA during the design and process phases to identify potential failure modes and devise mitigation strategies.
This proactive approach is crucial to reducing potential risks.
3. **Incorporate DRBFM for Changes**
When design changes occur, utilize DRBFM to evaluate their impact on the product.
This prevents the introduction of new risks and maintains product quality.
Challenges and Best Practices
Integrating these methodologies requires commitment across the organization.
A common challenge is ensuring clear communication between departments, as well as maintaining focus on the customer’s voice throughout the development process.
For best results, organizations should provide adequate training to all relevant teams and encourage a culture of quality and continuous improvement.
Additionally, leveraging software tools designed for QFD and FMEA can streamline processes and enhance collaboration.
By doing so, companies can maximize the benefits of these methodologies, leading to superior quality products and satisfied customers.
In conclusion, the effective use of QFD and efficient application of FMEA/DRBFM are vital strategies in preventing quality problems, enhancing product reliability, and achieving customer satisfaction.
Their integration into the product and process development cycles can drive significant improvements in both performance and market competitiveness.
資料ダウンロード
QCD管理受発注クラウド「newji」は、受発注部門で必要なQCD管理全てを備えた、現場特化型兼クラウド型の今世紀最高の受発注管理システムとなります。
ユーザー登録
受発注業務の効率化だけでなく、システムを導入することで、コスト削減や製品・資材のステータス可視化のほか、属人化していた受発注情報の共有化による内部不正防止や統制にも役立ちます。
NEWJI DX
製造業に特化したデジタルトランスフォーメーション(DX)の実現を目指す請負開発型のコンサルティングサービスです。AI、iPaaS、および先端の技術を駆使して、製造プロセスの効率化、業務効率化、チームワーク強化、コスト削減、品質向上を実現します。このサービスは、製造業の課題を深く理解し、それに対する最適なデジタルソリューションを提供することで、企業が持続的な成長とイノベーションを達成できるようサポートします。
製造業ニュース解説
製造業、主に購買・調達部門にお勤めの方々に向けた情報を配信しております。
新任の方やベテランの方、管理職を対象とした幅広いコンテンツをご用意しております。
お問い合わせ
コストダウンが利益に直結する術だと理解していても、なかなか前に進めることができない状況。そんな時は、newjiのコストダウン自動化機能で大きく利益貢献しよう!
(β版非公開)