- お役立ち記事
- Effective use of resin flow analysis technology and countermeasures against defects and troubles for high-precision, high-quality plastic molded products
月間77,185名の
製造業ご担当者様が閲覧しています*
*2025年2月28日現在のGoogle Analyticsのデータより
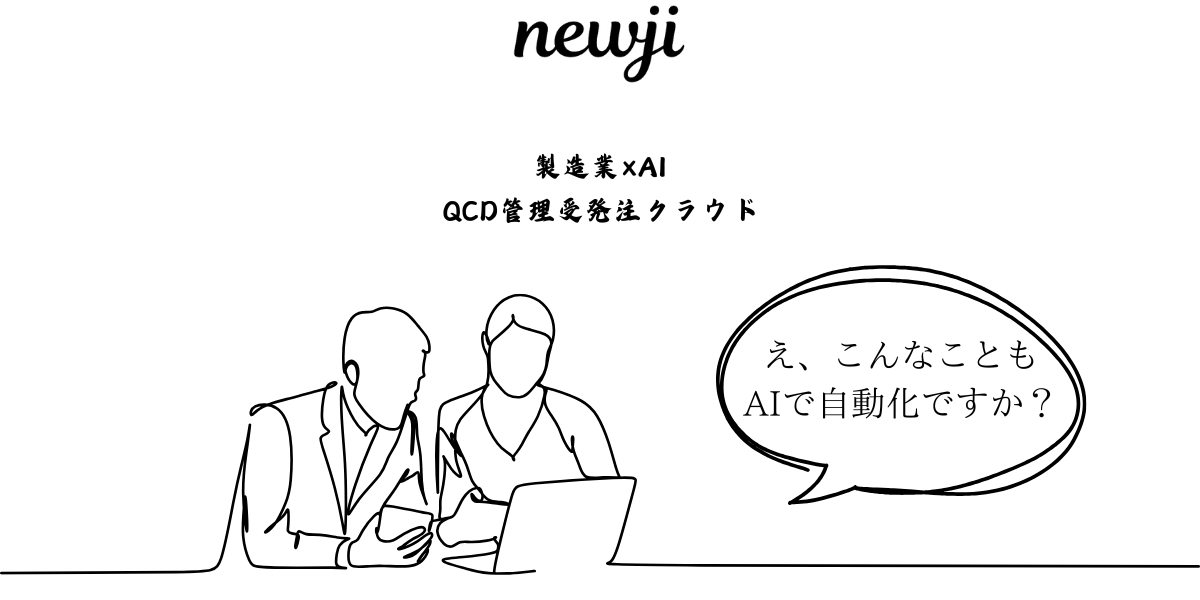
Effective use of resin flow analysis technology and countermeasures against defects and troubles for high-precision, high-quality plastic molded products
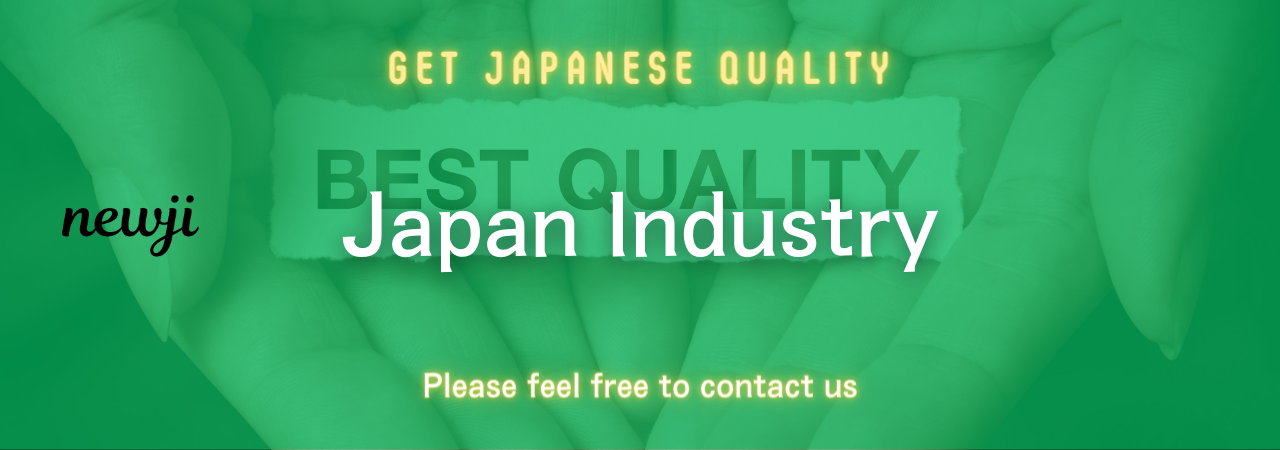
目次
Understanding Resin Flow Analysis Technology
Resin flow analysis technology is essential in the manufacturing of high-precision, high-quality plastic molded products.
This advanced technology helps engineers and designers predict how molten plastic will flow within a mold.
Utilizing simulation software, it identifies potential defects and trouble areas before production begins.
This ensures that the final product meets desired specifications and quality standards.
The process begins with creating a virtual model of the mold and the plastic part.
Using computer-aided engineering (CAE) software, the virtual model allows for simulation of the injection process.
Engineers can visualize how the plastic flows, fills, cools, and solidifies within the mold.
This critical information aids in optimizing the mold design and the injection molding process.
Benefits of Resin Flow Analysis
Resin flow analysis offers multiple benefits in the production of plastic molded products.
Foremost, it helps in identifying potential defects before manufacturing begins.
Issues such as short shots, weld lines, sink marks, and air traps can be detected virtually.
This reduces the need for costly and time-consuming trial and error with physical prototypes.
Moreover, the technology assists in optimizing the design of the mold itself.
By understanding the flow of resin within the mold, designers can make adjustments to ensure even filling and cooling.
This optimization improves the overall performance of the mold and the quality of the finished product.
Additionally, resin flow analysis contributes to reducing material waste and energy consumption.
By finding the optimal conditions for the molding process, manufacturers can minimize excess material usage and energy costs.
This contributes not only to cost efficiency but also to sustainability efforts.
Common Defects in Plastic Molded Products
Despite advances in technology, defects can still occur in plastic molded products.
Understanding common defects helps in identifying potential issues that can be mitigated through resin flow analysis.
Here are a few prevalent defects:
Weld Lines
Weld lines appear where two or more flow fronts meet and solidify before they completely join together.
These lines can be weak spots, compromising the structural integrity of the part.
Resin flow analysis can pinpoint where weld lines are likely to form, allowing for design adjustments.
Air Traps
Air traps occur when air gets encapsulated in the mold during injection.
This defect can lead to surface blemishes and weakened parts.
By simulating the molding process, engineers can identify potential air traps and redesign the mold or adjust processing parameters to eliminate them.
Sink Marks
Sink marks are depressions that occur when the inner part of the molded section cools and contracts.
They are typically found in thicker sections of a part.
Resin flow analysis can help predict these occurrences and suggest strategies for even cooling and solidification.
Warping
Warping happens when different parts of a molded product shrink at different rates, causing the product to twist or bend.
By understanding the flow and cooling cycle of the resin in the mold, this issue can be mitigated through improved design and process control.
Strategies for Mitigating Defects
Addressing defects in the early stages of design and production can save significant time and resources.
Here are some strategies to employ using resin flow analysis:
Optimize Mold Design
Modifying the design of the mold can lead to substantial improvements in the finished product.
Changing gate locations, adjusting wall thickness, and refining the cooling channel designs can all influence the flow and cooling of the resin.
Using resin flow analysis software to test these modifications virtually allows for the best possible design before creating the physical mold.
Adjust Process Parameters
Injecting resin at optimal temperature, pressure, and speed is crucial for achieving high-quality products.
Resin flow analysis can simulate different conditions to find the best combination of these parameters.
Adjustments based on analysis can lead to defects reduction and process efficiency improvement.
Material Selection
Choosing the right material is key to overcoming potential defects.
Different resins behave uniquely under the same conditions.
By analyzing the flow of different materials, engineers can select the best resin for the specific application and mold design.
Conclusion
Resin flow analysis technology is a powerful tool in achieving high-precision, high-quality plastic molded products.
By using advanced simulations, designers and engineers can predict and prevent defects and optimize production processes.
The integration of this technology not only enhances product quality but also leads to cost savings and reduced environmental impact.
For manufacturers aiming to stay competitive, the effective use of resin flow analysis is indispensable.
資料ダウンロード
QCD管理受発注クラウド「newji」は、受発注部門で必要なQCD管理全てを備えた、現場特化型兼クラウド型の今世紀最高の受発注管理システムとなります。
ユーザー登録
受発注業務の効率化だけでなく、システムを導入することで、コスト削減や製品・資材のステータス可視化のほか、属人化していた受発注情報の共有化による内部不正防止や統制にも役立ちます。
NEWJI DX
製造業に特化したデジタルトランスフォーメーション(DX)の実現を目指す請負開発型のコンサルティングサービスです。AI、iPaaS、および先端の技術を駆使して、製造プロセスの効率化、業務効率化、チームワーク強化、コスト削減、品質向上を実現します。このサービスは、製造業の課題を深く理解し、それに対する最適なデジタルソリューションを提供することで、企業が持続的な成長とイノベーションを達成できるようサポートします。
製造業ニュース解説
製造業、主に購買・調達部門にお勤めの方々に向けた情報を配信しております。
新任の方やベテランの方、管理職を対象とした幅広いコンテンツをご用意しております。
お問い合わせ
コストダウンが利益に直結する術だと理解していても、なかなか前に進めることができない状況。そんな時は、newjiのコストダウン自動化機能で大きく利益貢献しよう!
(β版非公開)